Aluminum casting processes have become a vital component in various industries. Understanding these processes and their benefits is crucial for manufacturers, engineers, and procurement managers looking to make informed decisions about their production methods. In this article, we’ll break down the key aluminum casting processes, explore their respective benefits, and provide you with insights on how to select the best process for your needs. Ready to dive in? Let’s get started.
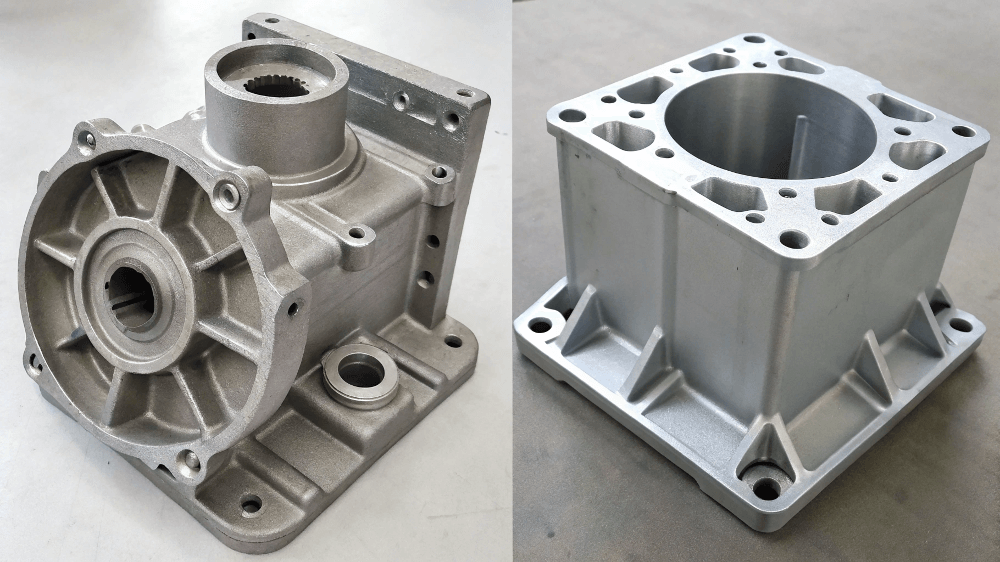
1. What Are Aluminum Casting Processes?
Aluminum casting processes are techniques used to create aluminum parts by pouring molten aluminum into molds. These molds are designed to shape the metal into specific forms, depending on the application. But here’s the kicker – aluminum casting is one of the most versatile and cost-effective ways to manufacture durable and complex parts. Whether you’re producing automotive components, aerospace parts, or household goods, aluminum casting processes play a critical role in manufacturing.
There are several casting methods, each with its own set of advantages. The most common methods include sand casting, die casting, and permanent mold casting. Let’s look at these processes in more detail.
Sand casting is perhaps the oldest and most traditional method. It involves creating a mold from sand mixed with a binder, into which molten aluminum is poured. The sand mold is then broken away to reveal the cast part. This process is ideal for larger parts or lower volume production runs.
Die casting, on the other hand, uses high-pressure injection to force molten aluminum into a metal mold. The process produces high-precision, smooth, and durable parts in high volumes. Die casting is especially popular in the automotive and electronics industries.
Permanent mold casting involves pouring molten aluminum into a reusable metal mold. This method is well-suited for medium to high-volume production runs and delivers excellent dimensional accuracy and surface finish.
These casting processes each have unique advantages, but they share a common goal: to provide high-quality, durable aluminum components. What’s the real story? Let’s explore the benefits of aluminum casting processes in more detail.
Process | Ideal Use Case | Key Benefits |
---|---|---|
Sand Casting | Large, low-volume parts | Low cost, flexible for custom parts |
Die Casting | High-volume, precision parts | High accuracy, fast production |
Permanent Mold Casting | Medium to high-volume parts | Excellent surface finish, durability |
2. What Are the Key Benefits of Aluminum Casting?
Aluminum casting provides numerous benefits that make it an attractive choice for manufacturers across various industries. Let’s break down these advantages, one by one.
First, aluminum is lightweight, which is crucial in industries like aerospace and automotive. Lighter parts can reduce overall vehicle weight, leading to improved fuel efficiency and performance. But here’s the kicker: aluminum also maintains its strength, even when it’s thin or lightweight.
Another key benefit is aluminum’s ability to resist corrosion. When aluminum is cast, it naturally forms a protective oxide layer that prevents rust and corrosion, making it ideal for outdoor and marine environments. This property makes aluminum casting an excellent choice for automotive, marine, and construction industries.
Aluminum also has excellent thermal and electrical conductivity. This makes it ideal for applications that require efficient heat dissipation, such as in electrical enclosures and heat exchangers. With high conductivity, aluminum parts can efficiently transfer heat away from sensitive components, ensuring that devices operate safely and efficiently.
The cost-effectiveness of aluminum casting is another major advantage. Aluminum is abundant and relatively inexpensive compared to other metals, and the casting processes themselves are cost-effective, especially for large production runs. What’s the real story? Aluminum casting processes provide manufacturers with a material that’s affordable, durable, and versatile, offering tremendous benefits across a wide range of applications.
Benefit | Description |
---|---|
Lightweight | Reduces overall weight, improves efficiency |
Corrosion Resistance | Protects parts from rust and degradation |
Thermal/Electrical Conductivity | Ideal for heat dissipation and electrical components |
Cost-Effectiveness | Lower production costs, affordable material |
3. How Does Sand Casting Work in Aluminum Casting?
Sand casting is one of the oldest and most common methods of aluminum casting. This process involves creating a mold from a mixture of sand and a binder material, which is then compacted around a pattern of the desired shape. The pattern is removed, leaving a cavity that is filled with molten aluminum to form the cast part.
What’s the real story? Sand casting is versatile and can be used to produce parts of various sizes and complexities. One of the key benefits of sand casting is its cost-effectiveness, especially for small production runs or custom parts. Since the mold is made from sand, it doesn’t require expensive tooling or machinery, making it ideal for low-budget or one-off projects.
However, sand casting also has its challenges. The surface finish of the cast parts is often rougher compared to other casting methods, and the process can produce parts with lower dimensional accuracy. Despite these limitations, sand casting remains a popular choice due to its flexibility, low cost, and ability to handle larger or irregularly shaped parts.
Another benefit of sand casting is that it can be used for both ferrous and non-ferrous metals. In the case of aluminum, the sand molds can be reused for multiple casting runs, which helps reduce costs even further. Ready for the good part? Let’s examine some common applications of sand-cast aluminum parts.
Advantage | Disadvantage | Common Applications |
---|---|---|
Cost-effective | Rougher surface finish | Automotive components, large parts |
Versatile | Lower dimensional accuracy | Industrial machinery, custom parts |
Low tooling cost | Slower production rates | Pipe fittings, engine blocks |
4. What Is Die Casting in Aluminum Manufacturing?
Die casting is a highly effective method for producing aluminum parts with exceptional dimensional accuracy. This process involves injecting molten aluminum into a metal mold (or die) under high pressure. The pressure forces the aluminum to fill the mold completely, creating precise, high-quality parts.
Ready for the good part? The primary advantage of die casting is the ability to produce high-volume parts with excellent surface finish and tight tolerances. Parts produced through die casting require minimal finishing, which reduces labor costs and production time.
The die casting process is ideal for producing complex, intricate parts that require high precision. Additionally, the process can create parts with thinner walls than other casting methods, making it a great option for industries like automotive and electronics where lightweight and high-strength components are crucial.
What sets die casting apart from other processes is the durability and longevity of the molds used in production. The metal molds used in die casting are durable and can withstand repeated use, making it cost-effective for large production runs. With this in mind, it’s clear why die casting is the go-to method for high-volume aluminum parts.
Advantage | Disadvantage | Common Applications |
---|---|---|
High precision | Higher initial tooling cost | Automotive parts, housings, enclosures |
High-volume production | Limited to smaller parts | Electronics, industrial components |
Excellent surface finish | Can’t be used for very large parts | Consumer products, medical devices |
5. What Are the Steps Involved in Permanent Mold Casting?
Permanent mold casting is another popular method of aluminum casting, especially for medium to high-volume production. In this process, molten aluminum is poured into a reusable metal mold, typically made of steel or iron. The mold is then cooled, and the solidified part is removed.
This method has several advantages over sand casting. For one, it offers better dimensional accuracy and a smoother surface finish. The molds used in permanent mold casting can be reused multiple times, which reduces the cost per part, making it ideal for medium to high-volume production runs.
What’s the real story? Permanent mold casting is ideal for applications where high precision is necessary but with a faster turnaround than investment casting. The process can produce complex parts, but it’s most effective for components that don’t require the intricate details that investment casting offers.
One of the challenges of permanent mold casting is that it can be more expensive than sand casting due to the cost of the metal molds. However, when considering the long-term benefits, such as improved production speed and reduced finishing costs, the investment is often worth it for high-volume applications.
Advantage | Disadvantage | Common Applications |
---|---|---|
Better dimensional accuracy | Higher mold cost | Engine components, pump housings |
Faster production times | Not ideal for very complex shapes | Structural parts, frames |
Reusable molds | Limited to lower volumes than die casting | Automotive parts, electrical components |
6. How Does Investment Casting Apply to Aluminum Casting?
Investment casting, also known as lost wax casting, is a process that involves creating a wax pattern of the part to be cast. The wax is coated with a ceramic shell, which is then heated to remove the wax and harden the shell. Molten aluminum is then poured into the mold to create the part.
But here’s the kicker: investment casting is ideal for producing highly detailed, intricate parts that require exceptional precision. It’s particularly useful in industries like aerospace and medical devices, where parts need to meet strict tolerance requirements. The key advantage of investment casting is that it can produce parts with incredibly fine features, which are not achievable with other casting methods.
Investment casting also offers a great surface finish, and because the mold is made of ceramic, it can handle high temperatures, making it suitable for casting aluminum alloys that would be difficult to cast with other methods. This method, however, is slower and more expensive compared to sand and die casting, so it’s best suited for low-volume, high-precision applications.
Advantage | Disadvantage | Common Applications |
---|---|---|
Exceptional detail | Expensive tooling and process | Aerospace parts, medical devices |
High precision | Slow production | Jewelry, turbine blades |
Excellent surface finish | Limited to lower volume production | Precision instruments, valves |
7. What Are the Key Aluminum Alloy Types Used in Casting?
Aluminum alloys are often used in casting due to their combination of strength, lightweight, and corrosion resistance. The most commonly used aluminum alloys in casting include the 1000, 2000, 3000, 4000, and 5000 series. Each series has distinct properties that make them suitable for different applications.
For example, 1000 series alloys are made of pure aluminum and are highly resistant to corrosion, making them ideal for applications in the marine and aerospace industries. The 2000 series alloys, on the other hand, contain copper, which enhances strength but reduces corrosion resistance, making them suitable for applications that require high strength but are not exposed to harsh environmental conditions.
What’s the real story? When choosing an aluminum alloy for casting, it’s crucial to consider the specific application requirements, such as strength, weight, corrosion resistance, and temperature resistance. The right alloy will provide the necessary properties to ensure the longevity and performance of the final product.
Alloy Series | Key Elements | Strength & Applications |
---|---|---|
1000 | Pure Aluminum | High corrosion resistance, aerospace |
2000 | Copper | High strength, low corrosion resistance |
3000 | Manganese | Excellent corrosion resistance, HVAC |
4000 | Silicon | Good wear resistance, automotive |
5000 | Magnesium | Strong, resistant to seawater corrosion |
8. What Are the Environmental Benefits of Aluminum Casting?
Aluminum casting offers significant environmental benefits, particularly when it comes to energy efficiency and recycling. One of the most compelling aspects of aluminum is its ability to be recycled without losing quality. In fact, recycled aluminum requires only 5% of the energy used to produce new aluminum, making it an environmentally sustainable choice for manufacturers.
Moreover, many aluminum casting processes have become more energy-efficient over time. Technologies such as low-energy furnaces and automated processes help reduce the overall environmental impact of casting. By using more efficient methods, manufacturers can reduce emissions and lower their carbon footprint, making aluminum casting an environmentally friendly option.
What’s the real story? The sustainability of aluminum casting is a key selling point for manufacturers looking to reduce their environmental impact while still producing high-quality parts. The ability to recycle aluminum indefinitely is a major advantage for industries looking to adopt greener practices.
Environmental Benefit | Explanation |
---|---|
Energy Efficiency | Recycled aluminum uses only 5% of energy |
Low Carbon Footprint | Reduced emissions with modern casting techniques |
Recyclability | Aluminum can be recycled indefinitely |
9. How Do Aluminum Casting Processes Compare to Other Casting Methods?
When it comes to casting processes, aluminum stands out due to its versatility and range of applications. However, it’s essential to understand how it compares to other common casting methods, such as steel and iron casting.
First, aluminum casting is significantly lighter than steel or iron, making it ideal for applications where weight is a critical factor, such as in the aerospace or automotive industries. What’s the real story? Aluminum’s lightweight nature contributes to fuel efficiency, better performance, and more cost-effective transportation solutions.
On the other hand, steel casting is favored in applications that require extreme strength and durability, like heavy machinery and structural components. While aluminum casting can produce strong parts, it can’t quite match the sheer strength of steel. However, aluminum casting is often more affordable and can produce parts faster due to shorter cooling times and lower material costs.
Iron casting is another common method, often used for parts that need to handle high temperatures or heavy loads. Iron is heavier and more rigid than aluminum, but aluminum has a superior resistance to corrosion, making it ideal for parts exposed to the elements.
In summary, aluminum casting offers a favorable balance of strength, lightweight properties, and corrosion resistance compared to steel and iron casting. When making a casting decision, it’s essential to weigh the benefits of aluminum casting against the material properties of other metals to ensure the right choice for your application.
Casting Method | Advantages | Common Applications |
---|---|---|
Aluminum | Lightweight, corrosion-resistant | Aerospace, automotive, electronics |
Steel | Strong, durable | Heavy machinery, structural parts |
Iron | High-temperature resistance | Engine blocks, industrial equipment |
10. What Challenges Can Arise During Aluminum Casting?
While aluminum casting processes are highly effective, there are several challenges that manufacturers must overcome to ensure the success of their production. One of the most common issues is porosity. Porosity occurs when gas bubbles become trapped in the aluminum during the cooling process, creating tiny holes in the cast part. This can weaken the part and affect its structural integrity.
What’s the real story? Preventing porosity involves controlling the temperature and speed at which molten aluminum is poured into the mold, ensuring that air pockets are minimized. In addition, using proper degassing techniques and ensuring the aluminum is of the highest quality can help eliminate this issue.
Another challenge in aluminum casting is shrinkage. As aluminum cools and solidifies, it tends to shrink. This can lead to dimensional inaccuracies, making it difficult to meet the precise requirements for certain applications. Manufacturers often address this issue by compensating for shrinkage in the mold design and employing advanced casting methods to control the cooling process.
Finally, the need for post-casting treatments like heat treatment, machining, and surface finishing can add additional time and cost to the production process. While aluminum casting can produce parts with good surface finishes, many applications require further treatments to achieve the desired quality.
Despite these challenges, careful process control and the use of advanced technology can help mitigate these issues and ensure the production of high-quality aluminum castings.
Challenge | Solution |
---|---|
Porosity | Proper temperature control, degassing techniques |
Shrinkage | Mold compensation, advanced cooling techniques |
Post-Casting Treatments | Heat treatment, surface finishing, machining |
11. How Do Advances in Technology Affect Aluminum Casting?
Advancements in technology have significantly impacted aluminum casting processes, leading to more efficient, accurate, and cost-effective production methods. One of the most significant innovations in recent years is the rise of automation in the casting process. Automated systems can control the flow of molten aluminum, monitor temperature, and adjust parameters in real-time, reducing human error and ensuring higher consistency.
Ready for the good part? 3D printing technology is also beginning to play a significant role in aluminum casting. 3D printing allows for rapid prototyping and the creation of complex molds and patterns that would be difficult or expensive to produce using traditional methods. This reduces the time and cost associated with mold making and allows manufacturers to create parts with more intricate designs.
Additionally, new materials and alloys are continually being developed for use in aluminum casting. These materials often offer improved properties, such as enhanced strength or better heat resistance, enabling manufacturers to meet increasingly demanding specifications. What’s the real story? These advances have made aluminum casting even more competitive, enabling manufacturers to produce parts that were previously impossible or impractical to make.
The integration of automation, 3D printing, and new materials is transforming aluminum casting, making it faster, more precise, and more adaptable to the needs of modern manufacturing.
Advancement | Impact on Casting Process |
---|---|
Automation | Reduces human error, improves consistency |
3D Printing | Rapid prototyping, complex mold creation |
New Materials/Alloys | Improved properties like strength, heat resistance |
12. What Are the Applications of Aluminum Casting in Different Industries?
Aluminum casting is widely used in a variety of industries due to its lightweight, corrosion-resistant, and durable nature. The automotive industry is one of the largest consumers of aluminum castings. Aluminum cast parts are used in engines, transmissions, wheels, and body panels. The lightweight properties of aluminum are essential for reducing vehicle weight, which improves fuel efficiency and overall performance.
In the aerospace industry, aluminum casting is used to produce components for aircraft engines, landing gear, and structural parts. The high strength-to-weight ratio of aluminum is particularly valuable in aerospace applications, where weight reduction is critical for fuel efficiency.
The construction industry also benefits from aluminum casting. Components such as window frames, doors, and structural supports are commonly made from cast aluminum due to its corrosion resistance and ability to withstand outdoor environments.
Other industries that rely on aluminum casting include electronics, where aluminum enclosures are used to protect sensitive components, and the energy sector, where aluminum is used in turbine blades and electrical housings. In short, aluminum casting is a key player in numerous industries, offering a wide range of benefits that enhance performance, durability, and cost-effectiveness.
Industry | Common Applications |
---|---|
Automotive | Engine blocks, wheels, body panels |
Aerospace | Aircraft engines, structural parts |
Construction | Window frames, doors, structural supports |
Electronics | Enclosures, heat sinks |
Energy | Turbine blades, electrical housings |
13. What Is the Future of Aluminum Casting?
The future of aluminum casting is exciting, with ongoing innovations driving growth and improving manufacturing processes. As industries continue to demand lighter, stronger, and more efficient materials, aluminum casting will play a crucial role in meeting these needs.
What’s the real story? The demand for aluminum in industries like automotive and aerospace is expected to rise as manufacturers push for more energy-efficient products. Advances in casting technologies, such as the use of 3D printing and automation, will further enhance aluminum casting’s ability to produce high-quality, complex parts at lower costs.
The future will also see greater emphasis on sustainability. Recycling aluminum will continue to be a key factor in reducing the environmental impact of aluminum casting, and manufacturers will explore new ways to make the casting process more energy-efficient.
In summary, the future of aluminum casting is bright. With new technologies, greater efficiency, and a continued focus on sustainability, aluminum casting will remain a critical component in modern manufacturing.
Future Trend | Impact on Aluminum Casting |
---|---|
Increased Demand | Growth in automotive, aerospace, and electronics sectors |
Technological Advances | 3D printing, automation, improved casting quality |
Sustainability Focus | More energy-efficient processes, increased recycling |
14. How Can You Choose the Right Aluminum Casting Process for Your Needs?
Selecting the right aluminum casting process is a critical decision that can impact the overall cost, quality, and efficiency of your production. The choice depends on several factors, including the complexity of the part, production volume, and material requirements.
What’s the real story? If you’re looking for high precision and excellent surface finish for complex, low-volume parts, investment casting may be your best option. On the other hand, if you need a fast, cost-effective process for larger parts, sand casting could be more suitable. Die casting is ideal for high-volume, precision parts, while permanent mold casting strikes a balance between cost and precision.
In addition, you should consider the material properties of the aluminum alloy you’re using, as different alloys are better suited to specific casting methods. It’s also essential to factor in lead times, cost per unit, and the required post-casting treatments to make the best decision for your manufacturing needs.
Factor | Sand Casting | Die Casting | Investment Casting | Permanent Mold Casting |
---|---|---|---|---|
Production Volume | Low to Medium | High | Low | Medium to High |
Precision | Low | High | Very High | Medium |
Cost per Part | Low | High | High | Medium |
Surface Finish | Rough | Excellent | Excellent | Good |
15. What Are the Best Practices for Quality Control in Aluminum Casting?
Quality control is crucial to ensuring that aluminum castings meet the required specifications and performance standards. The first step in quality control is selecting high-quality aluminum alloys. It’s important to ensure that the material is free from impurities that could affect the casting process.
What’s the real story? Proper mold preparation is essential to preventing defects such as cracks or porosity in the final part. Manufacturers should also ensure that the molten aluminum is of the right temperature and consistency before pouring it into the mold. Temperature control systems and degassing techniques can help ensure a smooth casting process.
After the parts are cast, post-casting inspections are necessary to check for defects. These inspections may include visual inspections, dimensional checks, and testing for mechanical properties like strength and hardness. Ready for the good part? Using automated systems for monitoring and inspections can improve consistency and reduce human error in the quality control process.
Quality Control Measure | Purpose |
---|---|
Material Inspection | Ensure no impurities are present in the aluminum |
Mold Preparation | Prevent cracks, porosity, and other defects |
Temperature Control | Ensure consistency in the molten aluminum |
Post-Casting Inspections | Verify dimensional accuracy, strength, and surface finish |
FAQ Section
Q1: What is aluminum casting?
Aluminum casting is a manufacturing process in which molten aluminum is poured into a mold to create various parts used in industries such as automotive, aerospace, and construction. The casting process can be achieved using different techniques like sand casting, die casting, and permanent mold casting.
Q2: How does sand casting work in aluminum casting?
Sand casting involves creating a mold from sand and a binder material. The mold is then filled with molten aluminum, which solidifies into the desired shape. After cooling, the mold is broken away, revealing the cast part.
Q3: What are the environmental benefits of aluminum casting?
Aluminum casting has environmental benefits, particularly in recycling. Aluminum can be recycled indefinitely, requiring only 5% of the energy compared to creating new aluminum. This reduces energy consumption and lowers carbon emissions.
Q4: What challenges can arise during aluminum casting?
Common challenges in aluminum casting include porosity, shrinkage, and the need for post-casting treatments. These issues can be addressed through proper temperature control, mold design, and inspection techniques.
Q5: How can you choose the right aluminum casting process?
The right casting process depends on factors such as part complexity, production volume, and cost. For low-volume, high-precision parts, investment casting is ideal. For larger parts, sand casting is more cost-effective, while die casting is best for high-volume production.