High temperature alloys are essential materials in various industrial sectors due to their ability to maintain strength and stability at elevated temperatures. In this article, we will explore what high temperature alloys are, their types, applications, and why they are crucial in industries like aerospace, automotive, and power generation. Whether you’re involved in the selection of materials for high-performance applications or just curious about these alloys, this guide will provide valuable insights into their properties, benefits, and challenges.
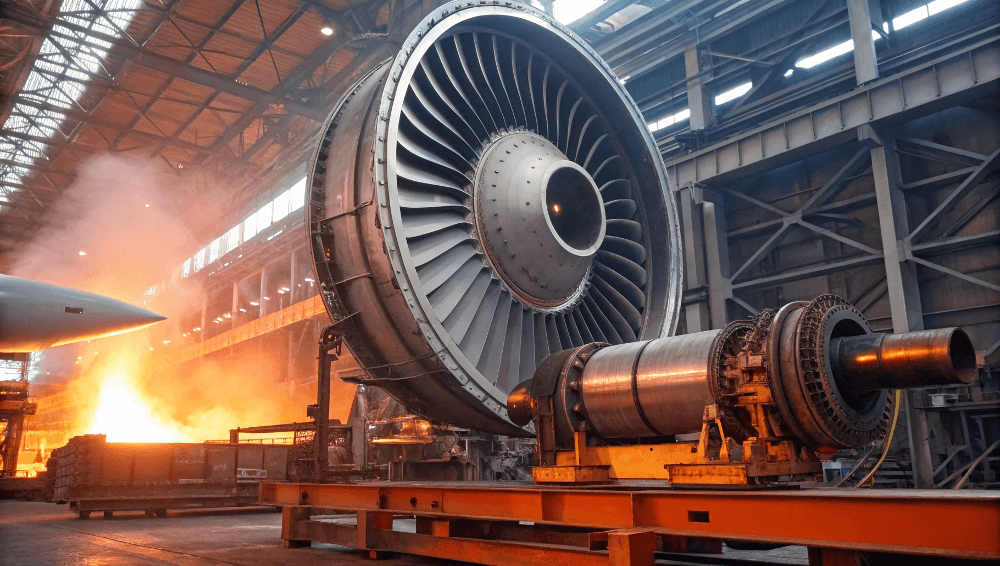
1. Introduction to High Temperature Alloys
High temperature alloys are specially designed materials capable of withstanding extreme temperatures and harsh environments without compromising their structural integrity. These alloys are vital in industries where components are exposed to continuous heat, such as in jet engines, power plants, and chemical reactors. So, what makes high temperature alloys so crucial? The secret lies in their exceptional properties, which allow them to perform reliably in applications that other materials would fail under.
But here’s the kicker—high temperature alloys maintain their strength and resistance to oxidation even in temperatures exceeding 1000°C. This property makes them indispensable for industries requiring materials that can withstand prolonged exposure to high heat without degrading. For instance, jet engines use these alloys for turbine blades and exhaust systems, where conventional metals would melt or lose their mechanical properties.
These alloys primarily consist of elements like nickel, cobalt, and iron, each contributing unique characteristics to the alloy’s performance. Ready for the good part? Let’s dive deeper into the types of high temperature alloys and how they differ in terms of composition and applications.
High Temperature Alloy Type | Key Components | Typical Applications |
---|---|---|
Nickel-based alloys | Nickel, chromium, molybdenum | Jet engines, gas turbines, chemical reactors |
Cobalt-based alloys | Cobalt, chromium, tungsten | Turbine blades, heat exchangers |
Iron-based alloys | Iron, chromium, aluminum | Industrial furnaces, boiler tubes |
Titanium alloys | Titanium, aluminum, vanadium | Aerospace, automotive, medical devices |
2. Types of High Temperature Alloys
High temperature alloys come in various compositions, each tailored to specific industrial needs. The most common types include nickel-based, cobalt-based, iron-based, and titanium alloys. Each alloy type is engineered to deliver high resistance to oxidation, corrosion, and thermal fatigue.
What’s the real story? Let’s explore each type in detail and understand where they are used most effectively.
Nickel-based alloys are the most widely used in high temperature applications. These alloys provide excellent resistance to both oxidation and corrosion, making them ideal for gas turbines and jet engine components. They also maintain their strength at temperatures that would cause other metals to soften or weaken. In aerospace, for example, nickel alloys are used in turbine blades that need to withstand extreme heat and mechanical stress.
This is where it gets interesting—cobalt-based alloys, while similar to nickel alloys, are particularly resistant to wear and oxidation at higher temperatures. These properties make them essential in applications like turbine blades in power generation and heat exchangers. Cobalt alloys are also used in the chemical processing industry, where they are exposed to high-temperature corrosive environments.
Iron-based alloys, on the other hand, are cost-effective and still provide good performance at high temperatures, though they are not as durable as their nickel and cobalt counterparts. These alloys are often used in industrial furnaces and boiler tubes, where extreme heat exposure is a regular occurrence.
Lastly, titanium alloys are unique for their lightweight and high strength at elevated temperatures. They are commonly used in aerospace components, where reducing weight while maintaining strength is critical. Titanium alloys are also used in automotive applications, particularly in parts that require both heat resistance and low mass.
Alloy Type | Advantages | Limitations | Best Use Case |
---|---|---|---|
Nickel-based alloys | Excellent oxidation and corrosion resistance | High cost | Aerospace, gas turbines |
Cobalt-based alloys | Exceptional wear resistance, high temperature stability | Costly | Heat exchangers, turbine blades |
Iron-based alloys | Affordable, good high temperature performance | Lower durability | Industrial furnaces, boiler tubes |
Titanium alloys | Lightweight, high strength, corrosion-resistant | Expensive, limited high-temperature range | Aerospace, automotive |
3. Applications of High Temperature Alloys
High temperature alloys play a pivotal role in several industries, where their ability to withstand extreme temperatures is crucial. Whether it’s for aerospace, automotive, or power generation, these alloys ensure that components operate efficiently, safely, and for extended periods without failure.
Here’s the deal—in the aerospace industry, high temperature alloys are indispensable. Jet engines, for instance, generate immense heat during operation. The turbine blades, which are exposed to the hottest parts of the engine, must be made of materials that can withstand such conditions. This is where nickel-based alloys excel, providing the strength and heat resistance needed for these critical components.
In the power generation sector, high temperature alloys are used in gas turbines and steam boilers, where they help improve the efficiency and lifespan of turbines. These alloys are designed to handle the continuous heat stress of electricity generation, ensuring that power plants operate smoothly without excessive maintenance costs or downtime.
You might be wondering—how about the automotive sector? High temperature alloys are also used in engine parts, such as exhaust valves and turbine wheels. The high temperatures generated in the engine’s combustion process require materials that won’t degrade, and high temperature alloys are the perfect solution. These alloys ensure that automotive engines run efficiently while maintaining performance and reliability.
Industry | Application | Alloy Type | Function |
---|---|---|---|
Aerospace | Jet engine turbine blades | Nickel-based alloys | Heat resistance, strength at high temperatures |
Power generation | Gas turbines, steam boilers | Nickel and cobalt alloys | High-temperature stability, wear resistance |
Automotive | Exhaust valves, turbine wheels | Iron-based and titanium alloys | Heat resistance, performance enhancement |
Chemical processing | Reactors, heat exchangers | Cobalt-based alloys | Corrosion resistance at high temperatures |
4. Key Properties of High Temperature Alloys
The key properties of high temperature alloys are what set them apart from other materials. These alloys are designed to perform under extreme conditions, ensuring that critical components function as required. Among the most important properties are strength at high temperatures, resistance to oxidation and corrosion, and thermal stability.
What’s the catch? Strength at high temperatures is one of the primary reasons high temperature alloys are so valuable. At high temperatures, most materials begin to lose their structural integrity, but high temperature alloys are engineered to maintain their strength, even when exposed to the most demanding conditions. This property is vital for components in jet engines, power plants, and chemical reactors, where structural failure can lead to catastrophic results.
But here’s the kicker—oxidation and corrosion resistance are also crucial properties of high temperature alloys. In high heat environments, components are not only subjected to thermal stress but also to corrosive gases and chemicals. Without adequate protection, these components would degrade quickly. High temperature alloys contain elements like chromium and molybdenum, which form protective oxide layers on the surface, preventing corrosion and ensuring the longevity of critical components.
Thermal stability is another defining characteristic. High temperature alloys retain their properties even when subjected to rapid temperature changes, a feature essential in industries where temperature fluctuations are common. Whether it’s in a furnace or a jet engine, these alloys are designed to endure without warping or losing their performance.
Property | Benefit | Importance |
---|---|---|
Strength at high temperatures | Maintains structural integrity | Essential for aerospace, power plants |
Oxidation resistance | Protects against corrosion | Vital for components exposed to harsh gases |
Corrosion resistance | Prevents degradation in corrosive environments | Crucial for chemical processing applications |
Thermal stability | Resists changes in shape under temperature fluctuations | Needed in dynamic temperature environments |
5. Factors Affecting the Performance of High Temperature Alloys
Several factors influence the performance of high temperature alloys in various applications. These include the composition of the alloy, the manufacturing process, environmental conditions, and the design of the components.
Ready for the good part? The composition of the alloy plays a significant role in determining its ability to withstand high temperatures. Alloys with higher amounts of nickel, for instance, tend to perform better in extreme heat environments. The type and amount of alloying elements used can determine the alloy’s strength, oxidation resistance, and thermal stability.
This is where it gets interesting—the manufacturing process also has a major impact on the alloy’s performance. Techniques such as casting, forging, and welding can affect the final properties of the alloy. For example, improper casting techniques may lead to defects in the alloy, compromising its ability to withstand high temperatures. As such, precision in the manufacturing process is key to ensuring the performance of high temperature alloys.
Environmental conditions, such as exposure to corrosive gases, moisture, or high-pressure environments, can also impact the performance of high temperature alloys. Components used in power plants or chemical reactors, for example, may experience different levels of stress depending on the operational conditions. Designing components with these factors in mind is essential for ensuring their longevity.
Factor | Impact on Performance | Explanation |
---|---|---|
Alloy composition | Affects strength and resistance | Higher nickel content improves heat resistance |
Manufacturing process | Influences structural integrity | Precision ensures performance under high temperatures |
Environmental conditions | Affects durability and lifespan | Exposure to corrosive gases or high pressure impacts longevity |
6. The Role of High Temperature Alloys in Aerospace
High temperature alloys are critical in aerospace applications, where they ensure the performance and safety of key components. These alloys are used extensively in jet engines, turbine blades, exhaust systems, and many other parts that are subjected to extreme conditions.
But here’s the kicker—in jet engines, turbine blades are exposed to extremely high temperatures and mechanical stress. Without high temperature alloys, these components would fail under the intense heat generated during flight. Nickel-based alloys are particularly popular in this application due to their ability to withstand both high temperatures and mechanical wear.
You might be wondering—how do these alloys help in improving fuel efficiency and engine performance? The key is in their ability to retain strength and form under high temperatures, allowing engines to operate at higher temperatures without sacrificing performance. This not only improves fuel efficiency but also reduces emissions, contributing to more sustainable aviation practices.
High temperature alloys are also used in other parts of the aircraft, such as the exhaust systems and afterburners, where their resistance to heat and oxidation ensures that components remain functional even in the most demanding environments.
Component | Alloy Used | Role in Aerospace |
---|---|---|
Turbine blades | Nickel-based alloys | High heat resistance, mechanical strength |
Exhaust systems | Cobalt-based alloys | Heat and oxidation resistance |
Afterburners | Titanium alloys | Lightweight, high heat resistance |
7. How High Temperature Alloys Improve Power Generation
High temperature alloys are essential in the power generation industry, where they are used in turbines, reactors, and other critical components. These alloys help improve efficiency and ensure the safe operation of power plants, even in the most demanding environments.
What’s the real story? Gas turbines, which are at the heart of most power plants, operate at extremely high temperatures. To function efficiently, these turbines need to be made from materials that can withstand the heat generated by the combustion process. High temperature alloys, such as nickel and cobalt alloys, provide the strength and resistance to oxidation required for these critical components.
This is where it gets interesting—the alloys used in power plants not only improve efficiency but also enhance safety. Components made from high temperature alloys can withstand the stresses of continuous operation without degrading, reducing the risk of catastrophic failure and minimizing downtime for repairs.
High temperature alloys are also used in boiler tubes, reactors, and heat exchangers, where they help maintain the integrity of the components exposed to high pressure and heat. These alloys ensure that power generation equipment can operate efficiently and safely for extended periods.
Component | Alloy Used | Function in Power Generation |
---|---|---|
Gas turbines | Nickel-based alloys | High heat resistance, durability |
Boiler tubes | Iron-based alloys | Cost-effective heat resistance |
Heat exchangers | Cobalt-based alloys | Corrosion resistance, high-temperature performance |
8. Automotive Industry and High Temperature Alloys
In the automotive industry, high temperature alloys are used in exhaust systems, engine components, and other parts that are exposed to extreme heat. These alloys help improve engine performance, reduce emissions, and ensure the longevity of critical components.
What’s the catch? Automotive engines generate immense heat during operation, particularly in the exhaust system and turbine wheels. High temperature alloys are used in exhaust valves, where their ability to withstand high temperatures without degrading is essential for maintaining performance.
Ready for the good part? High temperature alloys also play a role in improving fuel efficiency and reducing emissions. By using these alloys in critical engine components, manufacturers can design engines that run hotter and more efficiently, resulting in improved fuel economy and fewer emissions. These alloys are particularly important in the development of hybrid and electric vehicles, where maximizing efficiency is key to improving overall performance.
Component | Alloy Used | Role in Automotive |
---|---|---|
Exhaust valves | Iron-based alloys | Heat resistance, durability |
Turbine wheels | Titanium alloys | Lightweight, heat resistance |
Engine components | Nickel-based alloys | Strength, heat resistance |
9. Challenges in Manufacturing High Temperature Alloys
While high temperature alloys offer numerous benefits, manufacturing them comes with its own set of challenges. These alloys are often difficult to cast, weld, and machine due to their complex composition and high melting points.
What’s the real story? Casting high temperature alloys requires advanced techniques and equipment to handle their high melting points. Without the right tools and expertise, manufacturers may encounter defects that compromise the performance of the alloy. This is particularly true for alloys like nickel-based ones, which require precision casting to ensure their structural integrity.
You might be wondering—how does this affect the cost of high temperature alloys? The manufacturing process is often labor-intensive and expensive, contributing to the overall cost of these materials. As such, manufacturers must carefully weigh the cost of production against the performance benefits when selecting alloys for a specific application.
Welding high temperature alloys is another challenge, as the heat required for welding can cause warping or degradation of the material. Specialized techniques are often required to ensure that the welded joints maintain their strength and resistance to heat.
Challenge | Impact on Manufacturing | Solution |
---|---|---|
Casting high melting point alloys | Risk of defects | Advanced casting techniques, precision |
Welding high temperature alloys | Warping, material degradation | Specialized welding methods |
High production costs | Increased cost of alloys | Balancing cost with performance benefits |
10. Innovations in High Temperature Alloy Research
The field of high temperature alloy research is continuously evolving, with innovations focused on improving performance, reducing costs, and expanding the range of applications for these materials. Researchers are exploring new alloy compositions and production techniques to create materials that can perform even better under extreme conditions.
But here’s the kicker—new alloys are being developed that offer enhanced resistance to oxidation, corrosion, and thermal fatigue. These innovations promise to further extend the lifespan of critical components in industries like aerospace, power generation, and automotive manufacturing. For example, recent research has led to the development of alloys with improved resistance to sulfur and chlorine, which are common in high-temperature environments.
Ready for the good part? Researchers are also exploring the potential of nanotechnology in high temperature alloys. By manipulating the structure of alloys at the nanoscale, scientists hope to create materials that are even stronger and more resistant to high temperatures. These advancements could lead to even more efficient engines, power plants, and industrial processes.
Innovation | Benefit | Impact on Industry |
---|---|---|
Improved oxidation resistance | Longer lifespan, reduced maintenance | Aerospace, power generation |
Nanotechnology-enhanced alloys | Higher strength, better performance | Aerospace, automotive, energy sectors |
Sulfur and chlorine resistance | Better performance in harsh environments | Chemical processing, power plants |
11. The Environmental Impact of High Temperature Alloys
High temperature alloys, while essential for many industries, also come with an environmental footprint. The production of these materials requires significant energy input and can result in high emissions if not properly managed.
What’s the catch? The production of high temperature alloys involves mining raw materials, smelting, and processing, all of which contribute to environmental degradation. However, efforts are being made to reduce the carbon footprint of alloy production by implementing more sustainable practices, such as recycling and using cleaner energy sources.
This is where it gets interesting—recycling high temperature alloys is one of the most effective ways to minimize their environmental impact. By reusing these alloys, manufacturers can reduce the need for new raw materials and lower the energy consumption associated with production. Additionally, recycling can help mitigate the environmental impact of mining, which can be a major source of pollution.
Environmental Impact | Cause | Solution |
---|---|---|
High energy consumption | Smelting, alloy production | Use of renewable energy, recycling |
Mining pollution | Raw material extraction | Recycling, sustainable sourcing |
Carbon emissions | Industrial processes | Cleaner manufacturing technologies |
12. Selection Criteria for High Temperature Alloys
When selecting a high temperature alloy for a specific application, several factors need to be considered, including performance, cost, and material properties. The right alloy can ensure that components perform well over time without premature failure.
What’s the real story? The first consideration is the performance requirements of the application. For instance, in aerospace, the alloy must be able to withstand extreme temperatures and mechanical stress. In contrast, power generation applications may prioritize oxidation resistance over strength.
You might be wondering—how about cost? While high temperature alloys can be expensive, the benefits they provide in terms of performance, longevity, and safety often outweigh the upfront costs. It’s essential to strike the right balance between performance and cost when choosing an alloy for a specific application.
Another critical factor is the alloy’s resistance to environmental factors, such as corrosive gases or moisture. Depending on the industry, the alloy may need to perform under challenging environmental conditions, which may require additional properties like corrosion or oxidation resistance.
Consideration | Factors | Impact on Selection |
---|---|---|
Performance requirements | Temperature, mechanical stress | Ensures durability and reliability |
Cost | Initial price vs. long-term benefits | Balances affordability with longevity |
Environmental resistance | Corrosion, oxidation | Needed for industries like power generation, chemical processing |
13. How to Maintain High Temperature Alloys in Industrial Applications
Maintaining high temperature alloys in industrial applications is crucial to ensure their longevity and performance. Proper maintenance can prevent premature failure and reduce costly downtime for repairs.
What’s the real story? Regular inspections are essential to identify signs of wear and tear, such as cracks, oxidation, or corrosion. These inspections can help detect problems before they escalate into major failures, ensuring the continuous operation of critical components.
But here’s the kicker—keeping high temperature alloys in top shape also involves following best practices for maintenance, such as cleaning the components regularly and monitoring their operating conditions. For example, jet engines are subjected to extreme heat, so maintaining the temperature control systems is essential for avoiding overheating and ensuring optimal performance.
Ready for the good part? In industries like power generation and chemical processing, it’s also important to perform periodic repairs and replacements. Replacing worn components with new, high-quality alloys ensures that the system remains efficient and safe.
Maintenance Activity | Purpose | Impact |
---|---|---|
Regular inspections | Detect wear and tear early | Prevents catastrophic failures |
Cleaning components | Removes contaminants, reduces corrosion | Extends lifespan, maintains performance |
Periodic repairs and replacements | Ensures efficiency and safety | Reduces downtime, ensures reliability |
14. Cost Considerations in High Temperature Alloys
Cost is a major consideration when selecting high temperature alloys, but it’s important to look beyond the initial price tag and focus on long-term benefits.
What’s the catch? High temperature alloys are expensive, but they often provide significant cost savings over time by reducing maintenance costs and extending the lifespan of critical components. For instance, in aerospace applications, the durability of high temperature alloys can result in fewer replacements and less frequent repairs.
This is where it gets interesting—while the upfront cost may be higher, high temperature alloys often lead to reduced operational costs. Their superior performance can increase the overall efficiency of a system, leading to long-term savings. When selecting an alloy, manufacturers should consider both the initial cost and the potential long-term benefits.
Cost Factor | Impact on Selection | Benefit |
---|---|---|
Initial cost | Higher upfront expense | Long-term durability, reduced downtime |
Long-term savings | Reduced maintenance, fewer replacements | Cost-effective in the long run |
15. Conclusion: The Future of High Temperature Alloys
High temperature alloys will continue to play a vital role in industries that require materials to withstand extreme conditions. As new alloys are developed and innovations in manufacturing and material science progress, we can expect to see even greater performance and efficiency.
What’s the real story? The ongoing research and development of high temperature alloys promise to push the boundaries of what’s possible, enabling the creation of even more efficient engines, power plants, and manufacturing processes. As industries evolve and demands increase, high temperature alloys will remain essential for ensuring performance, reliability, and safety.
Ready for the good part? As these alloys continue to improve, we can expect even more applications, longer-lasting components, and more sustainable practices. High temperature alloys are not just a necessity—they are a key part of our technological future.
Future Trends | Impact | Industries Affected |
---|---|---|
New alloy compositions | Improved performance, higher efficiency | Aerospace, automotive, power generation |
Advanced manufacturing techniques | Lower costs, higher precision | All industries using high temperature alloys |
FAQ Section
Q1: What are high temperature alloys?
High temperature alloys are materials designed to maintain strength and resist oxidation at elevated temperatures, making them suitable for applications like jet engines, turbines, and chemical reactors.
Q2: How does the performance of high temperature alloys differ from regular alloys?
High temperature alloys offer superior heat resistance, corrosion resistance, and strength at elevated temperatures compared to regular alloys, which are unsuitable for extreme conditions.
Q3: What are the most common applications of high temperature alloys?
They are commonly used in aerospace for turbine blades, power generation in gas turbines and steam boilers, and automotive applications like exhaust valves and turbine wheels.
Q4: Why are nickel-based alloys commonly used for high-temperature applications?
Nickel-based alloys offer excellent resistance to heat, corrosion, and oxidation, making them ideal for high-temperature environments like aerospace engines and power plants.
Q5: How do innovations in high temperature alloys improve their performance?
Innovations focus on enhancing resistance to heat, oxidation, and corrosion. These advancements improve the longevity, efficiency, and safety of components used in high-performance industries.