Shrinkage in metal die-casting is a major concern for manufacturers, often leading to defects such as porosity, warping, or misalignment. The reduction of shrinkage is vital to ensuring high-quality, durable products. In this article, we will discuss the causes of shrinkage, how it affects metal die-casting, and the methods available to minimize its occurrence. Our goal is to provide manufacturers with practical solutions and a deeper understanding of the factors that contribute to shrinkage in die-casting processes.
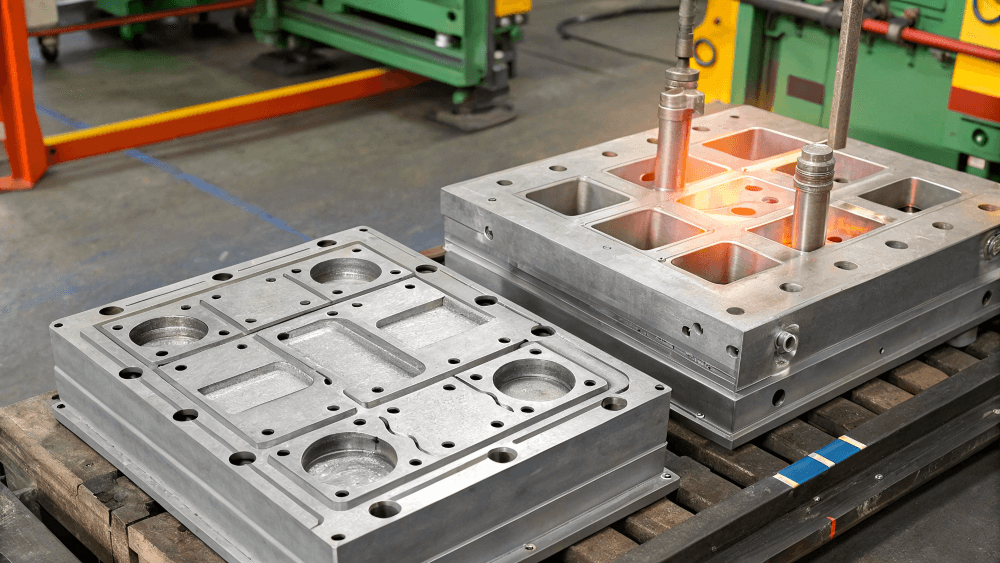
1. What is Shrinkage in Metal Die-Casting?
Shrinkage in metal die-casting refers to the decrease in volume of the metal as it cools and solidifies. This contraction can cause defects like voids, misalignments, and surface blemishes. Understanding the causes of shrinkage is crucial for designing effective solutions. The primary factors responsible for shrinkage include the type of material used, the cooling rate, the design of the mold, and the injection speed.
But here’s the kicker: when shrinkage occurs, it’s not just about the cosmetic appearance of the product. It can also affect the integrity and strength of the cast, leading to structural issues that could compromise the final product. That’s why it’s crucial to identify and mitigate these issues early on in the casting process.
To get a clearer picture, let’s take a look at how shrinkage can manifest in different types of metal die-casting:
Table: Common Shrinkage Defects in Metal Die-Casting
Defect Type | Description | Common Causes |
---|---|---|
Porosity | Small holes in the cast | Inconsistent cooling rate, air entrapment |
Warping | Distortion of the shape | Uneven cooling or improper mold design |
Misalignment | Inaccurate dimensions | Poor mold alignment or excessive shrinkage in one area |
Surface Blemishes | Imperfections on the surface | Inconsistent metal flow or poor mold surface quality |
By understanding these common defects and their causes, manufacturers can take the first steps toward reducing shrinkage.
2. Why Does Shrinkage Occur in Metal Die-Casting?
Shrinkage occurs primarily due to the physics of metal cooling. As metal transitions from a molten state to a solid form, its molecules move closer together, resulting in a reduction in volume. However, several factors can influence the extent of this shrinkage. The primary drivers of shrinkage in metal die-casting include the cooling rate, mold design, and the type of alloy used.
For instance, metals with a high melting point typically experience more shrinkage during the solidification process. But here’s the real story: the cooling rate has the most significant impact. Faster cooling typically leads to uneven shrinkage, which can cause cracks or other structural issues in the final product. On the other hand, slow cooling can result in a more uniform shrinkage but may increase the risk of defects like porosity.
Mold design also plays a critical role. A poorly designed mold can cause uneven cooling and, in turn, result in shrinkage. The positioning of cooling channels and the mold’s geometry can help mitigate these risks. But it doesn’t stop there. The choice of material used in the die-casting process also affects shrinkage. Some materials are more prone to contraction during cooling, while others can maintain their shape more effectively.
Table: Factors Affecting Shrinkage in Metal Die-Casting
Factor | Effect on Shrinkage | Key Considerations |
---|---|---|
Cooling Rate | Fast cooling causes uneven shrinkage | Control cooling speed for uniformity |
Mold Design | Poor designs lead to uneven cooling | Optimize mold geometry and channel placement |
Alloy Type | High melting point alloys shrink more | Choose appropriate alloys for your casting needs |
Injection Speed | Higher speeds may lead to better results | Adjust speed for optimal metal flow |
3. How Can Mold Design Help Reduce Shrinkage?
Mold design is one of the most important factors in controlling shrinkage. Proper mold design ensures that the metal solidifies evenly, preventing excessive contraction in any one area. The most significant aspect of mold design that impacts shrinkage is the layout of cooling channels. A well-designed mold with strategically placed cooling channels allows for the metal to cool uniformly, reducing the risk of defects such as warping or porosity.
But here’s the good part: optimizing mold design doesn’t just reduce shrinkage – it can also improve the overall strength and durability of the final product. For example, molds with a thicker section in areas that will experience more shrinkage can help balance the contraction across the entire part, preventing localized issues.
Mold material selection is also crucial. Using high-quality, durable materials for the mold ensures that it can withstand the high temperatures and pressure conditions required in die-casting while minimizing the potential for shrinkage. The overall design of the mold – including the thickness of its walls, the alignment of its parts, and the type of mold material used – will all influence the degree of shrinkage.
Table: Mold Design Elements That Affect Shrinkage
Mold Design Element | Impact on Shrinkage | Solution |
---|---|---|
Cooling Channels Placement | Even cooling reduces shrinkage | Place channels evenly throughout the mold |
Mold Material | Poor material causes warping | Use high-temperature-resistant alloys |
Mold Wall Thickness | Thicker walls reduce uneven shrinkage | Adjust wall thickness based on part geometry |
4. What Are the Key Factors in Controlling Shrinkage?
Controlling shrinkage requires a multi-faceted approach, as it depends on various factors such as alloy selection, cooling rate, injection speed, and pressure. One of the most effective ways to control shrinkage is by selecting the right alloy for your die-casting process. Certain alloys, like aluminum and zinc, tend to shrink less than others, such as copper or brass, during solidification.
The cooling rate plays an equally important role. A cooling rate that is too fast can cause the metal to contract unevenly, while a rate that is too slow can result in excessive shrinkage. The goal is to find a cooling rate that allows for even solidification without excessive shrinkage.
Pressure management during the casting process can also reduce shrinkage. Using higher pressure during the injection phase helps ensure that the metal fills the mold completely, reducing the chances of voids or porosity forming due to shrinkage.
Table: Key Factors in Shrinkage Control
Factor | Effect on Shrinkage | Control Measure |
---|---|---|
Alloy Selection | Alloys with lower melting points shrink less | Choose alloys like aluminum for less shrinkage |
Cooling Rate | Faster cooling leads to uneven shrinkage | Maintain consistent cooling rates |
Injection Speed | Faster speeds help reduce shrinkage | Adjust speed to match part size |
Pressure Management | Higher pressure reduces shrinkage | Use high pressure for better mold filling |
5. How Does Injection Speed Affect Shrinkage?
Injection speed is another critical factor in reducing shrinkage. When the metal is injected too quickly, it can cause turbulence, leading to uneven cooling and increased shrinkage. On the other hand, too slow an injection can cause the metal to solidify prematurely, leading to incomplete filling of the mold and potentially creating shrinkage-related defects.
Optimizing injection speed involves finding a balance that ensures smooth and consistent metal flow without causing excessive turbulence. Manufacturers can experiment with different injection speeds to determine the best approach for minimizing shrinkage in their specific die-casting processes.
But wait – this is where it gets interesting. Different parts might require different injection speeds based on their size and complexity. Smaller, thinner parts may benefit from slower injection speeds to allow for better control of the metal flow, while larger, more complex parts may need faster injection speeds to ensure proper filling.
Table: Injection Speed and Shrinkage Correlation
Injection Speed | Impact on Shrinkage | Solution |
---|---|---|
Fast Injection | Can cause turbulence and uneven shrinkage | Control speed to minimize turbulence |
Slow Injection | May result in incomplete filling | Use for smaller, intricate parts |
6. Can Mold Material Selection Influence Shrinkage?
The material used to make the mold can directly affect shrinkage. Mold materials that are too soft or have a low melting point might warp or lose their shape under the high temperatures required for die-casting. This can cause inconsistencies in the final cast and lead to increased shrinkage. The key here is selecting mold materials that can withstand these conditions while maintaining their integrity.
Steel alloys and other high-performance materials are commonly used for die-casting molds. These materials can endure the high temperatures and pressure typically found in the casting process, ensuring a more consistent and durable mold that minimizes the risk of shrinkage.
But here’s the kicker – some molds are treated with coatings to improve their resistance to heat and wear. This can help extend the lifespan of the mold and further reduce the likelihood of shrinkage-related issues.
Table: Mold Materials and Their Effects on Shrinkage
Mold Material | Effect on Shrinkage | Advantage |
---|---|---|
Steel Alloys | Highly durable and stable at high temperatures | Minimizes mold deformation |
Aluminum | Good thermal conductivity but prone to wear | Suitable for low-pressure applications |
Coated Molds | Enhanced heat resistance | Extended mold life and stability |
7. What Role Does Cooling Rate Play in Shrinkage?
Cooling rate is one of the most significant factors in controlling shrinkage. The faster the metal cools, the more likely it is that shrinkage will occur in an uneven manner, causing defects like warping and porosity. On the other hand, if the cooling rate is too slow, it can cause excessive shrinkage, leading to dimensional instability and poor surface finish.
The ideal cooling rate strikes a balance that ensures the metal solidifies evenly, preventing both excessive shrinkage and poor surface quality. Manufacturers can control cooling rates by adjusting the mold temperature, using cooling channels, or controlling the temperature of the metal before it’s injected.
But here’s the real story – advanced die-casting techniques, such as high-pressure die-casting, can help control the cooling rate more effectively, leading to reduced shrinkage and higher-quality parts.
Table: Cooling Rate and Shrinkage Management
Cooling Rate | Effect on Shrinkage | Solution |
---|---|---|
Fast Cooling | Leads to uneven shrinkage | Control cooling rate for uniformity |
Slow Cooling | Causes excessive shrinkage | Use for thicker parts with slow cooling |
8. How Does the Metal Alloy Affect Shrinkage?
The choice of alloy plays a significant role in determining the level of shrinkage in die-casting. Alloys with a higher melting point, such as copper, typically experience more shrinkage as they cool, while those with lower melting points, like aluminum, are less likely to shrink. The key is selecting an alloy that balances strength, durability, and shrinkage during the solidification process.
Different alloys have different cooling characteristics, which can lead to varying shrinkage rates. For instance, aluminum alloys tend to have a lower shrinkage rate compared to zinc or magnesium alloys. This makes aluminum a preferred choice for many die-casting applications.
Table: Alloy Types and Their Shrinkage Properties
Alloy Type | Shrinkage Rate | Common Applications |
---|---|---|
Aluminum | Low | Automotive parts, consumer electronics |
Zinc | Moderate | Precision castings, industrial components |
Copper | High | Electrical components, heavy machinery |
9. What Are the Benefits of Pressure Die-Casting in Reducing Shrinkage?
Pressure die-casting offers several advantages over traditional gravity-based methods when it comes to reducing shrinkage. Applying pressure during the injection phase ensures that the molten metal fills the mold completely, minimizing the formation of air pockets and voids that contribute to shrinkage.
One of the biggest benefits of pressure die-casting is the ability to maintain consistent pressure throughout the process, allowing for even cooling and reducing the chances of shrinkage defects.
By using pressure die-casting, manufacturers can achieve higher-density parts with fewer defects, leading to more durable and reliable products. The precise control over pressure also allows for greater flexibility in mold design and material selection.
Table: Pressure Die-Casting vs. Gravity Die-Casting
Type of Die-Casting | Benefits | Key Applications |
---|---|---|
Pressure Die-Casting | Reduces shrinkage, better density | Complex, high-quality parts |
Gravity Die-Casting | Lower cost, simpler designs | Low-volume, less complex parts |
10. How Can Simulation Software Help Control Shrinkage?
Simulation software plays an increasingly important role in die-casting by helping manufacturers predict and control shrinkage before the physical casting process begins. These tools simulate the flow of molten metal into the mold, as well as the cooling process, to identify potential areas where shrinkage may occur.
By using simulation software, manufacturers can make adjustments to mold design, cooling rate, and material selection before even starting the casting process. This predictive approach helps avoid common shrinkage-related issues and results in higher-quality castings with fewer defects.
Table: Benefits of Die-Casting Simulation Software
Benefit | Description |
---|---|
Early Detection of Shrinkage | Predicts shrinkage locations and defects |
Cost-Effective Testing | Avoids physical trial and error |
Optimizes Mold Design | Enhances cooling channels and pressure distribution |
11. What Are the Common Shrinkage Defects in Die-Casting?
Shrinkage-related defects are common in die-casting, and understanding these issues can help manufacturers take corrective actions before they compromise the final product. Common shrinkage defects include:
- Porosity: Small holes or voids in the cast metal caused by trapped air or gases.
- Hot Tearing: Cracking that occurs due to uneven cooling.
- Surface Defects: Imperfections on the surface of the cast that can be caused by inconsistent metal flow.
By identifying these defects early in the process, manufacturers can adjust factors like mold design, injection speed, and cooling rate to prevent them from occurring.
Table: Common Shrinkage Defects in Die-Casting
Defect Type | Description | Potential Causes |
---|---|---|
Porosity | Voids within the cast | Air entrapment, poor cooling |
Hot Tearing | Cracks due to uneven cooling | Rapid cooling, poor metal flow |
Surface Defects | Surface imperfections | Uneven filling or poor mold quality |
12. How Can Post-Casting Heat Treatment Reduce Shrinkage?
Post-casting heat treatment can help reduce shrinkage by relieving the internal stresses that build up during the casting process. Heat treatment involves heating the cast to a specific temperature and then cooling it slowly, allowing for more uniform shrinkage and reducing the risk of distortion or cracking.
Heat treatment can also improve the mechanical properties of the casting, making it stronger and more durable. However, heat treatment must be carefully controlled to avoid introducing new defects such as warping.
Table: Types of Post-Casting Heat Treatment
Heat Treatment Type | Effect on Shrinkage | Key Benefits |
---|---|---|
Annealing | Reduces internal stress | Improves dimensional stability |
Solution Heat Treatment | Relieves shrinkage-related issues | Increases part strength |
Aging | Hardens metal | Enhances mechanical properties |
13. What Are the Latest Technologies to Combat Shrinkage?
Innovations in die-casting technologies have provided new methods for reducing shrinkage. High-pressure die-casting, for example, uses increased pressure to ensure the molten metal fills the mold completely, reducing shrinkage-related defects. Another emerging technology is advanced mold coatings that enhance heat transfer and reduce wear, improving overall mold performance and minimizing shrinkage.
Table: Advanced Die-Casting Technologies
Technology | Benefits | Application |
---|---|---|
High-Pressure Die-Casting | Reduced shrinkage, higher density | Complex, precision parts |
Advanced Mold Coatings | Better heat transfer, mold durability | Increased mold lifespan |
14. How Can Proper Quality Control Prevent Shrinkage Issues?
Quality control is key in identifying and mitigating shrinkage issues during the die-casting process. By regularly monitoring the casting process, manufacturers can identify areas where shrinkage may be occurring and take corrective action before the final product is released.
Proper quality control procedures should include regular inspections, monitoring of cooling rates, and testing for defects like porosity and warping.
Table: Quality Control Measures in Die-Casting
QC Measure | Purpose | Benefits |
---|---|---|
Cooling Rate Monitoring | Ensure even cooling | Minimize shrinkage and defects |
Dimensional Inspection | Check for dimensional stability | Identify misalignment issues |
Defect Testing | Inspect for porosity and cracks | Early detection of shrinkage |
15. How Do Proper Training and Expertise Impact Shrinkage Control?
Skilled technicians play a crucial role in reducing shrinkage during die-casting. Proper training allows workers to understand the complexities of the casting process and how to adjust variables like injection speed, cooling rate, and mold design to minimize shrinkage. Additionally, experienced technicians can identify early signs of shrinkage issues and take immediate corrective action.
Table: Importance of Skilled Labor in Shrinkage Control
Training Type | Impact on Shrinkage Control | Outcome |
---|---|---|
Process Training | Better understanding of shrinkage causes | Improved casting quality |
Hands-On Experience | Identifies shrinkage early | Faster problem resolution |
Technical Skills Development | Accurate adjustments to casting parameters | Reduced defects and better quality |
FAQ Section
Q1: What is shrinkage in metal die-casting?
Shrinkage in metal die-casting refers to the reduction in volume of the metal as it cools and solidifies, often causing defects like porosity, warping, or misalignment.
Q2: How does cooling rate affect shrinkage?
The rate at which the metal cools significantly impacts shrinkage. Faster cooling typically leads to uneven shrinkage, while slower cooling allows for more uniform solidification and reduced shrinkage.
Q3: How can mold design reduce shrinkage?
Optimizing mold geometry, ensuring proper cooling channel design, and selecting the right mold material can all help manage the cooling rate and reduce shrinkage.
Q4: What is the best way to control shrinkage during die-casting?
Controlling shrinkage involves selecting the right alloys, managing injection speed, ensuring consistent temperature control, and using pressure die-casting techniques.
Q5: Can heat treatment reduce shrinkage?
Yes, post-casting heat treatment can reduce shrinkage by relieving internal stresses in the metal, leading to improved dimensional stability.