Understanding Heat-Resistant Alloys
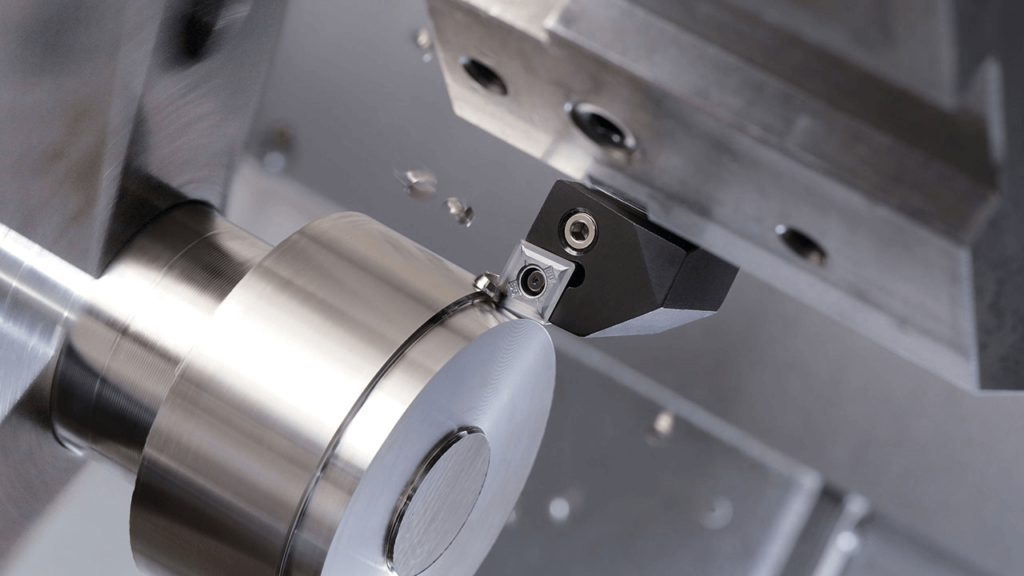
Heat-resistant alloys are indispensable materials in engineering and manufacturing. They are specially formulated to maintain their structural integrity and resist degradation under high temperatures, making them critical for industries like aerospace, power generation, and automotive engineering. These alloys can withstand extreme thermal and mechanical stress while delivering superior performance. However, selecting the right alloy can be challenging due to the vast number of properties to consider. This article will serve as a comprehensive guide to understanding and comparing the properties of heat-resistant alloys, empowering you to make informed decisions tailored to your specific application needs.
Why Compare Properties of Heat-Resistant Alloys?
When choosing a heat-resistant alloy for a project, it is crucial to consider more than just temperature limits. The specific demands of an application dictate the necessity of comparing various properties to identify the most suitable material. Industries dealing with extreme conditions, such as jet engines or nuclear reactors, require materials capable of maintaining stability under stress and environmental factors. A failure to choose correctly can lead to dire consequences, including compromised safety, increased maintenance costs, or even catastrophic failures.
The comparison process helps address multiple factors simultaneously, including performance, longevity, and cost-efficiency. For instance, a material suitable for a furnace may not perform well in a corrosive marine environment. Similarly, alloys used in turbine blades must resist both oxidation and mechanical fatigue. By systematically evaluating properties like tensile strength, thermal conductivity, and creep resistance, engineers and procurement specialists can balance the trade-offs inherent in alloy selection.
Moreover, the economic implications of alloy selection underscore the importance of comparison. High-performing alloys are often expensive, but the cost must be justified by their benefits, such as reduced downtime, maintenance, and longer lifecycle. Understanding the specific attributes of each material ensures investments are aligned with project goals.
The risks of not comparing alloys extend to safety and operational efficiency. Consider aerospace applications where a turbine blade’s failure could jeopardize an entire flight. Proper material selection ensures compliance with safety standards, prevents unnecessary expenditures, and supports optimal operational performance. Thus, taking the time to compare heat-resistant alloys is an indispensable step in ensuring both technical and financial success in high-stakes projects.
Key Properties of Heat-Resistant Alloys
To compare heat-resistant alloys effectively, one must evaluate their properties across multiple dimensions. These properties directly influence an alloy’s suitability for specific applications, such as those requiring high-temperature strength or corrosion resistance. Understanding these factors ensures a holistic approach to material selection.
Thermal Conductivity
Thermal conductivity measures how efficiently a material transfers heat. In some applications, such as heat exchangers, high thermal conductivity is beneficial. However, in other situations, such as insulation components, low thermal conductivity is preferred. This property plays a crucial role in determining how a material reacts to temperature gradients and whether it can maintain thermal stability under operational stress.
Creep Resistance
Creep resistance describes a material’s ability to withstand deformation under prolonged exposure to high temperatures and mechanical stress. This is particularly important in applications like turbines or power plants, where components are subjected to sustained loads at elevated temperatures. Alloys with high creep resistance, such as nickel-based superalloys, are essential in such scenarios.
Oxidation Resistance
Oxidation resistance refers to an alloy’s ability to resist chemical degradation when exposed to oxygen at high temperatures. This property is vital for materials used in high-temperature environments, such as combustion chambers, where oxygen exposure is inevitable. Alloys that lack this resistance can suffer from scaling and reduced structural integrity.
Strength and Durability
Strength is a fundamental property determining an alloy’s ability to bear loads without failure. Durability extends this concept by emphasizing how well a material retains its properties over time under specific conditions. For example, titanium alloys offer excellent strength-to-weight ratios, making them ideal for aerospace applications.
Corrosion Resistance
Corrosion resistance is critical in environments where chemical exposure or moisture could degrade materials. Stainless steels and cobalt-based alloys, for instance, are designed to resist aggressive chemicals and maintain performance in corrosive settings, such as marine or chemical processing environments.
By evaluating these properties, engineers can make data-driven decisions to select the most appropriate alloy for their specific needs.
Types of Heat-Resistant Alloys
Heat-resistant alloys come in various compositions, each tailored for specific performance attributes. Understanding the types of alloys available is essential for selecting the right material for your application.
Nickel-Based Alloys
Nickel-based alloys, such as Inconel and Hastelloy, are among the most widely used materials for high-temperature applications. They offer exceptional creep and oxidation resistance, making them ideal for jet engines, gas turbines, and chemical processing equipment. These alloys are also resistant to many corrosive substances, providing versatility in demanding environments.
Titanium-Based Alloys
Titanium-based alloys combine lightweight properties with exceptional strength and corrosion resistance. These materials are commonly used in aerospace applications where weight savings are critical. Titanium’s resistance to corrosion in seawater also makes it an excellent choice for marine applications.
Stainless Steels
Stainless steels are a versatile group of alloys known for their corrosion resistance and affordability. Austenitic stainless steels are particularly suited for high-temperature environments, while martensitic grades offer higher strength and toughness.
Cobalt-Based Alloys
Cobalt-based alloys, such as Stellite, are engineered for excellent wear and oxidation resistance. These materials are frequently used in cutting tools, valves, and turbine blades, where durability under high-stress conditions is paramount.
Each type of alloy has unique characteristics, and understanding these differences is crucial for optimal material selection.
Factors to Consider Before Comparison
Before comparing heat-resistant alloys, it is essential to define the parameters and requirements of your application. This ensures a more targeted evaluation and reduces the risk of overlooking critical factors.
Application Requirements
The intended use of an alloy heavily influences its selection criteria. Consider the operating temperature range, the magnitude of stress, and exposure to environmental factors such as moisture, chemicals, or oxygen. For example, materials used in a furnace environment must prioritize thermal stability and oxidation resistance, while those in a marine setting should focus on corrosion resistance.
Economic Considerations
Cost plays a significant role in material selection. While high-performance alloys can be expensive, their long-term benefits often justify the investment. Assess the total cost of ownership, including maintenance, replacement, and potential downtime costs. An alloy that requires frequent replacement may end up being more expensive over time than a premium material with superior durability.
Supply Chain Availability
The availability of certain alloys can vary depending on geographic and market conditions. Ensuring a steady supply of your chosen material is crucial for uninterrupted operations. Partnering with reliable suppliers and maintaining a stock buffer can mitigate supply chain risks.
By carefully analyzing these factors, decision-makers can approach the comparison process with clarity and confidence.
Methods for Comparing Alloy Properties
Comparing heat-resistant alloys involves a combination of experimental testing, computational analysis, and standards-based evaluation. Employing a systematic approach ensures comprehensive insights into each material’s performance.
Laboratory and Field Tests
Laboratory tests such as tensile strength analysis, thermal fatigue testing, and creep resistance evaluation provide quantitative data on material performance. Field tests simulate real-world conditions, offering insights into how alloys behave under operational stresses.
Analytical Tools
Advanced software tools enable predictive modeling of alloy behavior under various conditions. Programs like Thermo-Calc and CES Selector are invaluable for simulating performance metrics, such as thermal expansion and corrosion resistance, without requiring physical prototypes.
Industry Standards
Adhering to standards like ASTM or ISO ensures consistent quality and reliability in material testing. These standards provide benchmarks for comparing properties across different alloys, facilitating informed decision-making.
By leveraging these methods, engineers can develop a robust understanding of how each alloy will perform in its intended application.
Case Study: Comparing Alloys for Turbine Blades
Selecting the right material for turbine blades is one of the most challenging tasks in high-temperature engineering. Turbine blades operate under extreme conditions, including high mechanical stress, thermal gradients, and exposure to corrosive gases. This case study illustrates how a systematic comparison of alloy properties can guide material selection.
Creep Resistance Analysis
Turbine blades must resist deformation over extended periods. Materials like nickel-based superalloys are ideal due to their superior creep resistance at high temperatures.
Thermal Fatigue Endurance
Repeated temperature fluctuations can lead to material fatigue. Alloys with low thermal expansion coefficients minimize stress and prolong blade life.
Cost-Benefit Evaluation
High-performance alloys can be expensive, but their longevity and reliability often offset the initial investment. A detailed cost analysis helps identify materials that provide the best value for the application.
This case study demonstrates the critical role of a structured comparison process in ensuring optimal material performance and operational safety.
Challenges in Comparing Alloys
Comparing heat-resistant alloys is not without its challenges. Variability in test conditions, conflicting performance metrics, and the need to balance multiple priorities can complicate the process.
Test Condition Variability
Differences in laboratory setups and environmental conditions can lead to inconsistent results. Standardizing testing procedures helps reduce this variability.
Balancing Performance and Cost
High-performance alloys are often more expensive, necessitating trade-offs between technical and economic factors. Decision-makers must weigh the importance of each property against budget constraints.
Emerging Technologies
New materials and manufacturing techniques, such as additive manufacturing, introduce additional complexity to the comparison process. Staying updated on technological advancements is crucial for informed decision-making.
Understanding these challenges equips engineers to navigate the complexities of alloy selection effectively.
The Role of Standards and Certifications
Standards and certifications play a pivotal role in ensuring the quality and reliability of heat-resistant alloys. They provide a framework for evaluating material properties and verifying compliance with industry requirements.
Key Industry Standards
Standards like ASTM and ASME define specific criteria for material testing and performance. Adhering to these standards ensures consistency and reliability in alloy selection.
Certification Data Sheets
Material certifications provide detailed information on an alloy’s composition, properties, and performance. Understanding how to interpret these sheets is essential for making informed decisions.
By relying on standards and certifications, engineers can ensure the materials they select meet the highest quality benchmarks.
Innovative Alloys and Future Trends
The field of heat-resistant alloys is continually evolving, driven by advancements in material science and manufacturing technology. Emerging innovations promise to address many of the limitations of traditional materials.
High-Entropy Alloys
High-entropy alloys combine multiple elements in nearly equal proportions, offering exceptional strength and thermal stability. These materials are gaining attention for their potential in extreme environments.
Additive Manufacturing
3D printing enables the creation of complex geometries and customized alloys. This technology is transforming how heat-resistant materials are designed and used.
Sustainable Materials
Environmental concerns are driving the development of more sustainable alloys. These materials prioritize recyclability and reduced environmental impact without compromising performance.
By staying abreast of these trends, industries can capitalize on new opportunities to enhance performance and sustainability.
Comparing Alloy Costs
Cost considerations are a critical aspect of material selection. Understanding the factors influencing cost helps balance performance with budget constraints.
Raw Material Sourcing
The availability and price of raw materials significantly impact alloy costs. Rare elements like cobalt or nickel can drive up prices, necessitating careful evaluation of supply chain dynamics.
Processing Expenses
The complexity of manufacturing processes, such as forging or machining, adds to the overall cost. Alloys that require specialized equipment or techniques may incur higher expenses.
Lifecycle Costs
The total cost of ownership includes maintenance, replacement, and downtime expenses. High-performing alloys with longer lifecycles often provide better value despite their higher initial cost.
By analyzing these factors, decision-makers can identify materials that align with both performance and budgetary requirements.
Visual Tools for Comparison
Visual tools such as charts and tables simplify the comparison process, providing clear insights into material properties.
Decision Matrices
A decision matrix ranks alloys based on key performance metrics, offering a structured approach to material selection.
Graphical Representations
Graphs illustrating properties like thermal conductivity or strength make it easier to compare alloys at a glance.
Software Solutions
Programs like CES Selector enable dynamic visualization of alloy properties, streamlining the comparison process.
Incorporating these tools enhances the efficiency and accuracy of material selection.
Common Misconceptions in Alloy Selection
Several myths persist in the field of alloy selection, often leading to suboptimal decisions.
High-Cost Alloys Always Perform Better
While premium materials offer excellent properties, they are not always the best choice for every application. Balancing cost with specific requirements ensures better outcomes.
Certification Guarantees Suitability
Certification indicates quality but does not guarantee an alloy’s fitness for a specific application. Application-specific testing remains essential.
Ignoring Secondary Properties
Properties like weldability or machinability are often overlooked, leading to challenges during manufacturing or maintenance.
Addressing these misconceptions ensures a more informed approach to alloy selection.
Practical Tips for Engineers and Procurement Specialists
Selecting the right alloy requires collaboration, thorough research, and a strategic approach.
Collaborating with Material Scientists
Engaging with experts ensures access to the latest insights and technologies in material science.
Conducting Material Audits
Regular audits of material performance help identify opportunities for improvement and cost savings.
Asking Suppliers the Right Questions
Clear communication with suppliers about certification, testing, and lead times helps mitigate risks and ensures quality.
By adopting these practices, professionals can optimize the alloy selection process.
Conclusion: Making Informed Choices
Selecting the right heat-resistant alloy requires a thorough understanding of material properties, application requirements, and market trends. By systematically comparing alloys and leveraging tools, standards, and expert insights, decision-makers can achieve optimal outcomes. Whether balancing cost and performance or navigating emerging technologies, a strategic approach ensures success in even the most demanding environments. Explore our resources or share your challenges to continue learning and improving.
FAQ Section
Q1: What are the main industries that use heat-resistant alloys?
A: Aerospace, automotive, power generation, chemical processing, and industrial manufacturing.
Q2: How do I prioritize properties when comparing alloys?
A: Focus on application-specific requirements, such as operating temperature, stress conditions, and exposure to corrosive environments.
Q3: Are high-cost alloys always the best choice?
A: Not necessarily. It depends on the balance of performance needs, cost constraints, and long-term reliability.
Q4: What tools can I use to compare alloy properties?
A: Industry software like Thermo-Calc, CES Selector, or standard comparison charts from certification bodies.
Q5: How does 3D printing impact heat-resistant alloy selection?
A: It enables the use of complex geometries and lightweight structures, often requiring specially formulated alloys.