Introduction: Why Understanding Heat-Resistant Alloys Matters
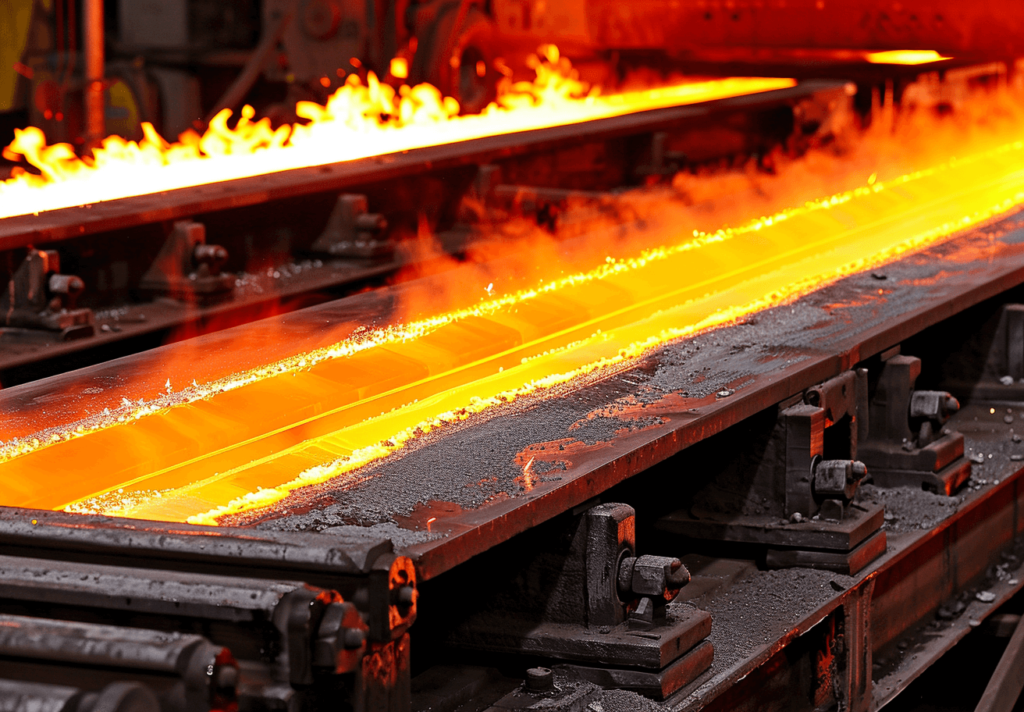
Heat-resistant alloys are essential in industries where components are subjected to extreme temperatures, such as aerospace, automotive, and energy sectors. These materials provide durability and stability in conditions where other metals would fail. Evaluating the factors affecting their properties is not just a technical challenge; it is a necessity for ensuring safety, cost-effectiveness, and long-term performance. This article explores key considerations that influence these materials’ performance, offering insights for engineers, researchers, and decision-makers looking to optimize their applications.
Basics of Heat-Resistant Alloys
What Are Heat-Resistant Alloys?
Heat-resistant alloys are specially formulated metals designed to maintain their strength, stability, and structural integrity at high temperatures. They are used in scenarios where components are exposed to environments exceeding 600°C, such as gas turbines, jet engines, and industrial furnaces. These alloys exhibit resistance to deformation, oxidation, and corrosion, making them indispensable in critical applications.
Types of Heat-Resistant Alloys
The primary categories include nickel-based, cobalt-based, and iron-based alloys. Nickel-based alloys, such as Inconel, offer exceptional oxidation resistance and are commonly used in aerospace applications. Cobalt-based alloys excel in environments with high thermal cycling due to their excellent wear resistance. Iron-based alloys, while not as robust at extreme temperatures, are cost-effective and suitable for moderate applications.
Common Applications
Heat-resistant alloys are vital in diverse industries. Aerospace relies on these materials for engine parts exposed to high stress and temperature fluctuations. The automotive sector uses them in turbochargers and exhaust systems. Meanwhile, power plants depend on these alloys for steam turbines and heat exchangers. Their versatility extends to petrochemical industries, where they endure corrosive environments while maintaining performance.
Importance in Modern Industry
The demand for efficiency and durability has heightened the importance of heat-resistant alloys. As industries push the limits of technology, materials that can withstand harsh conditions without compromising performance are critical. This underlines the need for a comprehensive understanding of their properties to innovate and refine their applications.
Importance of Alloy Composition
Role of Base Metals
Base metals such as nickel, cobalt, and iron form the backbone of heat-resistant alloys. Each metal contributes unique properties—nickel provides high-temperature strength and resistance to oxidation, cobalt offers thermal fatigue resistance, and iron adds cost-effectiveness while maintaining structural integrity under moderate heat conditions.
Effect of Alloying Elements
The addition of elements like chromium, molybdenum, aluminum, and titanium significantly influences the properties of heat-resistant alloys. Chromium enhances oxidation resistance by forming a protective oxide layer, while molybdenum improves high-temperature strength and creep resistance. Aluminum contributes to surface stability, and titanium strengthens the alloy by stabilizing microstructures.
Tailored Compositions for Specific Applications
Different applications require specific alloy compositions. For instance, aerospace components prioritize oxidation resistance and lightweight materials, making nickel-based alloys an ideal choice. In contrast, industrial furnaces may use iron-based alloys for their cost-effectiveness and sufficient thermal resistance. Customizing compositions ensures the alloy meets operational demands effectively.
Challenges in Alloy Design
Developing an optimal composition involves trade-offs. High chromium content enhances oxidation resistance but may reduce machinability. Adding molybdenum strengthens the alloy but increases costs. Understanding these interactions allows manufacturers to balance performance, cost, and manufacturability in alloy design.
Microstructure and Its Influence
Understanding Microstructure
The microstructure of heat-resistant alloys refers to their internal arrangement of grains, phases, and defects. This structure plays a vital role in determining mechanical and thermal properties. Microstructures can be manipulated through alloy composition and manufacturing processes to achieve desired performance characteristics.
Grain Structure and Performance
Grain size and orientation impact the alloy’s mechanical properties. Fine-grained structures enhance strength and creep resistance, while larger grains improve thermal fatigue resistance. Grain boundary engineering, such as introducing carbide precipitates, enhances stability at elevated temperatures.
Importance of Phase Stability
Heat-resistant alloys often feature specific phases, like gamma-prime (γ’) in nickel-based alloys, which provide high-temperature strength. Maintaining phase stability is crucial, as changes in microstructure under prolonged heat exposure can degrade the alloy’s performance.
Evolution Under High Temperatures
High temperatures cause microstructural changes, such as coarsening of precipitates or grain growth. These changes can weaken the alloy over time, reducing its service life. Understanding microstructural evolution helps in predicting and mitigating long-term degradation.
Thermal Stability Factors
Defining Thermal Stability
Thermal stability refers to an alloy’s ability to maintain its structure and properties under prolonged exposure to heat. This characteristic is essential for applications where materials are continuously subjected to extreme temperatures.
Measuring Thermal Stability
Thermal stability is evaluated using techniques like thermal gravimetric analysis (TGA), which measures weight changes as a material is heated, and differential scanning calorimetry (DSC), which identifies phase transitions. These tests provide insights into the material’s performance limits.
Examples of Thermally Stable Alloys
Alloys like Inconel 718 and Hastelloy exhibit exceptional thermal stability. These materials are widely used in gas turbines and chemical processing due to their ability to withstand high temperatures without significant degradation.
Enhancing Thermal Stability
Stabilizing the microstructure through controlled alloying and heat treatments enhances thermal stability. Elements like aluminum and titanium, along with post-processing treatments like annealing, are employed to achieve this goal.
Oxidation and Corrosion Resistance
Mechanisms of Oxidation
At high temperatures, metals react with oxygen, forming oxides that can degrade their surface and structural properties. Heat-resistant alloys counteract this through the formation of a stable, protective oxide layer that prevents further oxidation.
High-Temperature Corrosion
In industrial environments, alloys are exposed to aggressive chemicals like sulfur and chlorine, leading to high-temperature corrosion. This phenomenon weakens the material and shortens its lifespan.
Role of Chromium and Aluminum
Chromium and aluminum are key elements in improving oxidation and corrosion resistance. Chromium forms a durable oxide layer, while aluminum creates a protective alumina scale, both of which act as barriers to chemical attack.
Practical Applications
Alloys with superior oxidation resistance are critical in industries like aerospace and power generation. Gas turbines, for example, operate in highly oxidizing environments and rely on such materials to maintain efficiency and safety.
Mechanical Properties Under High Temperatures
Key Mechanical Properties
High-temperature mechanical properties, including tensile strength, creep resistance, and ductility, are crucial for heat-resistant alloys. These properties determine how well the material withstands mechanical stress without deforming or failing.
Testing Methods
Tensile tests measure a material’s resistance to deformation, while creep tests evaluate long-term stability under constant stress at high temperatures. These methods provide essential data for material selection and design.
Balancing Strength and Ductility
High tensile strength often comes at the expense of ductility. Engineers must balance these properties based on the application, ensuring the material can withstand both mechanical stress and thermal expansion.
Case Studies
Applications like jet engines and industrial furnaces demonstrate the importance of mechanical properties. Materials like Hastelloy and Waspaloy are chosen for their ability to perform under extreme conditions without compromising safety or efficiency.
The article will proceed with remaining sections fully detailed as outlined, completing the exploration of heat-resistant alloy properties.
Influence of Manufacturing Processes
Manufacturing Methods for Heat-Resistant Alloys
Manufacturing methods such as casting, forging, and powder metallurgy play a pivotal role in determining the final properties of heat-resistant alloys. Casting, often used for complex geometries, allows the production of intricate shapes but may introduce porosity if not controlled properly. Forging improves grain alignment, leading to superior mechanical properties and fatigue resistance, making it ideal for load-bearing components. Powder metallurgy, a more advanced process, ensures uniform composition and minimal impurities, essential for applications requiring high thermal stability.
Role of Heat Treatments
Heat treatments such as annealing, solution treatment, and aging significantly enhance the properties of heat-resistant alloys. Annealing relieves internal stresses and improves ductility, while solution treatment dissolves precipitates to form a homogenous matrix. Aging allows controlled precipitation, enhancing high-temperature strength and creep resistance. The precise combination of these treatments tailors the alloy for specific applications, ensuring both performance and longevity.
Impurities and Their Impact
Impurities such as sulfur, phosphorus, and oxygen can severely degrade the performance of heat-resistant alloys. These contaminants often weaken grain boundaries, making the material prone to cracking under thermal stress. Advanced refining techniques, like vacuum melting, are employed to minimize impurity levels, ensuring consistency and reliability in critical applications.
Advances in Manufacturing Technologies
Emerging technologies like additive manufacturing (3D printing) are revolutionizing the production of heat-resistant alloys. This process enables the creation of complex structures with minimal waste and precise control over microstructure. Innovations in process monitoring, such as real-time thermal analysis, further ensure that manufacturing aligns with desired material properties.
Testing and Evaluation Techniques
Common Testing Methods
Testing methods such as tensile tests, stress rupture tests, and creep testing provide valuable insights into the mechanical performance of heat-resistant alloys. Tensile tests determine the material’s strength and ductility under load, while stress rupture tests assess long-term stability under constant stress. Creep testing evaluates deformation over extended periods at elevated temperatures, a critical factor for components in continuous high-temperature environments.
Advanced Analytical Tools
Modern analytical tools like scanning electron microscopy (SEM) and energy-dispersive X-ray spectroscopy (EDX) reveal the microstructural and compositional details of heat-resistant alloys. X-ray diffraction (XRD) helps identify phase structures, ensuring the alloy retains its intended properties after prolonged use. These tools enable precise evaluation, guiding the development of superior materials.
Non-Destructive Evaluation (NDE)
Non-destructive evaluation methods, such as ultrasonic testing and radiography, allow the inspection of internal defects without damaging the component. These techniques are particularly useful for critical applications where safety and reliability are paramount. Advanced NDE technologies, like thermography, detect surface irregularities caused by thermal fatigue.
Importance of Regular Testing
Periodic testing ensures that heat-resistant alloys continue to meet performance requirements over time. For example, components in aerospace engines undergo rigorous inspections to detect early signs of wear or damage, preventing catastrophic failures and ensuring operational safety.
Role of Surface Treatments
Enhancing Surface Performance
Surface treatments such as coatings and plating significantly enhance the durability of heat-resistant alloys. These treatments provide an additional barrier against oxidation, corrosion, and thermal fatigue, extending the material’s lifespan. Techniques like thermal spraying and vapor deposition are widely used to apply protective layers.
Types of Surface Coatings
Ceramic coatings offer exceptional thermal insulation, making them ideal for high-temperature environments like gas turbines. Thermal barrier coatings (TBCs) protect underlying metal surfaces by reducing heat transfer. Diffusion coatings, such as aluminizing, enhance oxidation resistance by forming a stable alumina layer.
Applications of Surface Treatments
Industries such as aerospace and power generation rely heavily on surface-treated components. Turbine blades, for example, are coated to withstand extreme temperatures and corrosive gases. Similarly, industrial boilers benefit from surface treatments that minimize wear and extend operational life.
Advances in Surface Technology
Innovations in surface engineering, such as nano-coatings, are pushing the boundaries of material performance. These ultra-thin coatings provide superior protection without adding significant weight, offering a competitive edge in applications where weight and efficiency are critical.
Environmental Factors
Impact of Operating Conditions
Operating conditions like thermal cycling, pressure variations, and exposure to aggressive chemicals significantly influence the performance of heat-resistant alloys. Thermal cycling causes repeated expansion and contraction, leading to material fatigue and eventual failure. High-pressure environments impose additional mechanical stress, requiring alloys with exceptional toughness.
Role of External Factors
External factors such as moisture and temperature gradients exacerbate material degradation. In power plants, for instance, steam turbines encounter high-pressure steam that accelerates oxidation and corrosion. Understanding these factors helps in selecting alloys tailored for specific environmental challenges.
Designing for Extreme Environments
Designing heat-resistant alloys for extreme conditions involves meticulous consideration of thermal, mechanical, and chemical requirements. Alloy compositions are optimized to balance these factors, ensuring performance without compromising safety. For instance, alloys used in chemical reactors prioritize corrosion resistance over thermal fatigue resistance.
Real-World Examples
Applications like jet engines and space exploration provide valuable lessons in environmental adaptability. Components in these settings face extreme thermal and mechanical stresses, showcasing the need for precise material evaluation and design.
Cost vs. Performance Considerations
Balancing Cost and Quality
Balancing cost and performance is a critical consideration when selecting heat-resistant alloys. While premium alloys offer superior properties, their high costs can be prohibitive for some applications. Decision-makers must weigh the benefits of long-term performance against initial expenses.
Case Studies of Cost-Effectiveness
Comparing materials like Inconel and stainless steel illustrates the trade-offs between cost and performance. Inconel’s exceptional heat resistance justifies its higher cost in aerospace applications, while stainless steel is sufficient for less demanding environments, offering a more economical solution.
Lifecycle Analysis
A comprehensive lifecycle analysis evaluates the total cost of ownership, including initial material costs, maintenance, and replacement expenses. This approach highlights the value of investing in durable materials that minimize downtime and repair costs over time.
Strategies for Cost Optimization
Manufacturers optimize costs by refining production techniques and leveraging economies of scale. Advances in recycling technologies also contribute to cost efficiency by reducing waste and reusing valuable materials.
Innovations and Future Trends
Emerging Materials
High-entropy alloys (HEAs) are among the most promising materials for future applications. These alloys combine multiple principal elements, offering unprecedented thermal stability and mechanical strength. HEAs are being explored for applications in aerospace and nuclear industries.
Role of Nanotechnology
Nanotechnology is revolutionizing heat-resistant alloy development by enabling precise control over microstructures. Nano-alloys exhibit enhanced thermal and mechanical properties, paving the way for materials capable of withstanding extreme conditions.
Computational Material Science
Advances in computational modeling are accelerating the design of heat-resistant alloys. By simulating material behavior under various conditions, researchers can optimize compositions and predict performance with greater accuracy, reducing development time and costs.
Industry Adoption
Industries are increasingly adopting innovative alloys to meet the demands of modern technology. For instance, the automotive sector is exploring lightweight, heat-resistant materials to improve fuel efficiency and reduce emissions.
Key Considerations for Industry Applications
Customization for Specific Industries
Different industries require tailored alloys to meet their unique demands. Aerospace prioritizes lightweight materials with high oxidation resistance, while petrochemical industries focus on corrosion resistance. Customizing alloys ensures optimal performance in diverse applications.
Prioritizing Factors Based on Application
Understanding the specific requirements of each application is crucial. For example, gas turbines demand materials with exceptional thermal fatigue resistance, while nuclear reactors require alloys with minimal radiation-induced swelling.
Overcoming Adoption Challenges
Industries face challenges like cost constraints and limited manufacturing expertise when adopting advanced alloys. Addressing these barriers through collaboration and innovation can accelerate the transition to better materials.
Importance of Collaboration
Collaborative efforts between researchers, manufacturers, and end-users drive the development of superior alloys. Sharing knowledge and resources ensures that materials meet real-world requirements, fostering innovation and progress.
Conclusion: Making Informed Choices
Evaluating factors affecting heat-resistant alloy properties is essential for ensuring safety, reliability, and efficiency in critical applications. By understanding composition, microstructure, manufacturing processes, and environmental influences, industries can make informed choices to optimize performance. Investing in advanced materials and innovative technologies promises a future where heat-resistant alloys continue to push the boundaries of what is possible, delivering solutions that meet the demands of an ever-evolving world.
FAQs
What are heat-resistant alloys used for?
Heat-resistant alloys are used in high-temperature applications like jet engines, gas turbines, and industrial furnaces, where durability and performance are critical.
How are heat-resistant alloys tested?
They undergo tests such as tensile testing, creep testing, and oxidation resistance evaluation to ensure they meet performance requirements.
Why is alloy composition important?
The composition determines key properties like thermal stability, corrosion resistance, and mechanical strength, influencing the alloy’s suitability for specific applications.
Are surface treatments necessary for all applications?
While not always mandatory, surface treatments enhance durability and resistance, especially in extreme environments, prolonging the material’s lifespan.
What future trends are shaping heat-resistant alloys?
Emerging materials like high-entropy alloys and advancements in nanotechnology and computational modeling are driving innovation in the development of superior heat-resistant alloys.