Introduction
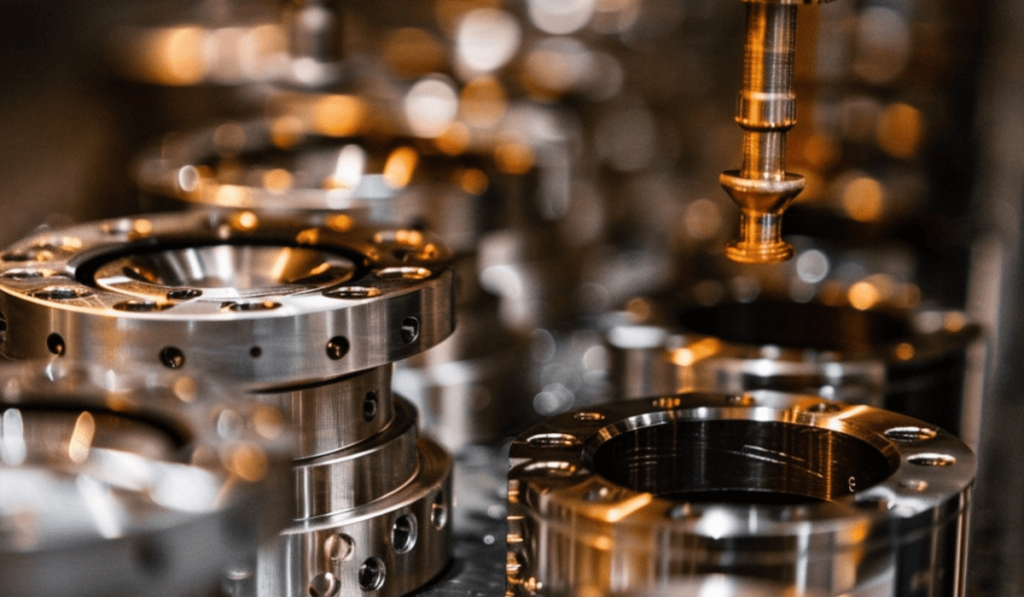
Understanding the properties of heat-resistant alloys is crucial in modern engineering. These materials are the backbone of industries like aerospace, automotive, and power generation, where extreme temperatures push conventional materials to their limits. Without heat-resistant alloys, equipment failure would be inevitable in high-temperature applications, leading to costly downtime and safety risks. This article offers a deep dive into the methods, testing standards, and practical insights required to evaluate these critical materials. Whether you’re a technician or a decision-maker, this guide equips you with everything you need to know about assessing the properties of heat-resistant alloys.
What Are Heat-Resistant Alloys?
Definition and Composition
Heat-resistant alloys are specialized materials designed to maintain strength, resist oxidation, and endure high temperatures without deforming or failing. They typically include elements like nickel, chromium, cobalt, and molybdenum, which enhance their ability to withstand extreme conditions. These elements contribute to the alloy’s melting point, mechanical integrity, and resistance to thermal degradation.
Examples of Heat-Resistant Alloys
Common examples include Inconel, known for its corrosion resistance and mechanical stability, and Hastelloy, which excels in chemical industries for its ability to resist oxidizing agents. Stainless steels such as 310 and 347 grades are also widely used due to their cost-effectiveness and adequate performance in moderately high temperatures.
Applications in Key Industries
Industries that rely heavily on heat-resistant alloys include aerospace, where they are used in jet engines and turbine blades. In automotive manufacturing, they serve critical roles in exhaust systems and turbochargers. Power plants use these materials in boilers, heat exchangers, and reactors to ensure safe and efficient operations. Without these alloys, many of these technologies would fail under the harsh conditions they endure daily.
Why These Alloys Are Indispensable
The unique properties of heat-resistant alloys allow them to operate in conditions where standard metals would fail. They offer not only safety and reliability but also the potential for innovation, enabling industries to push boundaries in performance and efficiency. By understanding their composition and application, you can better appreciate the value these materials bring to modern engineering.
Why Do We Need Heat-Resistant Alloys?
The Challenges of High-Temperature Applications
High-temperature environments pose unique challenges, such as thermal expansion, corrosion, and mechanical fatigue. Materials exposed to extreme heat often experience structural changes that compromise their integrity. For example, regular steel begins to weaken at temperatures above 400°C, making it unsuitable for many industrial applications.
Preventing Catastrophic Failures
One of the most critical reasons for using heat-resistant alloys is to prevent catastrophic failures. For instance, in jet engines, components experience temperatures exceeding 1,000°C. Without alloys like Inconel, these parts would melt or deform, leading to engine failure and potential safety hazards.
Economic and Safety Benefits
Investing in heat-resistant alloys saves money in the long term by reducing maintenance costs and prolonging equipment lifespan. They also enhance safety by minimizing the risk of failure in critical applications such as nuclear reactors or chemical processing plants, where accidents can have severe consequences.
Case Studies of Failures
Several historical incidents highlight the importance of these materials. For example, poorly selected materials in turbine blades led to several power outages in the 1990s. These failures underscore the necessity of using properly tested and certified heat-resistant alloys to meet operational demands.
Innovations Made Possible
Heat-resistant alloys are not just a necessity—they are a gateway to innovation. Their use enables the development of more efficient power plants, higher-performance vehicles, and advanced aerospace technologies. As industries push for greater efficiency and sustainability, these materials will play an increasingly vital role.
Properties That Make Alloys Heat-Resistant
High Melting Points
One of the defining features of heat-resistant alloys is their high melting points. Nickel and cobalt-based alloys, for instance, can endure temperatures upwards of 1,200°C, making them ideal for applications like gas turbines and industrial furnaces.
Oxidation and Corrosion Resistance
Heat-resistant alloys are engineered to resist oxidation, which occurs when metals react with oxygen at high temperatures. Chromium, a key element in many of these alloys, forms a protective oxide layer that shields the material from further degradation.
Retention of Mechanical Strength
Mechanical strength at elevated temperatures is another critical property. This ensures that components retain their load-bearing capacity under extreme heat. For example, molybdenum enhances the creep resistance of alloys, allowing them to perform reliably over long periods.
Thermal Fatigue Resistance
Thermal fatigue occurs due to repeated heating and cooling cycles, which cause micro-cracks in materials. Heat-resistant alloys are designed to withstand these stresses, ensuring durability in applications like engine exhaust systems and industrial kilns.
Thermal Conductivity and Expansion
The thermal conductivity of an alloy determines how effectively it can dissipate heat, while thermal expansion measures how much it expands when heated. These properties are crucial in applications where dimensional stability is critical, such as precision machinery and high-performance engines.
Tailored Properties Through Alloying
By adjusting the composition of elements like nickel, iron, and cobalt, manufacturers can tailor the properties of heat-resistant alloys to meet specific requirements. This flexibility makes them indispensable across a wide range of industries and applications.
Overview of Testing Methods for Heat-Resistant Alloys
Importance of Testing
Testing is the cornerstone of determining whether a heat-resistant alloy meets the required performance criteria. It ensures that the material can withstand the intended operating conditions, thereby preventing costly failures and ensuring safety.
Categories of Testing
Testing methods can be broadly categorized into mechanical, chemical, and thermal analyses. Each category addresses specific properties that are critical for high-temperature performance.
Role of Standardization
Standardized testing, guided by organizations like ASTM and ISO, ensures consistency and reliability. It provides a framework for comparing materials and verifying that they meet industry requirements.
Laboratory vs. Field Testing
Laboratory testing offers controlled conditions for precise measurements, while field testing simulates real-world applications to validate performance. Both approaches are essential for comprehensive evaluation.
Common Testing Challenges
Challenges in testing include replicating extreme conditions, ensuring sample consistency, and interpreting results accurately. Advanced equipment and skilled technicians are critical for overcoming these hurdles and obtaining reliable data.
Advancements in Testing Technology
Technological advancements, such as non-destructive testing methods and high-resolution imaging, have significantly improved the accuracy and efficiency of testing heat-resistant alloys. These innovations enable faster and more detailed assessments, benefiting both manufacturers and end-users.
Thermal Conductivity and Its Measurement
What Is Thermal Conductivity?
Thermal conductivity is a material’s ability to transfer heat. In heat-resistant alloys, this property determines how well the material can dissipate heat, which is critical in applications like turbine blades and heat exchangers. Efficient thermal conductivity ensures that heat is managed effectively, reducing thermal stress and preventing failure.
Why It Matters in High-Temperature Applications
Poor thermal conductivity can lead to overheating in critical areas, causing stress and potential cracks. For example, in jet engines, uneven heat distribution can degrade performance and increase maintenance costs. Understanding and measuring thermal conductivity helps engineers design systems that operate reliably under extreme conditions.
Methods to Measure Thermal Conductivity
Several techniques are used to measure thermal conductivity. Laser flash analysis is a common method, especially for metals and alloys. This technique measures the time it takes for heat to pass through a sample, providing precise data on thermal conductivity. Another widely used method is the guarded hot plate, where a sample is sandwiched between two plates at different temperatures, and heat flow is measured.
Standards for Thermal Conductivity Tests
Thermal conductivity testing follows strict standards to ensure accuracy and repeatability. Standards such as ASTM E1952 outline procedures for laser flash analysis, while ASTM C518 governs guarded hot plate methods. Adherence to these standards ensures that data is reliable and can be compared across different materials.
Real-World Applications of Thermal Conductivity
In power plants, heat exchangers rely on materials with high thermal conductivity to transfer heat efficiently. Similarly, in automotive exhaust systems, alloys with good conductivity help manage heat generated during operation, enhancing performance and longevity. These practical applications underscore the importance of accurate thermal conductivity measurements.
Challenges and Advancements
Challenges in measuring thermal conductivity include ensuring sample uniformity and accounting for factors like surface roughness and temperature gradients. Advances in technology, such as high-resolution sensors and computational modeling, have improved measurement accuracy, enabling better material design and application.
High-Temperature Tensile Testing
The Importance of Tensile Testing
Tensile testing evaluates how a material behaves under stress, specifically its ability to stretch or deform before breaking. At high temperatures, this test becomes critical as materials often lose strength, making it essential to understand their limits in extreme conditions.
How Tensile Testing Works
During a tensile test, a sample is placed in a testing machine and subjected to a pulling force until it breaks. The test measures properties like ultimate tensile strength, yield strength, and elongation. These parameters provide insights into the material’s performance under load.
High-Temperature Considerations
At elevated temperatures, alloys may exhibit different behavior compared to room-temperature conditions. For instance, metals like stainless steel might lose ductility, while nickel-based alloys retain their strength. High-temperature tensile tests simulate operational conditions to ensure accurate performance predictions.
Standards for Tensile Testing
ASTM E21 is the primary standard for tensile testing of metals at high temperatures. It specifies procedures for sample preparation, testing conditions, and result interpretation. Following these standards ensures consistency and reliability across tests.
Applications in Industry
Tensile testing is widely used in aerospace, automotive, and power generation industries. For example, in jet engines, turbine blades must endure extreme stress and temperatures without deforming. Tensile tests validate their suitability, ensuring safety and performance.
Innovations in Tensile Testing
Modern tensile testing machines incorporate advanced features like high-temperature chambers and digital sensors for precise measurements. These innovations improve test accuracy and provide detailed data for material selection and design optimization.
Oxidation and Corrosion Resistance Testing
Why Test for Oxidation and Corrosion?
Oxidation and corrosion are major concerns in high-temperature environments. These processes degrade materials, reducing their lifespan and performance. Testing for resistance ensures that alloys can withstand harsh conditions without significant deterioration.
Common Testing Methods
One method is cyclic oxidation testing, where a sample is repeatedly heated and cooled to simulate real-world conditions. Another approach is weight loss measurement, which tracks material degradation over time. Both methods provide valuable data on an alloy’s durability.
Standards for Oxidation and Corrosion Tests
Standards such as ASTM G54 outline procedures for evaluating oxidation resistance. These standards ensure that tests are conducted consistently, providing reliable data for material comparison.
Practical Applications
In chemical plants, heat exchangers operate in corrosive environments. Testing ensures that materials like Hastelloy can resist these conditions, maintaining efficiency and safety. Similarly, in power plants, oxidation resistance tests validate the performance of alloys in boilers and turbines.
Innovations in Testing
Advancements in testing include real-time monitoring using sensors and imaging technologies. These tools provide more detailed insights into how materials behave under oxidative and corrosive conditions, enabling better material development.
Creep Resistance
What Is Creep?
Creep is the slow, permanent deformation of a material under constant stress at high temperatures. It is a critical factor in applications like power plants, where components must endure prolonged exposure to heat and stress.
How Creep Resistance Is Measured
Creep resistance is tested by subjecting a sample to a constant load at a specified temperature over time. The test measures deformation rates, providing data on the material’s ability to maintain its shape and strength under prolonged stress.
Standards for Creep Testing
ASTM E139 is the standard for creep testing of metals. It outlines procedures for conducting tests, including sample preparation, testing conditions, and data analysis. Adhering to these standards ensures accuracy and comparability of results.
Real-World Implications
In gas turbines, creep resistance determines how long components like blades can operate without deformation. Materials with high creep resistance reduce maintenance needs and enhance operational efficiency.
Advances in Creep Testing
Modern creep testing machines feature advanced controls and sensors for precise measurements. Computational modeling is also used to predict creep behavior, enabling better material selection and design.
Hardness Testing for Heat-Resistant Alloys
Why Hardness Matters
Hardness indicates a material’s resistance to deformation and wear, which is crucial for components exposed to mechanical stress at high temperatures. Testing hardness provides insights into an alloy’s durability and performance.
Common Hardness Testing Methods
Brinell, Rockwell, and Vickers are the most common hardness tests. Each method involves indenting the material’s surface with a specific force and measuring the resulting impression. These tests are quick, reliable, and widely used across industries.
Standards for Hardness Testing
ASTM E10, E18, and E92 govern the Brinell, Rockwell, and Vickers methods, respectively. These standards ensure consistent testing procedures and reliable results.
Applications in Industry
In automotive manufacturing, hardness tests validate materials for engine components. In aerospace, they ensure that alloys can withstand mechanical stress during operation.
Innovations in Hardness Testing
Portable hardness testers and automated systems have made testing faster and more efficient. These advancements enable on-site evaluations, reducing downtime and improving material selection.
Conclusion
Determining the properties of heat-resistant alloys is essential for ensuring safety, performance, and efficiency in high-temperature applications. Through a combination of thermal, mechanical, and chemical tests, engineers can accurately assess an alloy’s suitability for specific conditions. With advancements in testing technology, these evaluations are becoming more precise and efficient, enabling better material development and application. Ready to optimize your material selection process? Contact our team for expert advice and testing services.
FAQ Section
What industries use heat-resistant alloys most?
Aerospace, automotive, and power generation are the primary industries relying on heat-resistant alloys for their high-temperature applications.
How is thermal conductivity measured?
Common methods include laser flash analysis and guarded hot plate tests, which provide precise measurements of heat transfer properties.
Why is creep resistance important?
Creep resistance ensures that materials maintain their shape and strength under prolonged stress at high temperatures, essential for components like turbine blades.
What are common standards for testing these alloys?
Standards like ASTM E21 for tensile testing, E139 for creep resistance, and G54 for oxidation testing ensure consistent and reliable results.
Are there emerging trends in testing heat-resistant alloys?
Yes, advancements like real-time monitoring, computational modeling, and portable testing devices are improving the accuracy and efficiency of evaluations.