Introduction
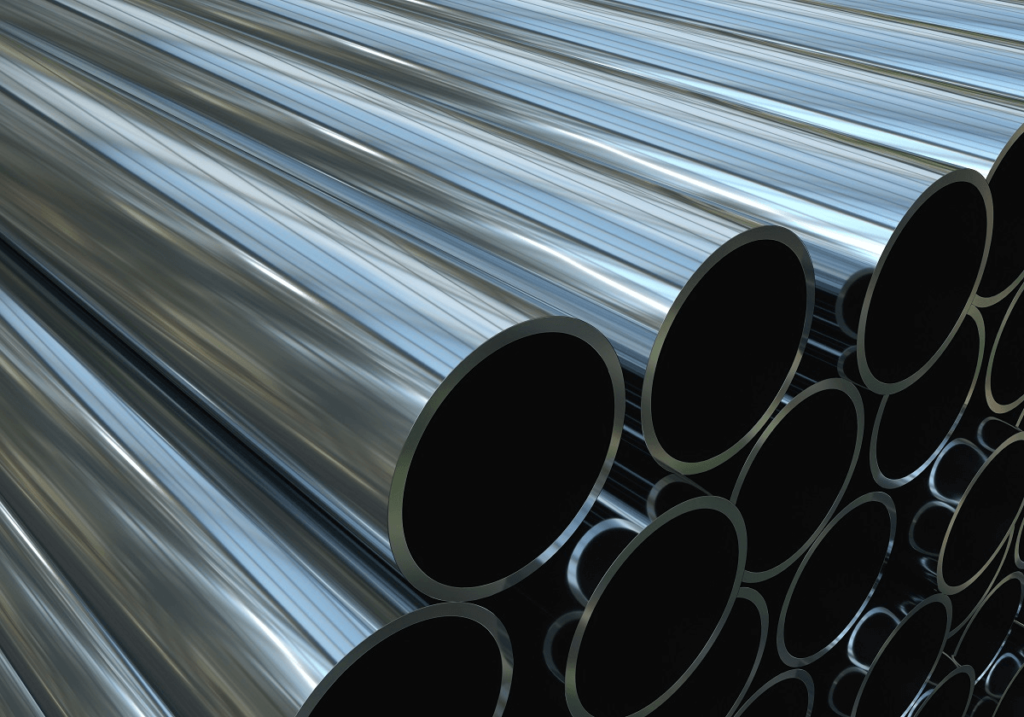
Carbon steel is one of the most widely used materials in various industries today, and for good reason. Its versatility, durability, and cost-effectiveness make it a preferred choice for a wide range of applications, from construction to manufacturing and beyond. Whether you’re involved in industrial production, engineering, or procurement, understanding the different types of carbon steel is crucial. This knowledge not only helps you choose the right material for your specific needs but also ensures the longevity and performance of the components you’re working with, including carbon steel casting parts.
In this comprehensive guide, we will explore the four main types of carbon steel, each with unique properties and applications. By the end of this article, you will have a solid understanding of these categories and be better equipped to select the appropriate carbon steel type for your project. We will cover everything from the basic definition of carbon steel to the key characteristics, advantages, and common uses of each type. Additionally, we’ll discuss how these steels compare to each other, the challenges associated with their use, and what the future holds for carbon steel in various industries.
What You Will Learn
In this article, you will gain:
- A fundamental understanding of carbon steel and its composition.
- Insight into the four classifications of carbon steel: Low Carbon Steel, Medium Carbon Steel, High Carbon Steel, and Ultra-High Carbon Steel.
- Detailed knowledge of the properties, benefits, and common applications of each type.
- Guidance on choosing the right carbon steel type for specific applications.
- Awareness of the potential challenges and limitations of using carbon steel.
- A glimpse into the future trends and innovations in the field of carbon steel, particularly in the realm of carbon steel casting parts.
So, let’s dive into the world of carbon steel, starting with the basics.
Understanding Carbon Steel: A Basic Overview
Definition of Carbon Steel
Carbon steel is a type of steel where the main interstitial alloying constituent is carbon. In other words, it is an iron-carbon alloy that contains up to 2.1% carbon by weight. The carbon content in steel plays a pivotal role in determining its properties, such as hardness, strength, and ductility. The higher the carbon content, the more durable and stronger the steel becomes; however, this also reduces its ductility.
Carbon steel is differentiated from other types of steel by its lack of other significant alloying elements. While trace amounts of elements like manganese, silicon, and copper may be present, their proportions are relatively low compared to the primary constituent, carbon. This simplicity in composition gives carbon steel its distinctive characteristics and makes it easier to manipulate during the manufacturing process.
Why Carbon Steel is Popular
The popularity of carbon steel stems from its balance of strength, durability, and affordability. It is a cost-effective material that offers a wide range of mechanical properties suitable for various applications. Here are a few reasons why carbon steel is so widely used:
- Strength and Durability: Carbon steel is known for its high tensile strength and durability, making it ideal for structures and components that require robustness and longevity.
- Versatility: From construction materials to automotive components, carbon steel can be adapted for numerous uses. Its ability to be heat-treated allows manufacturers to alter its properties to suit specific applications.
- Cost-Effectiveness: Compared to other types of steel, carbon steel is relatively inexpensive to produce and process, making it an attractive option for large-scale manufacturing and industrial projects.
- Wide Availability: The widespread production of carbon steel means it is readily available in various forms, such as bars, sheets, and carbon steel casting parts, ensuring that industries can easily source the materials they need.
Given these advantages, it’s clear why carbon steel is a staple in industries like construction, automotive, and manufacturing. However, the specific type of carbon steel used can vary greatly depending on the application, which brings us to the next point: the different types of carbon steel.
Factors That Influence Carbon Steel Properties
The properties of carbon steel are not static; they can be influenced by several factors, including:
- Carbon Content: The amount of carbon present in the steel directly impacts its hardness, strength, and ductility. As the carbon content increases, the steel becomes harder and stronger, but less ductile and more difficult to weld.
- Heat Treatment: Heat treatment processes such as annealing, quenching, and tempering can significantly alter the microstructure of carbon steel, thereby changing its mechanical properties. For example, quenching can increase hardness and strength, while annealing can improve ductility.
- Alloying Elements: While carbon steel primarily consists of iron and carbon, the presence of other alloying elements like manganese, silicon, and copper, even in small quantities, can enhance specific properties such as strength, toughness, and corrosion resistance.
- Manufacturing Process: The methods used in manufacturing carbon steel, including casting, rolling, and forging, also play a crucial role in determining its final properties. For instance, carbon steel casting parts may have different characteristics than those that are rolled or forged due to variations in cooling rates and internal stresses.
Understanding these factors is essential for selecting the right type of carbon steel for a particular application. It also highlights why different types of carbon steel exist, each tailored to meet specific performance requirements.
In the next section, we will delve into the four main types of carbon steel, exploring their unique characteristics and common applications.
The Four Types of Carbon Steel
Carbon steel is categorized into four distinct types based on its carbon content: Low Carbon Steel (Mild Steel), Medium Carbon Steel, High Carbon Steel, and Ultra-High Carbon Steel. Each of these types has specific properties and applications, making them suitable for different industrial uses. Below, we’ll explore each type in detail, focusing on their composition, key characteristics, advantages, and typical applications.
Low Carbon Steel (Mild Steel)
Definition and Carbon Content
Low Carbon Steel, often referred to as Mild Steel, is the most common form of carbon steel. It contains the least amount of carbon, typically less than 0.25% by weight. This low carbon content is responsible for the steel’s soft and malleable nature, which makes it easy to work with in various manufacturing processes, including welding and machining.
Key Characteristics
The primary characteristics of Low Carbon Steel include:
- Malleability and Ductility: Due to its low carbon content, Mild Steel is highly malleable, meaning it can be easily shaped and formed without breaking. It is also ductile, allowing it to be drawn into wires or thin sheets.
- Ease of Welding and Machining: Low Carbon Steel can be welded with minimal risk of cracking, and it machines easily due to its softness. This makes it ideal for manufacturing processes that require extensive shaping and joining of metal parts.
- Lower Tensile Strength: While it is relatively strong, Low Carbon Steel has lower tensile strength compared to steels with higher carbon content. This means it is less suited for applications where high strength is crucial.
- Surface Finish: Low Carbon Steel typically has a smooth surface finish, which is advantageous for aesthetic applications and those requiring a uniform appearance.
Common Applications
The versatility of Low Carbon Steel makes it suitable for a wide range of applications, including:
- Structural Components: Mild Steel is often used in construction for making structural steel components such as beams, columns, and frames due to its excellent balance of strength and flexibility.
- Automotive Body Panels: In the automotive industry, Low Carbon Steel is commonly used to manufacture body panels, chassis, and other parts that require forming into complex shapes without compromising safety.
- Pipes and Tubes: The ease of welding and machining makes Mild Steel a popular choice for pipes and tubes used in plumbing, gas lines, and other fluid transport systems.
- General Fabrication: Low Carbon Steel is extensively used in general metal fabrication for products like brackets, enclosures, and housings that require easy shaping and assembly.
Advantages and Disadvantages
Advantages:
- Cost-Effective: Low Carbon Steel is inexpensive to produce and readily available, making it a cost-effective option for many industries.
- Ease of Fabrication: Its malleability and weldability allow for easy fabrication into various forms and structures.
- Corrosion Resistance: With appropriate surface treatments, Mild Steel can offer decent corrosion resistance for certain applications.
Disadvantages:
- Lower Strength: The low carbon content means Mild Steel is not as strong as other types of carbon steel, limiting its use in high-strength applications.
- Susceptibility to Rust: Without protective coatings, Low Carbon Steel can rust easily when exposed to moisture.
Medium Carbon Steel
Definition and Carbon Content
Medium Carbon Steel contains a higher carbon content than Mild Steel, typically ranging from 0.25% to 0.60%. This increased carbon content enhances the steel’s strength and hardness while still maintaining a fair degree of ductility and toughness.
Key Characteristics
Medium Carbon Steel is characterized by:
- Balanced Strength and Ductility: Medium Carbon Steel strikes a balance between strength and ductility, offering greater tensile strength than Low Carbon Steel while still being workable enough for many manufacturing processes.
- Improved Hardness and Wear Resistance: The higher carbon content increases the steel’s hardness and wear resistance, making it suitable for applications that require durability.
- Moderate Ease of Machining and Forming: While not as easy to machine or form as Low Carbon Steel, Medium Carbon Steel can still be processed relatively easily with the right techniques, especially after heat treatment.
- Heat Treatment Responsiveness: Medium Carbon Steel responds well to heat treatment processes like quenching and tempering, which can further enhance its mechanical properties, particularly its hardness and strength.
Common Applications
Medium Carbon Steel is widely used in applications that require a good balance of strength and toughness, such as:
- Railway Tracks: Medium Carbon Steel’s wear resistance and strength make it ideal for manufacturing railway tracks, which must withstand constant mechanical stress and friction.
- Gears and Machinery Parts: The material’s hardness and ability to retain a sharp edge after machining make it suitable for gears, crankshafts, and other machinery parts that need to resist wear and tear.
- Structural Steel in Buildings: In the construction industry, Medium Carbon Steel is used in making structural steel that requires more strength than Low Carbon Steel but does not demand the highest strength available.
- Automotive Components: Components like axles, shafts, and connecting rods in vehicles often utilize Medium Carbon Steel for its superior strength and toughness.
Advantages and Disadvantages
Advantages:
- Increased Strength: Medium Carbon Steel offers a significant improvement in strength and hardness compared to Low Carbon Steel, making it more suitable for heavy-duty applications.
- Good Wear Resistance: The higher carbon content enhances the steel’s ability to resist wear, extending the life of parts made from it.
- Heat Treatable: The material can be further strengthened through heat treatment, allowing for greater versatility in its use.
Disadvantages:
- Reduced Ductility: The increased carbon content results in reduced ductility, making the steel less suitable for applications requiring significant deformation.
- Higher Cost: Medium Carbon Steel is generally more expensive than Low Carbon Steel due to its enhanced properties and the additional processing required.
High Carbon Steel
Definition and Carbon Content
High Carbon Steel contains between 0.60% and 1.0% carbon, making it much harder and stronger than both Low and Medium Carbon Steels. This type of steel is known for its high hardness and ability to retain sharp edges, but it also tends to be more brittle, with lower ductility.
Key Characteristics
High Carbon Steel is defined by several key characteristics:
- High Hardness and Strength: With its high carbon content, High Carbon Steel is extremely hard and strong, making it ideal for applications where resistance to wear and impact is crucial.
- Excellent Wear Resistance: This type of steel is highly resistant to wear, which is why it is commonly used in the production of cutting tools and other items that endure repeated friction.
- Lower Ductility: The increased hardness comes at the expense of ductility. High Carbon Steel is more brittle and can crack or break if subjected to excessive bending or deformation.
- Difficult to Weld and Machine: The hardness of High Carbon Steel makes it more challenging to weld and machine compared to Low and Medium Carbon Steels. Special techniques and tools are often required for these processes.
Common Applications
The high hardness and wear resistance of High Carbon Steel make it suitable for a variety of specialized applications, including:
- Cutting Tools: High Carbon Steel is commonly used to manufacture knives, blades, and other cutting tools that need to maintain a sharp edge even after prolonged use.
- Springs: The material’s ability to return to its original shape after deformation makes it ideal for springs used in mechanical systems, where elasticity is crucial.
- High-Strength Wires: High Carbon Steel is used to produce high-strength wires that require excellent tensile strength and durability, such as those used in suspension bridges or piano strings.
- Industrial Machinery and Tools: Components that need to withstand significant wear, such as drill bits, saw blades, and punching tools, are often made from High Carbon Steel.
Advantages and Disadvantages
Advantages:
- Superior Hardness: High Carbon Steel offers exceptional hardness and wear resistance, making it ideal for cutting tools and applications requiring long-lasting sharpness.
- High Strength: The material’s high tensile strength makes it suitable for demanding applications where structural integrity is critical.
Disadvantages:
- Brittleness: The increased hardness results in reduced ductility, making High Carbon Steel more brittle and prone to cracking under stress.
- Difficulty in Processing: High Carbon Steel is more difficult to weld and machine, often requiring specialized tools and techniques.
Ultra-High Carbon Steel
Definition and Carbon Content
Ultra-High Carbon Steel is the hardest and strongest of all carbon steels, with a carbon content ranging from 1.0% to 2.0%. This type of steel is extremely hard and brittle, with limited ductility, making it suitable for specialized applications that demand the utmost strength and wear resistance.
Key Characteristics
Ultra-High Carbon Steel possesses several defining characteristics:
- Maximum Hardness and Strength: Ultra-High Carbon Steel is the pinnacle of strength and hardness in carbon steels. It can withstand extreme mechanical stress without deforming.
- Exceptional Wear Resistance: The high carbon content provides unparalleled wear resistance, making this steel ideal for applications involving repetitive motion and friction.
- Very Brittle: While Ultra-High Carbon Steel is incredibly strong, it is also very brittle. This brittleness limits its use to applications where toughness and flexibility are not required.
- Limited Ductility: The material’s brittleness results in very low ductility, meaning it cannot be shaped or bent without breaking.
Common Applications
Due to its extreme properties, Ultra-High Carbon Steel is used in specialized applications, including:
- Specialized Cutting Tools: Ultra-High Carbon Steel is used to produce cutting tools like chisels, punches, and other industrial tools that require extreme hardness and sharpness.
- High-Strength Industrial Components: The material is used in components that must endure significant stress and wear, such as industrial dies and forming tools.
- Knives and Blades: Knives and blades made from Ultra-High Carbon Steel are exceptionally sharp and maintain their edge for a long time, though they can be more challenging to sharpen due to the material’s hardness.
- Martensitic Steels: Ultra-High Carbon Steel is used to create martensitic steels, which are hard, wear-resistant steels often used in applications like bearings, knives, and various types of cutting tools.
Advantages and Disadvantages
Advantages:
- Unmatched Hardness and Strength: Ultra-High Carbon Steel offers the highest hardness and strength among carbon steels, making it ideal for applications requiring maximum wear resistance.
- Extreme Wear Resistance: The material’s exceptional hardness provides superior wear resistance, extending the life of components made from it.
Disadvantages:
- Extreme Brittleness: The steel’s brittleness severely limits its ductility, making it prone to cracking or breaking under stress.
- Difficult to Work With: Ultra-High Carbon Steel is challenging to process, requiring specialized tools and methods for cutting, shaping, and welding.
Comparing the Four Types of Carbon Steel
Understanding the differences between the four types of carbon steel is essential for selecting the right material for your specific application. In this section, we will compare these types based on their mechanical properties, workability, and cost.
Mechanical Properties Comparison
The mechanical properties of carbon steel vary significantly depending on the carbon content. Here’s a comparison of the tensile strength, hardness, ductility, and toughness of the four types:
- Low Carbon Steel: Offers good ductility and toughness but has lower tensile strength and hardness. It is suitable for applications that do not require high strength but benefit from easy fabrication.
- Medium Carbon Steel: Balances strength and ductility, providing better tensile strength and hardness than Low Carbon Steel while retaining moderate ductility and toughness. This makes it ideal for structural applications and machinery components.
- High Carbon Steel: Exhibits high tensile strength and hardness but at the cost of reduced ductility. It is best used in applications requiring wear resistance and strength, such as cutting tools and high-strength wires.
- Ultra-High Carbon Steel: Offers maximum hardness and strength but is extremely brittle with very low ductility. It is suitable for specialized applications where toughness is less critical, and wear resistance is paramount.
Workability and Machinability
The workability and machinability of carbon steel decrease as the carbon content increases:
- Low Carbon Steel: Highly workable, easy to weld, and machine, making it ideal for general fabrication and construction.
- Medium Carbon Steel: Still relatively easy to work with but requires more effort than Low Carbon Steel. Heat treatment can improve its machinability.
- High Carbon Steel: More challenging to machine and weld due to its hardness. Special tools and techniques are often necessary.
- Ultra-High Carbon Steel: Extremely difficult to work with due to its brittleness and hardness. Requires specialized processing methods and is generally used only when absolutely necessary.
Cost Analysis
The cost of carbon steel generally increases with carbon content due to the additional processing required to achieve higher strength and hardness:
- Low Carbon Steel: The least expensive, making it the most cost-effective option for many applications.
- Medium Carbon Steel: More expensive than Low Carbon Steel but offers better performance for applications requiring more strength and wear resistance.
- High Carbon Steel: Costs more due to its enhanced properties and the specialized tools needed for machining and welding.
- Ultra-High Carbon Steel: The most expensive of the four, used only in applications where its extreme properties are indispensable.
Choosing the Right Type of Carbon Steel for Your Application
Selecting the right type of carbon steel is critical to the success of any project. The choice depends on several factors, including the required strength, ductility, and cost constraints. Here’s a guide to help you make an informed decision.
Key Considerations
When choosing carbon steel, consider the following factors:
- Application Requirements: Determine the mechanical properties needed for your application. For example, if you need high strength and wear resistance, High Carbon Steel might be the best choice. For applications requiring easy fabrication, Low Carbon Steel may be more suitable.
- Processing Methods: Consider how the steel will be processed. If the steel needs to be welded, formed, or machined extensively, Low or Medium Carbon Steel might be more appropriate due to their better workability.
- Budget Constraints: The cost of the steel is also a crucial factor. If your budget is tight, Low Carbon Steel offers a cost-effective solution for many applications. However, if performance is more critical than cost, investing in High or Ultra-High Carbon Steel might be worthwhile.
Case Studies/Examples
To further illustrate the importance of selecting the right type of carbon steel, let’s look at a couple of examples:
- Construction Example: In building a structure, Low Carbon Steel might be used for beams and columns due to its ease of fabrication and sufficient strength for most applications. However, for components that require more strength, such as a bridge, Medium Carbon Steel would be more appropriate.
- Tool Manufacturing Example: When manufacturing cutting tools, High Carbon Steel is often the material of choice because of its hardness and ability to maintain a sharp edge. For specialized industrial tools that require even greater wear resistance, Ultra-High Carbon Steel would be selected despite its brittleness.
Decision-Making Flowchart
Here’s a simple flowchart to help you decide which type of carbon steel might be best for your needs:
- Do you need maximum strength and wear resistance?
- Yes: Consider High or Ultra-High Carbon Steel.
- No: Proceed to the next question.
- Is ease of fabrication important?
- Yes: Consider Low or Medium Carbon Steel.
- No: Proceed to the next question.
- Do you have a tight budget?
- Yes: Low Carbon Steel is likely your best option.
- No: Consider the other factors before making your final decision.
This flowchart provides a basic framework, but consulting with a materials expert is always recommended for complex projects.
Challenges and Limitations of Using Carbon Steel
While carbon steel is incredibly versatile and widely used, it is not without its challenges and limitations. Understanding these issues can help you mitigate potential problems in your projects.
Potential Drawbacks
Some common drawbacks of carbon steel include:
- Brittleness in High and Ultra-High Carbon Steels: As the carbon content increases, the steel becomes harder but also more brittle. This can lead to cracking or breaking under stress, particularly in applications requiring flexibility.
- Corrosion Resistance Issues: Carbon steel is susceptible to rust and corrosion, especially in environments with high moisture or corrosive chemicals. This can be mitigated with coatings or by using alloying elements like chromium, but it remains a concern.
- Heat Treatment Challenges: While heat treatment can enhance the properties of carbon steel, it also requires precise control to avoid issues like warping or excessive brittleness. Improper heat treatment can significantly affect the performance of the steel.
Mitigation Strategies
To address these challenges, consider the following strategies:
- Heat Treatment Techniques: Properly executed heat treatment can enhance the performance of carbon steel without introducing brittleness or other issues. Techniques like tempering can help balance hardness and ductility.
- Surface Treatments for Corrosion Resistance: Applying coatings, such as galvanization or painting, can protect carbon steel from corrosion. In environments where corrosion is a significant concern, consider using stainless steel or applying a more robust coating.
- Alloying to Improve Specific Properties: Adding elements like manganese, silicon, or chromium can improve the steel’s properties, such as toughness, hardness, and corrosion resistance. This can help tailor the material to specific applications.
By understanding these challenges and implementing appropriate mitigation strategies, you can maximize the benefits of carbon steel while minimizing its limitations.
Future Trends in Carbon Steel
As industries evolve, so too does the technology and innovation surrounding carbon steel. Understanding future trends can help you stay ahead of the curve and make informed decisions about material selection and manufacturing processes.
Innovations in Carbon Steel Alloys
One of the most significant trends in the carbon steel industry is the development of new alloys. By experimenting with different alloying elements, researchers are finding ways to enhance the properties of carbon steel, making it more versatile and durable. For example:
- High-Strength Low-Alloy (HSLA) Steels: These steels offer higher strength without the brittleness associated with traditional High Carbon Steels. They achieve this by adding small amounts of alloying elements like vanadium, niobium, or titanium.
- Advanced Heat Treatment Processes: Innovations in heat treatment are allowing for more precise control over the mechanical properties of carbon steel. Techniques like thermomechanical processing are helping to produce steels with superior toughness and strength.
- Nano-Structured Steels: Research into nano-structured steels is exploring how manipulating the microstructure of carbon steel on a nanoscale can lead to improvements in strength, ductility, and resistance to wear.
These innovations are opening up new possibilities for carbon steel, making it suitable for even more demanding applications.
Sustainability and Carbon Steel
As sustainability becomes a growing concern across industries, carbon steel is also evolving to meet these demands:
- Recycling and Reusability: Carbon steel is highly recyclable, with over 70% of all steel being recycled worldwide. This not only conserves natural resources but also reduces the carbon footprint of steel production.
- Energy-Efficient Production: Advances in steel production technology are focusing on reducing energy consumption and emissions. Electric arc furnaces, for example, use significantly less energy compared to traditional blast furnaces and can melt scrap steel for recycling.
- Lightweighting: In industries like automotive and aerospace, there is a growing trend towards lightweighting, or reducing the weight of materials to improve fuel efficiency. Carbon steel alloys are being developed to offer high strength at lower weights, contributing to more sustainable designs.
The Role of Carbon Steel Casting Parts in the Future
With these trends in mind, the role of carbon steel casting parts is likely to grow even more significant. As industries seek materials that offer a balance of strength, durability, and sustainability, carbon steel castings will continue to be a go-to solution. Innovations in alloy development, heat treatment, and recycling will only enhance the performance and environmental friendliness of these critical components.
Conclusion
Summary of Key Points
Carbon steel is a versatile and essential material in many industries, with four main types: Low Carbon Steel, Medium Carbon Steel, High Carbon Steel, and Ultra-High Carbon Steel. Each type offers unique properties, making them suitable for different applications. Understanding the characteristics and limitations of each type is crucial for selecting the right material for your project.
Final Thoughts
Whether you’re involved in construction, automotive manufacturing, or any other industry that relies on strong, durable materials, carbon steel is likely to play a key role in your work. By choosing the right type of carbon steel and applying the appropriate processing techniques, you can ensure that your components—whether they’re carbon steel casting parts or structural elements—perform to the highest standards.
Call to Action
If you need expert advice on selecting the right type of carbon steel for your application or are looking for high-quality precision castings tailored to your specific needs, don’t hesitate to contact Precisionvast. Our team of experts is here to help you navigate the complexities of material selection and ensure the success of your projects.
Explore our other resources on material science, and feel free to reach out to us for personalized assistance. Together, we can find the best solutions to meet your manufacturing challenges and drive your business forward.