Heat-resistant metals are essential materials in industries that require components to withstand high temperatures without losing their structural integrity. These metals, often alloyed with special elements, are used in aerospace, automotive, and chemical industries. However, as vital as they are, they come with their own set of challenges. So, what are the common difficulties faced when working with these materials? In this article, we will explore the properties of heat-resistant metals, the challenges that arise in their application, and how to overcome them effectively.
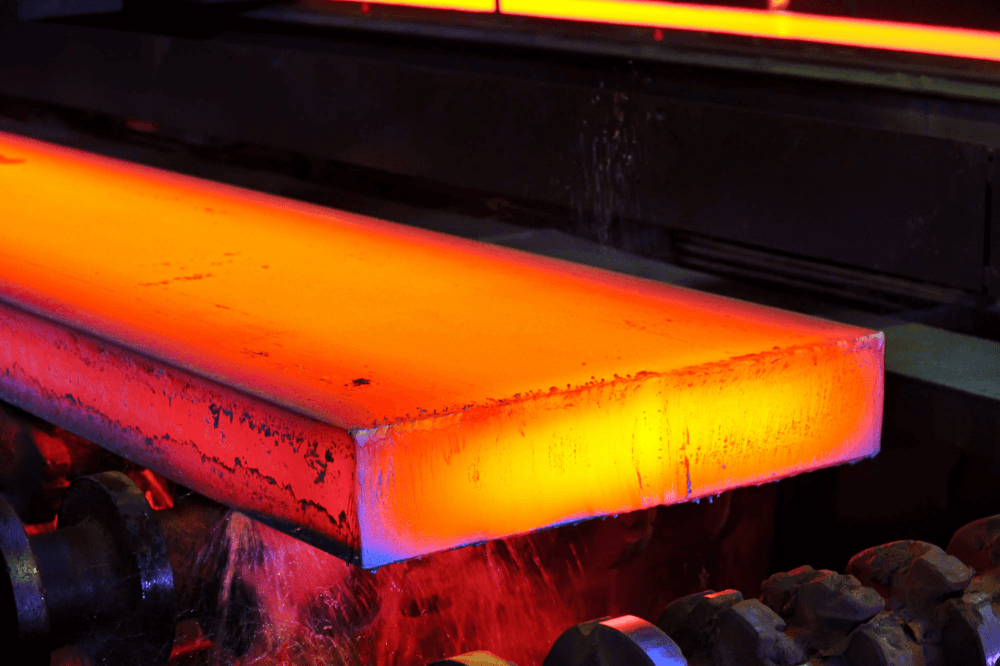
1. Introduction to Heat-Resistant Metals
Heat-resistant metals are specifically designed to perform in extreme temperature environments without degrading. These materials are critical in sectors where high heat is generated, such as aerospace, power generation, and chemical processing industries. While the need for these metals is undeniable, their complex properties often present challenges.
What’s the real story? Heat-resistant metals like Inconel, Titanium, and Hastelloy are alloys chosen for their ability to endure high temperatures without significant deformation. However, their unique characteristics also bring about hurdles such as cost, processing difficulties, and performance consistency. In industries where precision and reliability are paramount, these metals must meet stringent demands.
But here’s the kicker: These metals not only resist heat but also face challenges from thermal shock, corrosion, and fatigue under extreme conditions. Manufacturers and engineers need to balance cost, performance, and material properties to achieve optimal results.
Heat-Resistant Metals | Characteristics | Common Applications |
---|---|---|
Inconel | High-temperature resistance, oxidation resistance | Jet engines, gas turbines |
Titanium | Light weight, high strength-to-weight ratio | Aerospace, marine |
Hastelloy | Excellent corrosion resistance | Chemical reactors, high-pressure systems |
2. Properties of Heat-Resistant Metals
Heat-resistant metals are typically chosen for their ability to withstand extreme temperatures. These materials have high melting points, low thermal expansion, and resistance to corrosion at elevated temperatures. The most well-known examples of these metals are alloys like Inconel, which is used in jet engines, and Titanium, valued for its lightweight properties.
Ready for the good part? These metals often have specific properties that allow them to operate under harsh conditions. For instance, high melting points ensure they remain solid and stable even when exposed to temperatures far above those that would melt conventional metals. This property is critical in applications where metals are exposed to fire, extreme heat, and friction.
One of the key challenges, however, is managing the balance between thermal conductivity and insulation. While low thermal conductivity is often desired, too much insulation can lead to heat buildup, which may affect the metal’s structural integrity.
Metal Type | Melting Point | Thermal Conductivity | Common Uses |
---|---|---|---|
Inconel | 1,300°C | Low | Jet engines, heat exchangers |
Titanium | 1,668°C | Moderate | Aerospace, medical devices |
Hastelloy | 1,400°C | Low | Chemical reactors, high-temperature applications |
3. What Makes Heat-Resistant Metals Different?
Heat-resistant metals differ from standard metals in their ability to resist not only high temperatures but also oxidation and corrosion at these extreme levels. These metals are typically alloyed with other elements such as nickel, chromium, and molybdenum to improve their thermal and mechanical properties.
You might be wondering: What makes them stand out from regular metals like aluminum or steel? Regular metals may perform well under moderate heat, but when subjected to extreme conditions, they weaken, corrode, or even melt. Heat-resistant metals, on the other hand, are engineered to withstand prolonged exposure to elevated temperatures.
What’s the real story? The key difference lies in the chemical composition of heat-resistant alloys. For example, the addition of chromium enhances oxidation resistance, while molybdenum strengthens the material under high heat. These alloys provide exceptional strength, durability, and resistance to thermal fatigue, which is why they are indispensable in the industries that require high-performance materials.
Alloy | Key Element Added | Benefit |
---|---|---|
Inconel | Nickel | High-temperature stability |
Titanium | Aluminum | Lightweight, corrosion resistance |
Hastelloy | Molybdenum | Increased resistance to corrosion and high pressure |
4. Common Challenges with Heat-Resistant Metals
Heat-resistant metals, despite their impressive properties, are not without challenges. One of the most pressing difficulties is the high cost of these materials. Due to their specialized production processes and the rare elements used in alloys, heat-resistant metals can be significantly more expensive than standard metals.
Here’s the challenge: The high cost often limits their use in some industries, making it crucial for manufacturers to weigh the benefits against the investment. Another challenge lies in processing these materials. Heat-resistant metals require specialized equipment and techniques to manufacture, which can lead to longer production times and increased labor costs.
But here’s the kicker: Thermal fatigue and oxidation are also major concerns. Over time, heat-resistant metals can experience cracks or surface degradation when exposed to fluctuating temperatures, especially in applications like turbines or engines. Manufacturers need to use precise methods to ensure these metals perform at their peak without failing prematurely.
Challenge | Impact | Solutions |
---|---|---|
High cost | Limits use in some industries | Balance cost and performance with advanced alloys |
Processing difficulty | Requires specialized equipment | Invest in better machinery or outsource production |
Thermal fatigue | Can lead to premature failure | Improve alloy compositions, apply coatings |
5. Why Do Heat-Resistant Metals Fail?
Heat-resistant metals are designed to withstand extreme conditions, but they still have their limits. When subjected to rapid temperature changes, the metals can experience thermal shock, causing cracks or fractures. Additionally, exposure to high temperatures for prolonged periods can lead to oxidation, weakening the material’s structural integrity.
You might be wondering: Why do these metals fail despite their high resistance to heat? The answer lies in the factors that contribute to their performance degradation. Even the strongest alloys can become brittle over time due to the stresses of thermal cycling, which leads to micro-cracks in the material. Furthermore, oxidation can cause a breakdown of the metal’s surface, making it vulnerable to corrosion.
Here’s the catch: Preventing metal failure requires not only choosing the right alloys but also maintaining optimal operating conditions. This includes regulating the temperature to avoid rapid fluctuations, using protective coatings, and ensuring proper material selection based on the specific application requirements.
Failure Type | Cause | Prevention |
---|---|---|
Thermal shock | Rapid temperature changes | Use thermal cycling tests to predict performance |
Oxidation | Prolonged exposure to high heat | Apply protective coatings, select oxidation-resistant alloys |
Cracking | Thermal cycling stress | Choose materials designed for thermal stability |
6. Impact of Heat-Resistant Metal Properties on Manufacturing
The unique properties of heat-resistant metals play a crucial role in manufacturing processes. However, these properties also pose challenges during production. Because these metals require high temperatures for forging or casting, manufacturers must ensure that their equipment can withstand the same extreme conditions.
Ready for the good part? The manufacturing process also involves specialized machinery and techniques such as vacuum casting or precision forging, which are designed to preserve the properties of the metal during production. These methods are expensive and require highly skilled labor, adding to the overall production cost.
Additionally, the complexity of heat-resistant metal compositions means that even small variations in the mix can lead to significant changes in performance. Manufacturers must carefully control every step of the process to avoid costly mistakes.
Property | Manufacturing Challenge | Solution |
---|---|---|
High melting point | Requires high temperature equipment | Invest in specialized furnaces, use controlled environments |
Thermal stability | Can be altered during processing | Monitor alloy composition precisely |
Brittleness | Prone to cracking during forging | Use proper cooling techniques to avoid stress |
7. How Heat-Resistant Metals Are Tested
Testing heat-resistant metals is an essential step in ensuring their reliability and performance in real-world applications. Manufacturers subject these materials to a variety of tests to simulate the extreme conditions they will face in the field. These tests are designed to measure the metal’s strength, resistance to heat, and durability under thermal stress.
What’s the real story? Heat-resistant metals undergo high-temperature tensile strength tests, which evaluate their ability to maintain their integrity when subjected to constant heat. Corrosion and oxidation tests also simulate long-term exposure to heat, helping engineers understand how the material will perform over time.
This is where it gets interesting: The results of these tests provide valuable data that help manufacturers and engineers optimize the metal for specific applications. The tests ensure that the metal can handle the conditions it will encounter without failing prematurely.
Test Type | Purpose | Key Metrics Tested |
---|---|---|
Tensile strength | Evaluate material strength at high temperatures | Yield strength, elongation, ductility |
Corrosion resistance | Assess long-term heat exposure | Oxidation rate, surface degradation |
Thermal fatigue | Simulate temperature cycling | Crack formation, material failure |
8. Material Selection: Which Heat-Resistant Metal Is Best for Your Application?
Selecting the right heat-resistant metal for a specific application can be a daunting task. Factors such as operating temperature, stress levels, and exposure to corrosive environments all play a role in determining the best material.
What’s the real story? Different industries require different characteristics in their heat-resistant metals. Aerospace applications, for example, demand metals that can withstand extreme temperatures and maintain high strength-to-weight ratios. On the other hand, chemical processing industries may prioritize metals that are resistant to corrosion and oxidation at high temperatures.
Here’s the catch: It’s essential to balance performance and cost. While some heat-resistant metals like Inconel are perfect for high-performance applications, they may come with a high price tag. Manufacturers need to assess their specific needs before deciding on the material.
Metal Type | Best Use | Key Properties |
---|---|---|
Inconel | Aerospace, turbines | High strength, oxidation resistance |
Titanium | Aerospace, automotive | Lightweight, corrosion resistance |
Hastelloy | Chemical processing | Corrosion resistance, high temperature tolerance |
9. Common Industries and Applications of Heat-Resistant Metals
Heat-resistant metals are widely used across various industries, each with its specific requirements. The aerospace industry is one of the largest consumers of these materials, using them in engines, turbine blades, and exhaust systems.
But here’s the kicker: The automotive industry also relies heavily on heat-resistant alloys for components that must endure extreme heat, such as exhaust systems, catalytic converters, and engine parts. Similarly, power generation plants use these materials in turbine blades and heat exchangers to ensure optimal performance in high-temperature environments.
What’s the real story? These metals are crucial for ensuring the efficiency, safety, and longevity of critical components. Their unique properties allow them to operate under harsh conditions without degrading, which is why they are indispensable in high-performance applications.
Industry | Application | Heat-Resistant Metal Used |
---|---|---|
Aerospace | Jet engines, turbines | Inconel, Titanium |
Automotive | Exhaust systems, engine parts | Titanium, Stainless Steel |
Power generation | Turbines, heat exchangers | Hastelloy, Inconel |
10. Advanced Solutions to Overcome Challenges with Heat-Resistant Metals
The challenges faced by heat-resistant metals are not insurmountable. Engineers and material scientists are constantly working on new solutions to improve the performance and longevity of these metals.
Ready for the good part? Alloy optimization and new technologies in surface treatments have opened up new possibilities for overcoming the common challenges associated with heat-resistant metals. For instance, advanced coatings can enhance oxidation resistance, while nanotechnology has shown promise in increasing the strength and thermal stability of certain alloys.
But here’s the kicker: These innovations are making it possible to use heat-resistant metals in applications that were previously not feasible, expanding their potential across various industries.
Innovation | Impact | Example |
---|---|---|
Alloy optimization | Improved performance, lower cost | High-strength nickel alloys |
Surface coatings | Enhanced oxidation resistance | Ceramic coatings for turbines |
Nanotechnology | Increased strength and thermal stability | Nano-coated heat exchangers |
11. The Role of Heat-Resistant Metals in Future Technologies
Heat-resistant metals are essential for the development of new technologies, especially in high-performance sectors. As we move towards greener and more sustainable energy sources, the demand for advanced heat-resistant materials is expected to grow.
This is where it gets interesting: These metals will play a crucial role in industries like renewable energy, space exploration, and advanced manufacturing. Heat-resistant materials are already being tested for use in next-generation nuclear reactors, which operate at extremely high temperatures.
What’s the real story? As technology advances, the need for metals that can withstand extreme conditions will only increase. Engineers and scientists are pushing the limits of what heat-resistant metals can do, paving the way for more efficient and innovative applications.
Future Technology | Heat-Resistant Metal Required | Use |
---|---|---|
Nuclear reactors | Inconel, Hastelloy | High-temperature resistance |
Space exploration | Titanium, Inconel | Durability in extreme environments |
Renewable energy | Titanium, Stainless Steel | Resistance to high heat and corrosion |
12. How to Maintain and Extend the Life of Heat-Resistant Metals
While heat-resistant metals are durable, they still require maintenance to ensure long-term performance. Routine inspections and timely repairs can extend the life of these materials and prevent premature failure.
What’s the real story? Maintaining heat-resistant metals requires attention to factors like temperature fluctuations, surface degradation, and thermal cycling. Regular checks for cracks, oxidation, and material fatigue are necessary to ensure the components remain functional. Additionally, proper cleaning and the application of protective coatings can help maintain the material’s properties.
But here’s the kicker: Effective maintenance strategies can save costs in the long run by preventing major failures and ensuring that critical equipment operates at peak efficiency.
Maintenance Task | Frequency | Benefit |
---|---|---|
Regular inspections | Quarterly | Early detection of cracks or oxidation |
Surface treatments | Annually | Enhanced resistance to corrosion |
Thermal stress checks | Monthly | Prevent thermal fatigue |
13. Challenges in Recycling Heat-Resistant Metals
Recycling heat-resistant metals presents several challenges due to their complex compositions and the difficulty in reprocessing high-performance alloys.
You might be wondering: Why is recycling heat-resistant metals so difficult? The primary issue lies in the fact that these metals often contain a combination of elements that are hard to separate. Recycling processes that work for regular metals do not always work for these advanced alloys. Additionally, the cost of recycling these materials can be quite high.
Here’s the catch: Despite these challenges, research is underway to improve the recycling process and make it more cost-effective. The future may bring better methods to reclaim valuable materials from spent heat-resistant components.
Recycling Challenge | Issue | Potential Solution |
---|---|---|
Material complexity | Hard to separate alloy elements | Develop more efficient separation technologies |
High cost | Expensive processing | Investment in advanced recycling techniques |
Environmental impact | Waste disposal | Implement recycling programs to recover valuable metals |
14. Cost Analysis of Heat-Resistant Metals
Heat-resistant metals are often more expensive than other materials, which can be a significant factor when making decisions about material selection. The high cost is largely due to the raw materials used in alloy production and the specialized manufacturing processes required.
But here’s the kicker: Despite their higher upfront costs, heat-resistant metals can offer long-term savings due to their durability and ability to function under extreme conditions. This makes them a cost-effective option in critical industries where failure is not an option.
What’s the real story? The cost of these materials can vary significantly depending on the alloy and the supplier. However, the benefits they bring in terms of performance, longevity, and safety often outweigh the initial expense.
Metal Type | Cost per Unit | Applications | Benefits |
---|---|---|---|
Inconel | High | Aerospace, power generation | High temperature resistance, long-term durability |
Titanium | Moderate | Aerospace, medical devices | Lightweight, corrosion resistance |
Hastelloy | High | Chemical processing | Excellent resistance to corrosion and high pressure |
15. Conclusion: Managing the Challenges of Heat-Resistant Metals
Heat-resistant metals are indispensable in many high-performance applications, but their challenges cannot be ignored. From high costs and processing difficulties to issues like thermal fatigue and oxidation, these materials require careful consideration and management.
So, what’s the take-home message? By understanding the challenges and employing innovative solutions, industries can maximize the potential of heat-resistant metals while mitigating their drawbacks. Whether through improved alloy compositions, better maintenance practices, or investing in new technologies, the future of heat-resistant metals looks promising.
Summary | Key Takeaways | Solutions |
---|---|---|
Challenges | High cost, processing difficulties, failure risks | Use advanced alloys, regular maintenance, innovative coatings |
Solutions | Research into new materials, better recycling methods | Apply effective maintenance strategies |
FAQ Section
Q1: What are heat-resistant metals?
Heat-resistant metals are alloys designed to withstand extreme temperatures without losing their strength or structural integrity. These metals typically feature high melting points and resistance to thermal expansion, corrosion, and oxidation.
Q2: How do heat-resistant metals differ from regular metals?
Heat-resistant metals are engineered with specific properties such as high melting points, low thermal conductivity, and resistance to oxidation and thermal fatigue. Regular metals, by contrast, are often more prone to deformation, corrosion, or structural failure at high temperatures.
Q3: Why do heat-resistant metals fail under high temperatures?
Heat-resistant metals can fail due to thermal shock, oxidation, or deformation caused by prolonged exposure to high temperatures. These challenges can weaken the metal over time, especially if it’s not properly maintained or if the wrong material is selected for the application.
Q4: How are heat-resistant metals tested for performance?
Heat-resistant metals are tested through various methods such as heat cycling tests, high-temperature tensile strength tests, and corrosion resistance assessments. These tests simulate the conditions the metals will face in real-world applications, ensuring they meet necessary standards.
Q5: What industries benefit most from heat-resistant metals?
Industries such as aerospace, automotive, power generation, and chemical processing rely heavily on heat-resistant metals due to the extreme temperature conditions in which their equipment operates. These metals are crucial for components like engine parts, turbine blades, and reactors.