Introduction
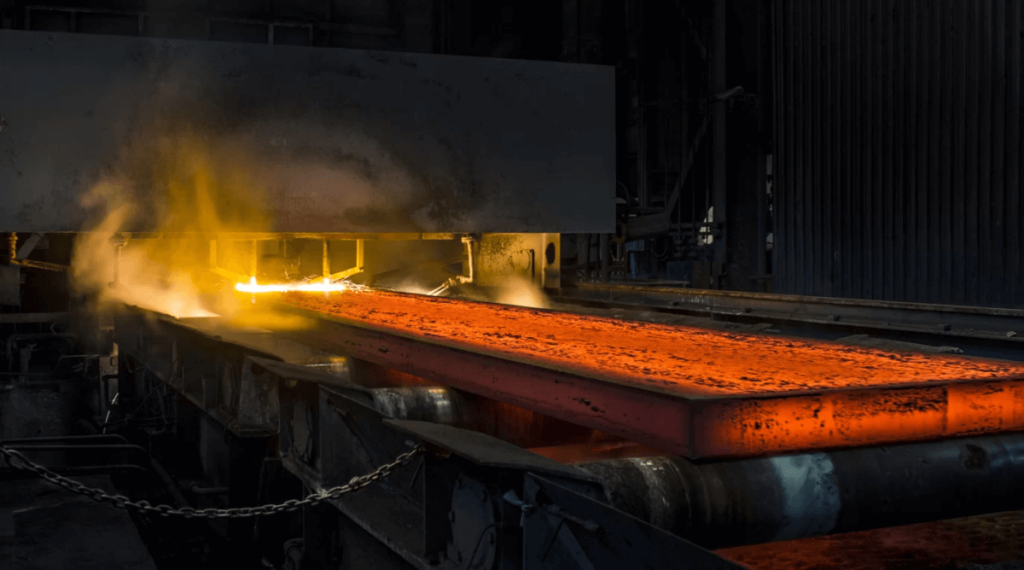
Heat-resistant alloys have revolutionized industries by providing materials capable of withstanding extreme temperatures and harsh environments. These alloys, such as Inconel and Hastelloy, play crucial roles in aerospace, power generation, and chemical applications. Understanding the distinction between their physical and chemical properties is essential for optimizing their use. Physical properties describe observable traits like density, while chemical properties involve the material’s reactivity and behavior under specific conditions. Differentiating these characteristics ensures engineers and technicians select the right alloy for the job, balancing durability, stability, and performance. This guide delves deep into these properties to aid better decision-making.
Understanding Heat-Resistant Alloys
What Are Heat-Resistant Alloys?
Heat-resistant alloys, also called superalloys, are engineered to perform under high temperatures and severe conditions without losing structural integrity. These alloys typically include elements like nickel, cobalt, and iron, which provide unique thermal stability. For example, Inconel 718 resists high temperatures while maintaining strength, making it a preferred choice in jet engine turbines. Another common alloy, Hastelloy, offers excellent corrosion resistance in chemical reactors. Each alloy is tailored for specific applications, combining elements to achieve desired properties.
Applications of Heat-Resistant Alloys
The versatility of heat-resistant alloys spans industries. In aerospace, turbine blades made from these alloys endure extreme operational temperatures. Automotive sectors use them in turbocharger systems to enhance efficiency and durability. In power plants, they are integral to gas turbines and boilers where temperatures often exceed 1000°C. Chemical processing plants rely on these alloys for vessels and pipes exposed to corrosive substances. Their use extends to electronics, where thermal management materials are critical for device longevity. These examples illustrate how these alloys are indispensable in advanced technology and infrastructure.
Why Are These Alloys Unique?
Heat-resistant alloys stand apart due to their ability to combine strength, resistance to oxidation, and thermal stability. This is achieved through precise metallurgical engineering. For instance, small additions of chromium improve oxidation resistance by forming protective oxide layers, while molybdenum enhances strength at elevated temperatures. Additionally, their microstructure, often fine-tuned during manufacturing, balances hardness and flexibility. These attributes allow them to function in environments where standard materials would fail, underscoring their critical role in innovation.
Basics of Physical and Chemical Properties
Physical Properties: Definitions and Examples
Physical properties are inherent attributes observable without altering the material’s composition. These include measurable traits such as density, thermal conductivity, and melting point. For instance, the density of a nickel-based alloy determines its weight, crucial in aerospace design. Hardness, another physical property, affects wear resistance and tooling capabilities.
Chemical Properties: Definitions and Examples
In contrast, chemical properties describe how a material reacts under specific conditions, involving changes in composition. Key examples include oxidation resistance and corrosion resistance. Heat-resistant alloys often rely on chromium or aluminum to prevent oxidation at high temperatures. Corrosion resistance ensures durability in chemical environments, such as acid or salt exposure. The chemical stability of these alloys is a cornerstone of their performance in demanding settings.
Why the Distinction Matters
Understanding the separation between physical and chemical properties aids in selecting materials for specific purposes. For instance, an alloy with excellent corrosion resistance (a chemical property) might lack the hardness needed for mechanical strength (a physical property). Differentiating these attributes prevents costly errors, ensures efficiency, and enhances material longevity in practical applications.
Key Differences Between Physical and Chemical Properties
Observable vs. Transformative Properties
Physical properties focus on traits observable without changing the material’s internal structure, such as color, texture, or thermal expansion. For example, a heat-resistant alloy’s coefficient of thermal expansion impacts its dimensional stability. On the other hand, chemical properties like oxidation resistance involve a chemical reaction where the material forms a protective oxide layer.
Examples Highlighting the Distinction
Consider the melting point (physical) versus corrosion resistance (chemical). While the former determines usability in high-temperature environments, the latter dictates performance in chemically aggressive surroundings. Inconel alloys excel in both, balancing physical strength with chemical stability.
Practical Implications of Differentiating
By understanding these differences, engineers can better match alloys to operational demands. For instance, high-hardness alloys may be chosen for cutting tools, while chemically inert alloys like Hastelloy are ideal for chemical reactors. This distinction streamlines material selection, ensuring optimal performance and cost efficiency.
Common Physical Properties of Heat-Resistant Alloys
Melting Point and Thermal Stability
A defining physical property of heat-resistant alloys is their ability to maintain strength near their melting point. Alloys like Inconel 625 withstand temperatures over 1000°C, enabling their use in jet engines. Thermal stability ensures the alloy doesn’t deform or weaken during operation.
Density and Weight Considerations
The density of an alloy impacts its application in weight-sensitive fields like aerospace. Engineers often balance strength with lightweight characteristics. Titanium alloys, with their lower density compared to nickel-based counterparts, are frequently chosen for structural components in aircraft.
Hardness and Ductility
Hardness determines wear resistance, while ductility affects the alloy’s ability to deform under stress without breaking. Heat-resistant alloys exhibit a fine-tuned balance, enabling both robust tooling applications and resilience under dynamic loads. For example, turbine blades require high hardness to resist erosion from airflow.
Chemical Properties of Heat-Resistant Alloys
Oxidation Resistance
High temperatures can cause metals to oxidize, degrading their surface. Heat-resistant alloys incorporate chromium or aluminum to form a protective oxide layer, preventing further oxidation. This property is vital for gas turbines operating in oxygen-rich environments.
Corrosion Resistance
Exposure to chemicals like acids or seawater demands materials resistant to corrosion. Hastelloy alloys, enriched with molybdenum, perform exceptionally in such conditions, making them ideal for desalination plants or chemical reactors.
Reactivity with Other Materials
Compatibility with other substances, whether gaseous or solid, is essential. For example, in reactors where catalysts are used, alloys must resist reactions that could compromise their structural integrity or the catalytic process.
Testing and Measuring Physical Properties
Techniques for Measuring Physical Properties
Standardized tests like tensile testing evaluate strength, while thermal conductivity is assessed using heat flow meters. These tests provide quantifiable data, ensuring alloys meet design criteria.
Tools for Evaluation
State-of-the-art tools, including spectrometers and microhardness testers, allow precise measurements. For example, differential scanning calorimetry assesses an alloy’s thermal stability by analyzing heat flow during temperature changes.
Challenges in Testing Physical Traits
Variability in microstructure can affect test outcomes. For instance, grain size impacts hardness readings, necessitating multiple tests to ensure consistency. Understanding these nuances is critical for reliable evaluations.
Analyzing Chemical Properties
Chemical Stability Tests
Common tests, like salt spray testing, simulate harsh environments to evaluate corrosion resistance. Other methods involve exposing alloys to high-temperature oxidation to measure their protective layer’s effectiveness.
Role of Elemental Composition
The inclusion of specific elements, such as chromium, directly influences an alloy’s chemical properties. Analyzing composition using techniques like X-ray fluorescence spectroscopy ensures alloys meet intended specifications.
Interplay Between Chemistry and Application
For example, in marine environments, an alloy’s corrosion resistance determines its longevity, directly impacting the lifespan of ship components. Proper analysis avoids premature failures.
Microstructural Influence on Properties
Grain Size and Distribution
Microstructure significantly impacts both physical and chemical properties. Fine-grained structures enhance strength, while certain distributions improve thermal conductivity.
Role in Chemical Resistance
The presence of microstructural features like inclusions can enhance or compromise chemical resistance. Optimizing these features during alloy processing maximizes performance.
Surface Treatment and Its Effects
Post-processing treatments, such as passivation, enhance chemical stability by removing contaminants, forming protective layers. This demonstrates how microstructure and treatment work in synergy.
Real-World Applications
How Physical Properties Are Prioritized
When selecting alloys for real-world applications, physical properties often take precedence in environments where structural performance is critical. For instance, in turbine blades used in jet engines, the melting point and thermal stability of the alloy dictate its usability. These components face high stresses due to centrifugal forces and exposure to temperatures exceeding 1000°C. An alloy like Inconel 718 is chosen specifically for its ability to maintain strength under such conditions. Additionally, hardness becomes a crucial consideration in environments where wear and tear are prominent, such as cutting tools or industrial dies. Engineers prioritize alloys that exhibit high hardness to minimize wear, ensuring longevity and reducing downtime.
Chemical Property Considerations in Selection
Chemical properties, while secondary in some cases, are indispensable in environments exposed to aggressive chemicals or gases. For example, in chemical processing plants, pipelines and reactors must endure corrosive substances such as hydrochloric acid. Hastelloy, known for its superior corrosion resistance, becomes the material of choice. Similarly, oxidation resistance is critical in high-temperature furnaces where the presence of oxygen could degrade the material’s surface. Alloys with high chromium or aluminum content develop protective oxide layers, extending their operational lifespan. The interplay between physical and chemical properties ensures that the chosen material is robust yet resistant to environmental challenges.
Balancing Both Property Types
Real-world applications often demand a balance of physical and chemical properties. In nuclear reactors, for instance, materials must withstand radiation (a chemical challenge) while maintaining structural integrity under extreme thermal loads. Zirconium alloys, commonly used in these environments, meet these dual requirements by offering both low neutron absorption (a chemical property) and high melting points (a physical property). This delicate balance demonstrates the importance of understanding and differentiating between property types to achieve optimal performance in demanding applications.
Challenges in Property Analysis
Overlapping Effects Between Properties
One of the significant challenges in analyzing material properties is the overlap between physical and chemical effects. For example, surface tarnishing might appear as a physical change but often results from a chemical reaction with environmental elements. This overlap complicates property testing and requires a nuanced understanding of material science. Similarly, creep deformation in alloys, while classified as a physical property, is influenced by the material’s chemical stability under prolonged stress at elevated temperatures.
Limitations of Standard Testing Methods
Traditional testing methods, while effective, often fall short in capturing complex interactions between properties. For instance, hardness tests may not account for microstructural changes induced by high-temperature oxidation, leading to incomplete assessments. Additionally, environmental simulation tests, such as salt spray tests for corrosion resistance, may not fully replicate real-world conditions, causing discrepancies between laboratory results and field performance. These limitations necessitate advanced testing techniques and rigorous standards.
Advancements Addressing These Challenges
Emerging technologies in material analysis, such as 3D microstructural mapping and real-time chemical stability monitoring, offer promising solutions. These advancements provide detailed insights into how physical and chemical properties interact, enabling engineers to predict material behavior more accurately. By integrating these technologies, industries can overcome traditional testing limitations and improve material selection processes, ensuring reliable performance in critical applications.
Physical Properties in Design
Role in Mechanical Design
In mechanical design, physical properties serve as foundational parameters. Properties such as tensile strength, ductility, and hardness dictate how a material behaves under mechanical stress. For example, in constructing high-performance automotive components like crankshafts, engineers prioritize materials with high fatigue resistance to endure repetitive loads. This ensures the component’s longevity and reliability under dynamic conditions.
Importance in Weight-Sensitive Industries
Weight is a critical factor in industries like aerospace and automotive engineering. Reducing weight without compromising strength is a constant challenge. Heat-resistant alloys like titanium stand out for their low density, making them ideal for aerospace components such as fuselages and engine mounts. The reduced weight translates into improved fuel efficiency and reduced operational costs, highlighting the value of physical properties in design considerations.
Optimizing Thermal Compatibility
Thermal expansion is another crucial physical property in design. Components that expand or contract significantly with temperature changes can cause mechanical failures. Alloys with low coefficients of thermal expansion are preferred for precision applications such as optical instruments and high-temperature sensors. These materials ensure dimensional stability, maintaining performance and accuracy across varying thermal environments.
Chemical Properties in Maintenance
Determining Maintenance Schedules
Chemical properties play a pivotal role in planning maintenance routines for critical systems. For example, the corrosion resistance of alloys in pipelines determines inspection intervals and replacement schedules. Alloys with superior chemical stability, such as those used in offshore drilling platforms, reduce maintenance frequency, leading to cost savings and enhanced operational efficiency.
Implications of Poor Chemical Resistance
Neglecting chemical properties can lead to catastrophic failures. In chemical plants, poorly selected materials may corrode rapidly, resulting in leaks or structural failures. These incidents not only incur significant repair costs but also pose safety risks. Using alloys with proven chemical resistance mitigates such risks, ensuring the long-term reliability of infrastructure.
Enhancing Durability Through Treatments
Post-processing treatments such as passivation and coating improve an alloy’s chemical resistance. For example, stainless steel is often passivated to remove surface contaminants and enhance its resistance to rust. These treatments extend the material’s lifespan, reducing the need for frequent replacements and minimizing operational disruptions.
Emerging Trends in Alloy Development
Nanostructured Alloys
Nanotechnology has opened new frontiers in alloy development. Nanostructured alloys exhibit superior physical and chemical properties due to their refined grain size and homogeneity. These alloys offer enhanced strength, improved wear resistance, and exceptional thermal stability, making them ideal for cutting-edge applications such as advanced aerospace systems and medical implants.
Sustainability and Recyclability
With growing environmental concerns, the development of sustainable and recyclable alloys has gained momentum. Materials engineers are exploring eco-friendly alternatives to traditional alloying elements, aiming to reduce the environmental impact of production and disposal. Alloys incorporating recycled materials without compromising performance are becoming a preferred choice across industries.
Customization for Specialized Applications
Advancements in additive manufacturing, or 3D printing, have enabled the customization of heat-resistant alloys for specialized applications. This approach allows engineers to tailor an alloy’s composition and microstructure precisely to its intended use, optimizing both physical and chemical properties for maximum efficiency and performance.
Common Misconceptions
Mistaking Tarnishing for Physical Change
A common misconception is equating tarnishing with a physical property. Tarnishing, often seen as discoloration on a material’s surface, results from a chemical reaction between the alloy and environmental elements such as oxygen or sulfur. Recognizing this as a chemical property is essential for accurate material assessment.
Overlooking Microstructure in Property Analysis
Another misconception is neglecting the role of microstructure in influencing properties. Physical properties like hardness and ductility depend significantly on the alloy’s microstructural arrangement. Similarly, chemical properties such as corrosion resistance are enhanced or diminished by microstructural features, emphasizing the importance of holistic evaluations.
Simplifying Property Classifications
Categorizing properties as purely physical or chemical can oversimplify material science. The interaction between these properties often creates a continuum rather than a clear division. For instance, thermal fatigue involves both physical stresses and chemical stability, highlighting the need for a nuanced understanding of material behavior.
How to Make Informed Choices
Guidelines for Material Selection
To make informed material choices, start by defining the operational requirements, including temperature range, mechanical loads, and environmental exposure. Prioritize properties based on these criteria, balancing physical traits like strength and weight with chemical traits like corrosion resistance.
Ensuring Compatibility with Applications
Material compatibility with the intended application is critical. For example, in power plants, alloys must endure high temperatures (a physical requirement) while resisting oxidation (a chemical need). Consulting experts and leveraging advanced testing methods ensure the chosen material aligns with operational demands.
Tips for Long-Term Performance
Select materials that offer durability and reliability in their specific applications. Incorporate safety margins by choosing alloys with superior properties than minimally required. Regular testing and monitoring further ensure the material performs as expected, reducing risks and maximizing efficiency.
Conclusion
Differentiating between physical and chemical properties of heat-resistant alloys is essential for effective material selection and application. By understanding observable traits like hardness and melting points, alongside reactive attributes such as oxidation resistance, engineers can optimize alloy performance in demanding environments. This distinction not only enhances functionality but also ensures safety and cost efficiency. Armed with this knowledge, professionals can confidently choose materials that meet their specific needs, driving innovation and reliability across industries. For further insights or assistance in alloy selection, consider consulting a materials expert to guide your decisions. Thank you for exploring this detailed guide, and we hope it empowers your next project with clarity and confidence.
FAQ Section
Why are heat-resistant alloys important?
They maintain structural integrity and resist chemical degradation under extreme conditions, making them vital in high-performance applications.
What distinguishes physical and chemical properties?
Physical properties are observable without altering the material, while chemical properties involve compositional changes during reactions.
How are these properties tested?
Physical properties use tests like tensile strength measurement, while chemical properties require corrosion or oxidation resistance analysis.
Can an alloy excel in both property types?
Yes, alloys like Inconel combine high thermal stability with excellent corrosion resistance, balancing physical and chemical performance.
What advancements are shaping future alloys?
Nanostructuring, sustainability, and additive manufacturing enable alloys with superior and customized properties for diverse applications.