Introduction: Why High-Temperature Alloys Matter in Aerospace
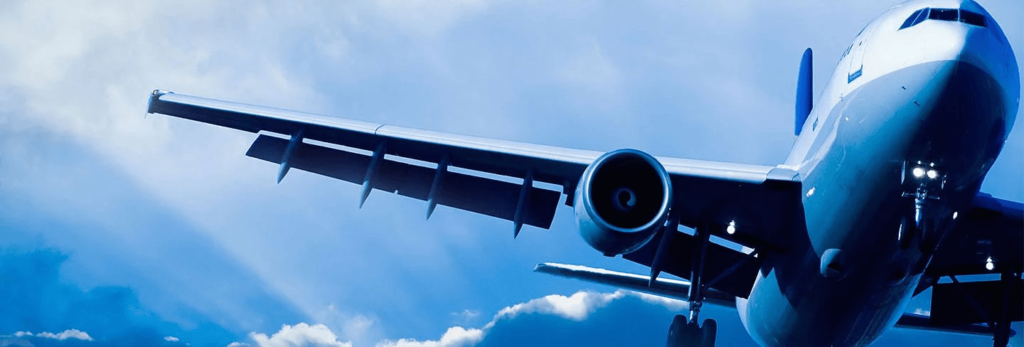
The aerospace industry has always been a frontier of innovation, constantly pushing the boundaries of engineering to meet the harsh realities of flight and space exploration. From soaring temperatures to extreme pressures, the materials used in aerospace must endure conditions few other industries encounter. This is where high-temperature alloys shine, playing a pivotal role in making modern aviation and space travel possible. But what exactly makes these materials so indispensable? Let’s dig into the science and uncover their secrets.
Think about this: an aircraft turbine blade spinning at thousands of rotations per minute (RPM) is exposed to temperatures well above the melting point of ordinary metals. In such an environment, materials must not only resist heat but also maintain mechanical integrity under immense stress. Now imagine the stakes if these components fail mid-flight. The result could be catastrophic! That’s why aerospace engineers rely on high-temperature alloys to provide unmatched thermal stability, durability, and performance.
You might wonder, “What are high-temperature alloys made of?” The answer lies in their unique compositions, often combining metals like nickel, titanium, or cobalt with other elements such as aluminum or molybdenum. These combinations create alloys capable of withstanding temperatures exceeding 1,000 degrees Celsius while remaining resistant to oxidation and corrosion. Sounds impressive, right? Keep reading, because it gets even more fascinating.
The journey to mastering these materials has been long and arduous, but the rewards have been monumental. High-temperature alloys are not just materials—they’re enablers of progress. Without them, advanced technologies like jet engines, reusable spacecraft, and hypersonic vehicles would remain out of reach. So, what makes these alloys so essential, and how can they be used effectively in aerospace? Stick with me, and we’ll uncover every detail. From understanding their properties to exploring real-world applications, this guide has everything you need to know about leveraging high-temperature alloys in aerospace.
Understanding High-Temperature Alloys
To truly appreciate the role of high-temperature alloys in aerospace, it’s crucial to understand what sets them apart from conventional materials. High-temperature alloys, often referred to as superalloys, are specially engineered metals designed to withstand extreme heat, pressure, and chemical degradation. But what makes them so special? Let’s break it down.
First, let’s explore their composition. High-temperature alloys are typically based on nickel, cobalt, or titanium. Each of these metals offers a unique set of properties that make them suitable for different aerospace applications. For instance, nickel-based alloys are highly resistant to heat and corrosion, making them a top choice for turbine blades and combustion chambers. Cobalt alloys, on the other hand, excel in retaining mechanical strength under extreme stress, which is critical in jet engines. Titanium alloys stand out for their lightweight properties, providing a solution to one of aerospace engineering’s biggest challenges—reducing overall weight while maintaining structural integrity.
Now, you might ask, “Why do we need these alloys in the first place?” The answer lies in the demands of aerospace environments. At cruising altitude, an aircraft’s engine operates under conditions where ordinary metals would melt, deform, or break apart. Add to this the exposure to oxidizing gases, thermal cycling (heating and cooling repeatedly), and mechanical stress, and it becomes clear why ordinary materials simply can’t cut it. This is where high-temperature alloys step in, proving themselves indispensable.
What about the properties that make these materials so resilient? One of the key characteristics is their creep resistance, which allows them to maintain shape and strength under prolonged exposure to high temperatures and stress. Additionally, these alloys boast exceptional oxidation and corrosion resistance, ensuring long-term reliability even in chemically aggressive environments. Their thermal conductivity and ability to resist cracking further enhance their performance, particularly in components subject to rapid temperature changes.
Here’s another fascinating fact: the development of high-temperature alloys didn’t happen overnight. It took decades of research and countless iterations to create alloys capable of meeting the stringent demands of aerospace. Scientists continually refine their formulas, introducing elements like chromium for corrosion resistance, aluminum for oxidation resistance, and molybdenum to improve strength. The result? Alloys that are nothing short of engineering marvels.
But let’s not stop there. It’s also important to understand the challenges associated with these materials. Despite their incredible properties, high-temperature alloys can be difficult to work with. Their hardness and resistance to wear, while advantageous in operation, pose challenges during manufacturing. Machining and forming these alloys require advanced techniques and specialized equipment, making them expensive to produce. However, for industries like aerospace, the benefits far outweigh the costs. Stick around as we dive into their applications next—you’ll see why these alloys are worth every penny.
Key Aerospace Applications for High-Temperature Alloys
If high-temperature alloys are the heroes of aerospace materials, their battlefield is the critical components of aircraft and spacecraft. From the roar of a jet engine to the blazing heat of atmospheric re-entry, these alloys prove their worth time and again. Let’s explore where and how they make a difference.
Jet engines are perhaps the most famous application of high-temperature alloys. Every component in a jet engine—from turbine blades to combustors—faces extraordinary heat and pressure. For instance, turbine blades must operate in temperatures exceeding 1,200 degrees Celsius, a feat that would be impossible without nickel-based superalloys. These blades are often coated with ceramic layers to further enhance their thermal resistance, creating a combination that enables modern engines to achieve unprecedented efficiency and power. In fact, without these materials, the commercial aviation industry as we know it simply wouldn’t exist.
Moving to airframes, high-temperature alloys are used in structural components exposed to thermal stress. Supersonic and hypersonic aircraft, which travel faster than the speed of sound, generate immense frictional heat as they slice through the atmosphere. Titanium alloys are often the go-to choice here, offering a perfect balance between heat resistance and lightweight properties. For example, the SR-71 Blackbird, a legendary reconnaissance aircraft, relied heavily on titanium alloys for its frame. This reliance on advanced materials allowed the plane to achieve speeds that remain unmatched even today.
Spacecraft are another domain where high-temperature alloys shine. During re-entry into Earth’s atmosphere, a spacecraft’s outer layers endure temperatures high enough to vaporize most materials. Here, alloys play a critical role in heat shields and other protective components, ensuring the safety of the mission and its crew. Rocket engines, which must withstand both extreme heat and high-pressure combustion, also depend on these alloys to function effectively. Think of SpaceX’s reusable Falcon 9 rockets—their success owes much to the advanced alloys used in their engines and structures.
But the applications don’t end there. High-temperature alloys are also used in smaller components like fasteners and brackets. These may seem insignificant, but in an industry where safety is paramount, every detail matters. These materials ensure that even the smallest parts can withstand the demanding conditions of aerospace environments. Clearly, high-temperature alloys are not just materials—they’re lifelines for modern aviation and space exploration.
Advantages of Using High-Temperature Alloys
So, what makes high-temperature alloys the material of choice for aerospace engineers? The advantages are as diverse as they are compelling, ranging from unparalleled performance to long-term cost efficiency. Let’s break it all down.
First and foremost is their performance in extreme environments. High-temperature alloys are engineered to operate in conditions where ordinary metals fail. Whether it’s the searing heat of a jet engine or the chemical aggression of oxidizing gases, these alloys hold their ground. They don’t just survive—they thrive under pressure, heat, and corrosion.
Another significant advantage is their durability and longevity. By resisting wear and tear over extended periods, these materials reduce the need for frequent maintenance and replacements. This translates to lower operational costs for airlines and space agencies, making them an economically sound choice despite their initial expense. In other words, they pay for themselves over time—a win-win for everyone involved.
Weight reduction is another critical benefit, particularly in an industry obsessed with efficiency. Every kilogram saved means reduced fuel consumption and increased payload capacity. Titanium alloys, in particular, are celebrated for their high strength-to-weight ratio, enabling engineers to design lighter, more efficient aircraft without compromising safety.
Finally, there’s the matter of safety. High-temperature alloys contribute to the overall reliability of aerospace systems by minimizing the risk of material failure. Their ability to withstand extreme conditions ensures that critical components continue to function as intended, even in the most challenging scenarios. In an industry where lives are at stake, such reliability is not just desirable—it’s essential.
But what about the flip side? Are there challenges to using these alloys? Absolutely, and we’ll explore those next. Stay with me—it’s crucial to understand both sides of the coin to appreciate the full picture.
Challenges and Limitations
While high-temperature alloys are undoubtedly remarkable, they are not without their challenges. From manufacturing difficulties to environmental concerns, these materials come with their own set of hurdles. Let’s take a closer look.
One of the most significant challenges is their manufacturing complexity. The same properties that make these alloys so valuable—hardness, strength, and heat resistance—also make them difficult to process. Traditional machining techniques often struggle to shape and form these materials, requiring advanced methods like additive manufacturing or powder metallurgy. This adds to the overall cost and time required for production, making them less accessible for smaller players in the industry.
Cost is another major consideration. High-temperature alloys are expensive to produce, not just because of their raw materials but also due to the specialized processes needed to work with them. This can pose a financial barrier, particularly for emerging aerospace companies or those operating on tight budgets. However, as we’ve discussed, the long-term benefits often outweigh these initial costs. Still, the upfront expense can’t be ignored—it’s a real challenge that the industry must address.
Material limitations also exist. While these alloys excel in many areas, they are not perfect. Trade-offs between thermal resistance, weight, and strength can sometimes limit their applications. For instance, an alloy that performs exceptionally well in high-temperature environments might lack the lightweight properties needed for certain aerospace designs. Balancing these factors is a constant juggling act for engineers.
Lastly, there’s the issue of sustainability. Recycling high-temperature alloys is a complex process due to their intricate compositions. This raises questions about their environmental impact, particularly as the aerospace industry strives to become more eco-friendly. Finding ways to recycle and reuse these materials effectively will be critical for the future.
Despite these challenges, the advantages of high-temperature alloys far outweigh their drawbacks. They remain a cornerstone of modern aerospace engineering, enabling feats that would otherwise be impossible. Up next, we’ll explore how engineers make these tough decisions when selecting materials. Don’t go anywhere—you’ll want to understand this!
Selection Criteria for Aerospace Engineers
When choosing materials for aerospace applications, engineers face a daunting task: balancing performance, cost, and practicality in environments where failure is not an option. High-temperature alloys often emerge as the top choice, but their selection is anything but straightforward. Let’s delve into the criteria that guide these decisions.
The foremost consideration is performance requirements. Every aerospace component has unique demands, from the extreme heat of turbine blades to the mechanical stress endured by fasteners. Engineers must evaluate how a material performs under specific conditions, focusing on factors like creep resistance, oxidation resistance, and fatigue strength. For example, a rocket nozzle exposed to constant thermal cycling requires an alloy capable of maintaining integrity despite rapid heating and cooling. The stakes couldn’t be higher—choosing the wrong material can lead to catastrophic failure.
Another critical factor is cost-effectiveness. While high-temperature alloys are undeniably expensive, their long-term benefits often justify the initial investment. That said, not every aerospace project has the budget for premium materials. Engineers must weigh the potential savings in maintenance and longevity against the upfront costs. This is particularly relevant in commercial aviation, where profit margins are tight, and every dollar counts. The challenge lies in finding a balance that meets performance needs without breaking the bank.
Environmental considerations also play a role. Certain alloys, such as those with high chromium content, offer superior resistance to oxidation and corrosion, making them ideal for chemically aggressive environments. However, engineers must also account for the alloy’s compatibility with other materials in the system. For instance, a material that resists oxidation may still corrode when exposed to specific fuels or lubricants. It’s a delicate dance of chemistry and engineering, requiring meticulous planning and testing.
Then there’s the question of supply chain reliability. Aerospace projects often have tight timelines, leaving little room for delays in material procurement. Sourcing high-temperature alloys from reputable suppliers is critical to ensuring quality and consistency. Engineers also consider the geographic availability of materials, as supply chain disruptions can have far-reaching consequences. In an industry where precision and reliability are paramount, even small delays can derail entire projects.
Ultimately, the selection process is a complex interplay of science, economics, and logistics. Engineers must rely on extensive testing, expert consultation, and sometimes even intuition to make the right choices. Up next, we’ll explore the advanced techniques used to process these remarkable materials. Stick with me—it’s fascinating stuff!
Advanced Techniques for Working with High-Temperature Alloys
Processing high-temperature alloys is as challenging as it is essential. Their unique properties, while beneficial in operation, make them notoriously difficult to manufacture and shape. Over the years, engineers and material scientists have developed cutting-edge techniques to overcome these hurdles. Let’s take a closer look.
One of the most promising methods is additive manufacturing, commonly known as 3D printing. This technology has revolutionized the aerospace industry, allowing for the precise fabrication of complex components with minimal waste. By building parts layer by layer, additive manufacturing enables engineers to create intricate designs that were previously impossible with traditional machining. For high-temperature alloys, this means greater flexibility in design and reduced material waste—a significant advantage given their cost. Additive manufacturing is not just a trend; it’s a game-changer in the world of aerospace materials.
Another widely used technique is investment casting, a process that dates back centuries but has been refined for modern applications. This method involves creating a wax model of the desired component, coating it in ceramic, and then melting the wax away to form a mold. Molten alloy is then poured into the mold, creating a precise and durable part. Investment casting is particularly effective for producing turbine blades and other high-performance components. Despite its age, this technique remains a cornerstone of aerospace manufacturing.
Powder metallurgy is another critical process, especially for producing high-performance alloys. This method involves compressing alloy powders into a desired shape and then sintering them at high temperatures. The result is a component with exceptional density and strength, suitable for demanding applications like rocket engines. Powder metallurgy also allows for the inclusion of rare and expensive elements in precise quantities, minimizing waste and cost. It’s an elegant solution to a complex problem, showcasing the ingenuity of modern engineering.
Processing doesn’t end with fabrication. Heat treatment is a vital step that enhances the properties of high-temperature alloys. By carefully controlling the heating and cooling cycles, engineers can optimize an alloy’s strength, ductility, and resistance to thermal fatigue. Additionally, surface treatments like coatings and claddings are used to further enhance performance, particularly in corrosive or oxidizing environments. Every detail matters, ensuring that these materials meet the stringent demands of aerospace.
Finally, testing and quality assurance play a critical role in the production process. Non-destructive testing methods, such as ultrasonic and radiographic inspections, are used to detect flaws without damaging the material. Stress testing in simulated environments ensures that components will perform as expected under real-world conditions. In aerospace, there’s no room for error, and every component must be flawless before it takes to the skies.
Innovations and Future Trends
The field of high-temperature alloys is far from static. As aerospace technology evolves, so too must the materials that support it. Emerging trends and innovations promise to take these alloys to new heights, enabling applications that were once the stuff of science fiction.
One exciting development is the advent of next-generation materials, such as metal-matrix and ceramic-matrix composites. These materials combine the strength and heat resistance of metals with the lightweight properties of ceramics, creating alloys that outperform even the best nickel or titanium-based options. Ultra-high-temperature ceramics (UHTCs) are also gaining traction, particularly for use in hypersonic vehicles and spacecraft. These materials represent the cutting edge of aerospace engineering, pushing the boundaries of what’s possible.
Another area of innovation is the application of high-temperature alloys in reusable spacecraft. Programs like SpaceX’s Starship and NASA’s Artemis missions are leading the way, demonstrating the need for materials that can withstand repeated use in harsh environments. These alloys are not just components; they’re enablers of the next era of space exploration. Think of the possibilities—commercial space travel, colonization of other planets, and beyond.
Sustainability is also becoming a major focus. Researchers are exploring ways to make high-temperature alloys more eco-friendly, from developing recyclable materials to reducing the environmental impact of production processes. As the aerospace industry grapples with its carbon footprint, sustainable materials will play a crucial role in shaping its future. It’s a challenge, but one that the industry is well-equipped to meet.
Finally, advancements in manufacturing technology continue to drive progress. From AI-driven design optimization to advanced robotics, the tools available to engineers are more powerful than ever. These technologies not only improve the quality of high-temperature alloys but also make their production more efficient and cost-effective. The future of aerospace materials is bright, and high-temperature alloys will remain at the forefront.
Conclusion
High-temperature alloys are the unsung heroes of aerospace engineering, enabling feats that defy imagination. From jet engines to spacecraft, these materials provide the strength, durability, and heat resistance needed to conquer the skies and beyond. While challenges remain—cost, manufacturing complexity, and sustainability—ongoing innovations promise to overcome these hurdles, paving the way for even greater achievements.
As we look to the future, one thing is clear: high-temperature alloys will continue to be a cornerstone of aerospace progress. Their unmatched performance and versatility make them indispensable, ensuring that humanity can reach new heights, whether in the stratosphere or among the stars.
Thank you for joining me on this deep dive into the world of high-temperature alloys. If you’re as fascinated as I am, explore more of our content on advanced aerospace materials!
FAQ
Q: What are the main types of high-temperature alloys used in aerospace?
A: The primary types include nickel-based superalloys, cobalt-based alloys, and titanium aluminides. Each offers unique properties suited to specific applications, such as jet engines, airframes, and spacecraft components.
Q: Why are high-temperature alloys so expensive?
A: Their cost stems from the complexity of their production processes, the rarity of certain raw materials, and the advanced techniques required for machining and forming them.
Q: Can high-temperature alloys be recycled?
A: Yes, but recycling them is challenging due to their intricate compositions. Researchers are working on methods to improve the recyclability of these valuable materials.
Q: How are high-temperature alloys tested for aerospace use?
A: Non-destructive testing methods, such as ultrasonic and radiographic inspections, are used alongside stress testing in simulated environments to ensure flawless performance.
Q: What’s the future of high-temperature alloys?
A: The future lies in next-generation materials like metal-matrix composites and ultra-high-temperature ceramics, as well as sustainable production methods and applications in reusable spacecraft.