Introduction: The Art and Science of High-Temperature Alloy Casting
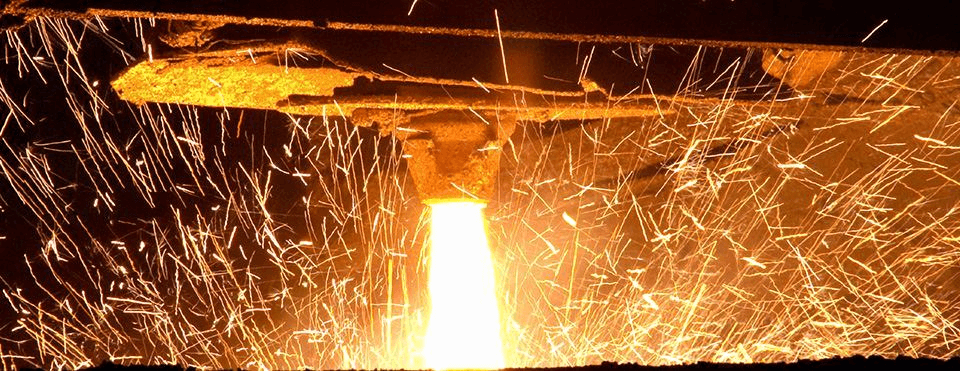
High-temperature alloy casting is an essential process that has revolutionized industries ranging from aerospace to automotive engineering. Whether you’re looking to create durable components for jet engines or intricate parts for industrial machinery, mastering this process is crucial for both novice and seasoned professionals. What makes high-temperature alloy casting so fascinating is its blend of ancient craftsmanship with cutting-edge technology. For centuries, humans have been pouring molten metals into molds to create useful items, but today’s methods take this time-tested technique to a whole new level of precision and complexity.
But wait—why is high-temperature casting so important in modern manufacturing? It’s because materials like titanium, nickel-based superalloys, and stainless steel need specialized handling at extreme temperatures to form the high-performance components required in these sectors. The process is not just about pouring molten metal into a mold; it’s about ensuring the integrity, durability, and quality of the final product. These factors make it a cornerstone of industries that demand excellence, from cutting-edge technology to heavy-duty construction equipment.
Let’s dive deeper. The intricacies of the high-temperature alloy casting process lie in its precision and ability to meet stringent requirements. This article aims to demystify this complex subject, breaking down each step so that you can approach it with confidence. You’ll not only learn about the science behind the process but also gain practical insights into how to apply it effectively in your projects. Whether you’re a beginner trying to grasp the basics or an expert looking for a refresher, there’s something here for everyone.
So, are you ready to master the high-temperature alloy casting process? Stick with me as we explore everything from selecting materials to handling the cooling phase. By the end, you’ll have a comprehensive understanding of this fascinating field and the know-how to execute it flawlessly. Ready? Let’s get started!
Understanding High-Temperature Alloy Casting Basics
What is High-Temperature Alloy Casting?
At its core, high-temperature alloy casting is a manufacturing method where alloys, melted at extremely high temperatures, are poured into molds to create various shapes and forms. Unlike conventional casting methods, this technique is specifically designed for materials that require extreme heat to melt—think titanium, nickel-based alloys, or cobalt-chromium alloys. These materials are prized for their exceptional strength, resistance to wear, and ability to perform in harsh environments, making them indispensable for demanding applications.
Understanding what sets high-temperature alloy casting apart involves diving into its scientific principles. What exactly happens during this process? First, the alloy must reach its melting point, a threshold where it transitions from solid to liquid. For instance, nickel-based alloys often require temperatures exceeding 1,450°C. At these extreme conditions, the alloy becomes malleable enough to fill every nook and cranny of the mold, capturing intricate details with remarkable accuracy. The molten metal’s behavior—its viscosity, thermal expansion, and solidification dynamics—plays a pivotal role in determining the final product’s quality.
Common Materials Used in High-Temperature Alloy Casting
Here’s a crucial point to remember: Not all metals are suitable for this process. The materials must have a melting point compatible with the chosen method and a composition that delivers the desired properties in the final product. For example, nickel-based superalloys are often the go-to choice for aerospace applications because of their excellent thermal stability and resistance to oxidation. Similarly, stainless steel finds extensive use in industrial equipment due to its corrosion resistance and durability.
Other alloys, like titanium and cobalt-chromium, have their own unique advantages. Titanium, for instance, combines lightweight characteristics with impressive strength, making it a favorite in industries like medical implants and sports equipment. Meanwhile, cobalt-chromium alloys are renowned for their biocompatibility and resistance to wear, ideal for applications in dentistry and orthopedic devices.
Key Properties of Materials for High-Temperature Casting
To fully grasp the high-temperature alloy casting process, you need to understand the essential properties that make a material suitable. These include:
- High Melting Point: The material must withstand extreme temperatures without degrading.
- Thermal Stability: Resistance to thermal expansion ensures the alloy retains its shape during cooling.
- Mechanical Strength: Durability under stress is vital for industrial and aerospace components.
- Corrosion and Oxidation Resistance: Especially critical for applications exposed to harsh environments.
So, why does this matter? Because the choice of material directly impacts the casting process and the final product’s performance. Selecting the wrong alloy can lead to defects, inefficiencies, or even catastrophic failures in critical applications.
The Science Behind the Process
Let’s not forget the role of science in ensuring a successful outcome. High-temperature alloy casting isn’t just about melting and pouring—it’s a dance of heat transfer, fluid dynamics, and solidification. When the molten alloy enters the mold, its temperature must be carefully controlled to prevent turbulence, which can cause air pockets and defects. As the metal cools, it undergoes a phase change from liquid to solid, a process influenced by cooling rates and thermal gradients.
But here’s the kicker: Cooling too quickly can lead to cracking, while cooling too slowly might result in unwanted grain structures. This delicate balance underscores the importance of understanding the alloy’s thermal properties and tailoring the process to meet specific requirements.
In conclusion, the basics of high-temperature alloy casting lay a strong foundation for mastering this intricate process. From selecting the right materials to understanding their properties and behavior, each step is critical. Are you ready to dive deeper into preparing for the process? Let’s move to the next section and uncover the essential steps before the molten metal even touches the mold.
Preparing for High-Temperature Alloy Casting
Designing the Mold for High-Temperature Casting
The mold is the unsung hero of the high-temperature alloy casting process. Its design and composition determine the precision, quality, and efficiency of the final product. Here’s why it’s so important: A well-designed mold ensures that the molten alloy flows smoothly, fills every cavity, and solidifies without creating defects. The choice of mold material must withstand extreme temperatures without breaking down, warping, or reacting with the molten metal.
There are three primary types of molds used in high-temperature casting: permanent molds, expendable molds, and investment molds. Permanent molds, often made of metal, are reusable and ideal for producing large quantities of uniform components. However, they require additional considerations, such as cooling channels, to maintain structural integrity during repeated use. Expendable molds, like sand molds, are single-use but highly versatile. They’re particularly useful for casting complex shapes that might otherwise damage a permanent mold. Investment molds, created using a wax pattern coated with a ceramic shell, are perfect for intricate designs and fine details, making them indispensable in industries like aerospace and jewelry.
But here’s the kicker: Designing a mold isn’t just about choosing the right type. The geometry of the mold must account for factors like shrinkage, thermal expansion, and gating systems. Shrinkage occurs as the alloy cools and contracts, so the mold must be slightly oversized to compensate. Thermal expansion can distort the mold’s shape, particularly in high-temperature conditions, necessitating materials with minimal thermal expansion coefficients. Gating systems, which control the flow of molten metal into the mold, must be strategically placed to prevent turbulence and ensure even filling.
Preparing the Workspace for High-Temperature Casting
Safety is paramount when dealing with the extreme conditions of high-temperature alloy casting. The workspace must be equipped to handle molten metal at temperatures exceeding 1,000°C, which means every detail counts. First, ensure that the area is well-ventilated to prevent the accumulation of harmful fumes. Exhaust systems and heat-resistant barriers are a must to protect workers and equipment.
What tools and gear do you need? At the heart of the operation is the furnace, whether it’s an induction furnace for precise temperature control or a gas-fired furnace for cost efficiency. Crucibles, which hold the molten metal, must be made from materials that can withstand repeated heating and cooling cycles, such as graphite or high-grade ceramics. Don’t forget thermocouples and pyrometers for accurate temperature measurement—precision here can mean the difference between success and failure.
Personal protective equipment (PPE) is non-negotiable. Workers should wear heat-resistant gloves, aprons, and face shields to guard against burns and splashes. Specialized footwear and fire-retardant clothing provide additional layers of protection. Emergency protocols, including fire extinguishers and burn treatment supplies, should be readily available. And here’s a pro tip: Always conduct a safety check before starting the process. Inspect equipment for wear and tear, and test ventilation systems to ensure they’re functioning properly.
Why Preparation Matters
Preparation sets the stage for success in high-temperature alloy casting. Skipping these critical steps can lead to defects, wasted materials, or even hazardous accidents. By focusing on meticulous mold design and a well-equipped workspace, you’re building the foundation for a flawless casting process. Ready to dive into the actual casting steps? Let’s move on to the next stage: melting, pouring, and cooling.
Step-by-Step Process of High-Temperature Alloy Casting
Melting the Alloy
Melting the alloy is where the magic begins, transforming solid metal into a molten state ready for casting. But let’s not oversimplify—it’s more than just heating metal. Achieving the perfect melt requires precise control of temperature and a deep understanding of the alloy’s properties. For instance, nickel-based alloys demand temperatures of around 1,450°C, while titanium alloys melt at approximately 1,670°C. Overshooting these temperatures can cause unwanted reactions, such as oxidation, while undershooting can lead to incomplete melting.
Furnaces play a pivotal role in this phase. Induction furnaces, known for their efficiency and precision, are commonly used for high-temperature alloy casting. They use electromagnetic fields to heat the alloy evenly, minimizing the risk of hot spots and thermal gradients. Gas-fired furnaces, though less precise, are another option for melting large quantities of metal. The choice of furnace depends on factors like the alloy type, batch size, and budget.
But wait—there’s more to melting than just heat. Impurities in the alloy can weaken the final product, so fluxes are added to the melt to absorb these contaminants. Slag, a byproduct of this purification process, must be carefully removed to ensure a clean pour. This step is critical because even minute impurities can lead to defects, such as porosity or weak points in the casting.
Pouring the Molten Metal
The pouring phase is a delicate dance of speed, precision, and safety. The molten alloy must be transferred from the furnace to the mold without introducing air pockets or turbulence. Why is this so crucial? Air pockets can create voids in the casting, while turbulence can lead to inclusions or uneven cooling. Preheating the mold helps mitigate these risks by reducing the temperature differential between the molten metal and the mold surface.
Pouring techniques vary depending on the casting method and alloy properties. For instance, vacuum-assisted pouring is often used for titanium alloys to prevent oxidation, while gravity pouring is sufficient for less reactive materials like stainless steel. Regardless of the method, the pouring process must be smooth and controlled, with the molten metal entering the mold at a steady rate.
Cooling and Solidification
Once the molten alloy fills the mold, the cooling phase begins—a critical period that determines the casting’s microstructure and mechanical properties. Cooling rates must be carefully controlled to avoid defects like cracks or warping. Here’s a pro tip: Use chillers or thermal blankets to manage thermal gradients and ensure uniform cooling.
Solidification involves a phase change from liquid to solid, during which the alloy’s grains form and grow. The size and orientation of these grains affect the casting’s strength, ductility, and toughness. Rapid cooling can produce fine-grained structures ideal for high-strength applications, while slower cooling may result in coarser grains suitable for other uses.
The step-by-step process of high-temperature alloy casting requires precision at every stage. From melting and pouring to cooling and solidification, each phase builds on the previous one to create a high-quality casting. But what comes next? Post-casting operations are equally important for achieving the desired finish and performance. Let’s explore these final steps in detail.
Post-Casting Operations
Removing the Casting
Once the alloy has cooled and solidified, it’s time to remove the casting from its mold. This phase can be deceptively challenging, especially for intricate designs or fragile materials. Here’s why: The mold and casting must be separated without causing damage to either. For expendable molds, this process often involves breaking the mold apart using tools like hammers or chisels. Permanent molds, on the other hand, require careful handling to preserve their integrity for future use.
Cleaning and Finishing
The raw casting is rarely perfect—it often needs cleaning and finishing to remove surface imperfections and achieve the desired dimensions. Sandblasting is a common method for cleaning castings, effectively removing residual mold material and smoothing rough surfaces. For more precise finishing, techniques like grinding, machining, or polishing may be employed.
Heat Treatment
Heat treatment is the final step in post-casting operations, enhancing the alloy’s mechanical properties and performance. Techniques like annealing, tempering, or quenching can improve the casting’s strength, ductility, and resistance to wear. But remember: The specific heat treatment method depends on the alloy and its intended application.
Conclusion
High-temperature alloy casting is more than a manufacturing process—it’s an art and a science that requires meticulous attention to detail at every step. From selecting materials and designing molds to managing heat and ensuring proper cooling, each phase builds on the previous one to create a flawless casting. This comprehensive guide has equipped you with the knowledge to approach this process with confidence, whether you’re a beginner or a seasoned expert. So go ahead—apply these principles and take your casting skills to new heights!
FAQ
1. What are the most commonly used alloys in high-temperature casting?
Nickel-based superalloys, titanium, and stainless steel are among the most common due to their strength and heat resistance.
2. How do I prevent defects like porosity or cracks in my castings?
Carefully control cooling rates and use clean, well-prepared molds to minimize defects.
3. Is high-temperature alloy casting suitable for small-scale projects?
Yes, but the process requires precise equipment and materials, even for small batches.
4. What safety precautions are necessary?
Wear heat-resistant PPE, ensure proper ventilation, and have emergency protocols in place.
5. How does investment casting differ from other methods?
Investment casting uses a ceramic mold created from a wax pattern, ideal for intricate designs with high precision.