Pattern and shrinkage are two critical concepts in the world of aluminum casting. If you’re in the casting industry, you’re likely familiar with how patterns and shrinkage impact the final product. Understanding these concepts is essential for ensuring the integrity, strength, and quality of your cast aluminum parts. In this article, we’ll dive deep into the details of pattern and shrinkage in aluminum casting processes, exploring why these factors matter, how to manage them, and the various techniques available to mitigate shrinkage.
So, why is this topic important? Aluminum is one of the most widely used metals in casting, but its properties make it prone to shrinkage during solidification. This can lead to defects such as cracks, dimensional inaccuracies, and decreased structural integrity in the final product. If you’re involved in the production or procurement of cast aluminum parts, you need to understand how to prevent and manage shrinkage while ensuring that the patterns used in casting align perfectly with the desired product specifications.
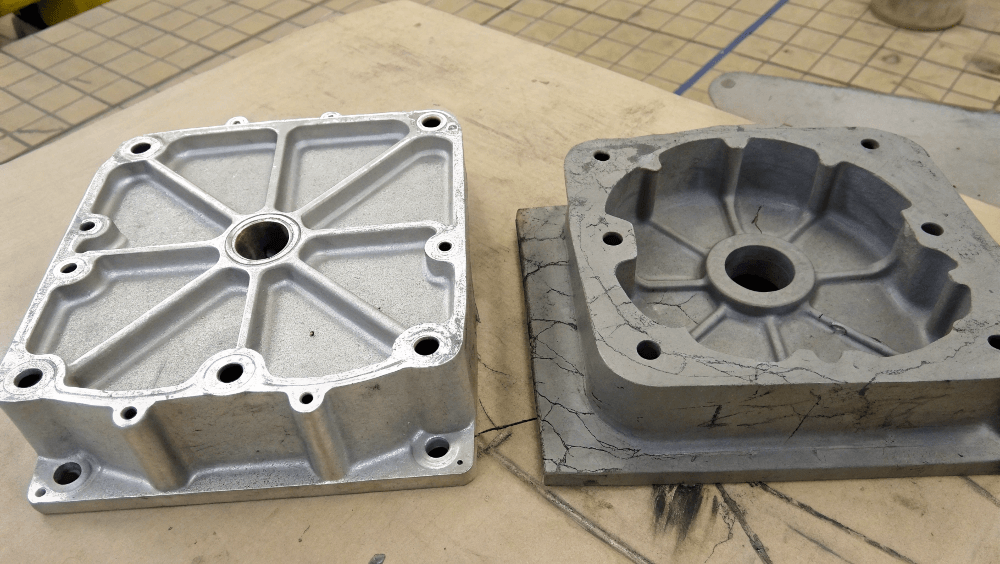
1. What is Pattern and Shrinkage in Cast Aluminum?
Before we dive into the details, it’s important to understand the basics. Pattern in aluminum casting refers to the mold used to create the desired shape of the final product. This pattern is typically made from a material like sand or metal and serves as the template that the molten aluminum is poured into. As the aluminum cools and solidifies, shrinkage occurs, meaning the aluminum contracts as it transitions from liquid to solid.
But here’s the kicker: shrinkage is not just a minor inconvenience. It can lead to serious defects if not managed correctly. When molten aluminum solidifies, it decreases in volume. This contraction can cause voids or cracks in the casting, which weakens the material and makes it unsuitable for some applications. That’s why it’s crucial to manage both pattern design and shrinkage control in the casting process.
Here’s the real story: the degree of shrinkage can vary based on a number of factors, including the composition of the alloy, the cooling rate, and the design of the pattern. In some cases, pattern design alone can help mitigate shrinkage to ensure a high-quality product.
Table 1: Basic Shrinkage Data for Cast Aluminum
Factor | Shrinkage Impact |
---|---|
Alloy Composition | Affects shrinkage rates based on alloy mix |
Cooling Rate | Faster cooling increases shrinkage |
Mold Material | Sand molds absorb heat slowly, reducing shrinkage |
Pattern Design | Thicker molds slow cooling, reducing shrinkage |
2. Why Do Patterns Matter in Cast Aluminum Production?
So, why do patterns play such an important role in aluminum casting? Well, the quality of the pattern directly affects the final outcome of the casting. When you pour molten aluminum into a mold, the pattern creates the shape, size, and features of the final product. If the pattern isn’t designed well, or if it deteriorates during the casting process, the final product will not meet the required specifications.
The pattern acts as the guide, and if it’s not accurate, the final aluminum part will exhibit defects. Ready for the good part? With a properly designed pattern, you can reduce the chances of shrinkage by controlling how the aluminum flows and cools within the mold. For example, thicker sections in the pattern can slow down the cooling rate, which helps prevent premature solidification and reduces the likelihood of shrinkage.
But there’s more: the type of material used for the pattern can also impact the rate of cooling and solidification. For example, sand molds tend to absorb heat slowly, which results in a slower cooling rate and, potentially, a lower degree of shrinkage. Metal molds, on the other hand, cool faster and can cause faster solidification, leading to more shrinkage.
Table 2: Pattern Material and Shrinkage Effect
Pattern Material | Effect on Shrinkage |
---|---|
Sand Molds | Absorb heat slowly, leading to slower cooling and less shrinkage |
Metal Molds | Cool faster, leading to quicker solidification and more shrinkage |
Ceramic Molds | Provide precise control over cooling, reducing shrinkage |
3. How Does Shrinkage Occur in Cast Aluminum?
Understanding how shrinkage happens during the casting process is essential for controlling it. Shrinkage occurs because of the inherent property of aluminum to contract as it cools and solidifies. The rate at which this happens depends on several factors, including the cooling speed, the aluminum alloy used, and the overall design of the mold.
Here’s where it gets interesting: the cooling rate of the aluminum directly influences how much shrinkage will occur. When molten aluminum is poured into the mold, it starts cooling at the outer edges first. As the outer part cools and solidifies, the material contracts, but the interior still remains in a liquid state. This leads to an imbalance in pressure and can cause voids or cracks in the casting.
The cooling process is a delicate balance—if it happens too quickly, shrinkage can be excessive, but if it happens too slowly, the aluminum might remain liquid too long, increasing the risk of oxidation and affecting the surface finish of the product. This is why cooling rate control is a vital part of minimizing shrinkage in cast aluminum.
Let’s break this down further with a table that summarizes the factors influencing shrinkage:
Table 3: Cooling Rate and Shrinkage in Aluminum
Cooling Rate | Effect on Shrinkage |
---|---|
Fast Cooling | Increases shrinkage due to rapid solidification |
Slow Cooling | Reduces shrinkage by allowing gradual solidification |
Uniform Cooling | Minimizes shrinkage by promoting even temperature distribution |
4. How to Manage Shrinkage in Cast Aluminum?
Now that we understand how shrinkage happens, the next logical step is figuring out how to manage it. Managing shrinkage in aluminum casting requires a combination of techniques and strategies. The first step is controlling the cooling rate. By managing how fast or slow the molten aluminum cools, you can minimize shrinkage.
This is where mold design comes in. For example, including risers and chills in the mold design can help control the flow and cooling of the molten metal. Risers are extra cavities that allow for the continuous feeding of molten aluminum into the mold, preventing shrinkage in the solidifying part. Chills, on the other hand, are inserts that absorb heat and slow down the cooling rate in specific areas of the mold, helping to reduce shrinkage in those areas.
Another technique that can help is adjusting the alloy composition. Some aluminum alloys are more prone to shrinkage than others, so selecting an alloy with lower shrinkage characteristics can make a significant difference in the final casting quality. But here’s the kicker—sometimes, it’s a combination of these techniques that provides the best results. Using the right alloy with the optimal mold design can go a long way in reducing shrinkage.
Table 4: Shrinkage Control Strategies
Control Technique | Description |
---|---|
Cooling Rate Control | Adjusting the cooling speed to manage shrinkage |
Mold Design | Using risers and chills to control molten aluminum flow |
Alloy Selection | Choosing alloys that shrink less during solidification |
5. What Are the Common Causes of Shrinkage in Cast Aluminum?
Let’s face it—shrinkage isn’t always easy to prevent. There are many factors that can cause shrinkage during the casting process. One of the main contributors is internal porosity. This happens when gas bubbles or trapped air become trapped inside the aluminum during solidification, causing voids or holes in the final product.
The type of mold material you use can also influence shrinkage. Sand molds, for instance, tend to absorb heat more slowly, which can cause the aluminum to cool at a slower rate and reduce shrinkage. On the other hand, metal molds tend to cool faster, causing the aluminum to solidify quickly and resulting in more shrinkage.
Temperature variations during casting can also contribute to shrinkage. If there are drastic temperature changes during the casting process, it can lead to uneven cooling, which in turn can lead to significant shrinkage defects.
Table 5: Common Causes of Shrinkage in Cast Aluminum
Cause | Effect on Shrinkage |
---|---|
Internal Porosity | Traps air and causes voids, increasing shrinkage |
Mold Material | Affects cooling rate, influencing shrinkage |
Temperature Variation | Uneven cooling causes more shrinkage defects |
6. How to Identify and Measure Shrinkage in Cast Aluminum?
Identifying and measuring shrinkage in cast aluminum can be tricky, but it’s an essential step in ensuring the final product is up to standard. There are several methods for detecting shrinkage, including visual inspection, ultrasonic testing, and x-ray imaging.
Visual inspection can reveal obvious shrinkage defects, such as cracks or voids in the aluminum. However, this method only works if the shrinkage is significant enough to be visible. For more subtle defects, ultrasonic testing and x-ray imaging can be used to detect internal shrinkage.
Let’s be honest—ultrasonic testing is one of the most effective ways to measure shrinkage. It uses sound waves to detect changes in density within the aluminum, which can indicate the presence of shrinkage. This technique is highly accurate and can detect even the smallest shrinkage defects.
Table 6: Methods to Identify Shrinkage in Cast Aluminum
Method | Effectiveness |
---|---|
Visual Inspection | Best for obvious shrinkage defects |
Ultrasonic Testing | Detects internal shrinkage defects |
X-ray Imaging | Detects both internal and external shrinkage |
7. What Are the Different Types of Shrinkage in Cast Aluminum?
Shrinkage in aluminum casting can be categorized into several types, each of which has different implications for the final product. Volumetric shrinkage occurs when the aluminum contracts as it solidifies, leading to a reduction in the overall volume of the casting.
Linear shrinkage refers to the reduction in the size of the casting in one dimension, such as the length or width. This can be a problem if the part needs to meet tight tolerances, as linear shrinkage can cause dimensional inaccuracies.
Finally, there’s macro shrinkage and micro shrinkage. Macro shrinkage is visible to the naked eye, often causing cracks or voids, while micro shrinkage is only detectable with specialized equipment like ultrasonic testing.
Table 7: Types of Shrinkage in Cast Aluminum
Type | Description |
---|---|
Volumetric Shrinkage | Overall reduction in the volume of the casting |
Linear Shrinkage | Shrinkage in one dimension, affecting size |
Macro Shrinkage | Visible shrinkage defects like cracks or voids |
Micro Shrinkage | Small, imperceptible shrinkage detected with tools |
8. What Is the Role of Mold Design in Minimizing Shrinkage?
As we’ve seen throughout the article, mold design is critical in minimizing shrinkage during aluminum casting. A well-designed mold helps control how the molten metal flows and solidifies, which directly affects shrinkage rates. One key aspect of mold design is the use of risers and chills.
Risers help ensure that the molten aluminum continues to flow into the mold as it solidifies, preventing shrinkage. Chills, on the other hand, are used to absorb heat and slow down the cooling process in specific areas, which can help prevent excessive shrinkage.
The strategic use of these mold design techniques is essential for producing high-quality aluminum castings with minimal shrinkage defects.
Table 8: Mold Design Strategies for Shrinkage Minimization
Design Technique | Effect on Shrinkage |
---|---|
Risers | Help feed molten aluminum into the mold as it solidifies, reducing shrinkage |
Chills | Absorb heat, slowing cooling in specific areas to prevent shrinkage |
Thick Mold Walls | Slow down the cooling rate, reducing overall shrinkage |
9. How Does the Alloy Composition Affect Shrinkage?
The alloy composition plays a significant role in the amount of shrinkage experienced during aluminum casting. Different aluminum alloys have varying shrinkage characteristics. The primary difference lies in the alloy’s composition, such as the amount of silicon, copper, and magnesium present in the mixture.
Here’s the deal: silicon, for instance, is often added to aluminum alloys because it helps reduce shrinkage by improving fluidity and enhancing the casting’s structural integrity. High-silicon alloys generally shrink less than others, and they are commonly used for casting parts that require precise dimensions.
On the flip side, certain alloys, particularly those with higher concentrations of copper, can experience more significant shrinkage. Copper increases the strength and hardness of aluminum, but it also leads to increased contraction as the metal cools. So, what does this mean for you? If you’re managing aluminum casting projects, selecting the right alloy composition is crucial to achieving minimal shrinkage and the desired final product quality.
By understanding the relationship between alloy composition and shrinkage, manufacturers can select the best alloys for specific applications and ensure that shrinkage doesn’t compromise the final product.
Table 9: Alloy Composition and Shrinkage Impact
Alloy Type | Effect on Shrinkage |
---|---|
High Silicon Alloys | Shrink less due to improved fluidity |
High Copper Alloys | Shrink more due to higher contraction rates |
Magnesium-based Alloys | Shrink moderately but offer high strength |
10. What Are the Most Effective Techniques for Minimizing Shrinkage?
There are several techniques available to help minimize shrinkage during the aluminum casting process. The most effective strategies involve a combination of controlling cooling rates, modifying mold designs, and choosing the right alloy.
For example, using sand casting can help reduce shrinkage because the sand mold absorbs heat more slowly than metal molds. This results in a slower cooling process, which minimizes the risk of shrinkage defects. Die casting, on the other hand, is typically faster but requires precise temperature control to prevent shrinkage from occurring.
Another key technique is post-casting machining. If shrinkage defects are detected after the casting process, machining can help remove these imperfections and correct the dimensional inaccuracies caused by shrinkage.
Ready for the good part? One of the most promising advancements in minimizing shrinkage is the use of simulation software. By using advanced simulation tools, manufacturers can predict where shrinkage is likely to occur and adjust the design or cooling process accordingly.
Table 10: Techniques for Minimizing Shrinkage
Technique | Description |
---|---|
Sand Casting | Slower cooling rate reduces shrinkage |
Die Casting | Requires precise temperature control to reduce shrinkage |
Post-Casting Machining | Corrects shrinkage defects after casting |
Simulation Software | Predicts shrinkage and optimizes the casting process |
11. How Does Cooling Rate Impact Shrinkage in Cast Aluminum?
Cooling rate is one of the most critical factors affecting shrinkage during aluminum casting. The rate at which molten aluminum solidifies directly influences the amount of shrinkage that occurs in the final product.
Here’s the kicker: if the aluminum cools too quickly, it will shrink more than if it cools slowly. Rapid cooling can cause surface hardening, while the inner portions of the casting remain in a liquid state, leading to shrinkage defects. On the other hand, slow cooling can lead to undesirable effects like oxidation and uneven surface finishes.
To control the cooling rate, manufacturers often use different methods depending on the type of casting. For example, in sand casting, the sand mold itself helps slow down the cooling rate by absorbing heat from the molten aluminum. In die casting, cooling channels are strategically placed within the mold to control the speed at which the aluminum cools.
In either case, cooling rate control is essential to minimizing shrinkage. By fine-tuning the cooling process, manufacturers can create castings with minimal defects, improving product quality and reducing waste.
Table 11: Cooling Rate Control in Cast Aluminum
Cooling Rate | Effect on Shrinkage |
---|---|
Fast Cooling | Increases shrinkage due to rapid solidification |
Slow Cooling | Reduces shrinkage by allowing gradual solidification |
Uniform Cooling | Minimizes shrinkage by promoting even temperature distribution |
12. What Are the Quality Control Measures for Shrinkage in Cast Aluminum?
When it comes to aluminum casting, quality control is a must. Monitoring and controlling shrinkage defects are critical to ensuring that the final product meets required specifications. So, what are the best ways to identify and manage shrinkage in aluminum castings?
First, inspection is key. Visual inspections can help detect obvious shrinkage defects like cracks, voids, or surface imperfections. But visual inspection can only go so far. For more precise detection, manufacturers turn to techniques like ultrasonic testing and x-ray imaging, which allow for the identification of internal shrinkage that may not be visible on the surface.
Next, process monitoring is vital. Keeping track of variables like mold temperature, alloy composition, and cooling rate can help predict where shrinkage may occur during the casting process. Using data logging systems, manufacturers can collect real-time data and adjust the process accordingly to minimize defects.
Let’s break this down with a table summarizing the most common quality control measures for shrinkage:
Table 12: Quality Control Measures for Shrinkage
Quality Control Measure | Description |
---|---|
Visual inspection | Identifying obvious defects like cracks or voids |
Ultrasonic testing | Detects internal shrinkage defects |
X-ray imaging | Detects both internal and external shrinkage |
Process monitoring | Tracks mold temperature, alloy composition, and cooling rate |
13. What Are the Consequences of Shrinkage in Cast Aluminum Parts?
Shrinkage can have serious consequences for the quality and functionality of cast aluminum parts. The most obvious consequence is dimensional inaccuracy. When shrinkage occurs, the final product can become too small or misshapen, leading to discrepancies in the required measurements.
But here’s the kicker: shrinkage doesn’t just affect the external dimensions of the part—it can also impact the mechanical properties. Shrinkage defects like voids or internal cracks can reduce the strength and durability of the aluminum, making it unsuitable for certain applications, especially those requiring high performance under stress.
Another significant consequence of shrinkage is increased costs. Shrinkage defects often require expensive repairs or machining to correct, adding to production costs. Additionally, defective parts may not meet quality standards and could lead to product rejections, further increasing the cost of production.
Table 13: Consequences of Shrinkage in Cast Aluminum
Consequence | Impact |
---|---|
Dimensional Inaccuracy | Leads to parts that don’t meet required measurements |
Reduced Mechanical Strength | Weakens the part due to voids or cracks |
Increased Costs | Requires repairs and corrections, raising production costs |
14. How Can Shrinkage Be Reduced in Large Aluminum Castings?
Reducing shrinkage in large aluminum castings presents unique challenges. The main issue is that large castings take longer to cool, increasing the likelihood of shrinkage. However, there are several strategies that can help minimize shrinkage in large-scale aluminum parts.
One effective method is to use thicker molds. Thicker molds provide more thermal mass, allowing for a more gradual cooling process that reduces the likelihood of shrinkage. Additionally, strategically placing chills within the mold can help control cooling rates in specific areas, preventing shrinkage from occurring in critical regions of the casting.
Another strategy is to use simulation software. For large castings, simulation tools can help manufacturers predict where shrinkage is likely to occur and adjust the design accordingly. By optimizing the cooling process and mold design, manufacturers can create large aluminum castings with minimal shrinkage.
Table 14: Techniques for Reducing Shrinkage in Large Castings
Technique | Description |
---|---|
Thicker Molds | Reduces rapid cooling by adding thermal mass |
Chills | Control cooling rate in specific areas to reduce shrinkage |
Simulation Software | Predicts shrinkage and optimizes mold design |
15. What Are the Latest Innovations in Reducing Shrinkage in Cast Aluminum?
As technology continues to advance, new innovations are being developed to help reduce shrinkage in aluminum casting. One promising development is the use of additive manufacturing in conjunction with traditional casting methods. 3D printing can create highly detailed, precise molds that can help reduce shrinkage by allowing for more accurate mold designs and cooling patterns.
Another innovation is advanced simulation software that uses artificial intelligence to predict shrinkage defects before the casting process even begins. These tools allow manufacturers to make adjustments in real-time, optimizing the casting process and reducing the risk of shrinkage.
But here’s the kicker: as these technologies continue to evolve, they’re opening up new possibilities for high-quality, defect-free aluminum castings. The future looks bright for manufacturers who embrace these advancements in shrinkage reduction.
Table 15: Innovations in Reducing Shrinkage
Innovation | Impact on Shrinkage |
---|---|
Additive Manufacturing | Creates precise molds for reduced shrinkage |
Simulation Software | Uses AI to predict and adjust shrinkage in real-time |
3D Printing | Improves mold design and cooling patterns |
Conclusion
In conclusion, pattern and shrinkage are crucial factors in the aluminum casting process that can significantly affect the quality and integrity of the final product. By understanding how shrinkage occurs and the role of patterns in controlling this process, manufacturers can implement effective strategies to minimize shrinkage and produce high-quality castings. The key to success lies in managing cooling rates, selecting the right alloy, and designing molds that promote even solidification.
Manufacturers who pay attention to these factors, use advanced technology, and adopt best practices will be able to produce aluminum castings that meet exacting standards for strength, durability, and dimensional accuracy.
FAQ Section
Q1: What is pattern and shrinkage in cast aluminum?
Pattern in cast aluminum refers to the mold used to create the desired shape of the final product. Shrinkage occurs as molten aluminum cools and contracts, leading to potential defects in the casting.
Q2: How does shrinkage affect the quality of cast aluminum?
Shrinkage can lead to defects such as cracks, voids, and dimensional inaccuracies, affecting the strength and durability of the final product.
Q3: What causes shrinkage in aluminum castings?
Shrinkage is caused by the contraction of molten aluminum as it cools and solidifies. Factors like cooling rate, alloy composition, and mold material can all influence shrinkage.
Q4: How can shrinkage in cast aluminum be minimized?
Shrinkage can be minimized by controlling the cooling rate, designing effective molds, and selecting the right aluminum alloys that are less prone to shrinkage.
Q5: What tools are used to measure shrinkage in aluminum castings?
Tools like ultrasonic testing, x-ray imaging, and visual inspection are used to detect and measure shrinkage defects in cast aluminum.