High-pressure aluminum die casting is a widely used manufacturing process that allows manufacturers to create high-precision, durable metal parts. This process involves injecting molten aluminum into a die under high pressure, which results in highly detailed and dimensionally accurate parts. But why is it so popular in industries like automotive, aerospace, and electronics? The benefits and drawbacks of high-pressure aluminum die casting are essential for understanding its value in manufacturing, and this article will break down the critical aspects of this process.
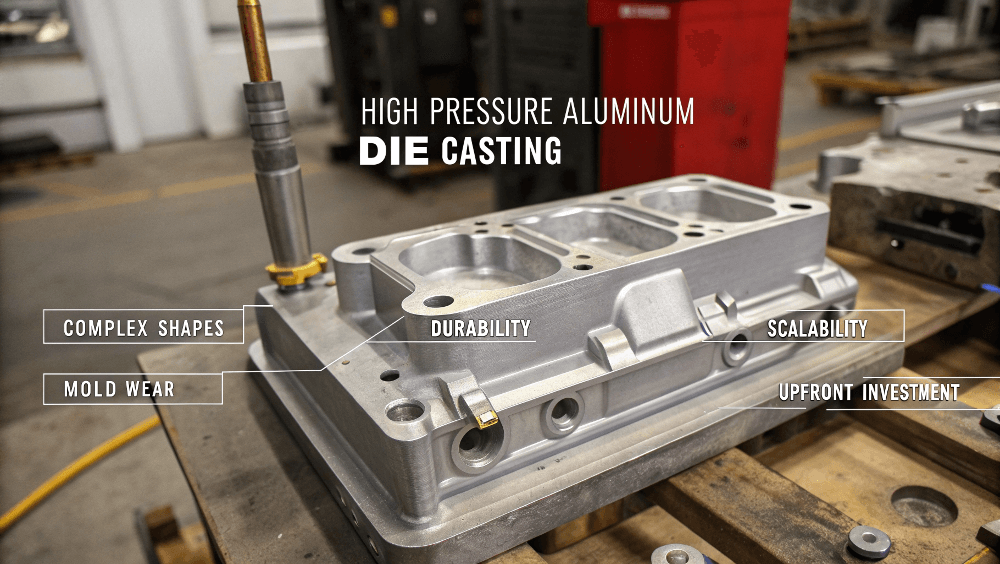
1. What is High-Pressure Aluminum Die Casting?
High-pressure aluminum die casting is a process that involves injecting molten aluminum into a metal mold under high pressure. This results in the production of precise, durable parts. Unlike other casting methods, high-pressure die casting can create intricate shapes with high dimensional accuracy. The key components in the process include the die (mold), the molten aluminum, and the machine that injects the molten metal into the die. One of the main differences between high-pressure die casting and low-pressure die casting is the level of pressure applied and the type of molds used. High-pressure casting is best suited for mass production, where speed and precision are crucial.
The process begins by heating aluminum to a molten state and injecting it into the die with great force. The metal fills the cavity of the mold, where it cools and solidifies to form the final part. After cooling, the part is ejected from the mold, and excess material is trimmed off. This process allows manufacturers to create parts that are both complex and durable, making it ideal for industries that demand high-quality products, such as the automotive and aerospace industries.
High-pressure die casting offers several advantages, but it also comes with certain limitations. Let’s explore both the benefits and drawbacks of this process in more detail.
What’s the real story? Well, high-pressure aluminum die casting is an effective method for creating precise, strong, and lightweight parts, but like any manufacturing process, it comes with trade-offs. Let’s dive into the next section to see what those benefits are.
Component | Description |
---|---|
Key Material | Aluminum, used for its lightweight, strength, and corrosion resistance. |
Process | Molten aluminum injected into a mold under high pressure. |
Mold Design | Mold needs proper cooling channels, gates, and vents to ensure the right filling and solidification. |
Suitability | Best for high-volume production due to high precision and quick cycle times. |
2. What are the Advantages of High-Pressure Aluminum Die Casting?
High-pressure aluminum die casting has several advantages that make it a popular choice for mass production of metal parts. One of the most significant benefits is precision and dimensional accuracy. The high pressure used during the process ensures that the molten aluminum fills the die completely, resulting in parts with high accuracy and minimal need for additional machining. This precision is crucial in industries like automotive and aerospace, where parts need to fit together perfectly for safety and functionality.
Ready for the good part? The process also offers short cycle times, which means that manufacturers can produce large quantities of parts quickly. This makes high-pressure aluminum die casting highly cost-effective for high-volume production. The efficiency of the process allows manufacturers to meet tight deadlines while maintaining the quality of the parts being produced.
But there’s more. High-pressure aluminum die casting allows for complex part designs. Since the molten aluminum is injected under high pressure, it can flow into intricate molds with small, fine features. This capability makes it possible to create parts that would be difficult or impossible to manufacture using other methods. This is especially important for industries like electronics, where complex shapes are often required for enclosures or connectors.
Additionally, the process results in parts with improved material properties. Aluminum is known for its strength-to-weight ratio, and when it’s cast using high-pressure die casting, it retains its lightweight nature while providing excellent strength and durability. This makes high-pressure aluminum die casting an excellent choice for producing parts used in demanding applications like automotive engines and structural components.
Advantage | Description |
---|---|
Precision & Dimensional Accuracy | High pressure ensures that molten aluminum fills the mold precisely, resulting in accurate parts. |
Short Cycle Time | The speed of the process reduces production time, making it ideal for high-volume manufacturing. |
Complex Designs | Capable of producing intricate, thin-walled parts with complex geometries. |
Material Strength | Aluminum maintains its lightweight nature while providing strength and durability. |
What’s the catch? Although high-pressure aluminum die casting offers many benefits, it’s essential to understand its drawbacks. Let’s examine those in the next section.
3. What are the Disadvantages of High-Pressure Aluminum Die Casting?
While high-pressure aluminum die casting offers many advantages, it also comes with several disadvantages that should be considered. One of the primary drawbacks is the high initial tooling costs. The molds used in high-pressure die casting are typically made of hardened steel, which can be expensive to produce. This high upfront cost can be a barrier for small manufacturers or those who only need to produce small quantities of parts.
This is where it gets interesting. High-pressure die casting is best suited for large-scale production, so if a manufacturer doesn’t need to produce a high volume of parts, the initial investment in molds and equipment may not be justifiable. This is a crucial factor to consider before choosing this method for your project.
Another downside of high-pressure aluminum die casting is that it is limited to certain part sizes. The process works best for producing smaller to medium-sized parts, and producing large parts may require specialized equipment. Larger parts also require thicker molds, which increases the cost and complexity of the process.
Additionally, high-pressure die casting can sometimes lead to surface defects. While the process generally produces smooth, accurate parts, it can also result in imperfections like porosity, cracks, or surface roughness. These defects can compromise the strength and appearance of the parts, requiring additional work to correct.
Finally, while high-pressure die casting is known for its precision, material wastage can be a concern. The molten aluminum that doesn’t fill the mold or is removed as scrap can be wasted, leading to higher material costs. However, many manufacturers recycle the aluminum waste, which helps reduce the overall environmental impact of the process.
Disadvantage | Description |
---|---|
High Initial Tooling Costs | The molds used in the process are expensive, making the initial investment high. |
Part Size Limitations | Best suited for small to medium-sized parts; large parts require specialized equipment and thicker molds. |
Surface Defects | Issues like porosity, cracks, or rough surfaces may occur, requiring additional finishing work. |
Material Wastage | Scrap aluminum and molten metal waste can increase material costs if not recycled properly. |
What’s the real story here? High-pressure aluminum die casting is an excellent choice for high-volume production of precise, durable parts, but it comes with some challenges, particularly when it comes to tooling costs and material waste. Let’s move on to the next section to see how the process works in more detail.
4. How Does High-Pressure Aluminum Die Casting Work?
High-pressure aluminum die casting involves injecting molten aluminum into a steel mold under high pressure. The process begins by melting aluminum in a furnace until it reaches a molten state. Once the metal is molten, it is fed into a die casting machine, where it is injected into a mold at high pressure. The pressure forces the molten aluminum to fill the mold, ensuring that the metal takes the shape of the cavity with high precision.
What’s the kicker? The high pressure used in this process allows for the creation of parts with intricate shapes and fine details that would be difficult to achieve using other methods. After the molten metal has filled the mold, it is allowed to cool and solidify. Once the part has cooled sufficiently, it is ejected from the mold, and any excess material is trimmed off.
The die casting machine is an essential component of this process. It is responsible for controlling the injection pressure, temperature, and speed of the molten aluminum. These factors are crucial to achieving the desired material properties and dimensional accuracy. The mold design also plays a significant role in the final outcome of the process. Molds need to be designed with proper cooling channels, vents, and gates to ensure efficient metal flow and reduce defects in the final part.
Process Step | Description |
---|---|
Melting Aluminum | Aluminum is heated in a furnace until it becomes molten and ready for injection. |
Injection into Mold | The molten aluminum is injected under high pressure into a precisely engineered mold. |
Cooling and Solidification | The part is allowed to cool and solidify before being ejected from the mold. |
Mold Design | Proper mold design with cooling channels, vents, and gates ensures efficient metal flow and high-quality parts. |
Ready for the next step? High-pressure aluminum die casting is a highly effective and efficient process for producing parts with high precision and durability. However, to achieve the best results, it’s essential to consider the design of both the molds and the machines used in the process. Let’s dive deeper into the types of materials used in this casting process.
5. What Materials Are Used in High-Pressure Aluminum Die Casting?
The primary material used in high-pressure aluminum die casting is aluminum, which is favored for its lightweight, strength-to-weight ratio, and excellent corrosion resistance. Aluminum alloys such as A380, A356, and A319 are commonly used in the casting process. These alloys offer good fluidity, making them ideal for high-pressure die casting, as they can easily flow into complex mold designs.
But here’s the kicker. The selection of the right aluminum alloy is crucial for achieving the desired mechanical properties in the final part. For instance, aluminum alloys like A356 are often used for producing parts in the automotive industry due to their excellent strength and durability. A380, on the other hand, is used for die casting parts that require good dimensional accuracy and surface finish, such as those found in electronics.
While aluminum is the primary material used, high-pressure die casting can also accommodate other metals, such as zinc and magnesium, though these materials are generally used for specific applications. Zinc alloys are used in die casting when parts require high strength and corrosion resistance, and magnesium is used when a lighter weight part is needed.
The advantages of aluminum for die casting are well-documented. Its lightweight nature, strength, and resistance to corrosion make it an ideal choice for industries like automotive, aerospace, and electronics. Additionally, aluminum is highly recyclable, which helps reduce material costs and environmental impact.
Material | Description |
---|---|
Aluminum A380 | Offers high dimensional accuracy and excellent surface finish, ideal for general die casting. |
Aluminum A356 | Known for strength and durability, often used in the automotive industry. |
Magnesium | Lightweight and used for parts requiring lower density and high strength. |
Zinc | High strength and corrosion resistance, used in specific applications such as connectors and enclosures. |
What’s the real story? Choosing the right material for high-pressure aluminum die casting is essential for ensuring that the final part meets the required specifications. Let’s continue by exploring the common applications of high-pressure aluminum die casting.
6. What Are the Common Applications of High-Pressure Aluminum Die Casting?
High-pressure aluminum die casting is used across a wide range of industries due to its ability to produce precise, durable, and lightweight parts. One of the most common applications is in the automotive industry, where aluminum die-cast parts are used in engine blocks, transmission housings, and wheels. The lightweight nature of aluminum helps reduce the overall weight of vehicles, improving fuel efficiency without compromising strength.
What’s the catch? The aerospace industry also heavily relies on high-pressure aluminum die casting for components such as brackets, housings, and structural parts. The high precision and strength of the parts made using this process make them suitable for demanding aerospace applications, where safety and reliability are paramount.
Additionally, the electronics industry benefits from high-pressure aluminum die casting. Parts such as enclosures for smartphones, laptops, and other devices are often made using this process. The ability to create intricate shapes and thin-walled parts makes aluminum die casting an excellent choice for electronics manufacturers.
Ready for the next step? The versatility of high-pressure aluminum die casting makes it suitable for a wide range of applications. From automotive to electronics, this process is used to create parts that are lightweight, durable, and precise. Let’s move on to compare high-pressure aluminum die casting with other casting methods.
Application | Description |
---|---|
Automotive Industry | Used for components like engine blocks and transmission housings due to aluminum’s lightweight and strength properties. |
Aerospace | Die-cast parts are used for brackets and housings that require high precision and reliability. |
Electronics | Enclosures for smartphones, laptops, and other devices benefit from aluminum’s durability and lightweight nature. |
Industrial Machinery | Parts such as structural components and housings are produced for use in heavy machinery. |
What’s the real story? High-pressure aluminum die casting is an essential process for industries that require lightweight, durable parts with complex geometries. Let’s continue to explore how high-pressure aluminum die casting compares to other casting methods.
7. How Does High-Pressure Aluminum Die Casting Compare to Other Casting Methods?
High-pressure aluminum die casting offers several advantages over other casting methods, such as sand casting and gravity die casting. Unlike sand casting, which involves pouring molten metal into a sand mold, high-pressure die casting uses high pressure to force the molten aluminum into a precisely engineered mold. This results in parts with higher dimensional accuracy and a smoother surface finish.
This is where it gets interesting. Gravity die casting, on the other hand, involves pouring molten metal into a mold under the force of gravity. While it is a more economical method for producing parts in small to medium quantities, high-pressure die casting excels in high-volume production, where speed and precision are essential. The high pressure used in die casting allows for the creation of parts with complex geometries and thin walls that are difficult to achieve with other methods.
What’s the catch? While high-pressure aluminum die casting offers numerous advantages, it may not be suitable for every application. The high initial tooling costs can be a barrier for small-scale production, and the process may not be ideal for producing large parts. However, for high-volume production, the precision, efficiency, and material properties offered by high-pressure aluminum die casting make it a preferred choice.
What’s the real story? High-pressure aluminum die casting is ideal for producing complex, high-quality parts in large volumes. While it has some drawbacks, such as high tooling costs, it offers superior precision and efficiency when compared to other casting methods. Let’s continue by exploring how high-pressure aluminum die casting affects product quality.
Casting Method | Pros | Cons |
---|---|---|
High-Pressure Die Casting | High precision, ideal for complex geometries, quick cycle times for high-volume production. | High initial tooling costs, limited to small to medium parts. |
Sand Casting | Economical for small runs, can be used for large parts. | Lower precision, rougher surface finish, longer production times. |
Gravity Die Casting | Economical for medium-volume production, simpler tooling. | Limited to simpler part designs, less precision than high-pressure die casting. |
What’s the real story? High-pressure aluminum die casting is perfect for high-precision, high-volume production but may not always be the best choice for small runs or very large parts. Let’s continue by exploring the key factors influencing the quality of die castings.
8. What Are the Key Factors Influencing the Quality of High-Pressure Aluminum Die Castings?
The quality of high-pressure aluminum die castings is influenced by several factors. One of the most important is mold design. The mold must be designed with proper cooling channels, vents, and gates to ensure that the molten aluminum flows evenly into the mold and cools uniformly. Proper mold design helps prevent defects like porosity and surface imperfections.
What’s the kicker? The die casting machine settings, such as pressure, temperature, and speed, also play a crucial role in determining the final quality of the part. These settings need to be optimized to ensure that the molten aluminum fills the mold properly and solidifies at the right rate to avoid defects.
But here’s the real story. Another key factor influencing part quality is the temperature control. Maintaining the correct temperature throughout the process helps prevent issues like shrinkage or distortion in the final part. Cooling rates also need to be carefully controlled to ensure that the aluminum solidifies properly without causing internal stresses.
The precision and durability of the final part are highly dependent on these variables. If any aspect of the process is off, it can lead to significant defects, resulting in costly rework or product failure. As a result, manufacturers must closely monitor these factors and continuously adjust them to ensure high-quality output.
Quality Factor | Description |
---|---|
Mold Design | Proper mold design with adequate cooling channels and vents ensures smooth metal flow and reduces defects. |
Machine Settings | The correct pressure, temperature, and speed settings ensure accurate filling and solidification of the mold. |
Temperature Control | Consistent temperature control prevents shrinkage, porosity, and other defects. |
Cooling Rate | Adjusting the cooling rate ensures uniform solidification and prevents distortion in the final part. |
What’s the catch? Achieving high-quality die castings requires a balance between proper mold design, machine settings, and temperature control. Let’s move on to the next section to see what common challenges manufacturers face in high-pressure aluminum die casting.
9. What Are the Common Challenges in High-Pressure Aluminum Die Casting?
One of the primary challenges in high-pressure aluminum die casting is porosity. This occurs when air pockets are trapped inside the molten aluminum as it solidifies. Porosity can weaken the final part, making it more prone to failure under stress. What’s the real story? Proper mold design and machine settings can minimize porosity, but it remains a challenge in some cases.
What’s the kicker? Shrinkage is another common challenge in die casting. As aluminum cools and solidifies, it contracts. If the cooling rate is not properly controlled, this shrinkage can lead to dimensional inaccuracies or surface defects. Manufacturers need to ensure that the cooling process is evenly controlled to prevent shrinkage and ensure high-quality parts.
Ready for the good part? Complex mold designs can also present challenges in high-pressure aluminum die casting. Designing molds for intricate shapes requires careful planning and expertise, and any mistakes in the design process can result in defects or inefficiencies in production. It’s essential for manufacturers to work closely with experienced die designers to avoid these issues.
What’s the real story? Despite these challenges, high-pressure aluminum die casting remains an efficient and effective method for producing high-precision parts. Manufacturers must carefully manage factors like porosity, shrinkage, and mold complexity to achieve the best results. Let’s continue by exploring how to improve the efficiency of the process.
Challenge | Description |
---|---|
Porosity | Trapped air pockets in the molten aluminum can weaken parts and make them prone to failure. |
Shrinkage | Cooling rates must be controlled to avoid shrinkage, which can cause dimensional inaccuracies. |
Complex Mold Designs | Intricate mold designs require careful planning and expertise to avoid defects or inefficiencies. |
Defects | Surface imperfections like cracks and roughness are common when the process isn’t optimized. |
What’s the real story? High-pressure aluminum die casting is a great option for producing precise parts, but it requires careful attention to potential issues like porosity and shrinkage. Let’s explore how to improve efficiency in this process.
10. How Can You Improve the Efficiency of High-Pressure Aluminum Die Casting?
There are several ways to improve the efficiency of high-pressure aluminum die casting. Optimizing die design is one of the most effective methods. A well-designed mold ensures that molten aluminum flows evenly, cooling at a consistent rate and minimizing defects. What’s the kicker? Advanced cooling techniques, such as using cooling channels or high-conductivity materials, can also help improve efficiency by reducing cycle times and minimizing defects.
But here’s the real story. Machine settings also play a crucial role in efficiency. Adjusting factors like injection pressure, temperature, and speed can help reduce cycle times and improve the quality of the parts. Manufacturers should work closely with die casting machine operators to fine-tune these settings for optimal performance.
Ready for the good part? Manufacturers can also improve efficiency by recycling scrap material. Since aluminum is highly recyclable, manufacturers can reuse material that’s trimmed off during production, helping reduce material costs and environmental impact. By implementing these strategies, manufacturers can improve both the efficiency and sustainability of the high-pressure aluminum die casting process.
Efficiency Improvement | Description |
---|---|
Optimizing Die Design | A well-designed mold improves flow, reduces defects, and accelerates cooling, leading to greater efficiency. |
Adjusting Machine Settings | Fine-tuning injection pressure, temperature, and speed helps reduce cycle time and improve part quality. |
Recycling Scrap Material | Reusing trimmed aluminum reduces material costs and environmental impact. |
What’s the real story? Improving the efficiency of high-pressure aluminum die casting requires a combination of optimized die design, machine settings, and material management. Let’s continue to explore the environmental impact of this process.
11. What Are the Environmental Considerations in High-Pressure Aluminum Die Casting?
High-pressure aluminum die casting, like any manufacturing process, has environmental implications. Energy consumption is one of the main concerns. The process requires high temperatures and pressure, which can result in significant energy usage. What’s the kicker? Manufacturers can reduce energy consumption by optimizing machine settings and using more efficient equipment.
But here’s the real story. Material recycling is another key environmental consideration. Since aluminum is highly recyclable, manufacturers can recycle scrap aluminum to reduce waste and minimize environmental impact. Many die casting manufacturers already have recycling systems in place to ensure that scrap material is reused.
What’s the catch? While the aluminum itself is recyclable, the overall environmental impact of the die casting process can still be significant if not properly managed. Manufacturers need to be mindful of energy use, material waste, and emissions during production to minimize the environmental footprint.
Environmental Factor | Description |
---|---|
Energy Consumption | High-pressure die casting consumes significant energy due to the high temperatures and pressures required. |
Material Recycling | Aluminum is highly recyclable, which helps reduce material waste and overall environmental impact. |
Emissions and Waste | Proper management of emissions and waste is crucial for reducing the environmental footprint of the process. |
What’s the real story? High-pressure aluminum die casting has environmental impacts, but with careful management, it’s possible to minimize those effects. Let’s move on to the next section to discuss the costs of the process.
12. How Much Does High-Pressure Aluminum Die Casting Cost?
The cost of high-pressure aluminum die casting can vary widely depending on several factors. One of the main costs is the initial setup for the molds. Since the molds used in high-pressure die casting are made from hardened steel, they can be expensive to produce. However, this cost is amortized over high-volume production runs.
Ready for the good part? Operational costs are also a key consideration. These include energy costs, labor costs, and maintenance costs for the equipment. Since the process involves high pressure and temperature, the equipment must be carefully maintained to ensure smooth operation.
What’s the kicker? Although the initial tooling costs are high, high-volume production can help reduce the overall cost per part. Manufacturers who need to produce large quantities of parts will typically see a reduction in unit costs, making the process more cost-effective.
Cost Factor | Description |
---|---|
Initial Tooling Costs | Molds made of hardened steel are expensive, but the cost is spread over large production runs. |
Operational Costs | Includes energy, labor, and maintenance costs associated with the die casting process. |
High-Volume Production | High-volume production reduces the cost per part, making the process more cost-effective for large runs. |
What’s the real story? The cost of high-pressure aluminum die casting can be high, but it is offset by the cost savings in high-volume production. Let’s explore the safety measures that should be followed in the process.
13. What Safety Measures Should Be Followed in High-Pressure Aluminum Die Casting?
High-pressure aluminum die casting involves working with molten metal, which can pose significant safety risks. To ensure the safety of workers, proper protective equipment should be worn, including heat-resistant gloves, safety goggles, and protective clothing. What’s the kicker? Workers should also be trained in the safe handling of molten aluminum and the operation of die casting machinery.
But here’s the real story. Preventing accidents is key in high-pressure aluminum die casting. Manufacturers should have strict safety protocols in place, including emergency procedures in the event of a fire, explosion, or equipment malfunction. It’s also important to regularly inspect machinery for wear and tear to prevent accidents caused by equipment failure.
What’s the catch? The high temperatures and pressures involved in high-pressure die casting make safety a top priority. By implementing comprehensive safety measures, manufacturers can reduce the risk of accidents and ensure a safe working environment for employees.
Safety Measure | Description |
---|---|
Protective Equipment | Workers should wear heat-resistant gloves, goggles, and clothing to protect against molten aluminum. |
Employee Training | Workers must be trained in the safe handling of molten aluminum and die casting equipment. |
Emergency Procedures | Strict protocols for emergencies, including fire, explosion, and equipment malfunction, should be in place. |
What’s the real story? Safety is paramount in high-pressure aluminum die casting, and manufacturers should take proactive steps to protect workers and ensure a safe working environment. Let’s continue by exploring the future of this process.
14. What Is the Future of High-Pressure Aluminum Die Casting?
The future of high-pressure aluminum die casting looks promising, with several innovations on the horizon. What’s the kicker? Advancements in die casting technology are improving the speed, efficiency, and quality of the process. New techniques, such as 3D printing of molds and automated systems, are helping reduce costs and improve precision.
Ready for the good part? Industry trends indicate that the demand for lightweight, durable parts is on the rise, particularly in industries like automotive, aerospace, and electronics. This means that high-pressure aluminum die casting will continue to play a crucial role in manufacturing for years to come.
What’s the catch? The future of high-pressure aluminum die casting will depend on continued technological innovation and the development of new materials. Manufacturers will need to stay ahead of the curve by adopting new technologies and processes to remain competitive in the marketplace.
Future Trend | Description |
---|---|
Technological Innovation | New advancements such as 3D printing and automation are improving speed and precision. |
Lightweight, Durable Parts | The increasing demand for lightweight, durable components in automotive, aerospace, and electronics drives growth. |
New Materials | The development of new materials for die casting will improve the versatility and quality of cast parts. |
What’s the real story? The future of high-pressure aluminum die casting is bright, with technological advancements driving improvements in efficiency, quality, and cost-effectiveness. Let’s move on to the next section to explore how to choose the right die casting supplier.
15. How Can You Choose the Right Die Casting Supplier?
When choosing a supplier for high-pressure aluminum die casting, it’s essential to consider factors such as experience, reputation, and quality control. The supplier should have a proven track record in producing high-quality die castings and be able to meet your specific production needs. What’s the kicker? It’s important to ask for references and case studies to verify their capabilities.
But here’s the real story. Customer service is another important factor to consider when choosing a die casting supplier. The supplier should be responsive and able to provide technical support throughout the production process. Additionally, the supplier should have the necessary certifications and adhere to industry standards to ensure the quality of their products.
What’s the catch? Choosing the right die casting supplier is crucial to the success of your project. By evaluating suppliers based on their experience, reputation, quality control, and customer service, you can ensure that you’re working with a reliable partner.
Supplier Selection Criteria | Description |
---|---|
Experience & Reputation | A proven track record in high-quality die casting and positive references from previous clients. |
Quality Control | Suppliers should have robust quality control systems in place to ensure the final product meets your specifications. |
Customer Service | Responsive support and technical assistance are critical for ensuring smooth production. |
What’s the real story? Selecting the right supplier for high-pressure aluminum die casting is key to achieving high-quality results. Let’s move on to the FAQ section for further clarification on this process.
FAQ Section
Q1: What is high-pressure aluminum die casting?
High-pressure aluminum die casting is a manufacturing process in which molten aluminum is injected into a mold under high pressure to create precise, durable parts.
Q2: How does high-pressure aluminum die casting work?
The process involves injecting molten aluminum into a mold under high pressure, which fills the mold completely and solidifies to form the desired part.
Q3: What are the advantages of high-pressure aluminum die casting?
The main advantages include precision, short cycle times, cost-effectiveness for high-volume production, and the ability to create complex part designs.
Q4: What are the disadvantages of high-pressure aluminum die casting?
The disadvantages include high initial tooling costs, limitations in part size, and potential for surface defects.
Q5: How do I choose the right die casting supplier?
Look for suppliers with experience, a strong reputation, robust quality control, and excellent customer service to ensure reliable, high-quality parts.