High-temperature alloys play a crucial role in industries that require materials to withstand extreme heat and pressure. These alloys are essential in sectors such as aerospace, automotive, and power generation, where performance is critical. However, there are several challenges associated with understanding and utilizing the properties of high-temperature alloys. These challenges impact everything from material design and manufacturing to long-term durability and performance in extreme conditions.
In this article, we will explore the key challenges associated with high-temperature alloys, focusing on issues like oxidation resistance, creep and fatigue resistance, thermal stability, manufacturing, and cost-performance trade-offs. We’ll also discuss the importance of proper alloy composition and ongoing research to overcome these challenges.
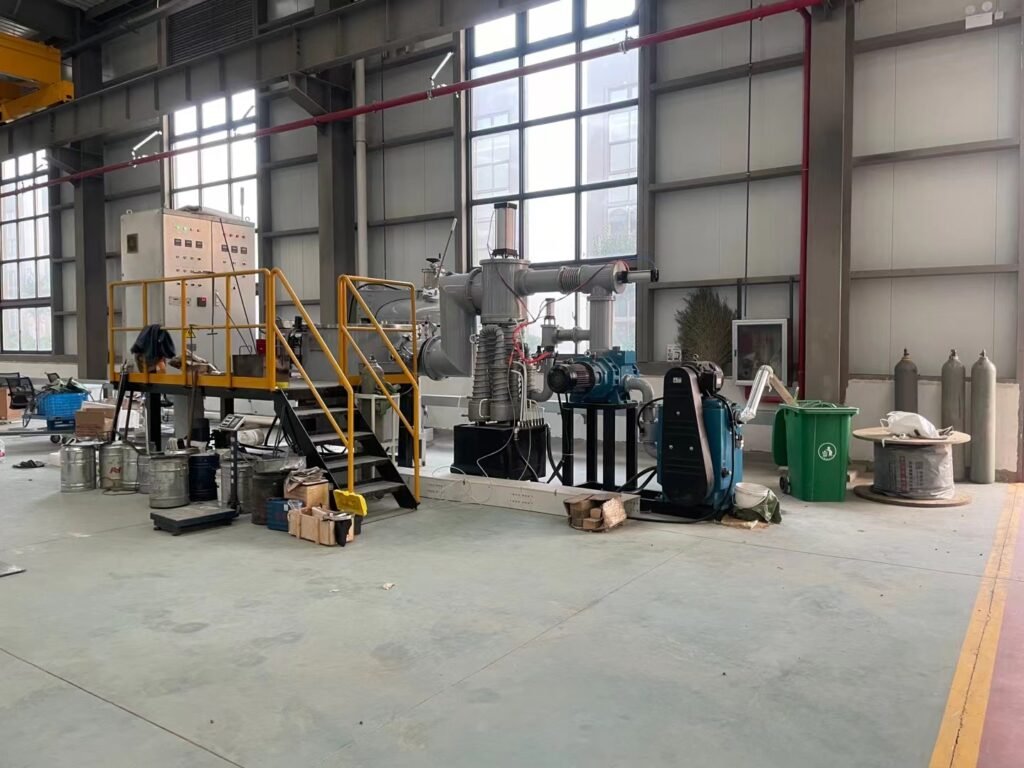
Understanding High-Temperature Alloys
High-temperature alloys are materials specifically designed to perform well at elevated temperatures. They are typically used in applications where extreme conditions such as high heat, oxidation, and corrosion are prevalent. These alloys are an essential component of industries such as aerospace, power generation, and automotive, where components need to endure temperatures above 500°C for extended periods.
Types and Composition of High-Temperature Alloys
High-temperature alloys are typically made from a combination of base metals such as nickel, cobalt, iron, or titanium, alloyed with elements like chromium, molybdenum, or aluminum. Each of these alloys is tailored to withstand specific environmental conditions and meet performance demands in various industries. For example, nickel-based superalloys are common in aerospace components like turbine blades, while cobalt-based alloys are used in power generation equipment.
Common Uses and Applications
High-temperature alloys are found in a variety of applications, including:
- Aerospace: Components in jet engines, turbine blades, and exhaust systems.
- Power Generation: Parts in gas turbines, heat exchangers, and nuclear reactors.
- Automotive: Turbochargers, exhaust systems, and internal engine components.
These applications require materials that can resist thermal degradation and maintain structural integrity over time, making high-temperature alloys indispensable in modern engineering.
Application | Example Components | Typical Temperature Range |
---|---|---|
Aerospace | Turbine blades, jet engine parts | 600–1,200°C |
Power Generation | Gas turbines, heat exchangers | 700–1,000°C |
Automotive | Turbochargers, exhaust systems | 400–800°C |
The Importance of Material Properties at Elevated Temperatures
At elevated temperatures, the properties of materials change significantly. For high-temperature alloys, this means they must maintain structural integrity and resist degradation caused by heat and other environmental factors. The material’s ability to resist oxidation, maintain strength, and prevent phase changes is crucial to its performance.
Key Properties of High-Temperature Alloys
There are several critical properties of high-temperature alloys that influence their effectiveness in extreme environments:
- Oxidation Resistance: Prevents the alloy from reacting with oxygen, which could lead to material degradation.
- Thermal Stability: Ensures the material retains its strength and structure at high temperatures.
- Strength and Creep Resistance: High-temperature alloys must be able to resist deformation under load and maintain their strength over extended periods.
Each of these properties is integral to ensuring the alloy performs well in its intended application. The challenges arise when trying to enhance these properties while also addressing factors like cost and manufacturing complexity.
Property | Importance | Challenges |
---|---|---|
Oxidation Resistance | Prevents material degradation and extends lifespan | High material cost |
Thermal Stability | Ensures structural integrity at high temperatures | Difficulty in achieving optimal stability |
Strength and Creep Resistance | Resists deformation and failure under load | Requires precise composition adjustments |
Challenge 1: Oxidation and Corrosion Resistance
Oxidation and corrosion are among the most significant challenges faced by high-temperature alloys. As these materials are exposed to high heat, oxygen, and other reactive gases, they can quickly degrade, leading to failure.
Why Oxidation is a Major Concern
High-temperature alloys in environments like jet engines or power plants are exposed to temperatures above 500°C, where oxidation can occur rapidly. Oxidation involves the reaction of the material with oxygen, leading to the formation of an oxide layer. While a thin oxide layer may be protective, over time it can grow, crack, or peel, leading to material failure.
Factors Influencing Oxidation Resistance
Several factors influence an alloy’s resistance to oxidation:
- Composition: The presence of alloying elements like chromium, aluminum, or silicon can improve oxidation resistance.
- Temperature: The higher the temperature, the more likely the alloy is to oxidize.
- Environment: The presence of reactive gases like sulfur or chlorine can accelerate oxidation.
Solutions and Advancements
To combat oxidation, engineers are continually developing alloys with better oxidation-resistant properties. This includes introducing elements like yttrium, which forms a stable oxide layer, or applying coatings to reduce direct exposure to reactive gases.
Alloy Type | Oxidation Resistance Features | Common Applications |
---|---|---|
Nickel-based | Excellent at high temperatures, forms protective oxide layers | Aerospace, gas turbines |
Cobalt-based | Strong oxidation resistance, used in harsh environments | Power generation, industrial heating |
Titanium-based | Forms a stable oxide layer, corrosion-resistant | Automotive, chemical industries |
Challenge 2: Creep and Fatigue Resistance
Creep and fatigue resistance are critical when designing high-temperature alloys, particularly in applications that require components to perform under sustained loads at elevated temperatures.
What is Creep?
Creep is the gradual deformation of a material under a constant load over time, especially at high temperatures. As alloys are subjected to heat and pressure, they can begin to elongate or distort, affecting their performance and lifespan. This can lead to catastrophic failures in critical components like turbine blades and engine parts.
Fatigue Resistance
In addition to creep, high-temperature alloys must also resist fatigue, which is the failure of a material after repeated cycles of stress. The combination of thermal cycling and mechanical load can cause cracks to form, leading to material fatigue.
Enhancing Creep and Fatigue Resistance
To improve creep resistance, alloy compositions are modified to include elements that strengthen the material’s grain structure. For fatigue resistance, manufacturers often use heat treatments or coatings that help to reduce crack formation.
Alloy Type | Creep Resistance Features | Fatigue Resistance Features |
---|---|---|
Nickel-based | Strong at elevated temperatures, resists creep under load | Improved fatigue life with proper heat treatment |
Titanium-based | Excellent creep resistance at moderate temperatures | Good fatigue resistance under cyclic loading |
Cobalt-based | Maintains strength at high temperatures, excellent for high-stress environments | Superior resistance to thermal cycling fatigue |
Challenge 3: Thermal Stability and Phase Changes
Thermal stability refers to an alloy’s ability to maintain its structure and properties at high temperatures. Phase changes in high-temperature alloys can significantly impact their performance.
The Issue of Phase Transitions
At high temperatures, high-temperature alloys can undergo phase transitions, where the crystal structure of the alloy changes. This can lead to loss of strength, ductility, or other critical properties. Maintaining a stable phase structure at elevated temperatures is essential to ensure the material’s reliability.
Methods to Improve Thermal Stability
To enhance thermal stability, manufacturers focus on optimizing the alloy composition and controlling the cooling rates during processing. Additionally, heat treatments are used to stabilize the phases in the alloy, preventing unwanted transformations during operation.
Alloy Type | Thermal Stability Features | Phase Stability Solutions |
---|---|---|
Nickel-based | Maintains strength and phase structure at high temperatures | Composition adjustments to stabilize phases |
Cobalt-based | High stability in extreme conditions | Heat treatments to maintain structural integrity |
Titanium-based | Stable at lower temperatures but prone to phase changes at high heat | Advanced processing techniques to stabilize phases |
Challenge 4: Manufacturing and Processing of High-Temperature Alloys
Manufacturing high-temperature alloys presents numerous challenges. These alloys often have high melting points and require specialized processing techniques to achieve the desired properties.
Difficulty in Casting and Shaping
One of the biggest challenges in alloy manufacturing is the difficulty of casting and shaping high-temperature alloys. These materials often have high melting points, making them difficult to mold and shape into the desired form.
Influence of Processing Techniques
The choice of processing techniques can significantly affect the final properties of the alloy. Techniques such as investment casting, powder metallurgy, and additive manufacturing are used to shape high-temperature alloys, but each comes with its own set of challenges and limitations.
Manufacturing Method | Challenges | Advantages |
---|---|---|
Investment Casting | High cost, difficult to achieve precise shapes | Can produce complex geometries with minimal waste |
Powder Metallurgy | Requires specialized equipment, difficulty in achieving uniform density | Good for producing high-performance alloys |
Additive Manufacturing | High cost, slower production time | Ability to create complex, customized parts |
Challenge 5: Cost vs. Performance Trade-off
Balancing cost and performance is always a challenge when designing and selecting high-temperature alloys. While some materials offer exceptional performance, they may come with high costs.
Cost Factors in High-Temperature Alloys
The cost of high-temperature alloys is driven by the rarity and cost of raw materials, the complexity of the manufacturing process, and the required post-processing steps. For example, nickel-based superalloys are more expensive than iron-based alloys but offer superior performance at high temperatures.
Impact on Design and Production
The cost-performance trade-off must be considered when selecting alloys for specific applications. Engineers and procurement professionals need to weigh the performance benefits of an alloy against its cost to ensure the material is suitable for the intended use.
Alloy Type | Cost | Performance Benefits | Applications |
---|---|---|---|
Nickel-based | High | Excellent high-temperature resistance | Aerospace, power generation |
Iron-based | Moderate | Good general performance | Automotive, industrial |
Cobalt-based | High | Excellent oxidation resistance | Power generation, chemical industries |
How Alloys Respond to Extreme Environments
High-temperature alloys must perform in extreme environments that include not only high heat but also exposure to reactive gases, intense pressures, and mechanical stresses. These alloys are used in environments such as gas turbines, nuclear reactors, and rocket engines, where failure can be catastrophic.
What Happens in Extreme Heat and Pressure?
At elevated temperatures and pressures, high-temperature alloys can undergo significant changes in their properties. These include oxidation, creep, and fatigue, which can all lead to material failure. The ability to withstand such extreme conditions is a key factor in alloy selection and material design.
Importance of Environmental Testing
To ensure high-temperature alloys perform well in extreme conditions, they are subjected to rigorous testing. Environmental testing helps simulate real-world conditions, allowing engineers to identify potential weaknesses and refine the alloy composition accordingly.
Environmental Factor | Impact on Alloy Performance | Testing Methods |
---|---|---|
High Heat | Accelerates oxidation, causes creep | Thermal cycling, oxidation tests |
Pressure | Can lead to deformation or failure | High-pressure testing |
Reactive Gases | Causes corrosion and material degradation | Corrosion resistance tests |
Alloy Design: The Role of Composition in Overcoming Challenges
The composition of high-temperature alloys plays a pivotal role in addressing challenges like oxidation resistance, creep resistance, and thermal stability. Manufacturers continuously modify alloy compositions to improve performance.
Role of Alloying Elements
Elements like chromium, molybdenum, and tungsten are commonly used to improve various properties of high-temperature alloys. Chromium, for example, enhances oxidation resistance, while molybdenum improves creep resistance. The careful selection of these elements allows engineers to design alloys that meet the specific demands of each application.
Element | Purpose in High-Temperature Alloys | Common Applications |
---|---|---|
Chromium | Enhances oxidation resistance | Aerospace, power generation |
Molybdenum | Improves creep resistance | Automotive, industrial applications |
Tungsten | Improves high-temperature strength | Aerospace, military |
The Role of Research and Innovation in Overcoming Challenges
The challenges associated with high-temperature alloys have led to ongoing research and innovation in alloy development. Universities, research institutions, and industries collaborate to improve the properties of these materials.
Ongoing Research and Development
Research into high-temperature alloys focuses on enhancing material properties like thermal stability, creep resistance, and oxidation resistance. New alloy compositions and processing techniques are constantly being tested to find solutions to these challenges.
Emerging Trends in Alloy Innovations
Emerging trends include the use of advanced manufacturing techniques such as additive manufacturing, which can help produce complex alloy parts with reduced waste and improved performance. Furthermore, the development of hybrid alloys, combining metallic and ceramic materials, is also a promising area of innovation.
Research Area | Focus | Benefits |
---|---|---|
Alloy Composition | Improving performance through material design | Enhanced thermal stability and creep resistance |
Advanced Manufacturing | Additive manufacturing, powder metallurgy | Cost reduction, customized part design |
Hybrid Alloys | Combining metals and ceramics | Improved high-temperature performance |
Testing Methods for High-Temperature Alloys
Testing is an essential part of the development and validation of high-temperature alloys. These tests simulate real-world conditions and help ensure the alloy will perform as expected in extreme environments.
Common Testing Methods
Testing methods include high-temperature creep testing, oxidation resistance testing, and fatigue testing. These tests are performed in controlled environments to replicate the conditions the alloys will face during use.
Importance of Testing Standards
Standardized testing methods are crucial to ensuring that high-temperature alloys meet the necessary performance criteria. These standards provide a benchmark for manufacturers and help ensure that alloys are reliable and effective in their intended applications.
Test Type | Purpose | Common Methods |
---|---|---|
Creep Testing | Measures the material’s deformation under stress at high temperatures | ASTM E139 |
Oxidation Resistance | Measures how well the alloy resists oxidation | ASTM G96 |
Fatigue Testing | Measures the material’s ability to withstand cyclic loading | ASTM E466 |
Real-World Applications of High-Temperature Alloys
High-temperature alloys are used in a wide range of industries, from aerospace to power generation. These materials must meet the specific demands of each sector to ensure safety, efficiency, and performance.
Case Studies of High-Temperature Alloy Applications
In aerospace, high-temperature alloys are critical for turbine engines, where they must withstand temperatures in excess of 1,000°C. In power generation, alloys are used in gas turbines that operate at temperatures of 900°C or higher.
Evolving Use in Modern Technologies
The use of high-temperature alloys continues to evolve as industries demand materials that can operate at higher temperatures and more extreme conditions. This trend is driving innovation in alloy design and manufacturing processes.
Industry | Applications | Temperature Range |
---|---|---|
Aerospace | Turbine blades, jet engines | 600–1,200°C |
Power Generation | Gas turbines, heat exchangers | 700–1,000°C |
Automotive | Exhaust systems, turbochargers | 400–800°C |
How Companies Overcome Alloy Challenges
To overcome the challenges associated with high-temperature alloys, companies employ a variety of strategies, from improving manufacturing techniques to developing new alloy compositions.
Solutions Employed by Manufacturers
Manufacturers use advanced processing techniques, including additive manufacturing and advanced casting methods, to overcome challenges like oxidation and creep resistance. Research into new alloy compositions and hybrid materials is also helping improve performance.
Successful Product Development
Companies that invest in research and development can often produce alloys that offer better performance while reducing costs. Case studies of companies successfully overcoming alloy challenges demonstrate the importance of innovation in this field.
Company | Solution Used | Outcome |
---|---|---|
General Electric | Development of advanced alloys | Improved turbine efficiency |
Rolls-Royce | Hybrid material research | Enhanced high-temperature resistance |
Sustainability in High-Temperature Alloy Production
The production of high-temperature alloys can have significant environmental impacts, from raw material extraction to energy consumption during manufacturing.
Environmental Impact
Manufacturing high-temperature alloys requires energy-intensive processes and the use of rare or hard-to-source materials. This can contribute to a larger carbon footprint for companies that rely heavily on these materials.
Sustainable Practices
To address environmental concerns, companies are increasingly focusing on sustainable practices, such as recycling alloys and reducing waste in the manufacturing process. Moreover, advancements in material science are leading to the development of more sustainable alloy compositions.
Practice | Impact on Sustainability | Example |
---|---|---|
Recycling | Reduces raw material consumption | Recycling of titanium alloys |
Energy Efficiency | Lowers carbon footprint | Use of renewable energy in production processes |
Waste Reduction | Minimizes environmental impact | Zero-waste manufacturing initiatives |
Conclusion: The Future of High-Temperature Alloys
The future of high-temperature alloys is filled with potential. As industries continue to demand higher performance and greater sustainability, the development of new alloys and advanced manufacturing processes will play a critical role in shaping the next generation of materials. By overcoming current challenges and embracing innovation, companies can continue to push the boundaries of what’s possible in high-temperature applications.
FAQ Section
What is a high-temperature alloy, and why are they important?
High-temperature alloys are materials designed to withstand extreme heat and pressure. They are crucial in industries like aerospace, automotive, and energy production, where components must endure high temperatures without failing.
What are the main challenges in high-temperature alloys?
The main challenges include oxidation resistance, creep and fatigue resistance, thermal stability, manufacturing difficulties, and balancing cost with performance.
How do high-temperature alloys perform under extreme heat and pressure?
These alloys maintain their strength and stability at high temperatures and pressures, but they can still experience oxidation, creep, and fatigue if not carefully designed.
How are high-temperature alloys tested for performance and durability?
Alloys are tested using methods like creep testing, oxidation resistance testing, and fatigue testing. These tests simulate real-world conditions to ensure the alloys will perform effectively in extreme environments.
What industries use high-temperature alloys, and for what purposes?
High-temperature alloys are used in aerospace, power generation, automotive, and other industries for components like turbine blades, gas turbines, and exhaust systems. These alloys help ensure performance and durability under extreme conditions.