Steel casting is a critical process used in manufacturing durable and high-performance parts. If you’re in industries like automotive or aerospace, it’s essential to understand how this method can benefit your production process.
Steel casting involves pouring molten steel into molds to create various components. This article will explain the process, its benefits, and key considerations for your business.
If you’re working with steel components, understanding steel casting can make a huge difference. In this article, we’ll dive into the different types of steel casting, why it’s important, and how it compares to other methods. Let’s explore how this method benefits industries worldwide.
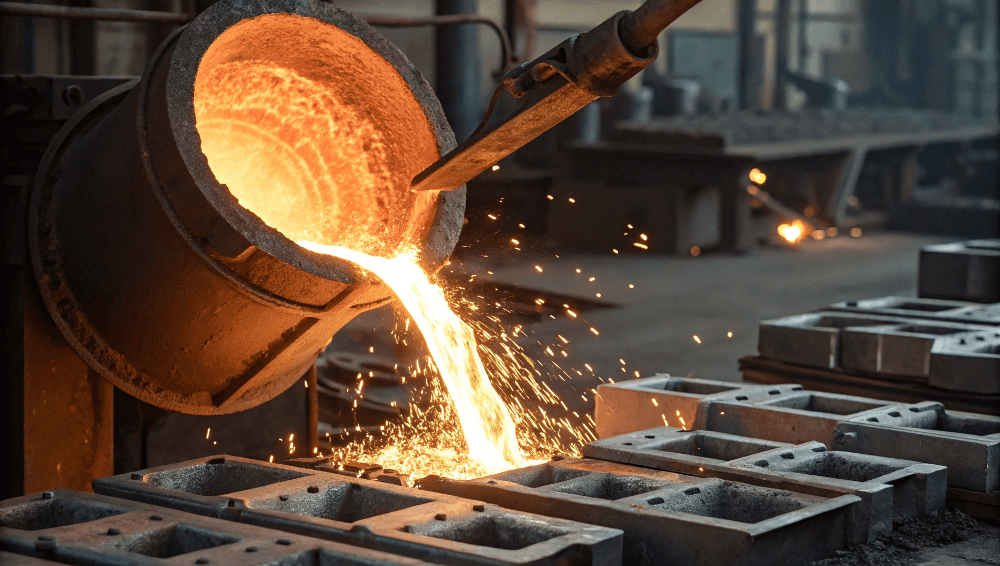
1. What is Steel Casting?
Steel casting refers to the process of shaping molten steel into parts and components by pouring it into molds. It’s one of the oldest and most reliable techniques for creating durable parts.
Steel casting works by melting steel and pouring it into a pre-shaped mold. The mold is left to cool and harden, forming a solid piece.
Steel casting is highly regarded for its ability to create complex shapes and parts. It’s an ideal solution for industries requiring high precision and strength. By understanding the steel casting process, you can see its critical role in manufacturing.
Types of Steel Casting
Steel casting comes in various forms, including carbon steel, alloy steel, and stainless steel. Each type has its advantages and is suitable for different applications.
Steel Type | Properties | Common Uses |
---|---|---|
Carbon Steel | High strength, low cost | Automotive, heavy machinery |
Alloy Steel | Enhanced durability | Aerospace, defense |
Stainless Steel | Corrosion resistance | Food processing, medical |
Steel Casting Process
The process involves several steps, including melting, pouring, cooling, and finishing. Let’s break down these steps to understand what each stage entails.
Stage | Description |
---|---|
Melting | Steel is heated to a liquid state |
Pouring | Liquid steel is poured into molds |
Cooling | Steel solidifies within the mold |
Finishing | The cast part is cleaned and processed |
2. How Does Steel Casting Work?
Steel casting involves multiple stages, but the key components are melting the steel, pouring it into a mold, and allowing it to cool and solidify. This process can be done with a variety of molds depending on the complexity of the part.
The steel casting process includes melting steel, pouring it into molds, cooling it, and finishing the cast part.
Understanding how steel casting works can help you recognize its benefits for industries requiring high-quality components. It’s the perfect method when you need strong, durable, and complex parts.
Different Methods of Steel Casting
There are various casting methods, such as sand casting, die casting, and investment casting. Each method has its specific advantages depending on the desired result.
Casting Method | Description | Common Uses |
---|---|---|
Sand Casting | Uses sand molds to form parts | Automotive, machine parts |
Die Casting | Uses metal molds for precision | High-volume production |
Investment Casting | Uses wax molds for complex shapes | Aerospace, intricate parts |
Choosing the Right Steel Casting Method
Not all steel casting methods are the same. Depending on your production needs, selecting the right method can improve efficiency and reduce costs.
3. Why is Steel Casting Important?
Steel casting is a preferred method for many industries due to its reliability and versatility. Its ability to create parts that withstand extreme conditions makes it indispensable in sectors like automotive, aerospace, and construction.
Steel casting is vital because it produces durable, high-strength parts that other manufacturing methods may struggle to create.
The importance of steel casting lies in its ability to create strong and precise parts. Let’s explore why it stands out among other manufacturing methods.
Benefits of Steel Casting
Steel casting offers several benefits, including cost efficiency, versatility, and the ability to produce complex shapes.
Benefit | Description |
---|---|
Durability | Steel cast parts are strong and long-lasting |
Cost Efficiency | Suitable for large-scale production at lower costs |
Complex Shapes | Steel casting can create intricate shapes that are otherwise difficult to manufacture |
Industries that Rely on Steel Casting
Many industries depend on steel casting for producing parts that must withstand extreme pressure, temperature, and stress. Automotive, aerospace, and heavy machinery are just a few of the sectors that benefit.
4. What Are the Types of Steel Used in Casting?
When choosing steel for casting, it’s important to understand the differences between carbon steel, alloy steel, and stainless steel. Each type serves different needs based on its composition and properties.
The primary steel types for casting include carbon steel, alloy steel, and stainless steel, each with distinct properties suited for specific applications.
Each type of steel has unique benefits that make it suitable for different industrial applications. For example, carbon steel is cost-effective and used for parts requiring high strength, while stainless steel offers corrosion resistance for food and medical equipment.
Comparing Steel Types for Casting
To choose the right steel type for your casting needs, it’s important to compare their properties and applications.
Steel Type | Strength | Corrosion Resistance | Applications |
---|---|---|---|
Carbon Steel | High strength | Low | Heavy machinery, automotive |
Alloy Steel | Very high strength | Medium | Aerospace, military |
Stainless Steel | Moderate strength | High | Medical, food processing |
5. How is Steel Casting Different from Other Types of Casting?
Steel casting offers several advantages over other casting methods, especially when it comes to strength, precision, and versatility. Understanding how it compares to alternatives can help you choose the right method for your needs.
Steel casting is different from other casting methods due to its ability to produce high-strength, durable parts that can withstand extreme conditions.
While methods like iron or aluminum casting have their own benefits, steel casting stands out in industries where performance under high pressure and temperature is essential. Let’s examine how steel casting compares to other types of casting.
Steel Casting vs. Iron Casting
Iron casting is commonly used for parts that don’t require as much strength as steel cast parts. Here’s how they compare:
Feature | Steel Casting | Iron Casting |
---|---|---|
Strength | Higher | Lower |
Durability | Very durable | Less durable |
Application | High-stress environments | General-purpose use |
Steel Casting vs. Aluminum Casting
Aluminum is lighter but less durable than steel. It is often used in parts where weight reduction is important but doesn’t have the strength that steel parts do.
Feature | Steel Casting | Aluminum Casting |
---|---|---|
Strength | Very high | Moderate |
Weight | Heavier | Lighter |
Common Uses | Automotive, aerospace | Automotive, consumer goods |
6. What Are the Key Benefits of Steel Casting?
Steel casting brings many benefits to manufacturers, such as producing durable parts with complex shapes. The cost-effectiveness of steel casting also plays a big role in its widespread use.
The key benefits of steel casting include strength, precision, and cost-effectiveness.
This method is especially beneficial for industries requiring high-precision parts that can perform under extreme conditions, like aerospace and automotive. Let’s break down the benefits further.
Durability and Strength
Steel casting offers outstanding durability and strength, making it ideal for heavy machinery and automotive components.
Benefit | Description |
---|---|
Strength | Can withstand high pressure and stress |
Durability | Long-lasting performance in harsh environments |
Cost Efficiency
Steel casting can be cost-effective when producing large quantities of parts. The ability to create complex parts without additional machining costs makes it a more economical choice.
Factor | Steel Casting Advantage |
---|---|
Production Volume | Lower cost for high-volume production |
Tooling Costs | Reduced need for expensive tooling |
7. What Are Common Applications of Steel Casting?
Steel casting is commonly used in a variety of industries, from automotive to construction. The ability to create strong, durable parts makes it versatile across sectors.
Steel casting is used in industries that require high-performance components.
Let’s take a look at the specific applications of steel casting in different industries.
Automotive Industry
In the automotive industry, steel castings are used for engine blocks, transmission parts, and other components that require high strength and durability.
Application | Part | Purpose |
---|---|---|
Engine Blocks | Cast steel engine blocks | High strength and temperature resistance |
Transmission Parts | Steel gears and shafts | Durability under high-stress loads |
Aerospace Industry
Steel castings in aerospace are used for landing gear, turbines, and other parts that need to withstand extreme pressure and temperature.
Application | Part | Purpose |
---|---|---|
Turbines | Cast steel turbine blades | Resistance to extreme temperatures and pressures |
Landing Gear | Steel structural components | Durability under high-stress conditions |
8. How Are Steel Castings Tested for Quality?
To ensure steel castings meet the necessary standards, they undergo rigorous testing. These tests help identify any defects and ensure the parts will perform as expected.
Testing steel castings is crucial to avoid defects and ensure reliability.
The testing process includes several methods, such as visual inspections, dimensional checks, and non-destructive testing. Let’s explore these methods.
Visual Inspections and Dimensional Checks
Visual inspections and dimensional checks are basic but important steps in ensuring the part meets specifications. These checks can identify surface defects or dimensional issues that could affect the part’s performance.
Test Type | Purpose | Method |
---|---|---|
Visual Inspection | Detect surface defects | Manual or automated visual checks |
Dimensional Check | Ensure correct dimensions | Measured with calipers or gauges |
Non-Destructive Testing (NDT)
Non-destructive testing ensures that the internal structure of the steel casting is free from cracks, voids, or other defects. Methods include ultrasonic testing, X-ray, and magnetic particle inspection.
Test Type | Purpose | Method |
---|---|---|
Ultrasonic Testing | Detect internal cracks and voids | Sound waves to measure thickness |
X-ray Inspection | Check for internal flaws | X-ray imaging |
9. What Are the Challenges in Steel Casting?
While steel casting offers many benefits, there are also challenges to consider. High production costs, quality control issues, and environmental concerns can be obstacles.
Steel casting comes with challenges that must be addressed to ensure quality and efficiency.
These challenges can affect both the cost-effectiveness and reliability of the steel casting process. Let’s discuss these issues in more detail.
High Production Costs
Steel casting requires high energy consumption for melting the steel and maintaining the casting process. This can lead to higher operational costs.
Challenge | Impact | Solution |
---|---|---|
High Costs | Increased production costs | Optimize process, use recycled steel |
Energy Consumption | Higher electricity use | Invest in energy-efficient equipment |
Environmental Concerns
Steel casting produces emissions, including CO2, and consumes significant energy. Manufacturers must focus on reducing the environmental impact of steel casting.
Environmental Issue | Impact | Solution |
---|---|---|
CO2 Emissions | Contribution to climate change | Use renewable energy sources |
Energy Consumption | High demand for electricity | Optimize energy usage |
10. How is Steel Casting Evolving?
Steel casting technology is evolving rapidly. Innovations in casting methods, automation, and sustainability are making the process more efficient and environmentally friendly.
Steel casting continues to evolve with new technologies and methods improving efficiency and sustainability.
Advancements in materials and processes are helping the industry create even stronger, more durable components. Let’s take a look at some of the latest developments.
Innovations in Casting Techniques
New technologies, such as 3D printing of molds, have begun to change how steel casting is performed. These innovations enable more complex shapes and faster production times.
Innovation | Description | Benefits |
---|---|---|
3D-Printed Molds | Creating molds with 3D printing technology | Faster production, intricate shapes |
Automation | Robotic arms and AI-driven processes | Increased precision, reduced labor costs |
Sustainable Casting Practices
To address environmental concerns, manufacturers are adopting sustainable practices, such as using recycled steel and reducing energy consumption.
Practice | Description | Benefits |
---|---|---|
Recycled Steel | Using scrap steel in the casting process | Reduces raw material costs and waste |
Energy Efficiency | Optimizing energy usage in casting operations | Lowers environmental impact |
11. What Are the Steps Involved in Steel Casting?
The steel casting process consists of several key steps that must be followed to produce high-quality parts. These steps include melting, pouring, cooling, and finishing.
The steel casting process involves multiple steps to ensure high-quality parts.
Each step is critical to achieving the final product, and any mistakes in these stages can lead to defects. Let’s break down the process further.
Melting and Pouring
The first step in steel casting is melting the steel and pouring it into the mold. This requires precise temperature control to avoid overheating or underheating the steel.
Step | Description |
---|---|
Melting | Steel is heated to the required temperature |
Pouring | Molten steel is poured into molds |
Cooling and Finishing
Once the steel is poured into the mold, it’s allowed to cool and solidify. The cooling process must be carefully controlled to avoid defects. After cooling, the part undergoes finishing processes to remove any excess material.
Step | Description |
---|---|
Cooling | Steel solidifies in the mold |
Finishing | Removing excess material and polishing the surface |
12. What is the Steel Casting Process Flow?
Understanding the flow of the steel casting process is key to ensuring efficient production. Each step plays a role in creating high-quality, reliable components.
The steel casting process flow ensures each stage is completed correctly to achieve the desired result.
The process flow involves melting, pouring, cooling, finishing, and quality control. Here’s a more detailed explanation of each stage.
Stage | Action |
---|---|
Melting | Steel is heated and liquefied |
Pouring | Molten steel is poured into molds |
Cooling | Steel solidifies in the mold |
Finishing | The casting is cleaned and shaped |
13. What Are the Different Steel Casting Methods?
There are various methods for steel casting, each offering different benefits depending on the complexity of the parts and the intended application.
Steel casting methods vary in terms of mold material, precision, and cost.
Each casting method has its strengths. For example, sand casting is more cost-effective but less precise than investment casting. Let’s explore the different methods used in steel casting.
Sand Casting
In sand casting, molds are made from sand, which is a cost-effective option for producing large quantities of parts.
Method | Description | Advantages |
---|---|---|
Sand Casting | Uses sand to create the mold | Cost-effective, versatile |
Investment Casting
Investment casting uses a wax pattern covered with a ceramic shell to create highly precise components. It is ideal for parts requiring complex geometries.
Method | Description | Advantages |
---|---|---|
Investment Casting | Uses wax patterns and ceramic shells | High precision, intricate designs |
14. What Are the Advantages of Steel Casting for Manufacturers?
Steel casting offers many advantages for manufacturers, especially those in industries requiring durable, high-performance components.
Steel casting offers cost-effective production and high-quality results for manufacturers.
With its ability to produce durable and complex parts, steel casting is a valuable method for companies across various industries. Let’s look at some of the key advantages.
Cost-Effectiveness for Mass Production
Steel casting allows manufacturers to produce large quantities of parts at a lower cost than many other manufacturing methods.
Advantage | Description |
---|---|
High Efficiency | Suitable for large-scale production |
Lower Costs | Reduced need for additional machining |
High Precision and Complex Geometries
Steel casting can create parts with intricate designs, making it ideal for industries that require high precision.
Advantage | Description |
---|---|
Precision | Capable of producing complex geometries |
Performance | Excellent performance under extreme conditions |
15. How Do I Choose a Steel Casting Supplier?
Choosing the right supplier is crucial for ensuring quality and timely delivery. It’s important to assess their reliability, production capabilities, and customer service.
When selecting a steel casting supplier, consider factors like quality, technology, and reliability.
Here’s what you should look for when choosing the best supplier for your steel casting needs.
Key Considerations for Selecting a Supplier
To choose the best supplier, ensure they offer high-quality products, timely delivery, and excellent customer support.
Consideration | Description |
---|---|
Quality Assurance | Look for suppliers with proven quality control |
Technology | Choose suppliers that use advanced technology |
Reliability | Ensure they can meet deadlines and deliver consistently |
Conclusion
Steel casting is a vital manufacturing process that offers durability, precision, and cost-efficiency. By understanding the methods, benefits, and challenges, you can make better decisions for your business and choose the right supplier to meet your needs.
FAQ Section
Q1: What is steel casting?
Steel casting is the process of pouring molten steel into molds to create components with high strength and precision.
Q2: How does steel casting work?
Steel casting involves melting steel, pouring it into molds, allowing it to solidify, and finishing the part for use.
Q3: What types of steel are commonly used in casting?
The most common types of steel used for casting include carbon steel, alloy steel, and stainless steel, each serving different industrial needs.
Q4: Why is steel casting preferred for certain industries?
Steel casting is preferred for its durability, cost efficiency, and ability to create complex shapes that other methods cannot easily produce.
Q5: How can I ensure the quality of steel castings?
To ensure quality, steel castings should undergo various testing methods, including non-destructive testing, to detect defects and ensure the parts meet industry standards.