Stainless steel is one of the most commonly used materials in various industries, from manufacturing to construction, due to its strength, corrosion resistance, and versatility. However, two major processes, stainless steel casting and forging, offer distinct advantages depending on the intended application. In this article, we’ll dive into the differences, benefits, and applications of stainless steel casting and forging. By the end of this article, you’ll understand how to choose between these methods based on the specific needs of your projects.
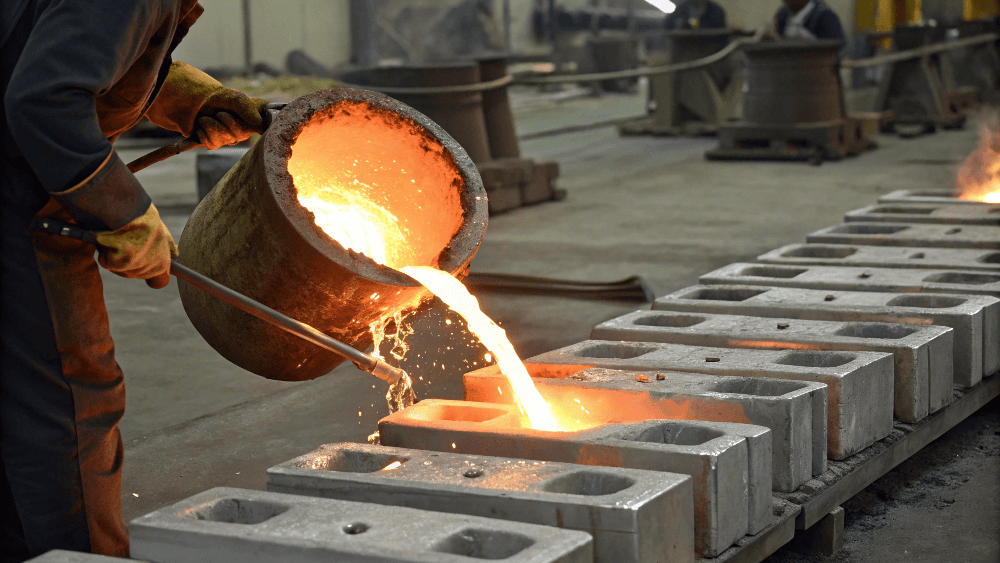
1. What is Stainless Steel Casting?
Stainless steel casting is a manufacturing process where molten stainless steel is poured into a mold to form specific shapes. This technique allows for high precision and can produce complex geometries that would be difficult or costly to achieve with other methods. Casting is commonly used for creating parts that require intricate designs, such as valve bodies, pump housings, and engine components.
But here’s the kicker – while casting is ideal for intricate shapes, it may not provide the same strength as forged components. It’s crucial to understand when to choose casting over other methods. Stainless steel casting is typically used for both low and high-volume production runs. The molten metal is poured into molds made of sand, investment materials, or metal molds. Once the metal cools and solidifies, the mold is removed, leaving a precise replica of the desired shape.
Stainless steel casting can be classified into different types based on the materials used, including investment casting, sand casting, and die casting. Each of these methods offers distinct advantages depending on the complexity and scale of the production. For instance, investment casting is often preferred when the part requires high precision and detailed features, while sand casting is better suited for larger parts or lower production runs.
One major advantage of stainless steel casting is its ability to create complex geometries that would be hard to achieve using traditional machining. Components with intricate internal channels, hollow sections, or detailed surface finishes can be easily produced, reducing the need for secondary processes. This efficiency helps reduce costs and lead times.
Stainless Steel Casting Types | Advantages | Applications |
---|---|---|
Investment Casting | High precision, complex shapes | Aerospace, medical devices |
Sand Casting | Suitable for large parts | Automotive, heavy machinery |
Die Casting | High production rate | Mass production, consumer goods |
2. What is Stainless Steel Forging?
Stainless steel forging is a process where stainless steel is heated to a high temperature and then shaped by applying compressive forces. Unlike casting, which involves pouring molten metal into molds, forging works by deforming the metal to achieve the desired shape. The forging process enhances the material’s properties, particularly its strength and fatigue resistance, making it ideal for high-stress applications.
What’s the real story? While casting offers flexibility in part design, forging provides enhanced mechanical properties, especially in terms of strength and durability. The forging process is primarily divided into two types: open-die forging and closed-die forging. Open-die forging involves shaping the material by repeatedly hammering or pressing it, while closed-die forging uses molds to shape the material.
Forged stainless steel components are highly resistant to fatigue and wear, making them an excellent choice for critical applications, such as components in high-pressure systems, aerospace parts, and heavy-duty machinery. The process creates a material with a refined grain structure, improving its mechanical properties compared to cast parts.
The key advantage of forging over casting lies in its ability to produce parts with superior strength and reliability. Because the forging process works with solid metal, it eliminates the porosity and voids that may exist in cast parts, resulting in components that are more resistant to cracks and failure.
Stainless Steel Forging Types | Advantages | Applications |
---|---|---|
Open-Die Forging | Strong, customizable shapes | Aerospace, automotive |
Closed-Die Forging | Precise, high-volume production | Oil and gas, medical devices |
3. Key Differences Between Stainless Steel Casting and Forging
When it comes to stainless steel casting vs forging, understanding the key differences between these two processes is essential to making the right choice for your project. Both methods are widely used across industries, but they serve different purposes based on the requirements of the application.
Here’s where it gets interesting – casting is ideal for producing parts with complex shapes and intricate details, while forging excels at delivering superior mechanical properties like strength and toughness. The choice between casting and forging depends on several factors, including the part’s intended use, production volume, and material properties required.
Casting allows for greater flexibility in terms of design and is suitable for producing complex shapes that would be challenging to create through other manufacturing methods. On the other hand, forging is known for producing stronger, more durable components. It’s often used in high-stress applications where performance and reliability are paramount.
One of the major differences between these two methods is their impact on material properties. Forging enhances the strength and grain structure of the metal, making it more resistant to fatigue, wear, and corrosion. In contrast, casting parts may have imperfections like porosity or inclusions that can affect their performance under stress. While casting is generally more affordable and better suited for large production runs, forging is the better option for high-performance, critical components.
Aspect | Stainless Steel Casting | Stainless Steel Forging |
---|---|---|
Material Properties | Less dense, potential porosity | Stronger, more durable |
Part Design Flexibility | Highly flexible | Limited by forging capabilities |
Suitable Applications | Complex shapes, mass production | High-stress, high-performance |
4. Benefits of Stainless Steel Casting
The benefits of stainless steel casting are numerous, and understanding these advantages can help you determine if this method is the right choice for your manufacturing needs. One of the main benefits of casting is its ability to produce complex shapes with high precision. This makes it particularly useful for parts that would be difficult or impossible to create with traditional machining methods.
Ready for the good part? Casting allows for a wide range of shapes and sizes, which makes it ideal for manufacturing everything from small, intricate components to large industrial parts. The process also offers cost efficiency for low to medium-volume production runs, particularly when the required parts have complex geometries.
Another significant benefit of stainless steel casting is its versatility in material selection. Depending on the specific needs of your application, you can choose from a variety of stainless steel alloys that offer different levels of corrosion resistance, strength, and toughness. This flexibility ensures that the final product meets the performance requirements of the application.
Casting also saves time and labor by eliminating the need for additional machining processes. Once the casting is made, it is often ready to use with minimal finishing required. This can significantly reduce the lead time and production costs.
Benefits of Stainless Steel Casting | Applications |
---|---|
Precision in Complex Shapes | Aerospace, automotive |
Cost-efficient for Mass Production | Industrial equipment, pumps |
Reduced Post-production Machining Needs | Medical devices, valves |
5. Benefits of Stainless Steel Forging
Stainless steel forging offers distinct advantages that make it a popular choice for industries requiring high-performance parts. The primary benefit of forging is the enhanced mechanical properties it imparts to the metal. By applying high heat and compressive forces, the material’s grain structure is refined, resulting in a part that is stronger and more durable.
But here’s the kicker – forging creates parts with superior fatigue resistance, making it ideal for components subjected to high stresses and harsh operating conditions. Forged parts are less likely to fail under extreme pressure, making them a safer and more reliable choice for critical applications such as aerospace, military, and automotive industries.
Another advantage of stainless steel forging is its ability to produce parts with consistent material properties, even in large production runs. Unlike casting, where the material properties can vary due to imperfections in the mold, forged components typically exhibit uniformity and consistency throughout the entire part.
Forging also improves the overall performance of components, as it eliminates voids and inclusions that can weaken the part. This leads to better performance in demanding applications where the integrity of the material is crucial for safety and reliability.
Benefits of Stainless Steel Forging | Applications |
---|---|
Superior strength and toughness | Aerospace, automotive components |
Increased fatigue resistance | Oil and gas, mining equipment |
Consistent material properties | Heavy machinery, structural parts |
6. Applications of Stainless Steel Casting
Stainless steel casting is widely used across various industries due to its ability to create parts with complex geometries and high precision. Automotive and aerospace industries heavily rely on casting to produce parts such as engine components, exhaust manifolds, and landing gear. These industries require parts that can withstand high temperatures and pressures, and casting is an excellent method for achieving the necessary material properties.
Chemical processing is another industry that benefits from stainless steel casting. Pump housings, valves, and pressure vessels are often cast to provide the strength and corrosion resistance needed for handling chemicals in harsh environments. Stainless steel casting is also used in the production of marine equipment due to its resistance to corrosion in saltwater.
Medical equipment manufacturers also use stainless steel casting for producing surgical tools, implants, and devices that require high precision and biocompatibility. Casting allows for the production of parts with intricate designs and fine details, ensuring that the final product meets stringent industry standards.
Applications of Stainless Steel Casting | Industries |
---|---|
Automotive and Aerospace | Engine components, landing gear |
Chemical Processing | Valves, pump housings |
Medical Devices | Surgical instruments, implants |
7. Applications of Stainless Steel Forging
Stainless steel forging is particularly beneficial for applications where high strength, durability, and resistance to wear are required. Heavy-duty machinery often uses forged stainless steel components, such as gears, shafts, and bearing housings. The superior strength of forged parts makes them ideal for handling high torque and mechanical stress.
Oil and gas industries also rely on stainless steel forging for components that must endure extreme temperatures and pressures. Forged valves, flanges, and connectors are commonly used in drilling and pipeline systems. These parts must withstand aggressive environmental conditions and constant mechanical stress.
In the automotive sector, forged components such as crankshafts, suspension parts, and connecting rods are widely used. The strength and toughness of forged stainless steel allow these parts to perform well under high-stress conditions, such as during high-speed driving or heavy load-bearing applications.
Applications of Stainless Steel Forging | Industries |
---|---|
Heavy-duty Machinery | Gears, shafts, bearings |
Oil and Gas | Valves, flanges, connectors |
Automotive | Crankshafts, suspension parts |
8. Factors to Consider When Choosing Between Casting and Forging
When deciding between stainless steel casting and forging, several factors come into play. The most important consideration is the mechanical properties required for the final product. If strength, durability, and resistance to fatigue are essential, forging is typically the better choice.
Another key factor is the complexity of the part design. Casting offers far greater flexibility when it comes to producing intricate shapes or parts with hollow sections. If your product requires high precision or complex geometries, casting is the method of choice.
The production volume also plays a significant role. Casting is ideal for low to medium-volume production runs, while forging is better suited for high-volume, high-performance applications. However, forging is often more costly due to the labor-intensive process and higher material waste.
Factor | Stainless Steel Casting | Stainless Steel Forging |
---|---|---|
Mechanical Properties | Good for complex shapes, moderate strength | Superior strength, resistance to fatigue |
Complexity of Design | Ideal for intricate shapes | Limited by forging capabilities |
Production Volume | Suitable for low to medium volume | High-volume, high-performance |
9. How Stainless Steel Casting and Forging Impact Product Performance
The choice between casting and forging directly affects the performance of the final product. In general, forged stainless steel offers superior mechanical properties due to its refined grain structure. The forging process results in parts that are denser, stronger, and more resistant to wear and fatigue.
On the other hand, cast parts may exhibit more variability in their properties due to imperfections such as voids or inclusions. Although casting can still produce strong components, it typically falls short in terms of durability when compared to forged parts.
So, what’s the bottom line? Forging is typically the best choice when strength, reliability, and performance are critical, while casting offers significant advantages in terms of design flexibility and cost efficiency for certain applications.
Process | Strength | Durability |
---|---|---|
Stainless Steel Casting | Moderate | Lower in high-stress applications |
Stainless Steel Forging | High | Superior, high-performance |
10. Stainless Steel Casting Process in Detail
Stainless steel casting involves several key steps, each designed to produce a final part with the necessary dimensional accuracy and surface finish. The process begins with preparing the mold or pattern, which can be made from sand, metal, or investment materials. After preparing the mold, molten stainless steel is poured into the cavity to form the desired shape.
The metal cools and solidifies inside the mold, and the mold is then removed to reveal the part. Investment casting is commonly used for parts requiring high precision, while sand casting is ideal for larger parts. After the casting is removed, it is often subjected to heat treatment and surface finishing processes to meet the required mechanical properties.
Stainless Steel Casting Process | Step | Description |
---|---|---|
1. Pattern Preparation | Sand or metal molds | Create the pattern for the part |
2. Pouring | Molten stainless steel | Metal is poured into the mold |
3. Cooling and Solidification | Mold removal | Allow the metal to cool and solidify |
4. Post-processing | Heat treatment, finishing | Improve material properties and finish |
11. Stainless Steel Forging Process in Detail
The stainless steel forging process begins by heating the raw material to a specific temperature, usually above 1000°C. Once the material reaches the desired temperature, it is placed into a die where it is shaped by applying compressive forces. This process refines the grain structure of the material, improving its strength and toughness.
After the part is forged, it is often subjected to heat treatment to further enhance its properties. The final step is surface finishing, which ensures the part meets the required surface roughness and dimensional accuracy.
Stainless Steel Forging Process | Step | Description |
---|---|---|
1. Heating | High temperature treatment | Raise the material to forging temperature |
2. Shaping | Die pressing | Apply compressive force to shape the material |
3. Heat treatment | Post-forging enhancement | Improve material properties |
4. Surface finishing | Final preparation | Ensure desired surface finish |
12. The Future of Stainless Steel Casting and Forging
The future of stainless steel casting and forging looks promising, with several exciting trends and innovations shaping the industry. New techniques like 3D printing and automation are already making their way into both casting and forging processes, improving efficiency and precision.
Ready for the good part? Innovations in material science and manufacturing technology are allowing manufacturers to produce even stronger, more durable stainless steel components. As the demand for high-performance materials continues to grow, casting and forging will evolve to meet these new challenges.
Future Trends | Stainless Steel Casting | Stainless Steel Forging |
---|---|---|
3D Printing | Improved design flexibility | Enhanced material properties |
Automation | Faster production cycles | Increased precision and speed |
Advanced Material Science | Stronger alloys, better performance | Higher strength, reduced weight |
13. Comparing Cost Efficiency: Stainless Steel Casting vs Forging
When it comes to cost efficiency, stainless steel casting and forging each have their own advantages. Casting tends to be more cost-effective for large production runs, especially when complex shapes are involved. However, forging can be more economical in high-performance applications where the final part’s durability and reliability are paramount.
So, how do you decide? Casting is typically a better choice when production volume is high and intricate designs are required, while forging is ideal for components that must withstand extreme conditions.
Cost Comparison | Stainless Steel Casting | Stainless Steel Forging |
---|---|---|
Initial Investment | Lower upfront costs | Higher upfront costs |
Production Speed | Faster for large volumes | Longer production times |
Long-term Costs | More economical for high volumes | Better long-term reliability |
14. Comparing Stainless Steel Casting and Forging in Performance
Performance is where stainless steel casting and forging truly diverge. While both processes produce high-quality parts, forging generally excels in high-stress environments due to its superior mechanical properties. Cast parts can sometimes experience porosity or other material defects that reduce performance, while forged parts offer enhanced strength, toughness, and fatigue resistance.
The final performance of a component largely depends on the application and the material properties required. If the part must withstand extreme pressure or high stress, forging is often the better choice.
Performance Factors | Stainless Steel Casting | Stainless Steel Forging |
---|---|---|
Strength and Toughness | Moderate | Superior |
Fatigue Resistance | Moderate | High |
Performance in High-Stress Conditions | Moderate | Excellent |
15. Conclusion
In conclusion, understanding the differences between stainless steel casting and forging is crucial for making the right choice based on your project’s needs. Both methods offer unique advantages, but selecting the right one depends on factors like material strength, design complexity, and production volume.
If your project requires complex geometries, low-volume production, and cost efficiency, casting may be the ideal option. However, for high-performance applications that demand strength, toughness, and reliability, forging is the best choice.
FAQ Section
Q1: What is stainless steel casting?
Stainless steel casting is a process where molten stainless steel is poured into molds to create parts with precise shapes and complex geometries.
Q2: How does stainless steel forging work?
Stainless steel forging involves heating the material and shaping it by applying compressive forces. This results in stronger and more durable parts compared to casting.
Q3: What are the main differences between stainless steel casting and forging?
The primary differences are material properties, cost, and the ability to produce complex shapes. Casting is better for intricate designs, while forging offers higher strength and durability.
Q4: Which method is more cost-effective: casting or forging?
Casting is generally more cost-effective for large production runs, especially for parts with complex shapes. Forging, while more expensive, offers superior strength and reliability.
Q5: Can stainless steel casting and forging be combined in production?
Yes, in some cases, both processes can be used together to achieve the best balance of complexity and mechanical strength in the final product.