When it comes to casting tolerances, manufacturers must adhere to various standards to ensure product precision. However, which standards should you follow: NADCA or ISO?
Casting tolerances play a crucial role in ensuring the quality of cast parts, especially in highly precise industries. In this article, we explore the differences between NADCA and ISO standards to help you navigate your choices effectively.
Ensuring your products meet exact tolerances can be the difference between success and failure in manufacturing. Read on to uncover the critical factors you need to understand when choosing between NADCA and ISO standards.
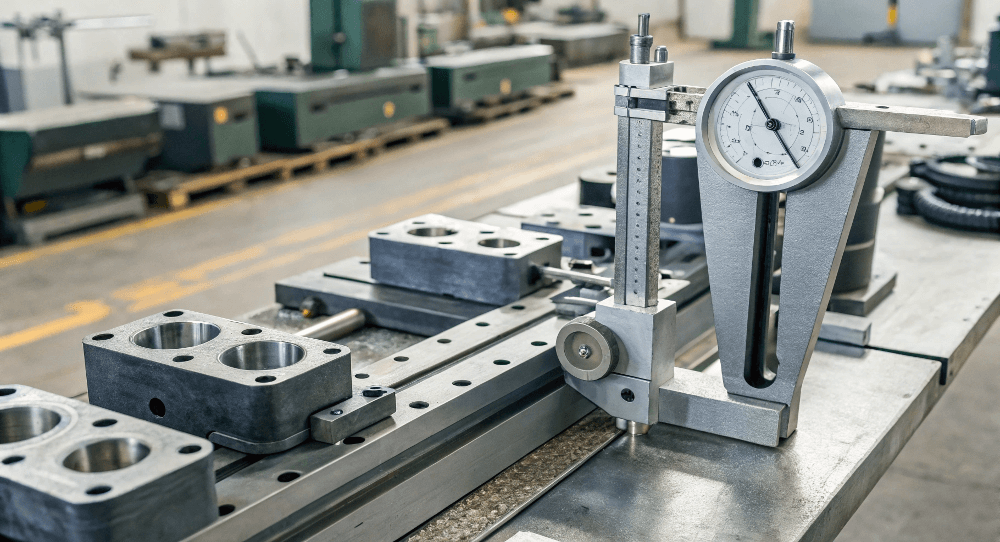
1. What are casting tolerances in manufacturing?
Casting tolerances define the acceptable variations in dimensions of a cast part. Without these measurements, parts may not fit together as intended, leading to faulty assembly and costly rework.
Casting tolerances ensure that cast parts meet specific dimensions, allowing them to fit and function precisely within the broader system. This practice is crucial in industries like aerospace and automotive, where even minor errors can lead to significant performance issues.
Casting tolerances in manufacturing help maintain uniformity across all parts produced, thus guaranteeing their effectiveness and durability. These measurements ensure consistency in production, thereby reducing errors in finished products. Failure to maintain precise tolerances could lead to catastrophic operational failures in high-stakes industries.
2. Why are NADCA and ISO casting tolerances important?
Casting tolerances defined by NADCA and ISO are essential because they guide manufacturers on how to achieve accurate dimensions for specific casting methods, ultimately affecting product performance, quality, and durability.
NADCA, the North American Die Casting Association, focuses primarily on die casting processes. Its standards ensure that die-cast parts meet the required quality levels and fit within the required tolerance ranges. ISO, on the other hand, offers more globally applicable standards, particularly for sand casting and other casting processes that aren’t limited to die casting.
Understanding the key differences between NADCA and ISO casting tolerances helps manufacturers choose the right standard for their casting needs.
Comparison of NADCA and ISO Standards
Standard | Application Scope | Material Focus | Tolerance Variations |
---|---|---|---|
NADCA | Die casting | Primarily metals like aluminum, zinc, and magnesium | Precision for die casting |
ISO | Sand, investment, and die casting | Broader application across metals and alloys | Flexibility for various materials |
3. How do NADCA standards define casting tolerances?
NADCA’s casting tolerances are specifically designed for die-casting processes. The tolerances vary based on factors like the type of material used, the size of the casting, and the complexity of the part.
The key benefit of NADCA standards is their focus on ensuring uniformity in die-casting processes. This leads to high-quality, repeatable results that minimize waste and improve production efficiency.
NADCA provides specific tolerances for various materials, which helps manufacturers optimize their casting processes to meet precise dimensional needs.
Key NADCA Tolerance Standards
Material | Standard Tolerance (mm) | Casting Type |
---|---|---|
Aluminum | ±0.30 | Die casting |
Zinc | ±0.25 | Die casting |
Magnesium | ±0.30 | Die casting |
4. How do ISO standards define casting tolerances?
ISO standards are internationally recognized and apply to a wider range of casting processes, including sand casting, investment casting, and die casting. These standards offer greater flexibility and are ideal for manufacturers who work with diverse materials.
ISO standards address a broader spectrum of dimensions and tolerance limits, making them useful for global operations. These standards also provide a framework for achieving consistency in casting processes across different regions and industries.
ISO tolerances ensure that cast parts meet required specifications regardless of the casting method used.
Examples of ISO Casting Tolerances
Casting Method | Standard Tolerance (mm) | Common Materials |
---|---|---|
Sand casting | ±1.00 | Steel, iron |
Investment casting | ±0.50 | Stainless steel, bronze |
Die casting | ±0.25 | Aluminum, zinc |
5. What are the main differences between NADCA and ISO casting tolerances?
While both NADCA and ISO standards aim to improve casting precision, they differ in several key aspects. NADCA is more focused on the die-casting process, while ISO encompasses a wider range of casting methods.
NADCA’s guidelines tend to be more specific to North American die-casting practices, whereas ISO’s global applicability makes it a preferred choice for manufacturers working internationally.
NADCA vs. ISO: A Comparison of Key Differences
Feature | NADCA | ISO |
---|---|---|
Geographic Scope | North America | Global |
Casting Method | Die casting only | Various (Die, Sand, Investment) |
Material Focus | Aluminum, Zinc, Magnesium | Various metals and alloys |
6. How do casting tolerances affect the final product?
Casting tolerances directly influence the quality and performance of the final product. Improper tolerances can lead to parts that don’t fit correctly, causing assembly issues, functional failure, or even operational hazards. Tight tolerances are necessary when parts need to fit within specific systems, such as in aerospace, automotive, and other precision-driven industries.
Maintaining accurate casting tolerances is vital for ensuring that the product operates as intended without issues during assembly.
Impact of Casting Tolerances on Product Quality
Tolerance Level | Impact on Product Quality | Example of Effect |
---|---|---|
±0.10mm | High precision | Aerospace parts requiring exact fit |
±0.50mm | Moderate precision | Automotive parts for standard applications |
±1.00mm | Low precision | Non-critical parts used in less demanding applications |
7. What factors affect casting tolerances?
Several factors influence the accuracy of casting tolerances, including material choice, the design of the mold, and the specific casting method. Variations in temperature, humidity, and even the skill of the workforce can also play a significant role in the final product’s dimensional accuracy.
Understanding these factors can help manufacturers optimize their processes to achieve the desired level of precision, ultimately reducing errors and ensuring consistency.
Key Factors Affecting Casting Tolerances
Factor | Influence on Tolerance Accuracy | Example Impact |
---|---|---|
Material Type | Different materials expand/contract differently, affecting tolerance | Metals like aluminum expand more than steel |
Mold Design | Poorly designed molds lead to irregularities in the cast part | Misalignment of mold can lead to uneven casting |
Temperature | Variations in temperature can cause distortion | Metal cooling too quickly may cause warping |
Workforce Skill | Inexperienced workers may not maintain precision | Inaccurate measurements or improper handling of materials |
8. How can manufacturers ensure they meet casting tolerances?
To meet casting tolerances, manufacturers must implement precise measurement techniques and maintain strict quality control throughout the production process. Using advanced technologies like CNC machines for finishing or automated measurement tools helps ensure dimensional accuracy. Consistent monitoring of casting equipment and tools also reduces the risk of deviations from the desired tolerances.
Investing in technology and establishing quality assurance protocols are key steps in ensuring that casting tolerances are consistently met.
Methods for Ensuring Tolerance Accuracy
Method | Description | Benefit |
---|---|---|
CNC Machining | Computerized control of machinery for precision finishing | High precision and repeatability |
Automated Measuring Tools | Use of automated systems to measure parts during production | Continuous monitoring and reduced error rates |
Regular Tool Calibration | Ensuring that casting equipment is calibrated for precision | Consistent performance of casting machinery |
9. How do different materials influence casting tolerances?
Different materials expand and contract at varying rates during the casting process, which can affect the precision of the final part. Metals like aluminum and magnesium have different thermal properties compared to steel, which influences the accuracy of the casting process. Understanding the specific tolerance requirements for each material type is crucial to achieving the best results.
Material choice is a key determinant in how tight or loose the casting tolerances can be, making it essential to choose the correct material for the intended application.
Material Influence on Casting Tolerances
Material | Tolerance Range (mm) | Casting Method | Common Applications |
---|---|---|---|
Aluminum | ±0.25 | Die casting | Automotive, consumer products |
Steel | ±0.50 | Sand casting, die casting | Industrial components, machinery |
Magnesium | ±0.30 | Die casting | Aerospace, automotive |
10. How are casting tolerances measured?
Accurate measurement of casting tolerances requires specialized tools and techniques. Commonly used instruments include micrometers, calipers, and laser scanning systems, which allow for precise measurement of the part’s dimensions. These instruments help verify that parts meet the specifications outlined in the NADCA or ISO standards.
Choosing the right measuring tool for your casting method is essential for maintaining consistent tolerance accuracy.
Common Tools for Measuring Casting Tolerances
Tool | Purpose | Accuracy Range |
---|---|---|
Micrometers | Measure the thickness or diameter of parts | ±0.01mm |
Calipers | Measure external and internal dimensions of parts | ±0.05mm |
Laser Scanners | Non-contact 3D scanning to measure complex parts | ±0.02mm |
Coordinate Measuring Machines (CMM) | Measures precise 3D geometry of parts | ±0.01mm |
11. How do casting tolerances affect cost and production time?
Casting tolerances directly impact both production time and cost. The tighter the tolerance, the more time and resources are required for the production process. Higher precision typically involves more advanced equipment, higher-quality materials, and greater attention to detail during the manufacturing process, all of which increase costs. However, achieving the required tolerances can also result in higher-quality products, reducing the need for rework and minimizing waste.
While tighter tolerances may increase costs initially, they often lead to more reliable and durable products, which can result in long-term cost savings.
Impact of Tolerances on Cost and Production Time
Tolerance Level | Cost Impact | Production Time Impact |
---|---|---|
±0.25mm | High | Longer production cycles |
±0.50mm | Moderate | Standard production time |
±1.00mm | Low | Faster production cycles |
12. How do casting tolerances impact the design process?
Casting tolerances significantly influence the design of a part. Designers must account for these tolerances to ensure that the part will fit into the larger assembly. Tight tolerances may require modifications to the design to ensure the part can be cast accurately, which may involve adjusting the part’s geometry or material choice. The casting method also affects how the design is executed, as some methods can better handle tighter tolerances than others.
Incorporating the right tolerances into the design process can help avoid costly revisions and ensure the final product meets specifications.
Designing for Tolerances
Design Factor | Influence on Tolerance Requirements | Example Impact |
---|---|---|
Material Selection | Determines how tightly tolerances can be controlled | Steel allows for tighter tolerances than cast iron |
Part Geometry | Complex shapes may require looser tolerances | Intricate designs often need more room for dimensional variation |
Casting Method | Some methods are better suited for tight tolerances | Die casting can achieve higher precision compared to sand casting |
13. What are the challenges in meeting casting tolerances?
Achieving casting tolerances comes with several challenges. Variations in the material, mold defects, environmental factors, and human error can all contribute to deviations from the required dimensions. Additionally, achieving tight tolerances often requires specialized equipment and skills, which may not always be available or affordable for all manufacturers.
Addressing these challenges involves investing in better equipment, training workers, and maintaining a rigorous quality control system.
Common Challenges in Meeting Casting Tolerances
Challenge | Impact on Tolerance Accuracy | Solution |
---|---|---|
Material Variability | Different batches of material may behave inconsistently | Standardize material sourcing and testing |
Mold Wear and Tear | Worn molds can lead to dimensional inaccuracies | Regular mold maintenance and replacement |
Temperature Variations | Rapid changes in temperature affect material shrinkage | Consistent temperature control in the production environment |
Human Error | Mistakes during casting or inspection lead to deviations | Regular training and quality control checks |
14. What industries rely on precise casting tolerances?
Several industries depend on precise casting tolerances for producing high-quality, durable parts. The automotive, aerospace, and medical industries, for example, require stringent dimensional accuracy to ensure the safety and functionality of their products. Even slight deviations can lead to product failure or safety hazards, making the adherence to strict tolerances essential in these fields.
Industries requiring high precision must invest in the right technology and standards to ensure consistent casting performance.
Industries Requiring High Precision in Casting
Industry | Precision Requirements | Examples of Applications |
---|---|---|
Aerospace | Extremely tight tolerances | Aircraft engine parts, structural components |
Automotive | High precision, moderate tolerances | Engine blocks, transmission components |
Medical Devices | High precision, strict standards | Surgical instruments, implants |
15. What are the future trends in casting tolerances?
The future of casting tolerances is shaped by advancements in technology, materials science, and automation. Additive manufacturing and advanced measurement tools are making it easier to achieve higher precision at lower costs. Additionally, the growing use of AI and machine learning in casting processes is improving the consistency and accuracy of tolerances.
These technological advancements promise to push the boundaries of what’s possible in casting precision, further enhancing product quality and efficiency.
Future Trends in Casting Tolerances
Trend | Impact on Tolerances | Example of Change |
---|---|---|
Additive Manufacturing | Ability to achieve complex geometries with tight tolerances | 3D-printed metal parts for aerospace applications |
AI and Machine Learning | Improved quality control and precision adjustments | Automated detection of tolerance deviations during casting |
New Materials | Materials with better dimensional stability | Carbon fiber-infused metals for automotive parts |
Conclusion
Understanding the differences between NADCA and ISO casting tolerances is crucial for ensuring your products meet the required standards of precision and quality. Whether you’re working within North America or globally, these standards will help guide your production process. To ensure the best results, consider your specific material, casting method, and regional requirements when choosing the appropriate standard for your casting needs.
FAQ Section
- Q1: What are casting tolerances?
Casting tolerances refer to the permissible variation in the dimensions of a cast part from the intended design. These tolerances ensure that cast parts fit together and function correctly in the final assembly. - Q2: How does NADCA standardize casting tolerances?
NADCA defines casting tolerances specifically for die casting, offering guidelines based on material type and casting complexity to ensure precision and quality. - Q3: How do ISO casting standards differ from NADCA?
ISO casting standards are more broadly applicable to various casting methods and materials, while NADCA is specific to die-casting and often used in North America. - Q4: What factors affect the accuracy of casting tolerances?
Material properties, casting methods, temperature variations, and tool precision all influence the accuracy of casting tolerances. - Q5: How do manufacturers ensure casting tolerances are met?
Manufacturers ensure casting tolerances by using accurate measuring tools, employing quality control techniques, and choosing the right materials and casting methods for the job.