Introduction
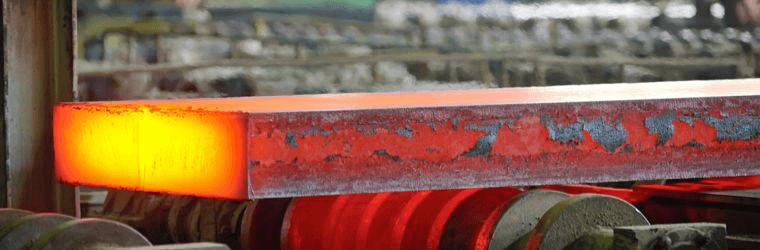
Heat-resistant alloys play a critical role in industries where materials must perform under extreme thermal conditions. From aerospace to power generation, these alloys enable applications where durability and reliability are non-negotiable. This article explores the science, methods, and considerations involved in evaluating the strength of these materials at varying temperatures. Whether you’re an engineer or a materials scientist, this guide provides practical insights into the properties, testing techniques, and real-world applications of heat-resistant alloys. By understanding how these alloys behave under thermal stress, you can make informed decisions for your projects.
Understanding Heat-Resistant Alloys
Definition and Importance
Heat-resistant alloys are materials engineered to retain their mechanical strength and resist degradation at high temperatures. Unlike standard metals, which can lose structural integrity when heated, these alloys are designed to withstand prolonged exposure to extreme thermal environments. Applications for these materials include jet engines, nuclear reactors, and industrial furnaces.
Types of Heat-Resistant Alloys
Several categories of heat-resistant alloys exist, each tailored to specific conditions:
- Stainless Steels: Known for their corrosion resistance and moderate heat resistance, stainless steels like 304 and 316 grades are widely used.
- Nickel-Based Alloys: These include Inconel and Hastelloy, designed for high-performance applications requiring exceptional strength at temperatures exceeding 1,000°C.
- Titanium Alloys: Lightweight and heat-tolerant, these alloys are common in aerospace applications.
Key Properties
Heat-resistant alloys derive their strength from a combination of physical and chemical attributes:
- High Melting Points: These alloys can maintain their form and function near their melting temperatures.
- Oxidation Resistance: Alloying elements like chromium form a protective oxide layer that prevents surface degradation.
- Creep Resistance: They exhibit minimal deformation under prolonged mechanical stress.
Relevance to Industry
Industries relying on heat-resistant alloys depend on their performance to ensure safety and efficiency. For instance, jet turbines must operate flawlessly under fluctuating thermal loads. Similarly, power plants require materials that can endure high-pressure steam without failing.
By understanding the composition, structure, and applications of heat-resistant alloys, professionals can select the best materials for specific operational challenges.
Fundamental Properties of Heat-Resistant Alloys
Tensile Strength
Tensile strength measures the maximum stress an alloy can withstand without breaking. For heat-resistant alloys, tensile strength is a critical factor as it indicates the material’s ability to handle mechanical loads even at high temperatures. This property depends on the alloy’s microstructure, which stabilizes under heat.
Creep Resistance
Creep refers to the gradual deformation of a material under constant stress over time. At elevated temperatures, even strong materials may deform. Heat-resistant alloys mitigate this with grain structures that inhibit movement at the atomic level. Creep testing typically involves prolonged exposure to stress in a controlled thermal environment, simulating real-world conditions.
Thermal Stability
Thermal stability ensures an alloy maintains its mechanical properties over extended periods of heat exposure. For example, nickel-based superalloys retain strength through solid-solution strengthening, precipitation hardening, and protective oxide layers.
Oxidation and Corrosion Resistance
At high temperatures, oxidation and corrosion can rapidly degrade materials. Heat-resistant alloys contain elements like chromium, aluminum, and silicon that form stable oxide layers, acting as shields against environmental damage.
Ductility and Toughness
Even under thermal stress, these alloys must remain ductile and tough to avoid catastrophic failure. Ductility allows materials to deform without breaking, while toughness ensures they can absorb energy during impact.
Measurement Standards
Industries adhere to standards like ASTM E21 and ISO 204 to quantify these properties under high temperatures. These standardized methods ensure consistency and reliability in assessing alloy performance.
Temperature Ranges and Industrial Applications
Low-Temperature Applications
Some heat-resistant alloys perform in moderate thermal environments, such as automotive exhaust systems. Stainless steels like 409 and 439 grades exhibit sufficient strength and corrosion resistance at temperatures below 500°C.
Medium-Temperature Applications
Industries such as chemical processing and marine environments demand materials that withstand temperatures between 500°C and 1,000°C. Nickel-based alloys like Incoloy are ideal for such conditions due to their robust oxidation resistance.
High-Temperature Applications
Applications above 1,000°C, such as jet engines and gas turbines, require alloys capable of extraordinary performance. Superalloys like Inconel 718 excel in these conditions, offering unmatched creep resistance and thermal stability.
Matching Applications to Alloys
Selecting the right alloy involves understanding operational demands:
- Aerospace: Lightweight titanium alloys for high-strength components.
- Power Generation: Nickel-based alloys for turbines and boilers.
- Automotive: Stainless steel for exhaust manifolds and catalytic converters.
Challenges in Selection
Matching an alloy to its intended environment involves balancing factors like cost, machinability, and performance under cyclic thermal stresses. Collaborating with material scientists ensures optimal choices.
Factors Affecting Alloy Strength at High Temperatures
Microstructural Changes
Elevated temperatures can alter an alloy’s microstructure, affecting its mechanical properties. Grain growth, phase transformations, and precipitate coarsening reduce strength. Alloy engineers counteract these changes by designing materials with stable microstructures.
Stress and Fatigue
Repeated thermal cycling causes thermal fatigue, a phenomenon where materials crack under fluctuating temperatures. Advanced alloys incorporate elements like cobalt and molybdenum to reduce stress concentrations and improve fatigue resistance.
Oxidation and Surface Reactions
Surface oxidation compromises structural integrity, especially in high-temperature environments. Engineers address this by using alloys with self-healing oxide layers, ensuring prolonged durability.
Prolonged Exposure Risks
Long-term exposure to extreme temperatures accelerates creep deformation and microstructural degradation. Periodic inspections and predictive modeling are essential to monitor alloy performance.
Managing Thermal Loads
Designers must account for thermal expansion and contraction to avoid stress-induced failures. Using compatible alloys in assemblies minimizes mismatched expansion coefficients, reducing risks.
By recognizing these factors, engineers can predict and mitigate potential weaknesses in heat-resistant alloys under extreme conditions.
Why Strength Testing is Crucial
Ensuring Safety and Reliability
Strength testing of heat-resistant alloys guarantees safety in critical applications. Whether it’s a power plant boiler or a jet engine, failure under high temperature could result in catastrophic consequences. This is particularly vital in industries like aerospace, where materials endure both extreme temperatures and mechanical stress during operation. Testing ensures that these materials meet performance benchmarks before deployment.
Avoiding Costly Failures
In industries like petrochemicals and power generation, a failed alloy component can lead to significant financial losses. Downtime for repairs or replacements is expensive, and unscheduled maintenance disrupts operations. Testing alloys thoroughly reduces the likelihood of such unexpected failures, saving money and resources in the long term.
Industry Standards and Compliance
Testing aligns alloy performance with global standards like ASTM E139 for creep and ASTM E21 for elevated temperature tensile tests. Adhering to these benchmarks is not just about meeting regulations but also about instilling confidence in clients and stakeholders. Industries with rigorous safety and quality protocols, such as aviation, depend on tested materials to maintain compliance and credibility.
Real-World Applications Demonstrating Importance
Consider the space exploration sector. Rocket engines experience temperatures exceeding 1,500°C, demanding materials that are not only heat-resistant but also highly durable under stress. Without extensive testing, such alloys would be prone to failure. Similarly, steam turbines in power plants operate continuously at high temperatures and pressures; their efficiency depends on materials verified for these conditions.
Common Testing Standards and Protocols
Overview of Testing Standards
Testing protocols such as ASTM and ISO ensure consistency in evaluating alloys. ASTM E8 focuses on tensile testing, while ASTM E139 provides guidelines for creep testing at high temperatures. Standards like these offer clear procedures for assessing strength, elongation, and fracture characteristics.
ASTM vs. ISO: Key Differences
While ASTM standards are widely recognized in North America, ISO standards find broader application globally. Both aim to ensure alloy reliability but may differ slightly in testing methodologies. For example, ASTM E21 emphasizes high-temperature tensile testing, whereas ISO 204 prioritizes creep behavior under load. Engineers must choose protocols aligned with their project’s regional requirements.
Consistency Through Standards
By standardizing testing, industries achieve comparable results across labs and organizations. This enables engineers to predict material behavior accurately and ensures that alloys perform consistently under diverse conditions.
Case Studies of Standards in Action
A leading aerospace company recently adopted ASTM E292 for creep testing on turbine blades. The results provided critical insights into alloy endurance, leading to improved engine efficiency. In another example, the power generation sector utilized ISO 204 for boiler materials, enhancing their lifespan and reducing maintenance intervals.
Why Strength Testing is Crucial
Ensuring Safety and Reliability
Strength testing is a non-negotiable step in ensuring the safety and reliability of heat-resistant alloys in real-world applications. In industries like aerospace and power generation, where these materials are exposed to extreme thermal stress, failure is not an option. Testing reveals the limits of the alloy under stress, heat, and long-term usage. For instance, jet engines operate at temperatures over 1,500°C, demanding materials that can endure without deforming or failing. By evaluating alloys in controlled conditions, manufacturers can verify that the material will perform reliably under expected—and unexpected—circumstances.
Avoiding Financial and Operational Risks
Failures caused by inadequate testing can lead to enormous financial losses. Consider an industrial furnace made with an insufficiently tested alloy: a structural failure might halt production for weeks, requiring costly repairs and disrupting supply chains. By identifying material weaknesses before deployment, strength testing prevents such costly scenarios. The economic benefits extend to reducing warranty claims and bolstering customer trust through dependable performance.
Meeting Industry Standards
Heat-resistant alloys must adhere to stringent industry standards to ensure widespread applicability and acceptance. Standards like ASTM E21 (tensile testing at elevated temperatures) and ISO 6892-2 (metallic material testing) define procedures to evaluate mechanical properties effectively. Following these protocols guarantees the materials are capable of withstanding the rigors of their intended environment, from high-pressure turbines to molten metal containment.
Real-Life Examples of Critical Failures
Historical examples underline the importance of strength testing. The 1986 Challenger disaster involved O-rings failing due to temperature extremes, highlighting the importance of thermal performance testing. Although not an alloy, the principle is the same: without thorough evaluation, even minor weaknesses can result in catastrophic outcomes. Similarly, boiler explosions caused by creep failures illustrate why creep testing is essential for pressure vessels and high-temperature equipment.
Common Testing Standards and Protocols
The Role of Standards
Standards provide a framework for evaluating heat-resistant alloys uniformly. They establish methods, benchmarks, and acceptable tolerances, enabling engineers to determine whether materials meet operational requirements. Standards like ASTM, ISO, and DIN govern testing for tensile strength, creep resistance, and thermal stability, making them indispensable in materials science.
Key Standards in Strength Testing
- ASTM E21: Defines tensile testing at elevated temperatures, offering insights into the ultimate strength and elongation of an alloy under heat.
- ASTM E139: Focuses on creep testing to simulate long-term performance under constant stress.
- ISO 204: Outlines uniaxial creep testing, particularly for materials intended for turbines and high-pressure systems.
Comparison of Standards Across Regions
ASTM standards are primarily used in the United States, while ISO standards dominate in Europe and other regions. While both share similar goals, they may vary slightly in sample preparation, testing speeds, and reporting criteria. Understanding these differences ensures compliance with regional and industry-specific requirements.
Ensuring Consistency and Reproducibility
Standards are essential for maintaining consistency. For example, a material tested in one country should exhibit comparable results when evaluated in another, provided the same standard is applied. This consistency aids in global supply chains, where materials sourced internationally must meet the same performance benchmarks.
Challenges in Adhering to Standards
Adherence to standards can sometimes present logistical and financial challenges. Testing facilities must invest in specialized equipment and training, and the process can be time-consuming. However, the long-term benefits, including reduced liability and enhanced material performance, outweigh the initial costs.
Methods to Test Strength at Varying Temperatures
Tensile Testing
Tensile testing evaluates how a material reacts when pulled apart. It reveals key properties like ultimate tensile strength, yield strength, and elongation. For heat-resistant alloys, tensile tests at high temperatures simulate operational conditions, helping predict performance. The process involves heating the alloy in a furnace while applying a tensile load until failure occurs.
Creep Testing
Creep testing measures an alloy’s ability to resist deformation under constant stress over time. This method replicates conditions like those in a turbine blade exposed to prolonged heat and pressure. Creep testers record strain at regular intervals, plotting it against time to identify when failure might occur.
Fatigue Testing
Heat-resistant alloys often face cyclic stresses, such as in engines or rotating machinery. Fatigue testing evaluates how materials respond to repeated loading and unloading. Coupled with thermal cycling, this test provides a comprehensive picture of alloy durability.
Hardness Testing
While not directly related to tensile strength, hardness testing evaluates surface resistance to deformation. Heat-resistant alloys must maintain hardness at high temperatures to resist wear and abrasion. Tests like Rockwell or Vickers hardness can include heating the sample to operational temperatures before applying the load.
Dynamic Thermal Analysis
This method uses equipment like a differential scanning calorimeter (DSC) to monitor phase changes, heat flow, and thermal expansion in alloys. It complements mechanical tests by explaining how thermal properties contribute to overall strength.
Thermal Simulation Techniques
The Role of Simulations in Testing
Thermal simulations using software like Finite Element Analysis (FEA) allow engineers to predict how alloys will perform under various conditions without physical tests. This approach saves time and resources while providing valuable insights into material behavior.
Benefits of Virtual Testing
Simulation can model extreme scenarios that might be difficult or expensive to replicate in a lab. For example, engineers can analyze stress distribution in a turbine blade during startup, operation, and shutdown. Additionally, simulations enable iterative design improvements before manufacturing.
Limitations of Simulations
While powerful, simulations depend on accurate input data. Misrepresenting alloy properties or boundary conditions can lead to misleading results. For this reason, simulations should complement—not replace—physical testing.
Integrating Simulations with Real-World Testing
A combined approach, where simulation informs physical testing and vice versa, ensures comprehensive analysis. For instance, if a simulation predicts a hotspot in a component, engineers can focus testing efforts on that specific area, validating the model.
Conclusion
Understanding the strength of heat-resistant alloys at varying temperatures is a cornerstone of material science. By combining physical testing methods, adherence to global standards, and advanced simulation techniques, industries can ensure the safety, reliability, and performance of these critical materials. Heat-resistant alloys enable innovation across sectors, and their thorough evaluation protects both people and systems. For professionals working with these alloys, prioritizing rigorous testing and informed material selection will result in long-term success and resilience in high-stakes environments.
FAQ
What are heat-resistant alloys commonly used for?
Heat-resistant alloys are used in industries like aerospace, power generation, and manufacturing, where materials must endure high temperatures without losing strength or corroding.
What is the best method for testing heat-resistant alloys?
The most effective approach combines tensile, creep, and fatigue testing with advanced simulation techniques for a holistic understanding of material performance.
Why is creep testing critical for heat-resistant alloys?
Creep testing evaluates long-term deformation under constant stress, helping predict failures in components exposed to prolonged high temperatures, such as turbine blades.
How do simulation techniques enhance alloy testing?
Simulations provide cost-effective insights by modeling extreme conditions and guiding physical tests, ensuring more efficient and focused evaluation.
What standards are used for strength testing?
Key standards include ASTM E21 for tensile testing, ASTM E139 for creep evaluation, and ISO 204 for uniaxial creep testing, ensuring consistent and reliable results globally.