Aluminum casting is a widely used process that allows manufacturers to create a wide range of products. This versatile method offers various benefits, including precision, flexibility, and cost-effectiveness. If you’re considering aluminum casting for your next project, it’s essential to understand the different casting methods, their applications, and how to overcome common challenges. This article delves into the most popular aluminum casting ideas, helping you make informed decisions. Let’s explore the various methods, applications, and advantages of aluminum casting and how they can benefit your business.
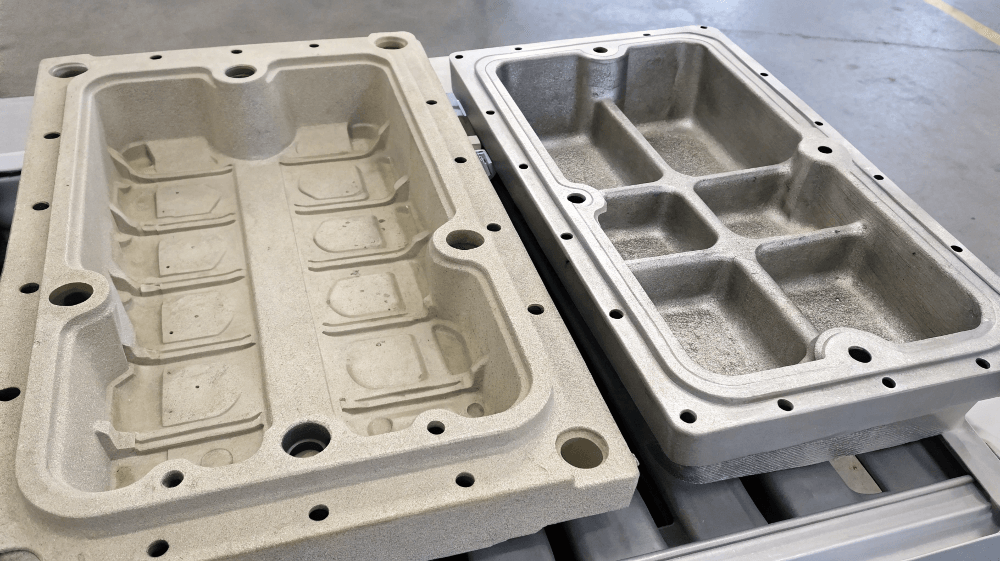
1. What Are Aluminum Castings and How Are They Made?
Aluminum castings are a crucial part of various industries, especially in sectors like automotive, aerospace, and manufacturing. The aluminum casting process involves melting aluminum and pouring it into a mold to solidify into a desired shape. It’s a highly versatile method, capable of producing intricate designs with excellent surface finishes.
But here’s the kicker: Understanding the process is vital for getting the best results. In the aluminum casting process, molten aluminum is carefully poured into a mold cavity, where it cools and solidifies, taking the mold’s shape. There are several methods for casting aluminum, including sand casting, die casting, and investment casting. Each method has its strengths and is chosen based on the complexity of the design, material properties, and production volume.
To ensure the casting is successful, several factors need to be considered, such as the temperature of the molten aluminum, the type of mold, and the cooling rate. A skilled technician must also monitor the entire process to avoid defects like porosity or cracks.
One key element of aluminum casting is the ability to produce complex shapes without the need for additional machining. This is especially useful for industries where parts need to be lightweight yet durable, such as in the aerospace sector.
Casting Method | Mold Material | Ideal Applications | Advantages |
---|---|---|---|
Sand Casting | Sand | Automotive, Large parts | Low cost, Flexibility |
Die Casting | Steel | High-volume, Precision parts | High accuracy, Speed |
Investment Casting | Wax/ceramic shell | Aerospace, Intricate designs | High precision, Fine finish |
2. Why Should You Consider Aluminum Casting?
When it comes to manufacturing, aluminum casting is often the preferred choice due to its numerous advantages. For one, it’s a cost-effective method for producing high-quality components in large quantities. But what’s the real story? Aluminum casting offers significant flexibility, allowing manufacturers to create parts of various sizes and shapes without excessive material waste.
Another reason to consider aluminum casting is its ability to provide excellent precision and finish. The process can achieve tight tolerances, which is crucial in industries like automotive and aerospace, where precision is a must. Moreover, aluminum castings can be designed with minimal need for post-casting machining, further reducing manufacturing costs and time.
Aluminum casting also provides exceptional material properties. Aluminum itself is lightweight, corrosion-resistant, and offers a high strength-to-weight ratio, making it suitable for industries where performance is critical. Whether it’s creating engine components or aircraft parts, aluminum casting is up to the task.
Let’s not forget the versatility of aluminum. It can be cast in different alloys to suit specific needs, further increasing the material’s appeal for various applications. This adaptability makes it a top choice for companies across multiple sectors, from automotive to industrial manufacturing.
Property | Aluminum Castings | Benefits | Common Industries |
---|---|---|---|
Weight | Lightweight | Reduced weight in parts | Automotive, Aerospace |
Strength-to-Weight | High | Improved strength and performance | Automotive, Construction |
Corrosion Resistance | Excellent | Durability in harsh environments | Marine, Industrial |
3. What Are the Different Types of Aluminum Casting Methods?
Aluminum casting comes in several methods, each with unique benefits and applications. So, which method should you choose?
Sand casting is one of the oldest and most widely used methods. In this process, a mold is created by packing sand around a pattern of the part to be cast. Once the sand mold is created, molten aluminum is poured into the mold and left to cool. Sand casting is ideal for creating large, simple parts or low-volume production runs. The key benefit of sand casting is its flexibility and low setup costs.
Die casting is another popular aluminum casting method, especially for high-volume production. In die casting, molten aluminum is injected into a steel mold under high pressure. This process results in parts with a smooth finish and high precision. It’s commonly used in industries like automotive, where large quantities of complex parts need to be produced quickly and at high precision.
Permanent mold casting involves pouring molten aluminum into a metal mold that can be reused for multiple castings. This method is well-suited for producing medium- to high-volume parts with tight tolerances. It’s commonly used for creating parts in industries such as automotive and aerospace.
Investment casting, also known as lost-wax casting, is a method where a wax pattern is coated with a ceramic shell, and the wax is melted out, leaving a mold for aluminum to be poured into. This technique is ideal for producing parts with intricate designs or those requiring high precision.
Casting Method | Best For | Advantages | Ideal For |
---|---|---|---|
Sand Casting | Low volume, Large parts | Flexibility, Low setup cost | Automotive, Industrial |
Die Casting | High-volume, Precision | Speed, Precision | Automotive, Electronics |
Permanent Mold Casting | Medium to High Volume | Reusability, Precision | Aerospace, Automotive |
Investment Casting | Complex, High precision | Detail, Intricate shapes | Aerospace, Medical |
4. What Makes Aluminum Casting a Popular Choice for Manufacturers?
Aluminum casting is popular among manufacturers for a variety of reasons. What’s the real secret? First, it’s a cost-effective option for producing parts in large quantities. The ability to produce complex shapes without the need for additional machining or assembly reduces both time and cost.
Another major advantage of aluminum casting is the material’s lightweight nature, which is especially important in industries such as aerospace and automotive. Aluminum’s low density reduces the overall weight of the parts, improving fuel efficiency and performance. This is crucial for sectors where reducing weight is a priority.
Moreover, aluminum casting offers the flexibility to create both small and large parts, making it suitable for a wide range of applications. From intricate engine components to large industrial machinery parts, aluminum casting is versatile enough to meet different manufacturing needs.
Aluminum is also corrosion-resistant, which makes it ideal for products that will be exposed to harsh environments. Whether in marine applications or exposed to chemicals, aluminum parts hold up well over time, reducing the need for frequent replacements.
But here’s where it gets interesting: Aluminum casting can be customized with various alloys to achieve specific mechanical properties. This customization allows manufacturers to tailor the casting to meet the exact requirements of their industry, providing a competitive edge.
Advantage | Impact on Manufacturing | Why It’s Important | Common Industries |
---|---|---|---|
Lightweight | Reduced part weight | Fuel efficiency, Performance | Aerospace, Automotive |
Corrosion Resistance | Longer part life | Durability in harsh environments | Marine, Industrial |
Flexibility | Ability to make diverse parts | Adapts to complex designs | Automotive, Electronics |
5. How Do You Select the Right Aluminum Casting Method?
Choosing the right aluminum casting method depends on several factors. Ready for the good part? Let’s break it down. The first consideration is the size and complexity of the part. For simple designs, sand casting might be the most economical choice. But if you’re working with intricate components that require high precision, investment casting or die casting might be more appropriate.
Another critical factor is the volume of production. If you need to produce large quantities of parts quickly, die casting is likely the best option. Die casting allows for high-speed production and can produce large volumes with high precision. On the other hand, if you need to create a low volume of parts, sand casting might be the way to go due to its lower setup costs.
The material properties required for the casting are also important. For parts that will undergo high stresses or require specific mechanical properties, permanent mold casting or investment casting may be the better options. These methods allow for more control over the final material properties, ensuring the part meets specific performance standards.
To help make the decision easier, it’s also important to consider the lead time. Some methods, like sand casting, have a shorter lead time, while others, like investment casting, may take longer due to the complexity of the process.
Casting Method | Best For | Production Volume | Lead Time | Cost Factor |
---|---|---|---|---|
Sand Casting | Simple Parts, Low Volume | Low | Short | Low |
Die Casting | High Volume, Precision | High | Short | High |
Permanent Mold Casting | Medium Volume, Precision | Medium | Medium | Medium |
Investment Casting | Complex Parts, High Precision | Low | Long | High |
6. What Are the Key Challenges in Aluminum Casting?
Aluminum casting is not without its challenges. The process itself can present a range of issues, but here’s the kicker: many of these challenges can be minimized with proper planning and expertise. The most common challenges in aluminum casting include defects such as porosity, shrinkage, and cold shuts.
Porosity occurs when gas bubbles become trapped in the molten aluminum during the casting process. This can lead to weak spots in the final product. To prevent porosity, it’s essential to carefully control the temperature of the molten aluminum and ensure the mold is free from contaminants.
Shrinkage is another common issue, especially in larger castings. As the molten aluminum cools, it shrinks, which can cause the casting to deform or crack. To mitigate shrinkage, manufacturers can use mold designs that allow for controlled cooling and compensation for shrinkage.
Cold shuts happen when the molten aluminum doesn’t flow smoothly into the mold, leading to defects at the point where two streams of metal meet. To prevent cold shuts, it’s important to maintain proper temperature control and ensure that the mold is designed to allow for consistent flow.
Finally, one of the most significant challenges in aluminum casting is the quality control process. Ensuring that every part meets the required standards requires close monitoring during the casting process, as well as regular inspections of the final product.
Casting Defect | Cause | Solution | Impact on Part |
---|---|---|---|
Porosity | Trapped gas bubbles | Temperature control, Degassing | Weak spots, Reduced strength |
Shrinkage | Cooling during solidification | Controlled cooling, Mold design | Deformation, Cracking |
Cold Shut | Inconsistent metal flow | Proper gating, Venting system | Incomplete parts, Weakness |
7. How Do You Improve the Quality of Aluminum Castings?
Ensuring high-quality aluminum castings requires careful attention to detail at every stage of the process. Ready for the good part? Let’s explore several strategies for improving the quality of aluminum castings.
One of the most effective ways to enhance casting quality is by refining mold design. A well-designed mold ensures that the molten aluminum flows smoothly into every cavity and cools uniformly. This helps minimize defects like porosity or shrinkage. It’s also crucial to choose the right materials for the mold. Refractory materials like sand or ceramic should be chosen based on the application and the temperature requirements.
Temperature control is another key factor in improving casting quality. Maintaining the correct temperature of the molten aluminum is essential for achieving smooth, consistent castings. If the aluminum is too hot, it can lead to excessive shrinkage, while a temperature that’s too low can cause incomplete filling of the mold. Monitoring the mold temperature is equally important to ensure the aluminum cools evenly, preventing cracks or distortion.
Finally, using proper gating and riser systems can help improve the flow of molten aluminum and reduce the chances of defects. The gating system controls the flow of aluminum into the mold, while risers help compensate for shrinkage by providing extra material during cooling. A well-designed gating and riser system can reduce air pockets, voids, and other common defects.
Improvement Method | Benefit | Key Focus | Outcome |
---|---|---|---|
Refined Mold Design | Smoother aluminum flow | Proper cavity alignment | Reduced defects |
Temperature Control | Consistent aluminum properties | Proper heat management | Fewer cracks, Shrinkage |
Gating & Riser Systems | Optimized material flow | Strategic placement | Less porosity, Better quality |
8. What Are Some Common Applications of Aluminum Castings?
Aluminum castings are used across a wide variety of industries due to their strength, durability, and versatility. You might be wondering: Where exactly are these castings used?
In the automotive industry, aluminum castings are commonly used for engine blocks, cylinder heads, transmission cases, and other components that require strength and lightweight properties. Aluminum’s high strength-to-weight ratio makes it ideal for these applications, as it helps reduce the overall weight of vehicles while maintaining structural integrity.
Aerospace is another industry that relies heavily on aluminum castings. Aircraft parts such as landing gear, engine components, and fuselage structures are often made from aluminum castings due to the material’s combination of lightness, strength, and resistance to corrosion. The ability to produce precise, high-strength components makes aluminum casting a go-to choice for aerospace manufacturers.
Aluminum castings are also used in industrial machinery, where they are employed to create parts such as pumps, valves, and housings. These parts must withstand harsh operating conditions, including high temperatures, vibrations, and corrosive environments. Aluminum is well-suited for these applications because it offers excellent thermal conductivity, resistance to corrosion, and the ability to withstand significant wear.
Finally, aluminum castings find use in the construction and electronics industries, where they are used to create parts like light fixtures, electrical housings, and structural supports. In these applications, aluminum’s versatility and ability to be molded into various shapes are key advantages.
Industry | Casting Application | Benefits | Key Materials Used |
---|---|---|---|
Automotive | Engine blocks, Transmission cases | Lightweight, Durable | Aluminum, Magnesium |
Aerospace | Aircraft parts, Landing gear | High strength, Precision | Aluminum alloys, Titanium |
Industrial Machinery | Pumps, Valves | Corrosion-resistant | Aluminum, Bronze |
Electronics | Housings, Light fixtures | Versatile, Malleable | Aluminum, Zinc |
9. How Can You Cut Costs in Aluminum Casting Projects?
Cutting costs in aluminum casting projects is always a priority for manufacturers. The good news is that there are several ways to reduce expenses without compromising quality. Let’s take a closer look.
One effective way to reduce costs is by selecting the right casting method. For low-volume production runs, sand casting might be the most cost-effective option, as it requires lower setup costs. Die casting, on the other hand, may be more expensive upfront due to tooling costs but offers significant cost savings in high-volume production due to faster cycle times and reduced labor costs.
Another way to cut costs is by optimizing the design of the part being cast. Simplifying complex designs can reduce the amount of material needed, as well as the complexity of the mold. This not only lowers material costs but also reduces the time and labor required for the casting process.
Using recycled aluminum can also help reduce costs, as it’s generally less expensive than virgin aluminum. Many foundries now offer recycled aluminum options, which can be used for casting without compromising the quality of the final product. Recycling aluminum also benefits the environment by reducing the need for primary aluminum production.
Streamlining the production process by reducing waste and improving efficiency can also result in cost savings. Techniques such as lean manufacturing and better process control can help minimize scrap material, reduce energy consumption, and improve overall productivity.
Cost-Cutting Strategy | Impact | How It Saves Money | Industry Applications |
---|---|---|---|
Choose the Right Method | Reduces initial setup costs | Lower material usage, reduced labor | Automotive, Aerospace |
Optimize Design | Reduces complexity | Less material, less machining | Automotive, Industrial |
Use Recycled Aluminum | Reduces raw material costs | Less expensive, more sustainable | All industries |
Streamline Production | Improves efficiency | Less waste, lower energy costs | Manufacturing, Aerospace |
10. How Do You Ensure Safety in Aluminum Casting Operations?
Safety is a top priority in aluminum casting operations, as the process involves high temperatures and the handling of molten metal. What’s the real story? There are several safety measures that must be in place to protect workers and ensure a safe working environment.
First, it’s essential to provide workers with proper training in safety procedures and equipment. Training should cover the proper handling of molten aluminum, the correct use of protective gear, and how to respond to emergencies. This is where the importance of safety comes in – ensuring that employees know how to act in dangerous situations can help prevent accidents.
Protective equipment is also critical. Workers should wear heat-resistant gloves, aprons, and face shields to protect themselves from molten metal splashes and the intense heat of the casting environment. In addition, proper ventilation systems should be in place to prevent the buildup of harmful fumes from the melting aluminum.
The casting area itself should be designed with safety in mind. This includes using heat-resistant materials for floors and walls, providing adequate lighting for visibility, and ensuring that emergency exits are clearly marked and accessible. Regular maintenance of equipment, including furnaces and molds, is also necessary to reduce the risk of accidents caused by equipment failure.
Finally, implementing strict safety protocols and regular inspections can help identify potential hazards before they become problems. Safety audits should be conducted regularly to ensure compliance with safety regulations and industry standards.
Safety Measure | Purpose | Protection Provided | Example |
---|---|---|---|
Worker Training | Ensure proper handling of molten aluminum | Prevent accidents | Safety briefings, drills |
Protective Equipment | Shield from molten metal | Protect from burns and heat exposure | Heat-resistant gear |
Ventilation Systems | Prevent harmful fume buildup | Improve air quality in casting area | Ventilation fans |
Equipment Maintenance | Prevent malfunctions | Avoid accidents from equipment failure | Furnace inspection |
11. What Are the Environmental Considerations in Aluminum Casting?
Environmental sustainability is an increasing concern in all industries, and aluminum casting is no exception. Let’s take a deeper look at some of the environmental considerations involved in the casting process.
One of the main environmental concerns with aluminum casting is the energy required to melt the aluminum. The process requires a significant amount of heat, which typically comes from natural gas or electricity. To mitigate this, many manufacturers are investing in energy-efficient furnaces and adopting energy-saving practices, such as using waste heat for other processes.
Recycling is another important consideration. Aluminum is one of the most recycled metals, and recycling aluminum requires only a fraction of the energy used in primary aluminum production. This makes it an environmentally friendly option. By using recycled aluminum, manufacturers can significantly reduce their environmental footprint while also lowering costs.
Waste management is another key factor. The aluminum casting process generates waste materials, including scrap aluminum, sand from sand casting molds, and other by-products. Effective waste management practices, such as recycling scrap aluminum and using sustainable sand, can help minimize the environmental impact of aluminum casting operations.
Finally, reducing emissions is a priority for many foundries. By investing in cleaner technologies and adhering to environmental regulations, manufacturers can reduce the carbon footprint of their casting operations and contribute to sustainability.
Environmental Factor | Impact | Mitigation Strategy | Industry Benefit |
---|---|---|---|
Energy Use | High energy consumption | Energy-efficient furnaces, Waste heat recovery | Reduced costs, Sustainability |
Recycling | Energy savings | Use recycled aluminum | Lower raw material costs |
Waste Management | Waste generation | Scrap aluminum recycling, Sustainable sand usage | Environmental sustainability |
Emissions | Carbon emissions | Cleaner technologies, Regulation adherence | Reduced carbon footprint |
12. How Do You Overcome Common Aluminum Casting Defects?
Aluminum casting defects can negatively impact the quality and performance of the final product. So, how do you deal with these issues? Let’s take a look at some strategies for overcoming common defects.
Porosity is one of the most common defects in aluminum casting. It occurs when gas bubbles become trapped in the molten aluminum, leading to weak spots in the finished part. To prevent porosity, it’s important to control the temperature of the molten aluminum and ensure that the mold is free from contaminants. Additionally, using degassing agents can help remove dissolved gases before the aluminum is poured into the mold.
Shrinkage is another common problem, especially in large parts. As the molten aluminum cools, it contracts, which can cause cracks or dimensional inaccuracies. To combat shrinkage, manufacturers can use mold designs that allow for controlled cooling and compensation for shrinkage.
Cold shuts occur when the molten aluminum doesn’t flow smoothly into the mold, causing defects at the points where two streams of metal meet. To prevent cold shuts, it’s crucial to maintain proper mold design and temperature control. Ensuring that the mold cavity is properly vented can also help reduce the likelihood of this defect.
Incorporating strict quality control processes, including regular inspections and testing, can also help identify defects early in the process, allowing for quick corrective action.
Defect | Cause | Solution | Effect on Product |
---|---|---|---|
Porosity | Trapped gas bubbles | Temperature control, Degassing | Weakness, Reduced durability |
Shrinkage | Cooling during solidification | Controlled cooling, Shrinkage compensation | Deformation, Cracking |
Cold Shut | Inconsistent flow of metal | Proper gating, Venting system | Incomplete parts, Weakness |
13. How Does the Future Look for Aluminum Casting Technology?
The future of aluminum casting looks bright, with continuous innovations and improvements in technology. So, what’s on the horizon?
One of the most exciting developments is the increased use of automation and robotics in the casting process. Automation can help streamline production, reduce labor costs, and improve precision. Robotics can also assist with tasks such as mold handling and pouring molten metal, reducing human exposure to dangerous conditions.
Another trend is the development of advanced alloys. Researchers are working on creating aluminum alloys that offer improved performance characteristics, such as higher strength, better corrosion resistance, and improved castability. These alloys are expected to open up new applications in industries like aerospace and automotive.
Additive manufacturing, or 3D printing, is also making its way into the aluminum casting industry. While still in the early stages, 3D printing allows for the creation of complex, customized molds and components, further enhancing the capabilities of aluminum casting.
As the demand for sustainable manufacturing grows, the use of recycled aluminum will also continue to rise. Advances in recycling technology will enable foundries to use more recycled aluminum without compromising the quality of the final product.
Technology | Impact | Benefit | Industry Application |
---|---|---|---|
Robotics & Automation | Streamlined production, Reduced labor | Faster, Precise, Safer production | Aerospace, Automotive |
Advanced Alloys | Enhanced material properties | Improved strength, Corrosion resistance | Aerospace, Automotive |
Additive Manufacturing | Customization, Complex shapes | Faster prototyping, Flexibility | Aerospace, Manufacturing |
14. How Can You Find a Reliable Aluminum Casting Supplier?
Finding the right supplier is critical for ensuring the quality and cost-effectiveness of your aluminum casting projects. Let’s break it down.
The first thing to look for in a supplier is experience. A supplier with a proven track record in aluminum casting will have the expertise needed to handle your project and ensure high-quality results. Ask potential suppliers about their experience with similar projects and their knowledge of different casting methods.
Next, inquire about the supplier’s quality control processes. A reliable supplier should have strict quality control procedures in place to identify defects and ensure that every part meets your specifications. You can also ask for samples of their previous work to assess the quality of their castings.
Another important factor is lead time. A supplier who can deliver parts on time is essential for maintaining your production schedule. Make sure to discuss lead times upfront and ask the supplier to commit to realistic deadlines.
Cost is, of course, a critical factor. While it’s important to choose a supplier who offers competitive pricing, don’t compromise on quality to save a few dollars. The long-term cost savings from high-quality aluminum castings will far outweigh the short-term savings from cheap, low-quality parts.
Finally, consider the supplier’s customer service and communication. A good supplier should be easy to work with, responsive, and willing to collaborate to meet your needs.
Supplier Criteria | Consideration | Key Questions | Outcome |
---|---|---|---|
Experience | Proven track record | Previous projects, Expertise | Reliable, Skilled supplier |
Quality Control | Consistent standards | Inspection processes, Samples | Defect-free, High standards |
Lead Time | On-time delivery | Delivery timelines, Capacity | Timely product delivery |
Cost | Competitive pricing | Cost breakdown, Hidden fees | Cost-effective, Transparent |
Communication | Easy collaboration | Responsiveness, Flexibility | Smooth process, Timely updates |
15. What Are the Costs Involved in Aluminum Casting Projects?
The cost of an aluminum casting project can vary depending on several factors. Ready for the good part? Let’s break it down.
The biggest cost factors in aluminum casting are the material, the casting method, and the complexity of the design. Material costs can vary depending on whether you’re using recycled or virgin aluminum. For high-volume production, the cost per part decreases due to economies of scale, but for low-volume or custom parts, costs may be higher.
The casting method also plays a significant role in the overall cost. Die casting tends to have a higher upfront cost due to tooling and setup, but it offers cost savings in high-volume production. On the other hand, sand casting has lower setup costs but may be less cost-effective for large production runs.
The complexity of the design is another key factor. Complex designs may require more intricate molds and additional processing, which can increase costs. Simplifying designs or reducing the need for post-casting machining can help lower costs.
Finally, labor costs, overhead, and transportation should also be considered when budgeting for an aluminum casting project. By carefully selecting the right casting method, material, and supplier, you can manage costs effectively and keep your project within budget.
Cost Factor | Impact | Influence on Total Cost | Cost-Saving Strategies |
---|---|---|---|
Material | Type of aluminum used | Affects cost per unit | Recycled aluminum |
Casting Method | Setup and tooling requirements | Impacts initial investment | Choose cost-effective methods |
Design Complexity | Detailed molds and processing | Increases time, labor, and material costs | Simplify designs |
Labor and Overhead | Labor intensity, Overhead cost | Impacts final cost | Automation, Lean processes |
FAQ Section
Q1: What is aluminum casting?
Aluminum casting is the process of pouring molten aluminum into a mold to create solid parts. This method is used to produce a wide range of components for industries like automotive and aerospace.
Q2: How does aluminum casting work?
In aluminum casting, molten aluminum is poured into a mold, where it cools and solidifies. The mold can be made from various materials, and the process used depends on the part’s complexity, production volume, and material requirements.
Q3: What are the benefits of aluminum casting?
Aluminum casting offers high precision, cost-effectiveness, and versatility. It allows manufacturers to create complex parts with excellent surface finishes while maintaining a high strength-to-weight ratio.
Q4: What are common defects in aluminum casting?
Common defects include porosity, shrinkage, and cold shuts. These can be avoided with proper temperature control, mold design, and quality monitoring.
Q5: How do you choose the right aluminum casting method?\
The right method depends on factors such as part complexity, production volume, and material properties. Die casting is best for high-volume production, while sand casting is suitable for low-volume or large parts.