Introduction
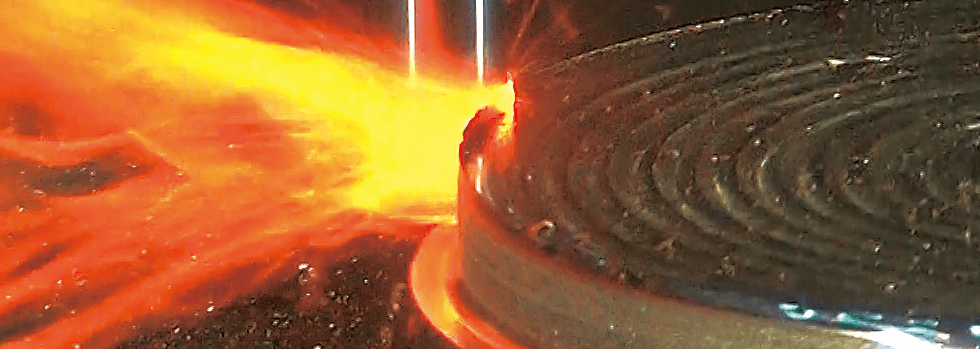
Heat-resistant alloys are critical in industries where extreme temperatures test material limits daily. From aerospace turbines to industrial furnaces, these materials enable innovation and safety. But what makes them so remarkable? Understanding why they excel in resisting high heat isn’t just about grasping the science—it’s about recognizing how these alloys save costs and enhance performance. This knowledge empowers engineers, manufacturers, and innovators to choose the best materials for their needs. In this article, we’ll dive into the structure, properties, and applications of these extraordinary materials to reveal their true potential.
What Are Heat-Resistant Alloys?
Heat-resistant alloys are metallic materials designed to maintain strength and functionality at high temperatures. Unlike pure metals, these alloys consist of combinations of elements that synergize to enhance properties like thermal stability, oxidation resistance, and creep resistance. Commonly, they include metals such as nickel, iron, or cobalt, combined with elements like chromium and molybdenum. The importance of these alloys cannot be overstated in modern engineering. They form the backbone of high-performance applications, especially in environments where failure due to heat could have catastrophic consequences.
The aerospace industry, for example, heavily relies on these materials. Jet engines experience temperatures exceeding 1,000 degrees Celsius, necessitating components that won’t deform or lose strength. Automotive applications, such as exhaust manifolds and turbocharger housings, similarly depend on heat-resistant alloys to perform reliably. Industrial furnaces, reactors, and even power plants also integrate these materials to ensure safety and durability.
Key to understanding these alloys is their ability to withstand high thermal loads without succumbing to oxidation or melting. Unlike pure metals, which often have singular melting points and limited structural integrity under stress, alloys combine the best characteristics of their components. This allows them to retain their shape, strength, and integrity in extreme environments.
In addition to their structural performance, heat-resistant alloys also bring economic benefits. They extend the lifespan of components, reduce maintenance, and prevent costly failures. Their initial cost may be high, but their long-term benefits make them a worthwhile investment. By preventing downtime and improving operational efficiency, these materials prove indispensable across industries. Understanding their role offers insight into the advancements in material science and their contribution to modern technology.
How Do Alloys Differ From Pure Metals?
Pure metals, while valuable in certain contexts, often lack the robustness needed for high-temperature applications. Their singular atomic structure makes them susceptible to specific weaknesses, such as low melting points or poor resistance to deformation under stress. Alloys, on the other hand, blend multiple elements to create a material that compensates for these weaknesses.
When metals are alloyed, their atomic arrangements shift. This creates a more complex microstructure that enhances physical and chemical properties. For example, adding chromium to iron increases resistance to oxidation, while nickel improves overall thermal stability. Each added element contributes specific benefits, enabling the alloy to outperform pure metals in demanding conditions.
The process of alloying also allows for customization. Engineers can tailor the composition of an alloy to meet precise requirements, balancing factors such as strength, ductility, and corrosion resistance. This flexibility makes alloys indispensable in fields where no one-size-fits-all solution exists.
In contrast, pure metals like aluminum or copper have limited applications at high temperatures. Their inherent properties, while advantageous in other ways, cannot compete with the engineered resilience of alloys. Aluminum, for instance, is lightweight and conductive but has a relatively low melting point. Copper resists corrosion well but softens under heat. By alloying these metals with others, their limitations can be addressed, making them suitable for more challenging environments.
A practical example is stainless steel, an alloy of iron, chromium, and nickel. It resists rust and withstands heat far better than pure iron. Similarly, Inconel, a nickel-based alloy, excels in environments that would melt or corrode most pure metals. Understanding the differences between pure metals and alloys reveals why the latter is essential in pushing the boundaries of technology and innovation.
Core Characteristics of Heat-Resistant Alloys
The superior heat resistance of these alloys stems from three primary characteristics: high melting points, resistance to oxidation, and creep resistance. Each of these properties plays a critical role in ensuring performance under extreme conditions.
High melting points are perhaps the most obvious feature. Materials used in jet engines or industrial furnaces must withstand temperatures that would cause most metals to melt or weaken. Alloys achieve this through their composite structure, which distributes thermal energy more effectively than pure metals. For instance, nickel-based superalloys remain stable at temperatures above 1,000 degrees Celsius, far exceeding the capabilities of pure nickel.
Oxidation resistance is equally important. At high temperatures, metals are prone to reacting with oxygen in the air, forming oxides that degrade their surface and compromise their integrity. Elements like chromium are added to heat-resistant alloys to combat this. Chromium forms a thin, stable oxide layer on the material’s surface, preventing further oxidation and preserving the alloy’s structural integrity.
Creep resistance is the ability of a material to resist deformation under long-term stress at elevated temperatures. This is critical in applications like power plants or aerospace turbines, where components are subjected to constant mechanical stress while exposed to extreme heat. Heat-resistant alloys achieve creep resistance through their complex microstructure and the addition of elements like molybdenum. These elements strengthen grain boundaries within the material, reducing the likelihood of deformation.
Together, these characteristics make heat-resistant alloys a cornerstone of high-performance engineering. By understanding how these properties interact and contribute to the overall performance of the material, engineers can select the right alloy for their specific application. This ensures safety, efficiency, and longevity, even in the most demanding environments.
The Role of Nickel, Chromium, and Molybdenum in Heat Resistance
Nickel, chromium, and molybdenum are the unsung heroes of heat-resistant alloys. Each of these elements contributes unique properties that, when combined, create materials capable of withstanding extreme conditions.
Nickel serves as the foundation for many heat-resistant alloys due to its exceptional thermal stability and resistance to oxidation. Its face-centered cubic (FCC) crystal structure remains stable at high temperatures, ensuring the material retains its shape and strength. Nickel also enhances corrosion resistance, making it ideal for applications involving harsh chemical environments, such as chemical processing plants or marine engineering.
Chromium’s primary contribution is its ability to form a protective oxide layer. This thin, stable coating prevents the underlying material from oxidizing further, even at high temperatures. Chromium also improves the alloy’s strength and resistance to wear, making it a crucial component in materials used in jet engines or industrial furnaces.
Molybdenum adds strength and creep resistance. It reinforces the grain boundaries within the alloy, preventing deformation under long-term stress and high heat. Molybdenum is particularly effective in environments where mechanical stress and temperature combine to push materials to their limits.
The synergy of these elements is what makes heat-resistant alloys so effective. By combining their strengths, engineers can create materials that outperform pure metals and other simpler alloys in every measure of high-temperature performance. Understanding the role of each element not only highlights their importance but also underscores the complexity and ingenuity behind modern material science.
The Science Behind Heat Resistance
The ability of heat-resistant alloys to maintain structural integrity and functionality at high temperatures lies in their atomic and molecular design. Thermodynamic stability is at the heart of this capability. When metals are exposed to heat, their atomic bonds weaken, causing structural deformation or melting. Heat-resistant alloys mitigate this by incorporating elements with high bonding energy, ensuring that the material remains stable even under extreme thermal stress.
Crystal lattice configurations also play a significant role in heat resistance. Many high-performance alloys adopt a face-centered cubic (FCC) structure, which is highly symmetrical and resistant to thermal expansion. This structure distributes heat evenly, reducing stress points and preventing warping or cracking. In addition, grain boundaries in the material act as barriers to dislocation movement, further enhancing the alloy’s strength at elevated temperatures.
Precipitation strengthening is another critical factor. By adding elements like aluminum or titanium, manufacturers induce the formation of fine particles within the alloy. These particles hinder dislocation movement, improving strength and resistance to deformation at high temperatures. This is particularly evident in nickel-based superalloys used in jet engines, where the material must endure not only heat but also mechanical stress.
Finally, oxidation resistance ensures that the material does not degrade when exposed to oxygen-rich environments at high temperatures. This is achieved through the formation of stable oxide layers, as seen with chromium in stainless steel. Together, these scientific principles explain why heat-resistant alloys outperform conventional metals, making them indispensable in modern engineering.
How Are Heat-Resistant Alloys Manufactured?
The manufacturing of heat-resistant alloys involves sophisticated processes that enhance their performance and tailor their properties to specific applications. Casting is one of the primary methods, where molten metal is poured into molds and allowed to solidify. This technique is ideal for creating components with complex shapes, such as turbine blades.
Forging, another common method, involves deforming the metal under high pressure to improve its mechanical properties. This process aligns the grain structure, enhancing strength and durability. Heat treatments, such as annealing and quenching, are often applied to further refine the material’s microstructure and optimize its properties.
Advanced techniques like powder metallurgy and additive manufacturing are revolutionizing the field. Powder metallurgy involves compressing metal powders into a desired shape and then sintering them at high temperatures. This method allows for precise control over the material’s composition and density, making it suitable for aerospace and medical applications.
Additive manufacturing, or 3D printing, has opened new possibilities for creating intricate designs and reducing waste. By building components layer by layer, this technology enables the production of parts with complex geometries that would be impossible to achieve through traditional methods.
Each of these manufacturing techniques contributes to the versatility and effectiveness of heat-resistant alloys. By combining traditional methods with cutting-edge technology, manufacturers can meet the growing demands of industries that rely on these exceptional materials.
Real-World Applications and Success Stories
Heat-resistant alloys have transformed industries by enabling innovations that were once thought impossible. In the aerospace sector, these materials are used in turbine blades, combustors, and exhaust nozzles. For instance, nickel-based superalloys in jet engines allow aircraft to operate at higher temperatures, improving fuel efficiency and reducing emissions.
The automotive industry also benefits from these materials. Heat-resistant alloys are essential for components such as exhaust manifolds, turbochargers, and catalytic converters. These parts must withstand the extreme heat generated by internal combustion engines while maintaining performance and durability.
Industrial equipment, including boilers, reactors, and heat exchangers, relies heavily on these alloys to ensure safe and efficient operation. In power plants, for example, components made from heat-resistant materials endure high temperatures and pressures, minimizing maintenance and maximizing output.
Success stories abound. The use of Inconel in space exploration has enabled spacecraft to endure the harsh conditions of re-entry. Similarly, Hastelloy’s corrosion resistance has revolutionized chemical processing, allowing for safer and more efficient production of chemicals. These examples highlight the indispensable role of heat-resistant alloys in advancing technology and improving lives.
Challenges in Working With Heat-Resistant Alloys
While heat-resistant alloys offer unparalleled performance, they come with their own set of challenges. One of the primary issues is machining difficulty. These materials are often harder and more abrasive than conventional metals, causing excessive wear on cutting tools. Specialized equipment and techniques are required to machine these alloys effectively.
Cost is another significant factor. The high price of raw materials, such as nickel and molybdenum, combined with the complexity of manufacturing processes, makes these alloys expensive. However, their longevity and reliability often justify the initial investment.
Joining and welding can also be challenging. The same properties that make these alloys heat-resistant can lead to issues such as cracking or distortion during welding. Advanced welding techniques, such as electron beam or laser welding, are often necessary to ensure a strong and defect-free joint.
Despite these challenges, the benefits of heat-resistant alloys far outweigh their drawbacks. With continued advancements in manufacturing technology and material science, these obstacles are gradually being overcome, making these alloys more accessible and cost-effective.
Key Testing Methods for Heat Resistance
To ensure the reliability of heat-resistant alloys, rigorous testing is essential. Thermal fatigue testing evaluates how materials respond to repeated heating and cooling cycles. This simulates real-world conditions, such as the stress experienced by turbine blades during flight.
Creep testing measures a material’s ability to resist deformation under constant stress and high temperatures. This is critical for components in power plants and industrial furnaces, where materials are subjected to prolonged stress.
Oxidation and corrosion testing assess the material’s durability in harsh environments. By exposing samples to oxygen, chemicals, or extreme temperatures, engineers can predict how the material will perform over time.
Non-destructive testing methods, such as X-ray or ultrasonic testing, are also used to detect internal flaws without damaging the material. These tests ensure the quality and reliability of heat-resistant alloys, giving engineers confidence in their performance.
Comparing Heat-Resistant Alloys
Choosing the right alloy requires a thorough understanding of their strengths and weaknesses. Inconel, a nickel-based alloy, excels in extreme heat and corrosive environments, making it ideal for aerospace and chemical processing. Hastelloy offers similar benefits but with enhanced resistance to certain chemicals, such as hydrochloric acid.
Stainless steel, while less heat-resistant than superalloys, provides a cost-effective option for applications requiring moderate heat resistance and corrosion protection. Comparing these alloys based on performance metrics, such as temperature range and mechanical strength, helps engineers select the best material for their needs.
Ultimately, the choice depends on factors such as the operating environment, budget, and desired lifespan of the component. By understanding the unique properties of each alloy, industries can make informed decisions that optimize performance and cost-efficiency.
Conclusion
Understanding why heat-resistant alloys excel at high temperatures reveals the remarkable science and engineering behind their creation. These materials combine high melting points, oxidation resistance, and creep resistance to deliver unmatched performance in demanding environments. While challenges such as cost and machining difficulty exist, ongoing advancements continue to expand their potential. For industries relying on durability and efficiency, heat-resistant alloys are indispensable. By exploring their properties and applications, engineers and innovators can unlock new possibilities for innovation and success.