In the world of manufacturing, precision investment casting plays a crucial role in producing intricate, high-quality components that meet stringent tolerances and performance requirements. This article will explore the fundamentals of precision investment casting, its benefits, applications, and why it’s an essential process for various industries. With a focus on its process, material selection, and advantages, we will also discuss how businesses can leverage this method for superior product design and manufacturing. Ready for the good part? Let’s dive into the details!
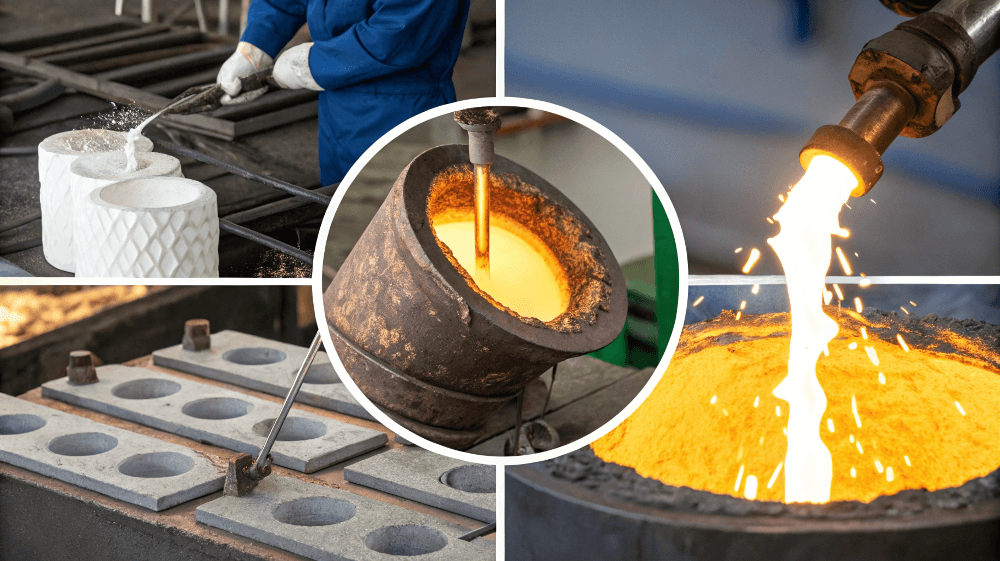
1. Introduction to Precision Investment Casting
Precision investment casting is a specialized manufacturing process used to create high-precision, complex parts that meet tight tolerances. It involves several steps, beginning with the creation of a wax pattern, followed by coating it in a ceramic shell, and then pouring molten metal into the mold to form the final product. What makes this process stand out is its ability to produce intricate shapes and maintain high dimensional accuracy, making it a favorite in industries like aerospace, automotive, and medical devices.
This method offers significant advantages over traditional casting processes, including the ability to cast complex geometries, reduce material waste, and improve part strength. It’s the go-to solution for producing parts that are both lightweight and durable, making it ideal for high-performance applications. But here’s the kicker: precision investment casting isn’t just about the process; it’s also about the materials used and the technological advancements that make it more efficient than ever.
Table 1: Key Advantages of Precision Investment Casting
Advantage | Description |
---|---|
High Precision | Produces parts with tight tolerances and fine details |
Complex Geometries | Can create intricate shapes that are difficult to achieve with other methods |
Material Efficiency | Reduces material waste compared to other methods |
Strength | Creates strong, durable parts suited for high-performance applications |
2. What is Precision Investment Casting?
At its core, precision investment casting is a process that involves creating a part from molten metal by pouring it into a mold made from a wax pattern. The mold is created by coating the pattern in a ceramic shell, which is then heated to remove the wax. Once the mold is prepared, molten metal is poured in, filling the cavity and forming the part.
But what sets precision investment casting apart is its ability to create parts with incredibly detailed features, such as thin walls, intricate internal structures, and complex geometries. This process is far superior to other casting methods like sand casting or die casting when it comes to producing high-precision parts with fewer defects. Ready for the good part? Let’s break it down further with examples from the aerospace industry, where this method is often used for turbine blades, structural components, and more.
Table 2: Comparison of Casting Methods
Casting Method | Precision | Best For |
---|---|---|
Investment Casting | High | Complex geometries, tight tolerances |
Sand Casting | Low | Large, simple parts |
Die Casting | Medium | High-volume production of small parts |
3. The Process of Precision Investment Casting
The precision investment casting process can be broken down into several critical steps, each of which ensures the part is created with high precision and strength. First, a wax pattern is made, often using injection molding or machining. This pattern is then coated in a ceramic shell, which is allowed to harden. Afterward, the shell is heated to remove the wax, leaving behind a hollow mold.
Next, molten metal is poured into the mold, filling the cavity to form the part. After cooling, the mold is broken away, revealing the cast part. The final product is then cleaned and finished, with any necessary machining or adjustments made to ensure it meets the required specifications.
One of the most significant advantages of this process is the ability to use a wide range of materials, including stainless steel, aluminum, and nickel alloys, depending on the part’s requirements. This flexibility makes precision investment casting a versatile option for producing components across various industries. What’s the real story? The materials and technology used in precision investment casting play a key role in its success.
Table 3: Materials Commonly Used in Precision Investment Casting
Material | Application | Advantage |
---|---|---|
Stainless Steel | Aerospace, automotive | Corrosion resistance, strength |
Aluminum | Automotive, consumer products | Lightweight, good strength-to-weight ratio |
Nickel Alloys | Aerospace, medical devices | High-temperature resistance, durability |
4. The Role of Pattern Creation in Investment Casting
Pattern creation is one of the most important aspects of the precision investment casting process. It involves creating a model of the part to be cast, typically from a material like wax. This model is then coated in a ceramic shell to form the mold for the molten metal. The precision of the pattern directly affects the quality and accuracy of the final part, making it crucial to ensure the pattern is made with high detail.
In addition to traditional wax patterns, modern technologies such as 3D printing are increasingly being used to create more complex and detailed patterns. This technology allows manufacturers to produce patterns with intricate internal features that would be difficult or impossible to achieve with traditional methods. This is where it gets interesting: 3D printing opens up new possibilities for precision investment casting, allowing for faster prototyping and more complex designs.
Table 4: Comparison of Pattern Materials
Pattern Material | Advantage | Disadvantage |
---|---|---|
Wax | Easy to work with, detailed | Melts during mold creation |
3D Printed | Allows for complex designs | Expensive, limited material options |
Metal | Durable, strong | Harder to create intricate details |
5. Key Advantages of Precision Investment Casting
Precision investment casting offers several key advantages that make it a popular choice for industries requiring high-performance parts. One of the most significant benefits is the ability to produce parts with extremely tight tolerances and high precision. This means that parts can be produced with minimal post-production machining, reducing both cost and lead time.
Another advantage is the ability to create complex geometries. Unlike other casting methods, precision investment casting can produce parts with intricate shapes and thin walls, making it ideal for industries like aerospace and medical devices. The process is also highly material-efficient, minimizing waste and allowing manufacturers to use expensive materials more effectively. Ready to take it up a notch? Let’s explore how these advantages translate into real-world applications.
Table 5: Benefits of Precision Investment Casting
Benefit | Description |
---|---|
Precision | High dimensional accuracy with minimal post-machining |
Complex Geometries | Capable of producing intricate shapes |
Material Efficiency | Reduces waste, saving costs on materials |
Strength | Produces strong, durable parts for high-performance applications |
6. Common Materials Used in Precision Investment Casting
Precision investment casting is highly versatile in terms of the materials that can be used. Stainless steel is one of the most common materials, chosen for its corrosion resistance and strength. It is ideal for applications that require durability, such as in the aerospace and automotive industries.
Aluminum is another popular material due to its lightweight properties, making it perfect for applications where weight reduction is important, such as in automotive and consumer products. Nickel alloys are often used in high-temperature applications, such as turbine blades in jet engines, due to their ability to withstand extreme conditions.
The choice of material plays a significant role in the performance of the final product, so manufacturers must carefully select the right material for each specific application. But here’s the kicker: the right material ensures the part can handle the stresses it will face in its end-use application.
Table 6: Material Selection for Investment Casting
Material | Typical Use | Key Benefits |
---|---|---|
Stainless Steel | Aerospace, automotive | Corrosion resistance, strength |
Aluminum | Automotive, consumer products | Lightweight, good strength-to-weight ratio |
Nickel Alloys | Aerospace, medical devices | High temperature resistance, durability |
7. The Importance of Quality Control in Investment Casting
Quality control is critical in precision investment casting, as it ensures the final part meets the required specifications and performs reliably in its intended application. The process typically includes several inspection methods, such as visual inspections, dimensional checks, and non-destructive testing (NDT) techniques like X-ray inspection.
One of the most important aspects of quality control is ensuring that the parts are free from defects, such as porosity, cracks, or inclusions, which can compromise the strength and performance of the part. Manufacturers use various methods to detect and eliminate these defects, ensuring the cast parts meet the required quality standards. What’s the real story? Effective quality control is what separates a high-performance part from a subpar one.
Table 7: Common Quality Control Methods in Investment Casting
Method | Purpose | Advantage |
---|---|---|
Visual Inspection | Detect surface defects | Quick and cost-effective |
Dimensional Checks | Ensure part meets specifications | High precision, critical for tight tolerances |
X-ray Inspection | Detect internal defects | Non-destructive, highly accurate |
8. Applications of Precision Investment Casting
Precision investment casting is used across a wide range of industries, with some of the most significant applications being found in aerospace, automotive, and medical devices. In aerospace, this method is used to produce turbine blades, structural components, and landing gear parts, all of which require high strength and precision.
In the automotive industry, precision casting is used to create engine components, transmission parts, and other high-performance components that need to meet strict standards for safety and durability. Medical devices, particularly those that require intricate, high-precision parts like surgical instruments or implants, are another key application of precision investment casting.
But here’s the kicker: precision investment casting isn’t just for large industries – it’s also used in consumer products like jewelry and electronics, where small, high-quality parts are needed. The versatility of this method makes it applicable across diverse industries.
Table 8: Key Applications of Precision Investment Casting
Industry | Applications |
---|---|
Aerospace | Turbine blades, structural components, landing gear |
Automotive | Engine components, transmission parts |
Medical Devices | Surgical instruments, implants |
Consumer Products | Jewelry, electronics |
9. Trends and Innovations in Precision Investment Casting
The precision investment casting industry is continuously evolving, with new technologies and innovations driving improvements in materials, design, and process efficiency. One major trend is the increasing use of 3D printing to create more complex and detailed patterns for investment casting. This technology allows manufacturers to produce parts faster, with greater flexibility in design.
Another significant development is the adoption of digitalization in the casting process, enabling manufacturers to improve the accuracy and consistency of the final parts. With the rise of Industry 4.0, automation and data analytics are playing an increasingly important role in optimizing the investment casting process. What’s the real story? These innovations are making precision investment casting faster, more efficient, and more versatile than ever before.
Table 9: Latest Trends in Precision Investment Casting
Trend | Description |
---|---|
3D Printing | Enables more complex patterns and faster production |
Digitalization | Improves accuracy and consistency through automation |
Industry 4.0 | Uses data analytics to optimize the process |
10. How Precision Investment Casting Enhances Product Design
Precision investment casting offers significant advantages when it comes to product design. One of the key benefits is the ability to produce parts with intricate geometries and features that would be difficult or impossible to achieve with traditional manufacturing methods. This enables designers to create components that are both lightweight and strong, helping to improve the overall performance of the product.
Moreover, precision casting can help reduce material waste by allowing for near-net-shape production. This is especially important when working with expensive materials, such as titanium or high-performance alloys, as it ensures that the material is used efficiently and cost-effectively. What’s the real story? Precision casting allows designers to push the boundaries of what’s possible in product design, leading to more innovative and efficient products.
Table 10: Benefits of Precision Casting in Product Design
Benefit | Description |
---|---|
Complex Geometries | Enables the production of intricate shapes and features |
Lightweight Components | Reduces weight while maintaining strength |
Material Efficiency | Reduces waste, ensuring efficient use of expensive materials |
11. Choosing the Right Investment Casting Supplier
Selecting the right supplier for precision investment casting is crucial to ensuring that your parts meet the required standards for quality and performance. When evaluating potential suppliers, consider their experience in the industry, their technical capabilities, and their ability to produce the parts you need with the required precision.
It’s also important to assess their quality control procedures and their ability to meet deadlines. After all, you don’t want to be stuck with delays or defective parts that don’t meet your specifications. Ready for the good part? Let’s break down what to look for when choosing the right supplier.
Table 11: Criteria for Choosing an Investment Casting Supplier
Criteria | Importance |
---|---|
Experience | Ensures expertise in precision investment casting |
Quality Control | Critical for ensuring high-quality parts |
Delivery Times | Ensures timely production and delivery |
Technical Capabilities | Ensures the ability to meet complex design needs |
12. The Cost-Effectiveness of Precision Investment Casting
While precision investment casting can be more expensive than other casting methods, it offers significant cost savings in the long run. The high precision and low material waste associated with the process reduce the need for additional machining or adjustments, which can help save money on post-production.
Additionally, precision casting is ideal for high-volume production runs, as the molds can be reused multiple times, reducing the cost per part. What’s the real story? Despite its higher upfront costs, precision investment casting can be a highly cost-effective solution for manufacturing complex, high-performance parts.
Table 12: Cost Breakdown of Precision Investment Casting
Cost Component | Description |
---|---|
Tooling | Initial cost of mold creation |
Materials | Cost of raw materials used in the casting process |
Labor | Cost of labor involved in the casting and finishing process |
Post-Production | Costs for machining and inspection after casting |
13. Precision Investment Casting vs. Other Manufacturing Methods
Precision investment casting stands out when compared to other manufacturing methods like die casting, sand casting, or forging. While sand casting is suitable for larger, simpler parts, it can’t achieve the same level of precision or detail as investment casting. Die casting, on the other hand, is more efficient for high-volume production of smaller parts but lacks the ability to produce complex geometries.
The flexibility of precision investment casting makes it the preferred method when complex shapes, tight tolerances, and high-strength parts are needed. Ready to take it up a notch? Let’s break down how precision investment casting compares to other methods in terms of key factors like cost, precision, and material options.
Table 13: Comparison of Manufacturing Methods
Manufacturing Method | Precision | Cost | Best For |
---|---|---|---|
Precision Investment Casting | High | Medium | Complex parts, tight tolerances |
Die Casting | Medium | Low | High-volume, small parts |
Sand Casting | Low | Low | Simple, large parts |
Forging | High | High | High-strength parts |
14. Environmental Considerations in Precision Investment Casting
Precision investment casting is a relatively sustainable manufacturing process, thanks to its material efficiency and reduced waste generation. The use of recyclable materials, such as stainless steel and aluminum, helps minimize the environmental impact. Additionally, advancements in energy efficiency and waste reduction have made the process even more environmentally friendly.
However, there are still some challenges, particularly regarding the energy-intensive nature of the melting process. What’s the real story? The precision investment casting industry is actively working to improve sustainability through better materials and more efficient processes.
Table 14: Environmental Impact of Investment Casting
Environmental Factor | Impact |
---|---|
Material Waste | Low due to near-net-shape production |
Energy Consumption | High due to the melting process |
Recycling | High potential for material recycling |
15. Conclusion: Why Precision Investment Casting is the Future of Manufacturing
Precision investment casting is an essential manufacturing process that offers unmatched precision, versatility, and material efficiency. From aerospace to automotive to medical devices, industries worldwide rely on this method to create high-performance parts with complex geometries and tight tolerances. The growing adoption of new technologies, such as 3D printing and digitalization, is making precision investment casting even more efficient and accessible.
In conclusion, precision investment casting is the go-to solution for industries seeking high-quality, cost-effective parts that meet the demands of modern manufacturing. Whether you’re producing components for aerospace or designing intricate jewelry, this process can help you achieve the precision and performance your projects require.
FAQ Section
Q1: What is precision investment casting?
Precision investment casting is a process used to create high-precision, complex parts by pouring molten metal into a mold made from a wax pattern.
Q2: How does the precision investment casting process work?
The process involves creating a wax pattern, coating it in a ceramic shell, removing the wax, and then pouring molten metal into the mold to form the part.
Q3: What are the key advantages of precision investment casting?
The primary benefits include high precision, the ability to create complex shapes, reduced material waste, and cost efficiency.
Q4: What materials are used in precision investment casting?
Common materials include stainless steel, aluminum, and nickel alloys, each chosen based on the requirements of the part being produced.
Q5: How do I choose the right investment casting supplier?
Consider factors such as experience, technical capabilities, quality control procedures, and delivery times when selecting a supplier.