Designing structural aluminum castings is crucial in modern manufacturing, especially for industries that require lightweight, durable, and cost-effective materials. These castings are used in aerospace, automotive, construction, and numerous other sectors. By designing structural aluminum castings efficiently, manufacturers can optimize performance while ensuring cost-effectiveness and sustainability. In this article, we’ll delve into the various aspects of designing these castings, including manufacturing methods, design considerations, and common challenges. But here’s the kicker: you’ll also discover how to make your designs stand out by overcoming these obstacles and achieving superior results.
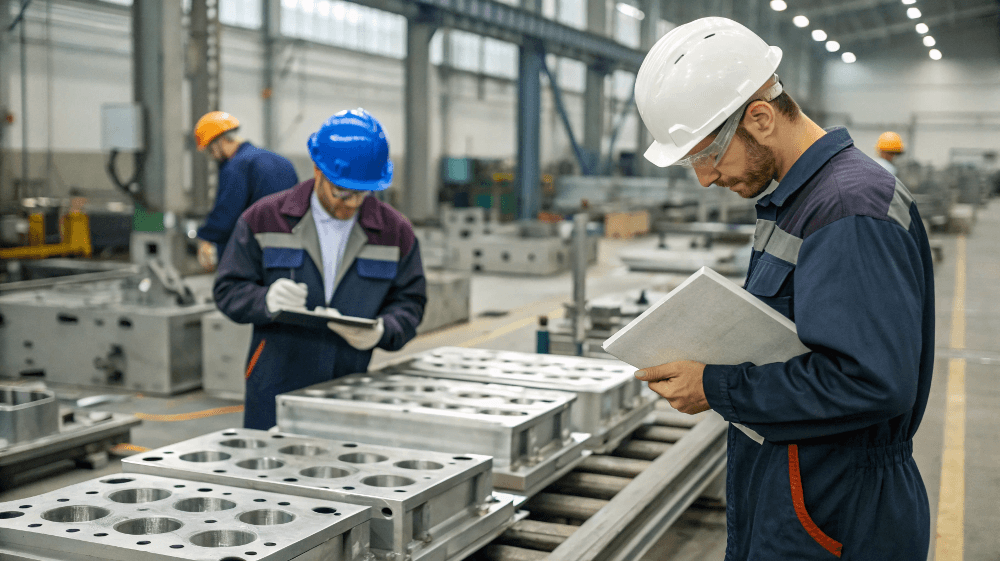
1. What Are Structural Aluminum Castings?
Structural aluminum castings are made from molten aluminum that is poured into molds to create complex shapes used in structural applications. They are highly valued for their strength-to-weight ratio, corrosion resistance, and versatility. What’s the real story behind these castings? Well, aluminum’s low density makes it ideal for applications where weight savings are critical, such as in the aerospace and automotive industries. These castings offer high strength even at low weights, making them an attractive alternative to other materials like steel or plastic.
Ready for the good part? Structural aluminum castings are incredibly versatile, used in everything from bridge components to aircraft parts. They can be produced using a variety of casting methods, each suitable for different applications. These methods include sand casting, die casting, and investment casting, which allow for both large-scale production and the creation of highly detailed components.
Another crucial aspect of structural aluminum castings is their sustainability. Aluminum can be recycled indefinitely without losing its properties, making it an environmentally friendly choice for design. This recycling capability has made aluminum casting popular in industries striving for sustainability. Now, let’s explore why aluminum is so widely used for structural components.
Property | Aluminum Castings | Steel Castings | Plastic Castings |
---|---|---|---|
Weight | Lightweight | Heavier | Lightweight |
Strength-to-Weight | High | Moderate | Low |
Corrosion Resistance | Excellent | Moderate | Low |
Cost | Moderate | High | Low |
2. Why Are Aluminum Castings Used for Structural Designs?
Structural aluminum castings are increasingly used in various industries due to their unique benefits. But here’s the kicker: these castings aren’t just lightweight; they’re strong, cost-effective, and highly adaptable. Ready to learn why manufacturers turn to aluminum?
First and foremost, aluminum’s strength-to-weight ratio is one of its most appealing qualities. It provides the strength required for structural applications without the heaviness of steel. This is particularly beneficial in sectors like aerospace, where every gram counts. Additionally, aluminum’s excellent corrosion resistance ensures that components remain durable and functional over time, even when exposed to harsh environmental conditions. This makes aluminum castings perfect for outdoor applications and marine environments.
What’s the real story? Aluminum castings also offer superior thermal and electrical conductivity compared to other materials like steel. This makes them essential in industries like electronics and power generation. By using aluminum in their designs, companies can achieve performance gains in both efficiency and safety.
Let’s take a closer look at the cost efficiency of aluminum castings. Aluminum is more affordable than high-strength alloys like titanium or certain types of steel, making it the go-to option for manufacturers seeking a cost-effective solution without sacrificing performance. The lightweight nature of aluminum also reduces shipping and handling costs, further lowering overall expenses. Now let’s examine how these advantages translate into the design process.
Factor | Aluminum Castings | Steel Castings | Titanium Castings |
---|---|---|---|
Strength-to-Weight | High | Moderate | Very High |
Cost | Moderate | High | Very High |
Corrosion Resistance | Excellent | Moderate | Excellent |
Weight | Low | High | Low |
3. How Are Structural Aluminum Castings Manufactured?
Manufacturing structural aluminum castings involves a carefully controlled process, where molten aluminum is poured into molds and allowed to solidify. But here’s the kicker: while this process seems straightforward, there are several methods used depending on the complexity and scale of the desired component. Ready for the good part?
One of the most common methods is sand casting, which involves packing sand around a pattern to form a mold. This is ideal for large, simple components but may not be the best choice for complex designs. On the other hand, die casting uses high-pressure to inject molten aluminum into a steel mold, producing parts with high precision. This method is best suited for mass production and applications that require tight tolerances.
Another widely used method is investment casting, which involves creating a detailed pattern and then coating it with a ceramic shell. Once the mold hardens, the pattern is melted out, leaving behind a mold for casting. Investment casting is often used for intricate designs and is preferred in industries like aerospace and medical device manufacturing.
These casting methods each have their own advantages and drawbacks. For example, sand casting is cost-effective for large, simple parts but might not provide the level of precision required for certain high-performance components. On the flip side, die casting and investment casting offer excellent precision but come with higher initial setup costs. Here’s a breakdown of the main aluminum casting methods.
Casting Method | Ideal For | Advantages | Disadvantages |
---|---|---|---|
Sand Casting | Large, simple parts | Cost-effective | Lower precision |
Die Casting | Mass production, high precision | High precision, fast | High setup costs |
Investment Casting | Intricate, detailed parts | High accuracy | Expensive, slower process |
4. What Are the Key Design Considerations for Aluminum Castings?
Designing structural aluminum castings requires careful consideration of several factors to ensure performance and cost-efficiency. What’s the real story behind these considerations? Well, every design decision has implications on the final casting’s strength, durability, and overall cost.
Let’s start with load-bearing capacity. Structural components often need to withstand significant forces, which means the design must account for factors such as stress and strain. Material choice, alloy selection, and wall thickness all play crucial roles in ensuring the final casting can handle the required load. For example, choosing an alloy with higher strength properties can help improve performance without increasing the size of the casting.
Weight is another key consideration. Aluminum is prized for its lightweight properties, but the casting design must still meet the necessary strength requirements. This means designers need to balance material distribution and optimize the geometry of the component to minimize weight while maximizing strength. Corrosion resistance is also vital, particularly in outdoor or marine applications where exposure to the elements is inevitable. Using coatings or selecting corrosion-resistant alloys can help prevent deterioration over time.
Another critical aspect of casting design is manufacturability. Complex designs may require more intricate molds or additional post-processing, which can drive up production costs. By simplifying the design and considering the limitations of the casting process, manufacturers can reduce costs and improve overall efficiency. Now let’s explore how designers ensure the structural integrity of aluminum castings.
Design Factor | Considerations | Impact on Design | Potential Solutions |
---|---|---|---|
Load-Bearing Capacity | Strength of material, thickness | Ensures safety and performance | Alloy selection, reinforcement |
Weight | Material distribution, geometry | Affects performance and cost | Lightweight design |
Corrosion Resistance | Exposure to elements | Longevity of parts | Coatings, alloy choice |
Manufacturability | Complexity of design | Cost of production | Simplify design, optimize mold |
5. How to Optimize the Structural Integrity of Aluminum Castings?
Optimizing the structural integrity of aluminum castings involves ensuring that the final product can withstand the loads and stresses it will encounter in its service life. Ready to learn how? Let’s dive into the key considerations.
The alloy chosen for the casting plays a significant role in determining its strength and durability. Different aluminum alloys have varying properties that can affect the casting’s performance. For example, 356 aluminum alloy is commonly used for structural applications due to its excellent strength and resistance to corrosion. By selecting the right alloy for the specific application, manufacturers can ensure that the casting will perform as expected.
In addition to alloy selection, the design of the casting itself must be optimized to avoid weaknesses like stress concentrators, which can lead to fractures or fatigue failure. Designers often use tools like finite element analysis (FEA) to simulate how the casting will behave under load and identify potential failure points before the part is produced.
Finally, heat treatment processes like aging or annealing can further enhance the strength and durability of aluminum castings. These processes alter the material’s microstructure, improving properties like tensile strength and elongation. By incorporating these processes into the design, manufacturers can optimize the casting for maximum performance.
Optimization Strategy | Benefits | Techniques Used | Application |
---|---|---|---|
Alloy Selection | Enhances strength and durability | Choose high-strength alloys | Aerospace, automotive |
Design Optimization | Prevents failure under load | FEA, stress analysis | Structural components |
Heat Treatment | Increases material strength | Aging, annealing | High-stress applications |
6. What Are the Common Challenges in Designing Structural Aluminum Castings?
Designing structural aluminum castings comes with a set of unique challenges that every designer and manufacturer must overcome. The real story here? Even though aluminum is a fantastic material, its casting process is not without its complications. Let’s dive into these common issues and see how they affect the design process.
One of the biggest challenges in aluminum casting design is controlling casting defects, especially porosity and shrinkage. Porosity refers to the presence of tiny holes in the material that can weaken the final product. These voids occur when gas is trapped during the cooling process. Shrinkage happens as the molten aluminum cools and contracts, which can result in uneven material thickness or distorted shapes. These issues are especially problematic when trying to create highly detailed or thin-walled components.
Another challenge is the material’s inherent thermal expansion and contraction properties. Aluminum expands when heated and contracts as it cools, which can cause deformation or misalignment during the casting process. Managing these thermal properties becomes essential, particularly when designing large, complex parts that must fit together precisely.
But here’s the kicker: designers can overcome these challenges by carefully controlling the cooling process and selecting the right casting technique. For example, die casting and investment casting methods allow for faster cooling rates, which can help reduce shrinkage and porosity. Additionally, the right alloy choice and careful mold design can minimize these issues.
Finally, the complexity of the design itself can pose challenges. Intricate, complex parts often require more detailed molds and can lead to longer production times and higher costs. However, by using advanced software for simulations and analysis, these challenges can be predicted and addressed during the design phase, ensuring smoother production.
Challenge | Issue | Solution |
---|---|---|
Porosity | Trapped gas creates holes | Control gas escape, optimize cooling rate |
Shrinkage | Material contraction during cooling | Use faster cooling rates, adjust design |
Thermal Expansion | Deformation during heating/cooling | Adjust cooling process, alloy selection |
Design Complexity | Increased mold and production costs | Use simulation software, simplify design |
7. How Do Aluminum Alloys Affect the Design of Structural Castings?
Aluminum alloys play a pivotal role in the design of structural castings. What’s the real story here? The selection of the right alloy can significantly impact the performance, durability, and cost-effectiveness of the final casting. Let’s dive into how different alloys affect the design process.
Aluminum alloys are categorized into two main types: wrought alloys and cast alloys. Cast alloys are typically used for structural applications, as they have a high percentage of alloying elements, which enhance specific properties like strength, corrosion resistance, and heat resistance. For example, the 356 alloy is one of the most commonly used in structural aluminum castings due to its high strength and good casting characteristics. It’s perfect for applications requiring high strength, like aerospace and automotive components.
Another popular alloy is 7075, which is known for its high strength and is commonly used in the aerospace industry. However, 7075 is more difficult to cast due to its higher strength and lower ductility, which requires more careful design and manufacturing techniques.
So, what’s the real kicker? Choosing the right alloy means balancing strength, weight, and cost. The higher the strength of the alloy, the more it may cost and the harder it may be to cast. On the other hand, using a lower-strength alloy may reduce material costs, but it could affect the component’s ability to withstand stress or load.
Alloy | Strength | Typical Uses | Key Properties |
---|---|---|---|
356 | High | Aerospace, automotive | High strength, good corrosion resistance |
7075 | Very High | Aerospace, military applications | High strength, tough to cast |
6061 | Moderate | General manufacturing, structural | Good corrosion resistance, weldable |
8. What Are the Best Practices for Ensuring Quality in Aluminum Casting Designs?
Ensuring the quality of aluminum castings requires more than just selecting the right alloy or casting method. What’s the real story? It’s about adopting best practices throughout the entire design, production, and post-production processes to guarantee the best possible results.
One essential practice is material selection. Choosing high-quality, high-purity aluminum can reduce the likelihood of defects such as porosity or inclusions. Furthermore, using advanced casting techniques like vacuum-assisted casting or pressure die casting can significantly improve the quality of the castings by ensuring uniform material flow and minimizing defects.
The next step is ensuring design optimization. A simplified and efficient design can reduce the likelihood of issues arising during casting and finishing. This involves considering the mold design, material distribution, and minimizing the use of complex features that may add unnecessary cost or increase production time.
But here’s where it gets interesting: the post-production phase is just as critical. Surface finish, heat treatment, and quality inspection all play a major role in ensuring that the final product meets the necessary standards. Post-production processes like shot blasting or coating can improve the surface quality and enhance corrosion resistance, while heat treatment can further increase the material’s strength.
Finally, integrating technology like 3D printing or digital twin simulations can also improve quality by allowing for precise design and testing. These technologies help identify potential problems early in the design phase, ensuring that the final casting is defect-free and performs as expected.
Quality Practice | Benefit | Application |
---|---|---|
Material Selection | Reduces defects | Use high-purity aluminum |
Design Optimization | Minimizes production issues | Simplify design, optimize mold |
Post-Production | Enhances durability and strength | Surface finishing, heat treatment |
Technology Integration | Improves precision and testing | 3D printing, digital twin simulations |
9. How Does the Casting Process Impact the Final Design?
The casting process has a significant impact on the final design of aluminum components. Ready for the good part? The method you choose will directly affect the precision, strength, and appearance of the finished product. Let’s take a closer look at how these factors come into play.
The first thing to consider is the precision of the casting method. Different methods provide varying levels of accuracy. For example, investment casting is known for its ability to produce highly detailed parts with tight tolerances, making it ideal for industries where precision is paramount, like aerospace or medical devices. On the other hand, sand casting is better suited for large, simpler parts, as it does not provide the same level of detail as other methods.
The cooling rate also plays a crucial role in the final design. Materials like aluminum expand and contract during cooling, which can lead to warping or dimensional changes. Fast cooling rates, as seen in die casting, can reduce the chances of deformation but may result in casting defects like porosity. Conversely, slow cooling rates may reduce the risk of defects but could cause other issues, such as increased shrinkage.
Designers need to factor in these potential impacts when creating the component. A well-planned mold design can help minimize defects and improve the overall quality of the casting. Also, choosing the right alloy and casting method for the application ensures that the component will meet both performance and cost objectives.
Casting Method | Precision | Cooling Rate | Ideal Use |
---|---|---|---|
Investment Casting | Very High | Slow | Complex, high-precision parts |
Die Casting | High | Fast | Mass production, tight tolerances |
Sand Casting | Moderate | Moderate | Large, simple components |
10. What Are the Cost Implications of Designing Structural Aluminum Castings?
When designing structural aluminum castings, cost is always a major consideration. What’s the real story? While aluminum is cost-effective compared to other materials, the casting process itself can be expensive, depending on the complexity of the design and the chosen manufacturing method. Let’s explore the key cost factors and how they impact the final price.
The first cost factor is material selection. Aluminum is generally more affordable than other materials like steel or titanium. However, the specific alloy chosen can significantly influence the price. High-performance alloys tend to be more expensive due to their improved properties, such as strength, corrosion resistance, and heat tolerance.
Next, the choice of casting method plays a large role in determining costs. Sand casting is typically the least expensive method, but it may not be suitable for intricate designs. On the other hand, die casting and investment casting provide higher precision but come with higher initial setup costs and longer production times. These methods are more suited for mass production, where the cost per part decreases as volume increases.
Finally, post-production processes like finishing, heat treatment, and inspection add to the overall cost. While these processes enhance the quality and durability of the casting, they also increase the time and resources required for production. By optimizing the design and selecting the right manufacturing method, it’s possible to minimize costs while ensuring that the final product meets the necessary performance standards.
Cost Factor | Impact on Design | Solution |
---|---|---|
Material Selection | Increases or decreases cost | Choose cost-effective alloys |
Casting Method | Determines precision and volume | Select optimal method based on part complexity |
Post-Production | Increases overall cost | Minimize unnecessary processes |
11. How to Ensure Environmental Sustainability in Aluminum Casting Design?
Environmental sustainability is a growing concern in all industries, and aluminum casting is no exception. What’s the kicker here? Aluminum is one of the most sustainable materials available, with the ability to be recycled indefinitely without losing its properties. Let’s explore how you can ensure that your aluminum casting designs are both eco-friendly and cost-effective.
The first step in promoting sustainability is using recycled aluminum in your castings. This reduces the demand for virgin materials and lowers the environmental impact of production. Recycling aluminum uses significantly less energy than producing new aluminum, which reduces both carbon emissions and energy consumption.
Another important factor is the design itself. By designing components with recycling in mind, manufacturers can reduce waste and make it easier to recycle the product at the end of its life cycle. This includes optimizing the material distribution and avoiding excessive use of non-recyclable coatings or additives.
Energy efficiency in the casting process is also a critical aspect of sustainability. Implementing energy-efficient technologies and optimizing the casting process can significantly reduce the environmental impact of production. Additionally, choosing casting methods that use less energy, such as die casting, can further improve sustainability.
Sustainability Factor | Benefits | Application |
---|---|---|
Recycled Aluminum | Reduces material costs and environmental impact | Use in casting production |
Design for Recycling | Reduces waste, facilitates reuse | Optimize material use |
Energy Efficiency | Lowers carbon emissions | Implement energy-efficient casting methods |
12. What Software Tools Can Help in Designing Structural Aluminum Castings?
Designing structural aluminum castings requires precision and accuracy, and software tools can play a vital role in ensuring the success of the design. What’s the real story? Well, these tools allow designers to simulate and test their designs before production, saving time and costs while improving accuracy. Let’s look at some of the top software tools that can assist in the design process.
Computer-Aided Design (CAD) software is a must-have for casting designers. CAD software allows designers to create detailed 3D models of their parts, which can be manipulated and refined before the casting process begins. Popular CAD tools like AutoCAD, SolidWorks, and CATIA are widely used in the industry for this purpose.
Simulation tools like CAE (Computer-Aided Engineering) can further enhance the design process by providing insights into how the part will behave under various conditions. These tools simulate factors like stress, thermal expansion, and flow patterns during the casting process. By using CAE software, designers can identify potential issues in their designs and make necessary adjustments before manufacturing begins.
Ready for the good part? Advanced simulation tools can also be used to optimize the casting process itself. Software that simulates the flow of molten metal into molds can help reduce defects like porosity and ensure a better quality final product.
Software Tool | Function | Benefits |
---|---|---|
CAD Software | Design 3D models | Detailed part visualization |
CAE Software | Simulate stresses and flows | Optimizes design, identifies issues |
Casting Simulation | Simulate molten metal flow | Improves mold design, reduces defects |
13. How Can Advanced Technologies Improve Structural Aluminum Casting Design?
The introduction of advanced technologies is transforming the world of aluminum casting design. What’s the kicker? These technologies provide designers with the tools they need to push the boundaries of performance and efficiency, ensuring that their castings are both cost-effective and highly functional.
Artificial intelligence (AI) and machine learning are making their way into the casting industry, helping to optimize design processes. AI can predict how a component will perform based on various parameters and suggest design improvements. For example, AI can help identify weaknesses in a design that may not be immediately obvious, improving the strength and durability of the final casting.
Automation is another game-changer. Automated systems can speed up the casting process, reducing production times and costs. These systems can also improve consistency and accuracy, ensuring that each part is produced to the same high standards. Automated inspection systems, for example, can detect defects early in the process, preventing costly rework.
The real kicker here is that these technologies also make the casting process more sustainable. By optimizing production techniques and improving efficiency, manufacturers can reduce waste and energy consumption, making the entire process more eco-friendly.
Technology | Benefits | Application |
---|---|---|
AI | Optimizes design, predicts performance | Casting design and testing |
Automation | Speeds up production, ensures consistency | Manufacturing, inspection |
Smart Sensors | Monitors quality and defects | Quality control, defect detection |
14. What Are the Future Trends in Structural Aluminum Casting Design?
The future of structural aluminum casting design is filled with exciting possibilities. What’s the real story? Well, the constant innovation in materials, manufacturing techniques, and technologies is pushing the industry to new heights. Let’s explore what’s coming next in the world of aluminum castings.
One of the most exciting trends is the rise of 3D printing in casting. 3D printing allows designers to create complex geometries that would be difficult or impossible to achieve with traditional casting methods. This technology enables rapid prototyping, faster design iterations, and even on-demand manufacturing, reducing lead times and costs.
Another key trend is the development of new aluminum alloys designed for even higher performance. These alloys are specifically engineered to withstand extreme temperatures, high pressures, and corrosive environments. As these advanced alloys become more widely available, the potential applications for structural aluminum castings will continue to expand.
Finally, sustainability will remain at the forefront of aluminum casting design. With the growing demand for eco-friendly solutions, manufacturers are focusing on reducing energy consumption, minimizing waste, and using recycled materials. These trends are expected to shape the future of the industry for years to come.
Trend | Impact | Potential Applications |
---|---|---|
3D Printing | Enables complex designs, rapid prototyping | Aerospace, automotive |
Advanced Alloys | Improves performance, withstands harsh conditions | High-performance parts |
Sustainability | Reduces waste, energy consumption | Eco-friendly manufacturing |
15. How to Avoid Common Mistakes When Designing Structural Aluminum Castings?
Avoiding common mistakes in aluminum casting design is crucial to ensure high-quality results. What’s the kicker here? Even minor design flaws can lead to defects that compromise the performance and safety of the component. Let’s dive into how to avoid these pitfalls.
The first mistake many designers make is overcomplicating the design. Complex features such as intricate geometries or thin walls can increase the likelihood of casting defects like porosity and warping. Simplifying the design can reduce production time and costs, while also improving the quality of the casting.
Another common mistake is neglecting to consider the cooling process. Aluminum expands when heated and contracts as it cools. If this thermal expansion and contraction aren’t accounted for in the design, the component could end up warped or out of specification. By carefully planning the cooling process, designers can avoid these issues.
Finally, it’s important not to overlook the material selection. Choosing the wrong alloy can result in a weaker or less durable casting. Always select an alloy that’s suitable for the specific application and provides the necessary strength, corrosion resistance, and heat tolerance.
Mistake | Impact | Solution |
---|---|---|
Overcomplicating Design | Increased defects, higher costs | Simplify design, optimize features |
Ignoring Cooling Process | Warping, dimensional changes | Plan cooling carefully |
Incorrect Alloy Selection | Reduced durability, strength | Choose the right alloy |
FAQ
Q1: What are structural aluminum castings?
Structural aluminum castings are components made from molten aluminum, poured into molds to form shapes used in structural applications. They are known for being lightweight, strong, and corrosion-resistant, making them ideal for industries like aerospace and automotive.
Q2: How does the casting process for aluminum work?
The aluminum casting process involves pouring molten aluminum into a mold. The metal solidifies to form the desired shape, with various methods like sand casting, die casting, and investment casting being used depending on the complexity of the design.
Q3: What benefits does aluminum offer for structural designs?
Aluminum provides an excellent strength-to-weight ratio, corrosion resistance, and durability. It is also cost-effective, lightweight, and suitable for a wide range of applications, making it ideal for structural components that require strength without added weight.
Q4: How do you optimize the structural integrity of aluminum castings?
Structural integrity can be optimized by selecting the right alloy, designing components to avoid stress concentrations, and using heat treatments like aging and annealing to enhance the material’s strength and durability.
Q5: What are common challenges in designing aluminum castings?
Common challenges include ensuring adequate load-bearing capacity, managing material distribution for weight reduction, preventing corrosion, and simplifying complex designs to reduce manufacturing costs.