Introduction
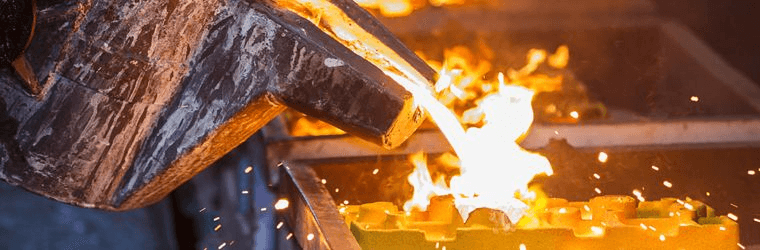
Heat-resistant alloys play an indispensable role in industries requiring high-temperature durability and mechanical stability, including aerospace, automotive, and power generation. These alloys must maintain their physical properties in extreme environments, ensuring reliability and safety. But how can engineers and technicians systematically analyze these properties? This guide dives deep into every aspect of testing and evaluation, from understanding key characteristics to leveraging cutting-edge technology. With detailed explanations and practical advice, this article equips professionals with the knowledge they need to assess and optimize heat-resistant alloys effectively. Whether for design or quality assurance, mastering these techniques is crucial.
What Defines Heat Resistance in Alloys?
Heat resistance in alloys is their ability to retain mechanical and chemical stability under extreme temperatures. This characteristic arises from the interplay of metallurgical factors such as alloy composition, microstructure, and phase stability. For instance, nickel-based alloys derive their heat resistance from their ability to form stable oxides on the surface and maintain a robust matrix structure.
Metals used to create heat-resistant alloys often include nickel, cobalt, and chromium due to their superior thermal stability. Nickel-based alloys, commonly used in jet engines and gas turbines, maintain strength at high temperatures through precipitation strengthening. Cobalt-based alloys excel in wear resistance and thermal fatigue properties, while stainless steels, enriched with chromium, resist oxidation and corrosion.
Heat resistance is not just about maintaining structural integrity; it also encompasses thermal conductivity, thermal expansion, and the ability to resist phase transformations. Alloys must minimize thermal expansion mismatches to avoid cracking or deformation during heating and cooling cycles. Additionally, stable microstructures are vital to prevent the growth of grain boundaries, which can weaken materials over time.
Factors such as melting point, stress rupture properties, and environmental exposure determine an alloy’s performance. For instance, alloys used in aerospace face simultaneous demands for creep resistance and high strength, while those in petrochemical industries must withstand corrosive environments.
Researchers continually develop new alloy compositions to meet specific demands. Advanced alloys such as Inconel and Hastelloy are tailored for demanding applications. Inconel, for example, features exceptional oxidation resistance, making it ideal for jet engines. Similarly, Hastelloy resists both high temperatures and chemical corrosion, performing well in chemical plants.
Understanding heat resistance is crucial for optimizing performance. Designers must balance properties like strength and ductility with environmental resistance. For industries relying on heat-resistant alloys, a comprehensive grasp of their defining characteristics ensures materials can meet operational challenges, from extreme thermal cycling to mechanical stresses in high-temperature environments.
Where Are Heat-Resistant Alloys Used?
Heat-resistant alloys are integral to industries where extreme temperatures are the norm, ensuring equipment reliability and longevity. In the aerospace sector, these materials are vital for turbine blades, combustion chambers, and afterburners. Their ability to withstand temperatures exceeding 1,000°C without losing mechanical integrity is crucial for aircraft performance and safety.
The automotive industry employs heat-resistant alloys in exhaust systems, turbochargers, and valves. Turbochargers, for instance, rely on alloys like Inconel to endure both high temperatures and corrosive exhaust gases, improving engine efficiency. Similarly, exhaust valves made of nickel-based alloys maintain durability under the intense heat of combustion.
In the energy sector, power plants utilize heat-resistant alloys for components like boiler tubes, gas turbines, and nuclear reactor parts. These alloys must endure thermal cycling, oxidation, and creep over extended periods. For example, advanced stainless steels in supercritical power plants resist both corrosion and high-pressure environments, ensuring efficient energy conversion.
Petrochemical plants demand materials that resist both heat and chemical attack. Reactors, distillation columns, and heat exchangers often employ alloys like Hastelloy to handle aggressive chemicals at elevated temperatures. The ability to combine corrosion resistance with thermal stability makes these alloys indispensable in such applications.
Additionally, heat-resistant alloys find roles in the manufacturing of glass, ceramics, and metals. Furnace linings, molds, and tooling require alloys that can maintain dimensional stability and resist wear under repeated heating and cooling cycles.
Space exploration also benefits from these materials. Heat shields, rocket nozzles, and spacecraft components must endure extreme thermal gradients during launch and reentry. Alloys designed for space applications prioritize a combination of low weight and high heat resistance to optimize performance.
By understanding where heat-resistant alloys are used, engineers can select the right materials for specific operational demands. Tailoring alloy selection to application needs ensures durability, efficiency, and safety in challenging environments.
Key Physical Properties to Analyze
Thermal Stability and Expansion
Thermal stability ensures that alloys maintain their mechanical properties under sustained high temperatures. It is crucial to assess thermal expansion, as excessive expansion can lead to stress or failure in components. Alloys with low thermal expansion coefficients, such as Invar, are preferred for applications demanding dimensional stability.
Oxidation and Corrosion Resistance
Oxidation occurs when metals react with oxygen at high temperatures, forming a protective oxide layer. Chromium-rich alloys, for example, form stable oxides that prevent further degradation. Testing for oxidation resistance typically involves prolonged exposure to high temperatures and oxidizing environments, followed by microstructural analysis.
Corrosion resistance ensures durability in aggressive environments, such as chemical plants or marine applications. Hastelloy and stainless steels, rich in chromium and molybdenum, excel in such conditions. Tests like salt spray or immersion testing evaluate corrosion resistance under simulated service conditions.
Creep Resistance
Creep refers to the slow deformation of materials under constant stress and elevated temperatures. It is a critical property for components in turbines and boilers, where materials endure high temperatures for extended periods. Standard creep tests involve applying a constant load and measuring deformation over time.
Tensile Strength and Ductility
The tensile strength of an alloy determines its ability to withstand forces without breaking, while ductility measures its capacity to deform without fracture. Both properties are crucial for structural applications. Tensile testing involves pulling a sample until failure, with results analyzed for yield strength, ultimate tensile strength, and elongation.
Fatigue Resistance
Fatigue resistance measures how well an alloy performs under cyclic loading, common in rotating or oscillating components like turbine blades. Fatigue tests subject samples to repeated stress cycles, identifying the number of cycles to failure. Alloys with high fatigue resistance, such as titanium alloys, excel in dynamic environments.
By systematically analyzing these physical properties, engineers can ensure heat-resistant alloys meet the rigorous demands of their applications.
Testing and Analytical Methods
Mechanical testing evaluates the strength, hardness, and elasticity of alloys. Tensile testing is a cornerstone, providing insights into yield strength, ultimate tensile strength, and elongation. For high-temperature applications, tests must replicate operational conditions, requiring specialized equipment capable of heating samples while maintaining precise stress measurements.
Hardness testing, such as Rockwell or Vickers, assesses an alloy’s resistance to deformation. These tests are vital for applications like cutting tools or wear-resistant surfaces. Microhardness testing allows for localized property evaluation, crucial for understanding variations within a single component.
Thermal analysis techniques, including Differential Scanning Calorimetry (DSC) and Thermogravimetric Analysis (TGA), examine an alloy’s behavior under heat. DSC measures heat flow, revealing phase transitions and thermal stability. TGA tracks weight changes, identifying oxidation or thermal decomposition.
Metallurgical characterization employs advanced microscopy techniques. Scanning Electron Microscopy (SEM) provides high-resolution images of surface features, while Transmission Electron Microscopy (TEM) offers insights into internal microstructures. These methods reveal grain size, phase distributions, and defect concentrations, influencing an alloy’s performance.
Spectroscopy methods, such as X-ray Diffraction (XRD) and Energy Dispersive Spectroscopy (EDS), analyze crystallographic structures and chemical compositions. XRD identifies phases and their orientations, crucial for understanding thermal expansion or corrosion behavior. EDS complements microscopy, offering elemental mapping to verify alloy composition.
By combining these testing and analytical methods, engineers gain a comprehensive understanding of an alloy’s properties, ensuring performance aligns with application demands.
Metallurgical Characterization
Metallurgical characterization delves deep into the structure and properties of heat-resistant alloys. This process evaluates the microstructural elements that define an alloy’s performance under high temperatures and mechanical stress. At its core, metallurgical characterization determines the grain structure, phase distribution, and defect presence within an alloy. These aspects directly affect critical properties like strength, ductility, and thermal resistance.
One of the foundational techniques in this area is optical microscopy. This method examines polished and etched samples to reveal grain size and distribution. Grain size plays a pivotal role in determining the alloy’s mechanical strength and thermal stability. For instance, smaller grains enhance strength but may reduce creep resistance. Conversely, larger grains improve creep performance but may compromise strength.
Scanning Electron Microscopy (SEM) takes the analysis further by offering high-resolution images of the surface and subsurface. SEM provides insights into surface defects, such as cracks or voids, that could compromise performance. Coupled with Energy Dispersive Spectroscopy (EDS), SEM also identifies elemental compositions, ensuring that the alloy meets design specifications.
Transmission Electron Microscopy (TEM) enables detailed exploration of an alloy’s internal structure. TEM uncovers dislocations, precipitates, and other microscopic features influencing mechanical and thermal behavior. For example, the presence of stable precipitates strengthens nickel-based superalloys, while their dissolution at high temperatures signals reduced heat resistance.
Electron Backscatter Diffraction (EBSD) is another advanced tool, mapping crystallographic orientations and revealing texture. Texture affects an alloy’s directional properties, such as anisotropic expansion under thermal stress. Understanding these characteristics helps engineers predict behavior under operational conditions.
Metallurgical characterization is incomplete without phase analysis. Techniques like X-ray Diffraction (XRD) determine the phases present and their stability at various temperatures. Stable phases ensure consistent performance, while metastable phases may lead to degradation under prolonged heat exposure. Phase diagrams guide alloy selection and processing, ensuring optimal microstructural stability.
Non-destructive evaluation (NDE) methods, such as ultrasonic testing and radiography, supplement metallurgical characterization. These techniques detect subsurface defects without damaging components, ensuring reliability in critical applications like aerospace or energy.
The integration of these techniques provides a comprehensive picture of an alloy’s metallurgical integrity. This level of analysis is essential for industries where failure is not an option, ensuring that every material meets the stringent demands of its application.
Spectroscopy Methods
Spectroscopy methods are essential for understanding the chemical composition and structural arrangement of heat-resistant alloys. These techniques uncover critical information about an alloy’s makeup, phases, and defects, all of which impact its performance in high-temperature environments.
X-ray Diffraction (XRD) is a cornerstone technique in structural analysis. By directing X-rays onto a crystalline material, XRD reveals the arrangement of atoms and identifies the phases present in the alloy. This method is particularly useful for detecting phase transformations caused by thermal exposure. For example, the appearance of brittle phases can signal reduced mechanical integrity, making XRD an indispensable tool for quality assurance.
Energy Dispersive Spectroscopy (EDS) complements structural analysis by providing a detailed chemical composition of the alloy. Often paired with Scanning Electron Microscopy (SEM), EDS maps elemental distributions, identifying compositional variations that may lead to weak points or corrosion susceptibility. This is especially important for alloys exposed to harsh chemical environments.
Electron Energy Loss Spectroscopy (EELS) offers further insights, particularly for studying fine structural details. EELS is highly sensitive to changes in bonding and oxidation states, making it valuable for assessing surface reactions in heat-resistant alloys. For instance, EELS can reveal the formation of protective oxide layers that enhance oxidation resistance.
Fourier Transform Infrared Spectroscopy (FTIR) is another powerful tool, particularly for detecting chemical bonds and molecular vibrations. While primarily used for organic materials, FTIR has applications in characterizing surface treatments or coatings on alloys. These treatments often improve thermal or corrosion resistance, and their integrity can be monitored using FTIR.
Mass spectroscopy, including techniques like Glow Discharge Mass Spectrometry (GDMS), provides precise measurements of trace elements. Trace elements significantly influence an alloy’s properties, such as its creep resistance or oxidation behavior. GDMS ensures that these elements remain within acceptable limits, maintaining the alloy’s overall performance.
By employing these spectroscopy methods, engineers gain a detailed understanding of both the macro and micro-level properties of heat-resistant alloys. This knowledge enables precise material selection and optimization, ensuring components perform reliably under extreme conditions.
Advanced Non-Destructive Testing Methods
Advanced non-destructive testing (NDT) methods have revolutionized the analysis of heat-resistant alloys. These techniques allow for the detection of internal flaws and property evaluation without damaging the material, making them ideal for critical applications in aerospace, power generation, and petrochemical industries.
Ultrasonic testing is a widely used NDT method, employing high-frequency sound waves to detect subsurface defects like cracks, voids, and inclusions. The reflected sound waves provide information about the material’s internal structure. In turbine blades, for instance, ultrasonic testing ensures that no hidden defects could compromise performance under high stress and temperature.
Radiographic testing, using X-rays or gamma rays, creates detailed images of the internal features of an alloy. This method is particularly effective for detecting porosity and inclusions in cast components. Radiographic inspection of boiler tubes in power plants ensures their integrity and safe operation.
Thermal imaging, or infrared thermography, evaluates surface temperature distributions to identify areas of heat concentration or thermal anomalies. This technique is valuable for assessing components in real-time operational environments. For example, thermal imaging can detect early signs of overheating in turbine blades, preventing catastrophic failures.
Magnetic Particle Testing (MPT) detects surface and near-surface defects in ferromagnetic alloys. By applying a magnetic field and ferrous particles, cracks and discontinuities become visible. MPT is commonly used for inspecting welds and castings in heat-resistant materials.
Eddy Current Testing (ECT) uses electromagnetic induction to identify surface and subsurface flaws in conductive materials. ECT is particularly useful for detecting cracks in thin sections, such as those found in heat exchangers or piping systems.
These advanced NDT methods provide critical insights into material integrity while preserving the usability of components. By integrating these techniques into regular maintenance and quality assurance programs, industries can enhance safety, performance, and reliability.
Machine Learning in Alloy Analysis
Machine learning (ML) is transforming the analysis of heat-resistant alloys by enabling faster, more accurate predictions of material behavior. This technology uses algorithms to process large datasets, identifying patterns and relationships that traditional methods might overlook. The integration of ML with alloy analysis offers significant advantages in material development and optimization.
Predictive modeling is one of the most impactful applications of ML. By training algorithms on historical data, ML can predict how an alloy will perform under specific conditions. For instance, it can forecast creep resistance or oxidation behavior, reducing the need for extensive physical testing. This accelerates the development of new alloys tailored to specific applications.
ML also enhances the interpretation of complex testing data. Techniques like XRD and SEM generate vast amounts of information, which can be overwhelming to analyze manually. ML algorithms efficiently process this data, identifying critical features such as phase changes or microstructural defects.
Another application is the optimization of alloy compositions. ML can simulate different combinations of elements and predict their impact on properties like tensile strength or corrosion resistance. This allows metallurgists to experiment virtually, saving time and resources in the alloy design process.
ML-powered quality control systems can detect manufacturing defects in real-time. For example, algorithms analyzing thermal imaging data can identify hot spots or inconsistencies in coatings, ensuring components meet stringent standards before deployment.
By integrating ML into alloy analysis, industries can achieve breakthroughs in material performance and reliability. This synergy between technology and metallurgy paves the way for innovations that meet the ever-increasing demands of high-temperature applications.
Setting Up a Comprehensive Testing Framework
Establishing a robust testing framework is essential for analyzing heat-resistant alloys effectively. This process begins with defining the objectives of the analysis, such as identifying critical properties for a specific application. Clear objectives guide the selection of testing methods and equipment.
The next step is assembling the required tools. A comprehensive framework includes mechanical testing equipment (e.g., tensile testers), thermal analysis tools (e.g., DSC), and advanced imaging systems (e.g., SEM and XRD). Each tool addresses a specific aspect of alloy performance, from strength to microstructure.
Sample preparation is a crucial component of the framework. Properly prepared samples ensure accurate and reproducible results. For instance, polished and etched samples reveal microstructural details during metallurgical characterization, while specimens for mechanical testing must meet precise dimensional standards.
Testing conditions should replicate real-world environments as closely as possible. For high-temperature applications, this means conducting tests at operational temperatures and stress levels. Environmental factors like oxidation or corrosive exposure should also be simulated to assess long-term performance.
Data interpretation is the final stage of the framework. Results from different tests must be synthesized to form a holistic understanding of the alloy’s properties. For example, combining tensile strength data with microstructural analysis provides insights into how grain size influences mechanical behavior.
By following a systematic approach, engineers can ensure that their testing framework delivers reliable and actionable insights. This foundation is critical for material selection, design, and quality assurance in high-performance applications.
Conclusion
Analyzing the physical properties of heat-resistant alloys is a meticulous but essential process for ensuring reliability in demanding environments. From understanding thermal stability to leveraging machine learning, each method adds a layer of insight into material performance. Comprehensive testing frameworks and advanced techniques empower engineers to make informed decisions, driving innovation and safety across industries. By mastering these approaches, you can unlock the full potential of heat-resistant alloys and meet the challenges of high-temperature applications.
FAQs
What are the key properties to analyze in heat-resistant alloys?
Critical properties include thermal stability, oxidation resistance, creep resistance, tensile strength, and fatigue resistance.
Why is machine learning important in alloy analysis?
Machine learning accelerates predictions, optimizes alloy compositions, and enhances data interpretation, making the analysis more efficient and accurate.
Which industries rely on heat-resistant alloys?
Key industries include aerospace, automotive, power generation, petrochemicals, and space exploration.
How do non-destructive testing methods benefit alloy analysis?
Non-destructive testing detects defects without damaging components, ensuring safety and reliability while preserving material usability.
What role does spectroscopy play in analyzing heat-resistant alloys?
Spectroscopy methods provide detailed insights into the chemical composition and structural arrangement, which are critical for performance optimization.