What Does Heat Resistance in Alloys Mean?
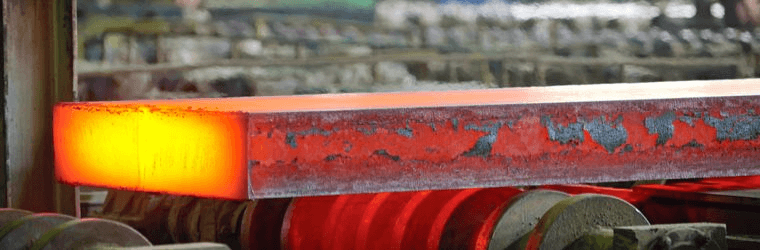
Heat resistance in alloys refers to the ability of a material to maintain its mechanical and structural properties when exposed to high temperatures. This property is essential in environments where extreme heat could otherwise weaken materials or cause deformation, leading to failure in critical applications. For example, in jet engines, heat-resistant alloys ensure the turbines can function efficiently under high thermal stress without losing their strength or corroding. The concept stems from a material’s ability to resist softening, oxidation, and thermal fatigue, all of which are major challenges in high-temperature scenarios.
Heat-resistant alloys typically have specialized compositions that enable them to withstand elevated temperatures. This often involves adding elements like nickel, chromium, or molybdenum to enhance the alloy’s structural integrity and resistance to oxidation. The science behind this lies in the material’s crystalline structure, which remains stable at high temperatures, and the formation of protective oxide layers that shield the alloy from degradation. These alloys find applications across industries such as aerospace, automotive, and energy, where durability and performance under heat stress are non-negotiable.
To fully grasp heat resistance, one must understand the balance between thermal stability, mechanical strength, and oxidation resistance. This interplay defines the alloy’s effectiveness in heat-intensive environments and sets the stage for understanding why such materials are indispensable in modern engineering.
Why Are Heat-Resistant Alloys Important?
Heat-resistant alloys are critical in engineering and industrial applications where components are exposed to extreme thermal conditions. These materials ensure the functionality and safety of systems operating under high temperatures, such as power plants, jet engines, and industrial furnaces. Without heat-resistant alloys, such systems would be prone to rapid degradation, leading to costly failures or even catastrophic accidents.
One of the primary reasons these alloys are vital is their role in maintaining structural integrity. In high-temperature environments, ordinary materials can lose their mechanical strength, becoming soft and deformable. Heat-resistant alloys, however, retain their properties due to their unique composition and structure. For example, nickel-based alloys, commonly used in jet engines, can withstand temperatures exceeding 1,000°C while maintaining their strength and resistance to oxidation.
Another critical factor is safety. In applications like aerospace and energy, failure of materials under heat stress can result in dangerous situations. Heat-resistant alloys prevent such scenarios by providing reliable performance, ensuring that components can handle prolonged exposure to high temperatures without failure. This is particularly important in industries like power generation, where turbines and boilers operate under constant thermal stress.
Economic considerations also play a role in the importance of these materials. Using heat-resistant alloys reduces maintenance costs by extending the lifespan of components. For instance, in manufacturing processes involving furnaces or kilns, components made from these alloys require less frequent replacement, saving both time and money. Furthermore, their durability contributes to energy efficiency, as systems can operate at higher temperatures, increasing output and reducing fuel consumption.
Lastly, these materials enable innovation in various industries. For example, in the automotive sector, heat-resistant alloys are used to develop advanced exhaust systems that comply with stringent emission regulations. Similarly, in electronics, these materials are employed in heat sinks and other components to dissipate heat effectively, allowing for the development of more compact and powerful devices.
In summary, heat-resistant alloys are indispensable for ensuring the safety, efficiency, and longevity of systems operating under extreme thermal conditions. Their unique properties not only solve critical engineering challenges but also pave the way for technological advancements across multiple industries.
Key Factors That Determine Heat Resistance in Alloys
The heat resistance of an alloy depends on several interrelated factors, each contributing to its ability to withstand high temperatures without losing functionality. These factors are primarily governed by the alloy’s chemical composition, microstructural properties, and physical characteristics.
One major factor is chemical composition. Heat-resistant alloys typically include elements like nickel, chromium, and molybdenum, which enhance their ability to withstand thermal stress. Nickel is known for its high melting point and ability to maintain strength at elevated temperatures, making it a common base material for superalloys. Chromium, on the other hand, provides excellent resistance to oxidation and corrosion by forming a stable oxide layer on the surface of the alloy. Molybdenum contributes by increasing the alloy’s hardness and resistance to deformation under high thermal loads.
Microstructural stability is another critical aspect. The arrangement of grains and phases within the alloy determines its performance under heat. Alloys with fine-grained structures tend to exhibit better mechanical properties at high temperatures, as the fine grains impede the movement of dislocations, which are a key mechanism of material failure. Additionally, precipitation strengthening, achieved by incorporating specific elements that form stable precipitates within the alloy, further enhances high-temperature strength.
Oxidation resistance is equally important. When exposed to heat, materials are often at risk of reacting with oxygen in the environment, leading to scaling and degradation. Heat-resistant alloys are designed to form protective oxide layers that prevent further oxidation. For example, chromium oxide and aluminum oxide are commonly used in such alloys to act as barriers against environmental damage.
Thermal conductivity and expansion also play roles. Materials with low thermal expansion coefficients are less prone to thermal fatigue, which occurs due to repeated heating and cooling cycles. Similarly, good thermal conductivity helps dissipate heat more effectively, reducing the risk of localized overheating.
In conclusion, the heat resistance of an alloy is a result of a carefully balanced combination of chemical composition, microstructural stability, and physical properties. Understanding these factors allows engineers to select or design alloys that meet specific requirements for high-temperature applications.
Common Elements in Heat-Resistant Alloys
Heat-resistant alloys are formulated using a variety of elements, each chosen for its unique properties that contribute to the alloy’s performance under high temperatures. Among these, nickel, chromium, molybdenum, and iron are some of the most significant.
Nickel is the backbone of many heat-resistant alloys, particularly superalloys. Its high melting point and excellent strength retention at elevated temperatures make it ideal for demanding applications such as jet engines and gas turbines. Additionally, nickel enhances the alloy’s resistance to corrosion and oxidation, ensuring longevity in harsh environments.
Chromium is another vital element. It provides exceptional oxidation resistance by forming a thin, stable oxide layer on the surface of the alloy. This layer acts as a barrier against further chemical reactions, protecting the material from degradation. Chromium is especially important in environments where the alloy is exposed to both high temperatures and corrosive gases.
Molybdenum contributes to the strength and toughness of heat-resistant alloys. Its presence enhances the alloy’s resistance to deformation and creep, which is the gradual deformation of a material under prolonged stress and heat. Molybdenum also improves the alloy’s hardness, making it suitable for applications that require wear resistance.
Iron, often used in stainless steels and other iron-based alloys, provides a cost-effective base material with good high-temperature properties. When combined with elements like nickel and chromium, iron-based alloys can achieve excellent heat resistance and corrosion protection.
Other elements, such as cobalt, aluminum, and titanium, are also used to tailor the properties of heat-resistant alloys. Cobalt enhances strength and corrosion resistance, while aluminum and titanium contribute to precipitation strengthening, which increases the alloy’s hardness and mechanical stability.
By carefully selecting and combining these elements, metallurgists can create alloys with properties optimized for specific high-temperature applications. The choice of elements depends on factors such as the operating environment, desired mechanical properties, and cost considerations.
This balance of elements ensures that heat-resistant alloys meet the rigorous demands of modern industries, from aerospace to energy production.
How Heat Resistance is Tested
Understanding the heat resistance of an alloy requires rigorous testing methods to evaluate its performance under high-temperature conditions. These tests ensure the alloy meets the specific requirements of applications where thermal stress is a significant factor. Engineers and scientists rely on several well-established laboratory and field-testing procedures to assess heat resistance accurately.
One of the most common methods is stress-rupture testing. This process involves applying a constant load to a sample at a specific temperature until it fails. The time to rupture provides valuable information about the material’s long-term strength and reliability under thermal stress. Stress-rupture tests are crucial for applications like jet engine turbines, where components are subjected to sustained high temperatures and loads.
Another widely used technique is creep testing. Creep refers to the gradual deformation of a material under constant stress over time. During this test, a sample is exposed to a fixed stress and temperature, and its deformation is measured over an extended period. The results help predict how the alloy will perform under prolonged high-temperature conditions, a critical factor in industries like power generation.
Thermal fatigue testing evaluates an alloy’s ability to withstand repeated heating and cooling cycles. This is particularly important for components like exhaust systems and heat exchangers, which experience fluctuating temperatures during operation. Thermal fatigue testing simulates these cycles to determine how the alloy handles thermal expansion and contraction, as well as the associated stresses.
For applications requiring oxidation resistance, high-temperature oxidation testing is performed. In this test, the alloy is exposed to an oxidizing environment at elevated temperatures, and the rate of oxidation is measured. This helps assess the effectiveness of protective oxide layers, such as chromium or aluminum oxide, in preventing material degradation.
Field testing complements laboratory tests by evaluating the performance of heat-resistant alloys in real-world conditions. For instance, a prototype component may be installed in a jet engine or industrial furnace to observe its behavior under actual operating conditions. Field tests provide practical insights that are difficult to replicate in a lab, ensuring the material’s reliability in its intended application.
Case studies often highlight successful applications of heat-resistant alloys in demanding environments. For example, nickel-based superalloys used in gas turbines have demonstrated exceptional durability, enabling turbines to operate at higher temperatures and efficiencies. Such examples showcase the practical benefits of thorough testing and material selection.
In summary, testing heat resistance involves a combination of laboratory and field methods designed to evaluate an alloy’s performance under thermal stress. These tests ensure that materials meet the stringent requirements of modern engineering applications, providing confidence in their safety and reliability.
Popular Heat-Resistant Alloys and Their Applications
Several heat-resistant alloys have become staples in industries requiring materials capable of withstanding extreme temperatures. Each alloy offers a unique set of properties, making it suitable for specific applications.
Nickel-based alloys, such as Inconel and Hastelloy, are among the most commonly used heat-resistant materials. These alloys excel in high-temperature environments due to their excellent mechanical strength and resistance to oxidation and corrosion. Inconel, for example, is widely used in jet engine components and gas turbines, where temperatures often exceed 1,000°C. Hastelloy is preferred in chemical processing equipment for its ability to resist corrosive environments and high heat.
Stainless steels, particularly those in the austenitic and ferritic categories, are also popular choices. Austenitic stainless steels, like 304 and 316 grades, provide a good balance of heat resistance, corrosion resistance, and cost-effectiveness. These materials are frequently used in applications such as exhaust systems, heat exchangers, and industrial ovens. Ferritic stainless steels, on the other hand, are valued for their thermal conductivity and resistance to scaling.
Cobalt-chromium alloys, often used in aerospace and medical applications, offer exceptional wear resistance and mechanical stability at high temperatures. These alloys are commonly found in jet engine turbine blades and prosthetic implants, where both heat resistance and durability are critical.
Iron-based superalloys provide a more cost-effective alternative to nickel-based superalloys while still delivering good high-temperature performance. These materials are used in less demanding applications, such as industrial furnace components and automotive parts.
Emerging materials are also making waves in the field of heat resistance. For example, titanium aluminides are gaining attention for their lightweight and high-temperature capabilities, making them ideal for aerospace applications. Similarly, ceramics and ceramic-matrix composites are being explored for their ability to withstand extreme temperatures far beyond the limits of traditional metal alloys.
The choice of alloy depends on the specific requirements of the application, including the operating temperature, environmental conditions, and mechanical stresses involved. By selecting the right material, engineers can optimize performance, safety, and cost-effectiveness in high-temperature systems.
Physical and Chemical Mechanisms Behind Heat Resistance
The heat resistance of alloys is rooted in both physical and chemical mechanisms that work together to maintain the material’s stability under high temperatures. These mechanisms are influenced by the alloy’s composition, microstructure, and the interactions between its elements.
A critical physical mechanism is grain boundary strengthening. The microstructure of an alloy consists of grains, and the boundaries between these grains act as barriers to the movement of dislocations, which are defects that weaken materials. Fine-grained alloys have more grain boundaries, which enhance their resistance to deformation at high temperatures. Techniques such as controlled cooling during manufacturing can refine the grain structure, improving heat resistance.
Precipitation strengthening is another key mechanism. This involves the formation of small, stable particles within the alloy’s matrix that impede the movement of dislocations. Elements like aluminum and titanium are often added to alloys to create these precipitates, which enhance mechanical strength and stability at elevated temperatures.
On the chemical side, oxidation resistance is paramount. When exposed to high temperatures, metals are prone to reacting with oxygen, forming scales that degrade the material. Heat-resistant alloys mitigate this by forming protective oxide layers, such as chromium oxide or aluminum oxide. These layers act as shields, preventing further oxidation and maintaining the alloy’s structural integrity.
The interaction between alloying elements also plays a significant role. For instance, the addition of molybdenum can improve creep resistance by reducing the mobility of atoms within the alloy at high temperatures. Similarly, the presence of nickel enhances the alloy’s thermal stability by promoting a face-centered cubic (FCC) crystal structure, which is more stable under heat stress.
Thermal conductivity and expansion are additional factors. Alloys with high thermal conductivity can dissipate heat more effectively, reducing the risk of localized overheating. Low thermal expansion coefficients help minimize thermal fatigue, which occurs due to repeated heating and cooling cycles.
In conclusion, the heat resistance of alloys is the result of a complex interplay between physical and chemical mechanisms. Understanding these processes enables the design of materials that can withstand the most demanding high-temperature environments.
Challenges in Manufacturing Heat-Resistant Alloys
Producing heat-resistant alloys involves overcoming several technical and economic challenges to meet the stringent requirements of high-temperature applications. These challenges stem from the complexity of alloy compositions and the need for precise manufacturing processes.
One major challenge is achieving the desired chemical composition. Heat-resistant alloys often contain multiple elements in specific proportions to optimize their properties. For instance, nickel-based superalloys may include chromium, molybdenum, cobalt, and aluminum in carefully balanced amounts. Ensuring uniform distribution of these elements during alloying is critical, as any inconsistency can compromise the material’s performance.
The manufacturing process itself is also demanding. Techniques such as vacuum induction melting and powder metallurgy are commonly used to produce heat-resistant alloys. These methods require specialized equipment and expertise to maintain the purity and quality of the material. For example, vacuum induction melting prevents contamination from oxygen and other gases, which can weaken the alloy.
Machinability is another hurdle. Heat-resistant alloys are often harder and more abrasive than standard materials, making them challenging to machine and shape. This increases manufacturing costs and necessitates the use of advanced cutting tools and techniques, such as high-speed machining or electrical discharge machining.
Cost considerations are significant as well. The addition of high-performance elements like nickel and cobalt makes these alloys expensive to produce. Balancing cost with performance is a constant challenge, particularly in industries where budget constraints are a factor.
In summary, manufacturing heat-resistant alloys requires addressing challenges related to composition, processing, machinability, and cost. Overcoming these obstacles ensures that these critical materials can meet the demands of modern engineering.
How to Choose the Right Heat-Resistant Alloy
Selecting the right heat-resistant alloy is a crucial decision in engineering and manufacturing. It requires a thorough understanding of the application’s specific requirements, including operating temperature, environmental conditions, and mechanical stress. By carefully evaluating these factors, engineers can identify materials that optimize performance, safety, and cost-effectiveness.
The first consideration is operating temperature. Different alloys are designed to perform within specific temperature ranges. For example, nickel-based superalloys like Inconel excel at temperatures exceeding 1,000°C, making them ideal for jet engines and gas turbines. Stainless steels, on the other hand, are more suited for moderate temperatures, such as those found in industrial furnaces or automotive exhaust systems.
Environmental conditions also play a significant role. In corrosive environments, such as chemical processing plants or marine applications, alloys with high chromium or molybdenum content provide superior resistance to oxidation and corrosion. For example, Hastelloy is a preferred choice for chemical reactors due to its ability to withstand both heat and aggressive chemical exposure.
The mechanical stresses involved in the application must be considered as well. Applications subjected to constant loads or vibrations, like power plant turbines, require alloys with excellent creep resistance and fatigue strength. Materials like cobalt-chromium alloys or titanium aluminides are often used in such scenarios due to their exceptional durability.
Budget and lifecycle costs are additional factors. While high-performance alloys like nickel-based superalloys offer unparalleled heat resistance, their cost can be prohibitive for some projects. In such cases, engineers may opt for more affordable options, such as ferritic stainless steels, that still meet the necessary performance criteria.
Component design can influence material selection too. Complex geometries may require alloys with better machinability or those compatible with advanced manufacturing techniques like additive manufacturing. For instance, 3D printing allows for the production of intricate components using heat-resistant materials, enabling design flexibility and material efficiency.
Finally, consulting with material suppliers and conducting prototype testing can help ensure the chosen alloy meets the application’s requirements. Testing in real-world conditions provides valuable insights into the material’s performance, helping to avoid costly mistakes and ensuring long-term reliability.
By carefully evaluating these factors, engineers can select the most suitable heat-resistant alloy, ensuring optimal performance and cost-effectiveness for their specific application.
Innovations in Heat-Resistant Materials
The field of heat-resistant materials has seen significant innovations in recent years, driven by advancements in material science and engineering. These developments are expanding the boundaries of what is possible in high-temperature applications, enabling new levels of performance and efficiency.
One notable innovation is the development of high-entropy alloys (HEAs). Unlike traditional alloys, which are typically based on one or two primary elements, HEAs are composed of multiple elements in nearly equal proportions. This unique composition results in exceptional mechanical strength, thermal stability, and resistance to oxidation. HEAs are being explored for applications in aerospace, energy, and electronics, where extreme conditions demand superior materials.
Additive manufacturing (AM), commonly known as 3D printing, has also revolutionized the production of heat-resistant components. AM enables the creation of complex geometries that were previously impossible to achieve with traditional manufacturing methods. This allows for more efficient heat dissipation and weight reduction in components such as turbine blades and heat exchangers. Moreover, AM facilitates the use of advanced materials like nickel-based superalloys, further enhancing performance.
Ceramic matrix composites (CMCs) are another area of innovation. These materials offer exceptional heat resistance, far surpassing that of traditional metal alloys. CMCs are lightweight and can withstand temperatures exceeding 1,500°C, making them ideal for applications like jet engine components and thermal protection systems for spacecraft.
Nanotechnology is also playing a role in advancing heat-resistant materials. Nanostructured coatings can be applied to alloys to improve their resistance to oxidation and thermal fatigue. These coatings, often made of materials like aluminum oxide or zirconium oxide, provide an additional layer of protection, extending the lifespan of components in high-temperature environments.
In addition, smart materials are being developed that can adapt to changing thermal conditions. For example, shape-memory alloys can revert to their original form when exposed to heat, making them useful in applications like actuators and sensors in high-temperature systems.
The ongoing research and development in this field promise even more breakthroughs in the future. As industries continue to demand materials that can perform under increasingly extreme conditions, the innovations in heat-resistant materials will play a pivotal role in shaping the next generation of engineering solutions.
Environmental and Sustainability Considerations
In the era of environmental awareness, sustainability has become a critical consideration in the production and use of heat-resistant alloys. These materials, while essential for modern engineering, also present challenges and opportunities in terms of their environmental impact.
Recycling of heat-resistant alloys is one of the most effective ways to reduce their environmental footprint. Many alloys, such as stainless steels and nickel-based superalloys, are highly recyclable. The process involves melting down scrap material to create new components, significantly reducing the demand for raw materials and energy. Recycling not only conserves natural resources but also reduces greenhouse gas emissions associated with mining and processing.
Energy efficiency in production is another key factor. Manufacturing heat-resistant alloys requires high temperatures and specialized processes, which consume significant amounts of energy. By adopting advanced manufacturing techniques, such as vacuum induction melting or powder metallurgy, producers can optimize energy use and minimize waste.
The development of sustainable alloys is also gaining momentum. Researchers are exploring materials that require less energy-intensive production methods or utilize more abundant elements. For example, iron-based alloys, which rely on widely available raw materials, are being engineered to achieve performance levels comparable to those of more expensive and resource-intensive superalloys.
Lifecycle analysis (LCA) is increasingly used to assess the environmental impact of heat-resistant materials. LCA evaluates the entire lifecycle of a material, from raw material extraction to manufacturing, use, and recycling or disposal. This approach helps identify areas for improvement and ensures that sustainability is considered at every stage of the material’s life.
Regulations and certifications also play a role in promoting sustainability. Industry standards encourage the adoption of environmentally friendly practices in the production and use of heat-resistant alloys. For example, certifications like ISO 14001 recognize companies that implement effective environmental management systems.
In conclusion, the push for sustainability in heat-resistant alloys is shaping the way these materials are produced and used. By prioritizing recycling, energy efficiency, and sustainable practices, the industry can reduce its environmental impact while continuing to meet the demands of modern engineering.
Common Misconceptions About Heat Resistance
Despite their critical role in engineering, heat-resistant alloys are often misunderstood. Clearing up these misconceptions is essential for making informed decisions about their use and performance.
One common myth is that heat resistance equals indestructibility. While heat-resistant alloys are designed to perform well under high temperatures, they are not immune to failure. Factors like excessive stress, poor maintenance, or exposure to unexpected environmental conditions can compromise their integrity.
Another misconception is that all heat-resistant alloys are prohibitively expensive. While some materials, such as nickel-based superalloys, can be costly, there are more affordable options, like stainless steels, that still provide excellent performance for moderate temperature applications.
Some believe that heat resistance eliminates the need for maintenance. In reality, even the best materials require regular inspection and care to ensure their longevity. Protective coatings, for instance, may need to be reapplied over time to maintain oxidation resistance.
Lastly, there is a tendency to assume that one alloy fits all applications. The truth is that each application has unique requirements, and selecting the right material involves careful consideration of factors like temperature, environment, and mechanical stress.
By addressing these misconceptions, engineers and decision-makers can better understand the capabilities and limitations of heat-resistant alloys, leading to more effective and efficient use of these materials.
FAQs About Heat Resistance in Alloys
What is the maximum temperature most alloys can withstand?
The maximum temperature depends on the alloy type. Nickel-based superalloys can handle temperatures above 1,000°C, while stainless steels are suitable for moderate temperatures, typically up to 800°C.
How do I maintain the performance of heat-resistant alloys?
Regular maintenance, such as inspecting for wear and reapplying protective coatings, is crucial. Avoid exposing the alloy to conditions outside its design specifications.
Are there affordable options for small-scale applications?
Yes, stainless steels and iron-based alloys offer cost-effective solutions for applications with moderate heat requirements.
Conclusion
Heat-resistant alloys are indispensable in modern engineering, offering the strength and durability needed to thrive in high-temperature environments. From understanding their properties and testing methods to exploring innovations and sustainability, these materials continue to shape industries worldwide. As the demand for advanced materials grows, heat-resistant alloys remain at the forefront of technological progress.