Why Understanding High-Temperature Alloys is Critical
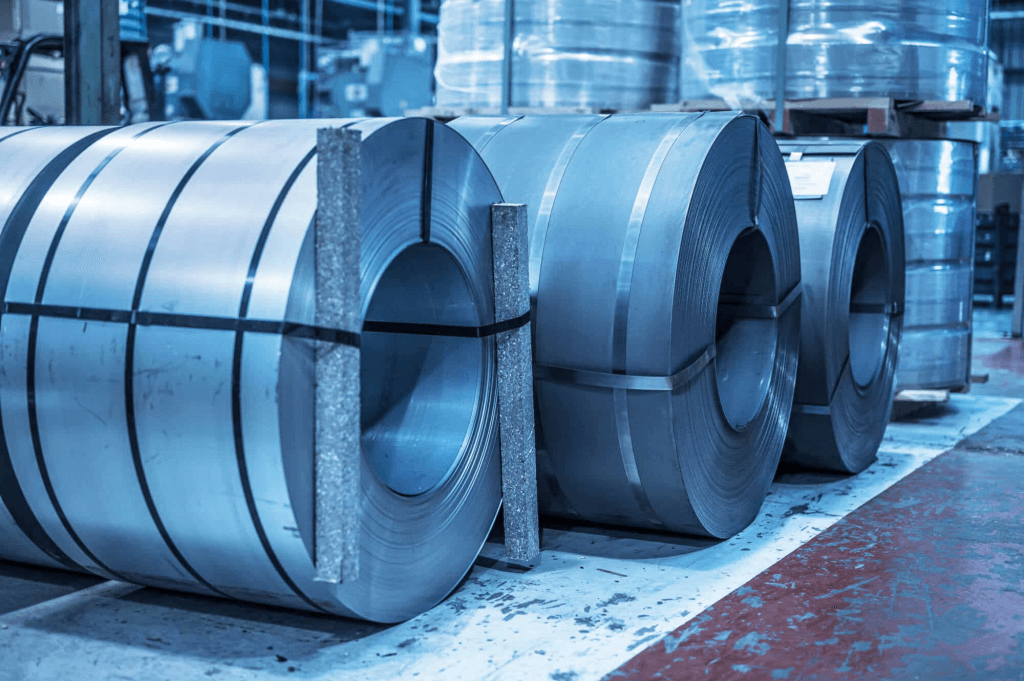
In industries where performance meets extremes, high-temperature alloys are the unsung heroes holding everything together. From the relentless heat inside jet engines to the grueling conditions of power plants, these materials are pivotal. But why are they so crucial? It’s because their unique properties defy the limitations of ordinary metals. While most materials falter when exposed to high heat, these alloys exhibit remarkable stability, strength, and resistance, making them indispensable in engineering and manufacturing.
Think about it—every time you fly, the turbine engines beneath the wings are operating at thousands of degrees Celsius, far beyond what traditional metals can withstand. This isn’t just impressive; it’s life-saving. High-temperature alloys make this possible because they are specifically engineered to handle thermal and mechanical stress. Without them, modern aviation and energy production as we know it would simply crumble.
Now, let’s dig deeper into the scope of their use. Aerospace isn’t their only playground. These alloys also find applications in gas turbines, nuclear reactors, and even automotive components like turbochargers. Their ability to endure harsh conditions without losing their structural integrity gives engineers a competitive edge in designing durable and reliable systems.
Still with me? Great, because here’s another fascinating detail: these alloys are not a single entity. They come in various compositions, each tailored to meet specific demands. For example, a nickel-based alloy used in turbine blades is different from a cobalt-based alloy designed for medical implants. The science behind these materials is as complex as their applications are diverse.
Let’s not forget, the story doesn’t end with performance. High-temperature alloys must also pass rigorous testing to ensure they meet industry standards. Tests like creep resistance, oxidation endurance, and thermal expansion are part of the process. Why does this matter? Because the reliability of these materials could mean the difference between success and catastrophic failure in critical systems. In the following sections, we’ll explore what makes high-temperature alloys exceptional and how their properties are meticulously determined.
What Are High-Temperature Alloys?
High-temperature alloys are not just another category of materials; they are a marvel of modern engineering, purpose-built for environments where ordinary metals would fail. These alloys are meticulously engineered to maintain their strength, stability, and performance even under extreme thermal conditions. So, what exactly qualifies as a high-temperature alloy? In essence, these are materials capable of withstanding prolonged exposure to high heat, usually above 500°C (932°F), without losing their mechanical integrity or undergoing excessive corrosion.
The classification of high-temperature alloys generally falls into three main groups: nickel-based, cobalt-based, and iron-based alloys. Each has its distinct advantages. For instance, nickel-based alloys are celebrated for their exceptional strength and oxidation resistance, making them a go-to choice in aerospace and power generation. Cobalt-based alloys, on the other hand, excel in wear resistance and are often used in medical and dental applications. Finally, iron-based alloys, though less heat-resistant than the other two, are cost-effective solutions for applications requiring moderate thermal resilience.
But there’s more! What makes these alloys so special is their intricate composition. They are typically made by blending a base metal—such as nickel, cobalt, or iron—with additional elements like chromium, molybdenum, aluminum, and titanium. These secondary elements enhance specific properties, such as resistance to oxidation, improved creep strength, or enhanced corrosion resistance. The result is a tailored material designed to thrive in demanding environments.
Industries relying on these alloys are as varied as their compositions. Aerospace, for example, uses high-temperature alloys in jet engines, where extreme heat and stress are constants. The energy sector employs these materials in turbines and reactors, while the automotive industry finds them invaluable for turbochargers and exhaust systems. It’s no exaggeration to say that high-temperature alloys form the backbone of modern engineering.
But wait, there’s more! The versatility of these alloys also extends to cutting-edge fields like additive manufacturing and advanced medical technologies. Their adaptability means they are constantly evolving, with new formulations pushing the boundaries of what’s possible. In the next section, we’ll delve into the key properties that set these materials apart, offering a closer look at why they are indispensable in so many industries.
Key Properties of High-Temperature Alloys
What makes high-temperature alloys so extraordinary? Their properties go beyond what conventional metals can achieve, ensuring performance and reliability under conditions that would destroy other materials. At the heart of these alloys’ uniqueness are four fundamental properties: thermal resistance, mechanical strength, oxidation resistance, and controlled thermal conductivity. Each of these traits plays a critical role in their effectiveness.
Thermal resistance is perhaps the most defining feature of high-temperature alloys. Unlike standard metals, which tend to soften and lose structural integrity at elevated temperatures, these alloys retain their strength and hardness even in extreme heat. How is this achieved? The answer lies in their microstructure, which is specifically designed to resist the diffusion of atoms—a key factor that leads to deformation at high temperatures.
Mechanical strength is equally vital, particularly in applications that involve heavy loads or stress. High-temperature alloys boast impressive tensile strength, meaning they can endure significant force without breaking. Creep resistance—a material’s ability to resist slow deformation under constant stress at high temperatures—is another critical property. Why does this matter? Because in industries like aerospace, even minute deformations can lead to catastrophic failures.
Oxidation and corrosion resistance set high-temperature alloys apart from their peers. In harsh environments where exposure to oxygen and corrosive substances is inevitable, these materials form protective oxide layers on their surfaces, preventing further degradation. This property is particularly crucial in gas turbines and chemical processing plants, where corrosion could otherwise lead to frequent maintenance or early component failure.
Lastly, thermal conductivity and expansion deserve mention. While high-temperature alloys are generally poor conductors of heat compared to materials like copper, this characteristic is often beneficial, as it minimizes heat transfer in applications requiring thermal insulation. Controlled thermal expansion also ensures that components maintain dimensional stability during temperature fluctuations, which is essential for precision engineering.
But there’s more to the story! Each of these properties is influenced by the alloy’s composition and heat treatment processes, making the selection of the right alloy for a specific application both an art and a science. In the upcoming sections, we’ll explore the advanced methods used to test and verify these properties, shedding light on how engineers ensure these materials meet stringent performance standards.
Methods to Determine Properties
Determining the properties of high-temperature alloys is no straightforward task. These materials are destined for critical applications, where even the smallest flaw can have devastating consequences. So, how do engineers and scientists ensure these alloys perform as expected? Through a combination of rigorous testing methods, each designed to evaluate specific characteristics. Let’s dive into the details.
Physical property testing is the first step in understanding a high-temperature alloy’s performance. Techniques like dilatometry are used to measure thermal expansion, providing insights into how a material changes in size when exposed to heat. Similarly, Differential Scanning Calorimetry (DSC) is employed to analyze heat capacity and thermal transitions, helping engineers predict how the material will behave under thermal stress. Why is this important? Because understanding these properties is crucial for designing components that must fit precisely, even under varying temperatures.
Next comes mechanical property testing, which evaluates an alloy’s ability to withstand forces without failure. Tensile strength tests are conducted to determine how much stress the material can endure before breaking. Creep testing, on the other hand, examines the alloy’s resistance to slow deformation under prolonged stress at high temperatures. Hardness tests, such as Rockwell, Brinell, and Vickers methods, further assess the material’s resistance to surface deformation and wear. Each of these tests provides a piece of the puzzle, ensuring the alloy’s mechanical reliability.
Chemical analysis is another cornerstone of property determination. Techniques like X-ray fluorescence (XRF) and Inductively Coupled Plasma Mass Spectrometry (ICP-MS) are used to precisely identify the elements in an alloy. This step is vital because even minor variations in composition can significantly impact performance. Ever wonder why quality control is so stringent? It’s because consistent chemical composition ensures predictable behavior, a non-negotiable requirement for high-stakes applications.
Finally, corrosion and oxidation resistance are assessed through specialized tests. High-temperature exposure tests simulate the harsh environments the alloy will face, while salt spray tests evaluate resistance to corrosive chemicals. These tests are indispensable, especially in industries like aerospace and energy, where materials are constantly exposed to aggressive conditions.
In the following section, we’ll explore how non-destructive testing techniques complement these methods, offering additional assurance without compromising the material’s integrity.
Non-Destructive Testing Techniques
Non-destructive testing (NDT) is a game-changer when it comes to evaluating high-temperature alloys. Unlike destructive methods that involve cutting, breaking, or otherwise damaging a sample, NDT allows engineers to assess a material’s properties without altering its usability. Why is this so important? Because in many cases, the materials being tested are costly or irreplaceable components intended for critical applications.
One of the most common NDT techniques is ultrasonic testing (UT). This method uses high-frequency sound waves to detect internal flaws or inconsistencies within the material. By analyzing how sound waves travel through the alloy, engineers can identify cracks, voids, or inclusions that might compromise performance. The best part? UT is quick, precise, and can be applied to components of various shapes and sizes.
Eddy current testing is another valuable technique, particularly for detecting surface and near-surface defects. By introducing a magnetic field into the material, this method can reveal irregularities based on changes in electrical conductivity. What’s fascinating about eddy current testing? It’s highly sensitive and effective for detecting even microscopic flaws.
Advanced imaging techniques like X-ray and computed tomography (CT) scanning take NDT to the next level. These methods provide detailed visualizations of the internal structure of a material, offering insights into its homogeneity and detecting hidden defects. It’s like having X-ray vision for metals!
But wait, there’s more! Magnetic particle testing and dye penetrant testing are also widely used, especially for identifying surface cracks in ferromagnetic and non-ferromagnetic materials, respectively. These methods are particularly useful for ensuring the integrity of components that will undergo high-stress conditions.
In the next sections, we’ll shift focus to the standards and guidelines that govern the testing and application of high-temperature alloys, ensuring consistency and reliability across industries.
Common Standards and Guidelines
High-temperature alloys, due to their critical applications, must adhere to stringent standards and guidelines that ensure their reliability and performance. These standards are the benchmark for quality, providing a uniform framework that manufacturers, engineers, and testers follow globally. But why are standards so critical in this field? They ensure consistency, safety, and compatibility across industries that depend on these advanced materials.
One of the most widely recognized organizations in this realm is ASTM International (American Society for Testing and Materials). ASTM standards cover various aspects of high-temperature alloys, from their chemical composition to mechanical properties and testing methods. For instance, ASTM E139 specifies procedures for conducting creep tests, a vital method for assessing an alloy’s long-term strength under high stress and temperature. These guidelines are not optional; they are the backbone of the industry.
ISO (International Organization for Standardization) standards also play a crucial role. These globally recognized protocols ensure that high-temperature alloys meet international requirements, making cross-border collaboration and application seamless. Standards like ISO 6892-2 outline the methodology for tensile testing at elevated temperatures, ensuring consistent results regardless of geographical location. This harmonization is vital, particularly in sectors like aerospace, where components are often sourced from multiple countries.
Aerospace Material Specifications (AMS) further exemplify the importance of tailored standards. AMS documents provide detailed requirements for materials used in aircraft and space vehicles, emphasizing high-temperature alloys for their unparalleled performance. These specifications are designed to guarantee reliability under the extreme conditions typical of aerospace applications. Imagine the consequences of a failure in such environments—it’s unthinkable!
In addition to these, national and industry-specific guidelines exist, addressing the unique demands of sectors like power generation and automotive engineering. These frameworks ensure that high-temperature alloys are not only fit for purpose but also align with environmental and safety regulations.
What’s the takeaway? Standards and guidelines are the unsung heroes of the high-temperature alloy industry, providing the assurance that these materials will perform as intended. As we move forward, let’s explore the challenges associated with testing these alloys and how emerging trends are shaping the future of this field.
Challenges in Testing High-Temperature Alloys
Testing high-temperature alloys is a complex endeavor, fraught with challenges that stem from their very nature and the environments in which they are used. These materials are engineered for extremes, and evaluating their properties requires methods that are equally robust and precise. What are the main hurdles? Let’s take a closer look.
One significant challenge is the handling and preparation of high-temperature alloys for testing. These materials are often hard and resistant to conventional machining, making sample preparation both time-consuming and costly. Why does this matter? Because improper preparation can compromise the accuracy of test results, rendering them unreliable.
Accuracy issues are another pressing concern. High-temperature tests, such as creep and thermal expansion evaluations, must replicate real-world conditions as closely as possible. Small deviations in testing parameters—such as temperature control or applied stress—can lead to significant errors. This is a high-stakes game, where precision is not just a preference but a necessity.
Cost is an omnipresent factor in testing these alloys. Advanced equipment, such as high-temperature furnaces and specialized sensors, comes with a hefty price tag. Add to this the skilled personnel required to operate these systems, and it’s clear why testing high-temperature alloys is a considerable investment. But here’s the catch: the cost of failure is even higher, making rigorous testing an unavoidable expense.
There’s also the issue of replicating environmental conditions. High-temperature alloys are often used in environments that combine heat with other stressors, such as corrosion or cyclic loading. Simulating these complex scenarios in a laboratory setting is incredibly challenging, yet necessary to gain a full understanding of an alloy’s performance.
Still wondering why testing is so demanding? It’s because the applications of these alloys leave no room for error. Whether it’s a jet engine or a nuclear reactor, the consequences of material failure are catastrophic. In the next section, we’ll explore emerging trends that are helping to overcome these challenges, offering innovative solutions for the future of alloy testing.
Emerging Trends in Alloy Property Testing
The field of alloy testing is evolving rapidly, driven by advancements in technology and the increasing demands of modern engineering. Emerging trends are addressing longstanding challenges, offering innovative ways to evaluate high-temperature alloys with greater precision and efficiency. What’s on the horizon? Let’s explore the cutting-edge developments reshaping this field.
One exciting trend is the use of advanced simulation tools like Finite Element Analysis (FEA). By creating virtual models of materials and subjecting them to simulated stresses and temperatures, engineers can predict an alloy’s behavior without physical testing. Why is this a game-changer? Because it significantly reduces the time and cost associated with traditional methods while providing invaluable insights into performance.
Artificial Intelligence (AI) and Machine Learning (ML) are also making their mark. These technologies analyze vast datasets from past tests to identify patterns and predict outcomes for new alloys. Imagine having an AI assistant that not only identifies the best alloy for a specific application but also suggests ways to enhance its properties. This is no longer science fiction; it’s happening now.
Additive manufacturing, or 3D printing, is another frontier. As industries increasingly adopt this technology for creating complex components, there’s a growing need for testing methods tailored to 3D-printed alloys. These materials often have unique microstructures compared to their traditionally manufactured counterparts, necessitating specialized evaluation techniques.
Finally, green testing methods are gaining traction. With sustainability becoming a priority across industries, researchers are developing eco-friendly testing processes that minimize environmental impact. These include using less energy-intensive equipment and reducing waste during sample preparation and testing.
The future of alloy testing is bright, but it’s also dynamic. As these trends continue to evolve, they promise to make testing more efficient, accurate, and sustainable. In the next section, we’ll discuss practical tips for engineers and technicians working with high-temperature alloys, providing actionable insights for real-world applications.
FAQ: Frequently Asked Questions
1. What are the primary elements used in high-temperature alloys?
Nickel, cobalt, and iron are the most common base metals, often combined with elements like chromium, molybdenum, aluminum, and titanium to enhance properties.
2. How is creep resistance tested?
Creep resistance is evaluated by applying a constant load to a material at a specific temperature and measuring its deformation over time.
3. Can high-temperature alloys be 3D-printed?
Yes, additive manufacturing is increasingly used for producing high-temperature alloy components, though testing methods may vary for these materials.
4. What industries rely on high-temperature alloys?
Key industries include aerospace, power generation, automotive, and medical fields, each with unique requirements for alloy performance.
5. Why are standards like ASTM and ISO important for high-temperature alloys?
They ensure consistency, safety, and reliability, providing a uniform framework for manufacturing, testing, and application.
Congratulations on making it to the end of this guide! By now, you have a comprehensive understanding of high-temperature alloys and the fascinating science behind their properties and testing. Whether you’re an engineer, technician, or enthusiast, these insights will empower you to make informed decisions in this crucial field.