Investment casting tolerances play a crucial role in the production of precision castings, ensuring the parts are produced within required dimensions for high-quality applications. In this comprehensive guide, we will explore investment casting tolerances, their impact on part quality, and how various factors influence their accuracy. We will dive into industry standards, measurement techniques, and offer best practices to achieve tight tolerances. By the end, you will have a thorough understanding of how to manage and optimize tolerances in your investment casting process.
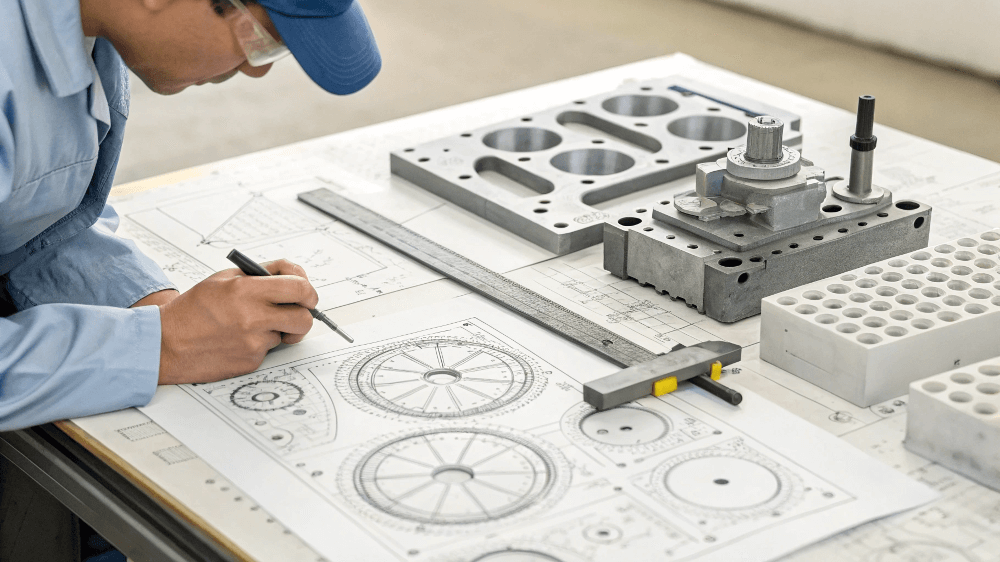
1. Introduction to Investment Casting Tolerances
Investment casting is a method used to produce high-precision metal parts for various industries, from aerospace to medical equipment. At the heart of this process lies the concept of tolerances, which define the allowable deviations in the dimensions of a part. Without proper tolerances, parts may fail to meet design specifications, potentially resulting in costly rework, delays, or even product failure.
What’s the real story here? Tolerances ensure that castings meet the required specifications and that each part will function as intended. From small mechanical components to large industrial parts, the need for precise dimensions cannot be overstated. By adhering to tight tolerances, manufacturers can produce complex geometries with superior surface finishes, making investment casting ideal for applications where precision is critical.
In the following sections, we will break down the different types of tolerances used in investment casting and explore how they impact both the process and the final product. You’ll gain a solid understanding of the key principles that govern tolerances and why they matter so much.
Tolerance Type | Description | Typical Use Cases |
---|---|---|
Linear Tolerances | Variations in length or width | Small mechanical parts |
Angular Tolerances | Angles between surfaces | Aerospace components |
Geometric Tolerances | Complex geometric relationships | Automotive parts |
2. What Are Investment Casting Tolerances?
Investment casting tolerances refer to the allowable variations in the size and shape of the cast part. These tolerances are critical because they define how accurately a casting must conform to its design, ensuring that the part will fit into the assembly or function as intended. The tighter the tolerance, the more precise the part must be.
So, how do investment casting tolerances compare to other manufacturing methods? Investment casting typically offers much tighter tolerances compared to processes like sand casting, where deviations can be larger. This high precision is what makes investment casting an ideal choice for industries like aerospace, medical devices, and high-performance engineering.
Here’s the kicker: tighter tolerances often require more advanced techniques, equipment, and higher-quality materials, which may come at a premium cost. However, the benefits of precise tolerances far outweigh the extra investment when it comes to high-performance applications. Parts that meet strict tolerances perform better, have longer lifespans, and reduce the likelihood of failure in critical environments.
Tolerance Range | Material Type | Precision Level |
---|---|---|
±0.002 inches | Stainless Steel | High Precision |
±0.005 inches | Aluminum | Medium Precision |
±0.010 inches | Bronze | Low Precision |
3. Common Tolerances in Investment Casting
Investment casting uses several types of tolerances to control the accuracy of parts. These include linear dimensional tolerances, angular tolerances, and geometric tolerances. Each plays a distinct role in ensuring the final product meets the design specifications and functions correctly in its application.
Let’s break it down: linear dimensional tolerances govern the variation in size along the length or width of a part. Angular tolerances, on the other hand, are used to control the angles between surfaces, ensuring that components fit together perfectly. Finally, geometric tolerances address more complex relationships between surfaces, such as flatness, roundness, and parallelism.
What’s the real story? These tolerances are not just numbers on paper—they directly impact how the parts interact in the final assembly. For example, a poorly aligned angle in a critical aerospace component could lead to catastrophic failure. This is why controlling investment casting tolerances is so important, especially in high-risk industries.
Tolerance Type | Description | Key Applications |
---|---|---|
Linear | Length, width, or height | Automotive, Machinery |
Angular | Angles between surfaces | Aerospace, Medical |
Geometric | Surface relationships | High-precision tooling |
4. Factors That Affect Investment Casting Tolerances
There are several factors that influence the tolerances achievable in investment casting. One of the biggest is material selection. Different materials exhibit varying levels of thermal expansion, which can affect the final dimensions of a casting. For example, metals like steel and aluminum expand at different rates when heated, which can lead to discrepancies in the final part dimensions if not carefully managed.
What’s the real story here? Temperature control during the casting process is another major factor. Any fluctuation in temperature can cause the material to shrink or expand unevenly, leading to a deviation from the intended size. Furthermore, mold design plays a critical role—an inefficient mold design can introduce errors into the final part.
Ready for the good part? Post-casting processes like machining, heat treatment, and surface finishing also affect the final tolerances. While machining can help refine the dimensions, excessive removal of material can compromise the strength and integrity of the casting. It’s a delicate balancing act.
Factor | Impact on Tolerance | Best Practices |
---|---|---|
Material Type | Thermal expansion | Select low-expansion alloys |
Temperature Control | Shrinkage/expansion | Maintain stable conditions |
Mold Design | Geometrical accuracy | Use precision mold design |
5. Investment Casting Tolerances vs. Other Casting Methods
When compared to other casting methods like sand casting or die casting, investment casting offers superior precision. Sand casting, while economical, tends to produce larger tolerance ranges, which makes it less suitable for high-precision applications. Die casting can achieve better precision than sand casting but still falls short of the level offered by investment casting.
But here’s the kicker: despite the advantages of investment casting, it’s not always the best choice for every application. For large parts with less stringent tolerance requirements, sand casting may be the more cost-effective option. However, when it comes to parts that demand tight tolerances—such as medical devices or complex aerospace components—investment casting is the go-to solution.
Here’s why: investment casting provides a high level of accuracy, can handle intricate designs, and supports a wide variety of materials. These features make it the preferred choice for industries where reliability and precision are paramount.
Casting Method | Tolerances | Cost Level | Best Use Case |
---|---|---|---|
Investment Casting | ±0.002–±0.005 inches | High | Aerospace, Medical |
Sand Casting | ±0.050–±0.125 inches | Low | Large parts, General use |
Die Casting | ±0.005–±0.010 inches | Medium | High-volume, medium tolerance |
6. How to Measure Investment Casting Tolerances
Measuring investment casting tolerances is a critical step in ensuring the parts meet design specifications. The process typically involves tools such as micrometers, calipers, and specialized gauges. These instruments allow manufacturers to measure dimensions with high accuracy.
What’s the real story? Measurement also involves checking the surface finish and geometric relationships. Tools like coordinate measuring machines (CMM) can be used to assess not only dimensions but also complex shapes and surfaces. These machines create detailed 3D maps of the part, ensuring it meets all the necessary tolerances.
What’s the kicker? Automated inspection systems, including vision-based systems, have become increasingly popular. These systems can detect even the smallest deviations from design specifications, making them invaluable in high-precision manufacturing.
Measurement Tool | Accuracy Level | Typical Use Case |
---|---|---|
Micrometer | ±0.0001 inches | Small parts, precision checks |
Coordinate Measuring Machine (CMM) | ±0.0001 inches | Complex shapes and geometry |
Vision-Based Systems | ±0.001 inches | High-speed automated inspection |
7. The Role of Tolerances in Product Quality
Tolerances are directly linked to product quality. When parts are produced within tight tolerances, they fit and function as designed, reducing the risk of failures in the field. For industries like aerospace, medical, and automotive, this is especially critical. Parts that don’t meet the required tolerances can cause operational issues or even catastrophic failure.
Here’s the kicker: in high-precision industries, the cost of failure is immense. A malfunctioning part could lead to expensive recalls, project delays, and even safety risks. For example, in the aerospace industry, a deviation of even a few microns could cause a part to fail under stress.
Ready for the good part? Investment casting offers superior control over tolerances, ensuring the highest level of precision for mission-critical applications. This guarantees that the parts will meet the necessary performance standards, contributing to the overall reliability and success of the end product.
Industry | Tolerance Requirements | Impact of Tolerances |
---|---|---|
Aerospace | ±0.002 inches | High precision, safety-critical |
Medical Devices | ±0.003 inches | Performance and reliability |
Automotive | ±0.010 inches | Fit and function in assembly |
8. Industry Standards for Investment Casting Tolerances
There are several industry standards that govern investment casting tolerances. These standards, such as those set by ISO, ASTM, and AMS, ensure consistency and quality across the board. For example, ASTM A 780 outlines the necessary tolerance ranges for various metals used in casting.
What’s the real story? These standards provide manufacturers with a clear set of guidelines to follow, ensuring that every part produced meets the required quality levels. Adhering to these standards also helps ensure that parts are compatible with other components, reducing the likelihood of costly errors.
What’s the kicker? Certification and testing for compliance with these standards are crucial. Not only do they provide assurance to customers, but they also serve as proof that the manufacturer adheres to the best industry practices.
Standard | Tolerance Range | Material Type |
---|---|---|
ASTM A 780 | ±0.005 inches | Stainless Steel |
ISO 8062-3 | ±0.01 inches | Aluminum |
AMS 2175 | ±0.002 inches | Titanium |
9. Tight Tolerances in Investment Casting: When and Why?
Tight tolerances are crucial in many industries, especially when the parts in question are integral to safety or performance. For instance, in aerospace, parts must meet exact specifications to ensure that they function properly under extreme conditions. Medical devices, too, require precise tolerances to ensure that they fit together seamlessly and function as intended.
Here’s the kicker: tight tolerances come with challenges. The more precise the tolerance, the more costly and time-consuming the casting process becomes. However, for industries where failure is not an option, these costs are well worth the investment.
Ready for the good part? Achieving tight tolerances in investment casting is possible through advanced mold design, careful material selection, and precise control over the casting environment. When done correctly, the result is a part that performs flawlessly and stands the test of time.
Industry | Tolerance Range | Importance of Tight Tolerances |
---|---|---|
Aerospace | ±0.002 inches | Safety, reliability |
Medical Devices | ±0.003 inches | Precision and functionality |
Automotive | ±0.005 inches | Perfect fit and performance |
10. Adjusting Tolerances in Investment Casting for Different Applications
Adjusting tolerances for different applications is essential for optimizing cost and performance. For example, parts used in low-stress environments may not require the same tight tolerances as components used in high-performance machinery.
What’s the real story? Customizing tolerances based on customer needs can save money while still delivering a high-quality product. For instance, a part that will undergo additional machining might require looser tolerances, as the final dimensions will be refined later.
Ready for the good part? By carefully assessing the requirements of each project, manufacturers can offer flexibility in tolerance ranges while still meeting the functional needs of the part. This helps balance precision with cost-effectiveness.
Application | Tolerance Range | Key Considerations |
---|---|---|
Low-Stress Parts | ±0.010 inches | Cost-effective production |
High-Performance | ±0.002 inches | High precision required |
Custom Machining | ±0.005 inches | Tolerances adjusted post-production |
11. Managing Tolerances in High-Volume Production
Maintaining consistent tolerances in high-volume production can be challenging. As production scales up, even small errors in tolerance can be magnified, leading to significant discrepancies in the final parts.
But here’s the kicker: maintaining high tolerances in mass production requires robust quality control measures, automation, and regular inspections. Techniques like statistical process control (SPC) can help monitor and maintain precision during large-scale production runs.
Ready for the good part? Automation and advanced inspection technologies can help ensure that even in high-volume runs, each part meets the necessary tolerances, ensuring both consistency and efficiency in production.
Production Scale | Tolerance Control | Method Used |
---|---|---|
Low Volume | ±0.005 inches | Manual inspection |
High Volume | ±0.002 inches | Automated inspection |
Mass Production | ±0.010 inches | SPC and automated tools |
12. Impact of Tolerances on Cost and Lead Time
Tighter tolerances usually lead to higher costs and longer lead times. Why? Achieving high precision requires advanced techniques, better materials, and more rigorous quality control measures. Additionally, producing parts within tight tolerances can take longer due to the need for detailed checks and adjustments.
What’s the kicker? While tight tolerances drive up costs, they can reduce rework and ensure better product quality in the long run. For high-performance industries, such as aerospace and medical devices, the investment is often justified by the reliability and functionality of the final product.
Ready for the good part? By carefully selecting the appropriate tolerance level for each project, manufacturers can strike the right balance between cost, time, and precision, ensuring optimal outcomes for both the business and the customer.
Tolerance Level | Impact on Cost | Impact on Lead Time |
---|---|---|
±0.005 inches | Higher | Longer |
±0.010 inches | Lower | Shorter |
±0.002 inches | Highest | Longest |
13. Tolerance Adjustments During Post-Casting Processes
After the initial casting is complete, further processes like machining, heat treatment, and surface finishing can influence the final tolerances. Machining, for instance, is often used to refine the dimensions of cast parts, but it can introduce variations in size, especially if not controlled properly.
What’s the real story here? Post-casting processes give manufacturers the opportunity to improve the final product, but these adjustments can also introduce new challenges. Heat treatment, for example, may cause slight dimensional changes due to thermal expansion.
Ready for the good part? By carefully managing post-casting processes, manufacturers can ensure that the final part remains within required tolerances and performs as expected in its application.
Post-Casting Process | Impact on Tolerance | Key Considerations |
---|---|---|
Machining | ±0.002 inches | Surface finish improvement |
Heat Treatment | ±0.010 inches | Thermal expansion control |
Surface Finishing | ±0.005 inches | Final dimensional accuracy |
14. Troubleshooting Tolerance Issues in Investment Casting
Even with careful planning, tolerance issues can arise during the casting process. Common causes of tolerance problems include inaccurate mold designs, improper material selection, and errors during the casting or cooling stages.
What’s the real story? Troubleshooting tolerance issues requires a systematic approach. First, identify the source of the problem—whether it’s a mold design flaw, material issue, or cooling-related error. Then, apply corrective measures to ensure the issue doesn’t recur in future productions.
Here’s the kicker: prevention is key. By investing in high-quality molds, using the right materials, and monitoring the casting environment, manufacturers can prevent most tolerance issues before they occur.
Problem Cause | Common Issue | Solution |
---|---|---|
Mold Design | Dimensional error | Optimize mold design |
Material Selection | Thermal expansion | Select low-expansion alloys |
Cooling Process | Uneven shrinkage | Control cooling rate |
15. Conclusion and Final Thoughts on Investment Casting Tolerances
Investment casting tolerances are a vital aspect of the manufacturing process, directly influencing the quality, performance, and cost of the final product. By understanding the different types of tolerances, the factors that affect them, and the methods used to control and measure them, manufacturers can ensure that their parts meet design specifications and function reliably in their applications.
Ready for the good part? With the right approach, investment casting can deliver parts with superior precision, making it an ideal choice for industries that demand high-performance components. By focusing on tight tolerance management, manufacturers can meet the rigorous standards of industries like aerospace, medical, and automotive while optimizing cost and lead time.
FAQ Section
Q1: What are investment casting tolerances?
Investment casting tolerances refer to the allowable variations in the size and shape of the cast part. These tolerances define how closely the part must conform to its intended dimensions.
Q2: How does the material used affect investment casting tolerances?
The material selected for investment casting affects its thermal expansion properties, which in turn influence the achievable tolerances. Different materials expand and contract at different rates when heated.
Q3: What is the difference between investment casting and other casting methods in terms of tolerances?
Investment casting offers tighter tolerances compared to sand casting and die casting, making it ideal for high-precision applications that require exact dimensions.
Q4: How are investment casting tolerances measured?
Tolerances in investment casting are measured using tools like micrometers, coordinate measuring machines (CMM), and vision-based systems, depending on the complexity of the part.
Q5: Why are tight tolerances important in investment casting?
Tight tolerances are essential in industries like aerospace and medical devices, where even small deviations from specifications can lead to failure, safety risks, or performance issues.