Why Thermal Stability Matters in Heat-Resistant Alloys
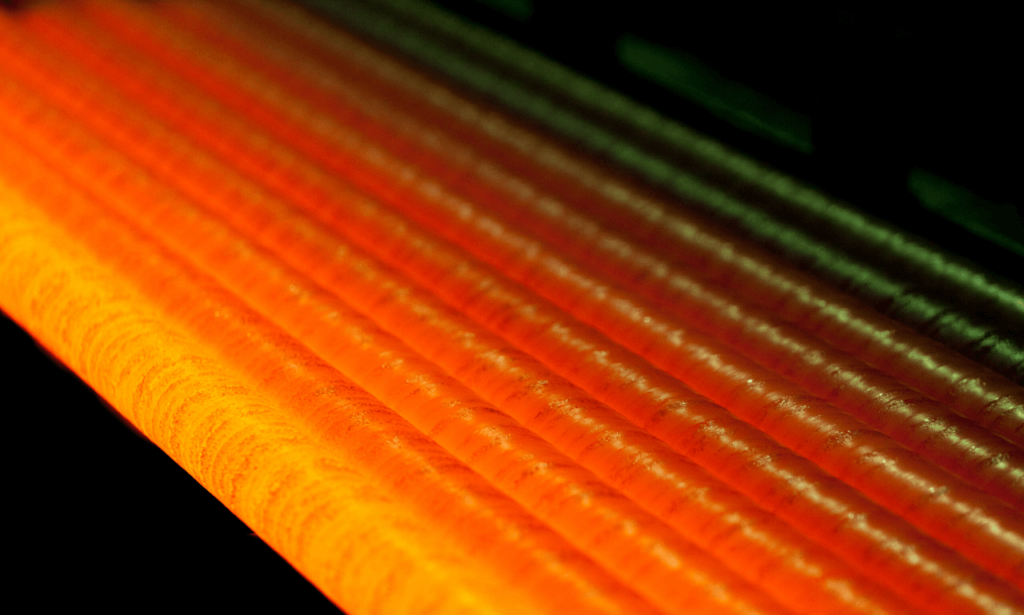
Thermal stability plays a critical role in determining the performance and safety of materials used in high-temperature environments. From aerospace engineering to automotive manufacturing, the ability of an alloy to withstand extreme heat without significant changes in its properties is vital. Imagine the consequences of a turbine blade failing mid-flight or an engine component deforming due to inadequate heat resistance. The implications are not just technical but also economic and environmental. Assessing thermal stability ensures that materials remain reliable and effective in demanding conditions. This guide aims to demystify the process, equipping engineers and manufacturers with the tools and insights they need to make informed decisions.
The Science Behind Thermal Stability
Understanding thermal stability begins with the fundamentals of material science. At its core, thermal stability refers to the ability of a material to maintain its structural integrity, chemical properties, and mechanical performance under prolonged exposure to high temperatures. This concept is particularly critical in alloys designed for heat resistance.
The behavior of materials at high temperatures is influenced by their atomic and crystalline structure. Metals and alloys are composed of a lattice of atoms bound together by metallic bonds. When subjected to heat, the energy from thermal vibrations can disrupt these bonds. For alloys, the addition of elements like chromium, molybdenum, or nickel modifies the lattice, enhancing its ability to resist heat-induced deformation.
Another aspect to consider is phase stability. Alloys often contain multiple phases—regions with distinct atomic arrangements. Thermal stability involves maintaining the equilibrium of these phases over time. For instance, the gamma phase in nickel-based superalloys provides superior strength and resistance at elevated temperatures, but improper heat treatment can cause detrimental phase transformations.
Key properties such as thermal expansion, conductivity, and melting point also define thermal stability. Thermal expansion refers to how much a material expands when heated, which is crucial for components like turbine blades that operate under fluctuating temperatures. Conductivity determines the material’s ability to dissipate heat, influencing its performance in thermal management systems.
In summary, the science of thermal stability encompasses the interplay of atomic structures, phase equilibrium, and physical properties. These principles guide the design and testing of heat-resistant alloys, ensuring they meet the rigorous demands of high-temperature applications.
Common Applications of Heat-Resistant Alloys
Heat-resistant alloys are indispensable in industries where extreme temperatures are the norm. Their unique properties make them suitable for a wide range of applications, from aviation to renewable energy.
In aerospace and aviation, heat-resistant alloys are vital for components like turbine blades, exhaust systems, and afterburners. These parts must endure temperatures exceeding 1,000°C while maintaining strength and resisting oxidation. Nickel-based superalloys dominate this field due to their exceptional thermal stability and resistance to creep.
The automotive industry also benefits from heat-resistant alloys, particularly in high-performance engines and exhaust systems. Materials like stainless steel and titanium alloys are used to withstand the heat generated during combustion. Advanced catalytic converters rely on these alloys for durability and efficiency in reducing emissions.
Industrial applications include heat exchangers, boilers, and chemical processing equipment. Here, alloys like Inconel and Hastelloy are favored for their ability to resist corrosion and thermal fatigue. In the energy sector, heat-resistant materials are crucial for components in nuclear reactors and concentrated solar power plants, where they must endure extreme heat and radiation.
Emerging technologies, such as hypersonic travel and hydrogen production, further expand the demand for heat-resistant alloys. These cutting-edge applications push the boundaries of material science, requiring alloys that perform under unprecedented thermal stresses.
Understanding the diverse applications of heat-resistant alloys underscores their importance in modern technology. Each use case demands a tailored approach to alloy selection and assessment, ensuring optimal performance in specific environments.
Properties Influencing Thermal Stability
The thermal stability of an alloy is determined by a combination of physical, chemical, and structural properties. These factors interact to define how a material behaves under high-temperature conditions, making them crucial considerations in alloy design and testing.
One of the most significant influences is the crystalline structure of the material. Grain size, for example, plays a critical role. Fine-grained structures typically offer higher strength at room temperature, but coarser grains may provide better stability at elevated temperatures due to reduced grain boundary sliding. Engineers must balance these attributes to optimize performance.
Chemical composition is another key factor. The addition of alloying elements such as chromium, molybdenum, and tungsten enhances thermal stability by improving resistance to oxidation, corrosion, and creep. Chromium forms a protective oxide layer on the surface, preventing further oxidation. Nickel improves toughness, while molybdenum increases strength at high temperatures.
Oxidation and corrosion resistance are directly linked to an alloy’s thermal stability. High-temperature environments often contain reactive gases like oxygen, sulfur, and chlorine, which can degrade materials over time. Alloys with higher chromium or aluminum content form stable oxide layers that act as barriers against such attacks.
Other properties like thermal conductivity and expansion also affect stability. High thermal conductivity helps dissipate heat, preventing localized overheating, while controlled thermal expansion minimizes stress caused by temperature fluctuations. These attributes are particularly critical for components in cyclic thermal environments, such as gas turbines or automotive engines.
By understanding and optimizing these properties, engineers can design alloys that meet the stringent demands of high-temperature applications. This holistic approach ensures that materials not only survive but thrive in challenging environments.
Testing Methods for Thermal Stability
Accurately assessing the thermal stability of heat-resistant alloys requires a range of testing methods, each designed to evaluate specific properties and behaviors. These tests provide valuable insights into how materials will perform under real-world conditions.
Thermogravimetric Analysis (TGA) is a fundamental technique that measures changes in a material’s weight as it is heated. This test is particularly useful for assessing oxidation resistance, as weight gain indicates the formation of an oxide layer. By analyzing the rate and extent of oxidation, engineers can determine the suitability of an alloy for high-temperature environments.
Differential Scanning Calorimetry (DSC) focuses on the heat flow associated with phase transitions. This method identifies melting points, crystallization temperatures, and other thermal events that affect an alloy’s performance. DSC is invaluable for understanding phase stability and designing heat treatment processes.
Creep testing evaluates a material’s ability to withstand prolonged stress at elevated temperatures. This test measures the deformation of an alloy over time, providing insights into its long-term durability. Components like turbine blades and pressure vessels rely on creep-resistant materials to maintain safety and efficiency.
Fatigue testing assesses the impact of cyclic thermal loads on material integrity. Repeated heating and cooling cycles can cause microstructural damage, leading to cracks and eventual failure. Fatigue testing simulates these conditions, helping engineers identify alloys that can endure such stresses.
Each of these methods offers a unique perspective on thermal stability, enabling a comprehensive evaluation of heat-resistant alloys. By combining multiple tests, manufacturers can ensure that their materials meet the rigorous demands of modern applications.
Advanced Analytical Techniques
Advanced analytical techniques provide deeper insights into the behavior of heat-resistant alloys under high-temperature conditions. These methods go beyond conventional tests, offering precise data on microstructural, chemical, and physical changes that occur during thermal exposure.
X-Ray Diffraction (XRD) is a powerful tool for studying phase transformations in alloys. By analyzing the diffraction patterns of X-rays scattered by the material’s crystal lattice, engineers can identify changes in phase composition and structural integrity. This technique is particularly effective for detecting high-temperature phase instabilities, such as the transformation of gamma prime phases in nickel-based superalloys, which are critical for maintaining strength at elevated temperatures.
Electron microscopy, including Scanning Electron Microscopy (SEM) and Transmission Electron Microscopy (TEM), provides high-resolution images of the alloy’s microstructure. SEM is ideal for surface analysis, revealing oxidation layers, grain boundaries, and cracks. TEM, on the other hand, allows for the visualization of atomic-scale defects, dislocations, and precipitates. Together, these methods enable a detailed understanding of how heat affects the material’s internal structure.
Spectroscopic methods, such as Energy Dispersive Spectroscopy (EDS) and Secondary Ion Mass Spectrometry (SIMS), complement electron microscopy by offering elemental analysis. These techniques can detect changes in chemical composition, such as the diffusion of alloying elements or the formation of oxide scales. This information is crucial for evaluating the corrosion resistance and overall thermal stability of the alloy.
Thermal imaging and infrared spectroscopy are also gaining traction as non-destructive testing methods. These techniques measure heat distribution and emissivity changes on the material’s surface, providing real-time data on thermal performance. For example, thermal imaging can identify hotspots or uneven heating, which may indicate areas of weakness.
By integrating these advanced techniques, researchers and engineers can achieve a comprehensive understanding of an alloy’s thermal stability. This knowledge not only guides material selection and design but also informs the development of innovative alloys tailored to meet the demands of cutting-edge applications.
Benchmarking Standards and Protocols
Adhering to standardized testing protocols ensures consistency, reliability, and comparability of thermal stability assessments. Organizations such as ASTM International, ISO, and specific industry consortia have established guidelines that serve as benchmarks for evaluating heat-resistant alloys.
ASTM standards, such as ASTM E228 for thermal expansion testing and ASTM E139 for creep testing, provide detailed methodologies for conducting experiments. These standards specify parameters like sample preparation, testing environments, and data interpretation, ensuring that results are accurate and reproducible. For instance, ASTM E1461 outlines the laser flash method for measuring thermal diffusivity and conductivity, critical properties for heat management applications.
ISO standards, including ISO 6892 for tensile testing and ISO 204 for creep testing, offer internationally recognized procedures that align with global trade and manufacturing practices. These standards emphasize precision and uniformity, making them essential for cross-border collaborations and supply chain integration.
Industry-specific protocols address the unique requirements of sectors such as aerospace, automotive, and energy. For example, the aviation industry often requires compliance with AMS (Aerospace Material Specifications) standards, which focus on high-temperature performance and oxidation resistance.
Case studies highlight the practical application of these standards. For instance, a nickel-based superalloy used in turbine blades must pass rigorous testing for creep, fatigue, and oxidation resistance under simulated flight conditions. Benchmarking against industry standards ensures that the material meets or exceeds performance expectations, reducing the risk of failure.
Adopting standardized testing protocols not only validates the thermal stability of heat-resistant alloys but also builds trust among stakeholders. It demonstrates a commitment to quality and reliability, essential for maintaining competitiveness in high-stakes industries.
Factors Affecting Test Accuracy
Achieving accurate results in thermal stability testing requires careful attention to multiple factors that can influence the outcomes. These considerations are crucial for ensuring the reliability and validity of the data obtained.
Sample preparation is a critical step that can significantly impact test accuracy. Improper cleaning, machining, or handling can introduce contaminants or defects that skew results. For example, residual oils or surface scratches may affect oxidation tests, leading to erroneous conclusions about the material’s performance. Standardized procedures for sample preparation help mitigate these risks, ensuring consistency across experiments.
Environmental variables, such as temperature fluctuations, humidity, and atmospheric composition, play a significant role in testing outcomes. Controlled environments, such as vacuum chambers or inert gas atmospheres, are often required to minimize external influences. For instance, creep testing in an oxygen-rich environment may accelerate oxidation, affecting the material’s deformation rate.
Instrumentation calibration is another essential factor. Testing equipment must be regularly calibrated to maintain precision and accuracy. Misaligned sensors, outdated software, or worn components can lead to discrepancies in measurements. Periodic calibration and maintenance schedules ensure that instruments deliver reliable data.
Operator expertise also affects test accuracy. Proper training and adherence to standardized procedures are necessary to avoid human errors. For example, inconsistent loading rates during tensile tests can lead to variable results. Clear documentation and quality control measures help minimize such discrepancies.
Finally, data interpretation is a critical aspect of ensuring test accuracy. Misreading thermal curves, overlooking anomalies, or applying incorrect models can lead to flawed conclusions. Advanced software tools and cross-validation with multiple testing methods enhance the robustness of data analysis.
By addressing these factors, engineers and researchers can achieve high levels of accuracy in thermal stability testing, providing a solid foundation for material evaluation and decision-making.
How to Interpret Test Results
Interpreting test results is a vital step in assessing the thermal stability of heat-resistant alloys. Understanding the data allows engineers to make informed decisions about material suitability and performance in specific applications.
Thermal curves generated during tests like TGA and DSC provide key insights into material behavior. For example, a TGA curve showing a steady weight gain indicates oxidation resistance, while a sharp weight loss may signal material degradation. Similarly, DSC curves reveal phase transitions, such as melting or crystallization, which are critical for evaluating phase stability.
Identifying fail points is another important aspect of result interpretation. Tests like creep and fatigue provide data on the conditions under which a material fails, such as the stress level or number of cycles. This information helps engineers determine safety margins and predict component lifespan under operational conditions.
Comparative analysis is often used to benchmark materials against industry standards or competing alloys. By comparing properties like thermal expansion coefficients, conductivity, and oxidation resistance, engineers can select the best alloy for a given application. For instance, an alloy with a lower thermal expansion coefficient may be preferable for precision components to minimize dimensional changes under heat.
Visualizing data through graphs, charts, and tables enhances clarity and aids decision-making. Software tools can further streamline this process, offering simulations and predictive models based on test data. These tools allow for scenario analysis, helping engineers anticipate material performance under varying conditions.
In conclusion, effective interpretation of test results bridges the gap between laboratory analysis and real-world application. It empowers engineers to optimize material selection, design, and performance, ensuring the success of high-temperature systems.
Enhancing Thermal Stability Through Alloy Design
Designing heat-resistant alloys with enhanced thermal stability requires a strategic approach that balances multiple factors, including composition, microstructure, and processing techniques. Innovations in alloy design continue to push the boundaries of material performance.
Optimizing composition is a primary strategy for improving thermal stability. Adding elements like chromium, nickel, and molybdenum enhances oxidation resistance, strength, and creep resistance. For example, chromium forms a protective oxide layer that prevents further oxidation, while nickel improves ductility and toughness at high temperatures.
Microstructural engineering plays a significant role in alloy design. Controlling grain size and orientation can enhance resistance to thermal fatigue and creep. Techniques like grain boundary strengthening and precipitation hardening create stable microstructures that maintain integrity under stress. Advanced processing methods, such as powder metallurgy and additive manufacturing, offer precise control over microstructural features.
Coatings and surface treatments provide an additional layer of protection against high-temperature degradation. Ceramic coatings, for instance, act as thermal barriers, reducing heat transfer to the underlying material. Plasma-sprayed coatings and chemical vapor deposition are common techniques for applying these protective layers.
Research into nano-engineered alloys is opening new possibilities for thermal stability. Nanostructured materials exhibit unique properties, such as higher strength and thermal resistance, due to their refined microstructures. These materials are being explored for applications in aerospace, energy, and advanced manufacturing.
By integrating these design strategies, engineers can create alloys that meet the demanding requirements of high-temperature applications. This iterative process of innovation ensures that heat-resistant materials remain at the forefront of technological advancement.
Challenges in Assessing Thermal Stability
Despite advances in testing and design, assessing thermal stability presents several challenges that require innovative solutions. These challenges stem from the complexity of materials, technological limitations, and economic constraints.
Material complexity is a significant hurdle. Heat-resistant alloys often consist of multiple phases and alloying elements, each contributing to thermal stability. Predicting the behavior of such complex systems under high temperatures requires sophisticated models and simulations. Variability in manufacturing processes further adds to the challenge, as slight differences in composition or microstructure can impact performance.
Technological limitations also affect the assessment process. Current testing methods may not fully capture long-term performance or account for extreme conditions. For instance, creep testing can take months or even years to complete, making it impractical for rapid evaluations. Developing accelerated testing techniques that provide reliable data in shorter timeframes is an ongoing area of research.
Economic considerations are another challenge. Comprehensive testing and advanced analytical techniques can be costly, especially for small-scale manufacturers or niche applications. Balancing cost and accuracy is critical for making thermal stability assessment accessible to a broader range of industries.
Addressing these challenges requires collaboration among researchers, engineers, and industry stakeholders. Investments in research and development, along with the adoption of emerging technologies, will pave the way for more effective and efficient assessment methods.
Advances in Thermal Stability Research
The field of thermal stability research is evolving rapidly, driven by advancements in computational tools, experimental techniques, and material innovation. These developments are transforming how heat-resistant alloys are designed and evaluated.
Simulation and modeling play a pivotal role in modern research. Computational tools like finite element analysis and molecular dynamics allow for detailed predictions of material behavior under heat. These simulations can replicate complex scenarios, such as thermal cycling or multi-phase interactions, providing valuable insights before physical testing.
Nano-engineered alloys represent a significant breakthrough in material science. By manipulating materials at the nanoscale, researchers can achieve unprecedented levels of thermal resistance and mechanical strength. For example, adding nanoparticles to alloys can create stable precipitates that inhibit grain growth and enhance creep resistance.
Collaborative research initiatives are accelerating progress. Universities, research institutes, and industry leaders are working together to address challenges and explore new frontiers. Open-source databases and shared experimental data are fostering innovation by making information more accessible.
The integration of artificial intelligence and machine learning is also revolutionizing thermal stability research. These technologies can analyze large datasets, identify patterns, and optimize alloy design. AI-driven approaches are particularly valuable for exploring vast compositional spaces and predicting the performance of novel materials.
By leveraging these advances, the field of thermal stability research is poised to deliver next-generation alloys that meet the demands of tomorrow’s high-temperature applications.
Practical Tips for Engineers and Manufacturers
For engineers and manufacturers, practical strategies for assessing and enhancing thermal stability are essential for achieving optimal performance and reliability in high-temperature applications.
Choosing the right testing method is the first step. Consider the specific requirements of the application, such as temperature range, mechanical load, and environmental conditions. Combining multiple methods, such as TGA, DSC, and creep testing, provides a comprehensive evaluation of thermal stability.
Maintaining testing equipment is equally important. Regular calibration and maintenance ensure accurate and consistent results. Investing in modern instruments with advanced capabilities, such as thermal imaging or automated data analysis, enhances the efficiency of testing processes.
Collaboration with experts and third-party testing services can provide additional insights and validation. Independent laboratories often have specialized equipment and expertise, making them valuable partners for complex assessments.
Finally, staying informed about the latest developments in thermal stability research and industry standards ensures that engineers and manufacturers remain competitive. Attending conferences, participating in professional organizations, and subscribing to relevant journals are effective ways to stay updated.
Frequently Asked Questions
What makes an alloy heat-resistant? Heat resistance is achieved through a combination of alloying elements, microstructural engineering, and protective coatings, which enhance properties like oxidation resistance and creep strength.
How does thermal stability impact long-term performance? Thermal stability ensures that materials maintain their structural integrity, mechanical properties, and resistance to degradation under prolonged exposure to high temperatures.
Can coatings improve the thermal stability of non-heat-resistant alloys? Yes, coatings such as ceramic or plasma-sprayed layers can enhance the thermal stability of materials by acting as thermal barriers and protecting against oxidation.
What is the most cost-effective testing method? Thermogravimetric Analysis (TGA) and Differential Scanning Calorimetry (DSC) are relatively cost-effective methods that provide valuable insights into thermal behavior.
Conclusion
Understanding and assessing the thermal stability of heat-resistant alloys is critical for ensuring the success of high-temperature systems. From aerospace to automotive industries, reliable materials are the foundation of safety and efficiency. By leveraging advanced techniques, adhering to standards, and embracing innovation, engineers and manufacturers can meet the challenges of modern applications. Ready to optimize your material selection and testing processes? Start exploring advanced solutions today!