High-temperature alloys play a crucial role in industries where performance, durability, and safety are non-negotiable. These specialized materials are designed to withstand extreme conditions, making them essential in sectors like aerospace, automotive, and power generation. In this article, we’ll dive deep into the properties of high-temperature alloys, supported by real-world case studies. We’ll explore how these alloys perform under stress, their critical applications, and the challenges that come with using them. But here’s the kicker—understanding their properties and applications can help businesses in these industries optimize performance and increase efficiency. So, let’s dive in and explore what makes these alloys indispensable!
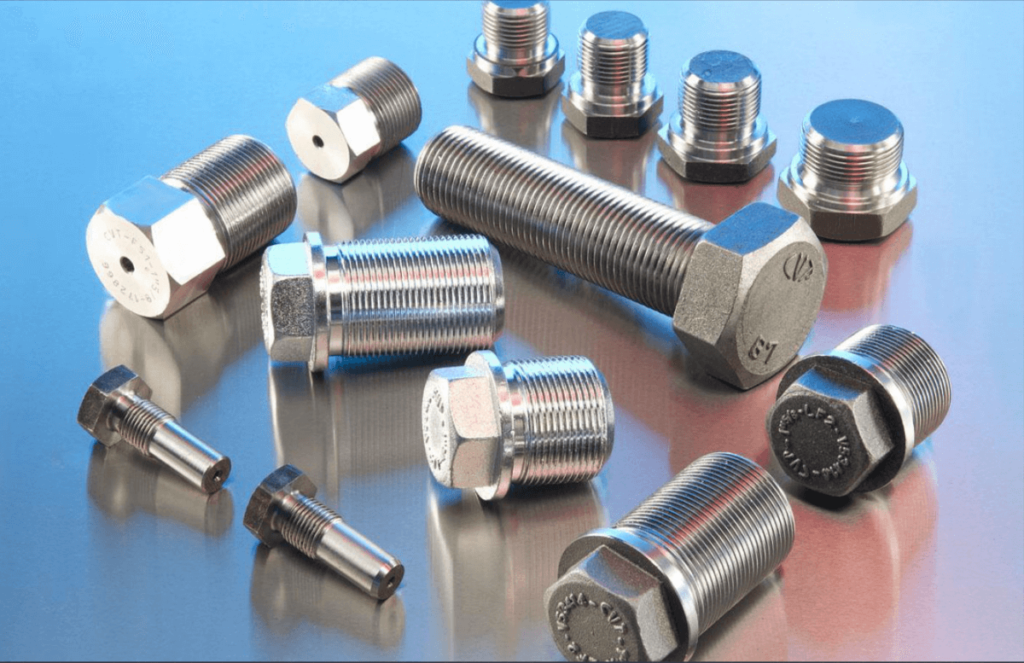
1. Introduction to High-Temperature Alloys
High-temperature alloys are materials engineered to maintain their mechanical properties even when subjected to elevated temperatures. These alloys are often used in high-performance applications where extreme heat and stress are part of the regular operating conditions. From jet engines to power plant turbines, high-temperature alloys are critical components that ensure the safety and efficiency of industrial systems.
What makes these alloys special? They exhibit remarkable strength, resistance to thermal expansion, and excellent durability at high temperatures. This is why industries like aerospace, automotive, and energy rely on them for critical parts like turbine blades, exhaust systems, and heat exchangers.
In the following sections, we’ll uncover the specific properties of high-temperature alloys and how they perform in demanding environments. Ready for the good part? Let’s get into the details of what high-temperature alloys are and why they matter.
2. What Are High-Temperature Alloys?
High-temperature alloys are materials specifically designed to perform in environments with extreme heat. These alloys are typically composed of elements like nickel, cobalt, and titanium, which give them their unique resistance to heat, corrosion, and thermal fatigue.
Here’s the deal: High-temperature alloys are classified into different categories based on their composition and the temperature range they can withstand. For example, nickel-based alloys are some of the most widely used due to their superior high-temperature strength and resistance to oxidation and corrosion. Titanium alloys are favored for their lightweight yet durable properties, making them ideal for applications in aerospace.
The ability to maintain structural integrity at high temperatures is what sets these alloys apart from regular metals. You might be wondering, how do these alloys stand up to the intense conditions of jet engines or power plant turbines? Let’s explore their specific properties and performance in real-world applications.
Alloy Type | Composition | Common Applications | Max Operating Temperature (°C) |
---|---|---|---|
Nickel-Based | Nickel, chromium | Jet engines, turbines | 1,000-1,200 |
Titanium-Based | Titanium, aluminum | Aerospace, automotive | 500-600 |
Cobalt-Based | Cobalt, chromium | Power generation, heat exchangers | 800-1,000 |
3. Why Are High-Temperature Alloys Important?
So, why do high-temperature alloys matter? The answer is simple: they are essential for maintaining efficiency and safety in high-performance environments. In industries like aerospace, automotive, and energy, the performance of a system is directly tied to the quality of the materials used.
For example, in aerospace applications, the turbines in jet engines are exposed to extreme temperatures. These engines need alloys that can resist oxidation and maintain their strength even when operating at over 1,000°C. Without high-temperature alloys, jet engines wouldn’t be able to achieve the efficiency and power necessary for modern air travel.
Similarly, power plants rely on these alloys in their turbines and heat exchangers to convert heat into energy without compromising on efficiency or safety. Without these specialized materials, power generation would be far less reliable and more prone to failure.
This is where it gets interesting: these alloys are not just important for maintaining current technology but are also driving innovation in emerging fields like renewable energy and advanced manufacturing. Let’s look at how high-temperature alloys perform in some of the most demanding industries.
4. The Properties of High-Temperature Alloys
High-temperature alloys are engineered with specific properties that enable them to perform in extreme conditions. Some of these key properties include:
- Heat Resistance and Stability: High-temperature alloys maintain their mechanical properties at elevated temperatures, which is critical in applications where parts are subjected to heat for extended periods.
- Mechanical Strength: These alloys exhibit high tensile strength, allowing them to bear heavy loads without deforming, even at high temperatures.
- Corrosion Resistance: Exposure to high heat often leads to oxidation and corrosion. High-temperature alloys are designed to resist these effects, extending the lifespan of components in harsh environments.
- Thermal Expansion: These alloys are engineered to have controlled thermal expansion, ensuring that parts fit together properly even when subjected to significant temperature changes.
You may be wondering, how do these properties translate into real-world applications? Let’s take a look at some case studies that illustrate the importance of these properties.
5. Case Study 1: Aerospace Industry and High-Temperature Alloys
In the aerospace industry, high-temperature alloys play a critical role in the performance and safety of jet engines. These engines must operate at extreme temperatures to provide thrust, making materials like nickel-based alloys indispensable. One example of a high-performance alloy used in aerospace is the Inconel family of alloys, which is commonly used in turbine blades and exhaust systems.
Here’s the kicker: Inconel alloys can withstand temperatures exceeding 1,000°C without losing strength or becoming brittle. This property is essential for jet engines, where high temperatures are generated during combustion. Without high-temperature alloys, the components in the engine would fail under the stress of these extreme conditions.
Case studies have shown that high-temperature alloys improve engine performance, reduce maintenance costs, and increase the lifespan of engine components. What’s the real story? High-temperature alloys are directly responsible for making air travel safer and more efficient.
Alloy Type | Application | Max Operating Temperature (°C) | Common Aerospace Uses |
---|---|---|---|
Inconel | Turbine blades | 1,000-1,200 | Jet engines, heat exchangers |
Hastelloy | Exhaust systems | 1,200-1,400 | Jet engines, fuel systems |
Titanium Alloys | Aircraft structures | 500-600 | Fuselages, wings |
6. Case Study 2: High-Temperature Alloys in Automotive Engineering
The automotive industry also relies heavily on high-temperature alloys, particularly in the manufacturing of engine components and exhaust systems. High-performance alloys like Inconel and titanium alloys are used in applications such as exhaust valves, turbochargers, and catalytic converters.
What’s the deal? These components are exposed to extreme heat and pressure during engine operation. Without high-temperature alloys, the lifespan of these components would be drastically reduced, leading to performance issues and higher maintenance costs.
The automotive sector has seen significant improvements in both efficiency and emissions thanks to the use of these advanced materials. Ready for the good part? Case studies show that the use of high-temperature alloys in automotive engines can improve fuel efficiency and reduce carbon emissions by enabling better engine performance at higher temperatures.
Alloy Type | Application | Max Operating Temperature (°C) | Common Automotive Uses |
---|---|---|---|
Inconel | Turbochargers | 1,000-1,200 | Turbochargers, valves |
Titanium Alloys | Exhaust systems | 600-800 | Exhaust valves, pipes |
Stainless Steel | Engine components | 800-1,000 | Pistons, cylinder heads |
7. Case Study 3: High-Temperature Alloys in Power Generation
Power generation plants depend on high-temperature alloys to ensure the efficient conversion of heat into electricity. Components like turbine blades, heat exchangers, and boiler tubes are subjected to extremely high temperatures and need alloys that can withstand both heat and stress over long periods of time.
This is where it gets interesting: High-temperature alloys, particularly those based on nickel and cobalt, are ideal for use in power plant turbines, where temperatures can reach up to 1,100°C. The ability of these alloys to maintain strength and resist corrosion ensures that turbines operate at maximum efficiency without the need for frequent repairs.
What’s the takeaway? The reliability of these alloys directly impacts the performance and longevity of power generation plants, reducing downtime and maintenance costs. Case studies show that power plants using high-temperature alloys enjoy higher energy outputs and reduced operational costs.
Alloy Type | Application | Max Operating Temperature (°C) | Common Power Plant Uses |
---|---|---|---|
Inconel | Turbine blades | 1,000-1,200 | Turbines, heat exchangers |
Hastelloy | Heat exchangers | 1,200-1,400 | Boiler tubes, valves |
Cobalt Alloys | Power plant systems | 800-1,000 | Turbines, combustion chambers |
8. How High-Temperature Alloys Are Manufactured
The production of high-temperature alloys involves specialized manufacturing processes designed to create materials that can withstand extreme conditions. These processes include casting, forging, and powder metallurgy.
But here’s the kicker: Manufacturing high-temperature alloys is complex and requires precise control over factors like temperature, pressure, and chemical composition. Ready for the good part? The use of advanced techniques like electron beam melting allows manufacturers to create alloys with consistent properties that perform reliably under high stress and temperature.
These manufacturing processes also involve extensive testing and quality control to ensure the alloys meet the required performance standards. What’s the real story? High-temperature alloys are carefully crafted to meet the demanding needs of industries like aerospace, automotive, and power generation.
Manufacturing Process | Material Type | Key Features | Applications |
---|---|---|---|
Casting | Nickel-based | High strength, corrosion resistance | Turbine blades, jet engines |
Forging | Titanium | Lightweight, high thermal resistance | Aerospace, automotive |
Powder Metallurgy | Cobalt-based | Fine-grain structure, enhanced durability | Power generation, heat exchangers |
9. The Challenges of Working with High-Temperature Alloys
While high-temperature alloys offer numerous benefits, working with them presents several challenges. These include issues with material deformation, fatigue resistance, and creep under high temperatures.
Here’s the deal: The high strength of these alloys can sometimes lead to brittleness at extremely high temperatures, which can cause components to fail unexpectedly. Additionally, creep, the slow deformation of materials under constant stress, is a significant concern in industries like aerospace and power generation.
What’s the real story? Engineers and manufacturers must carefully select the right alloys and design components to minimize these risks, ensuring that they can operate safely and efficiently over the long term.
Challenge | Impact on Performance | Solution | Industry Impact |
---|---|---|---|
Material Deformation | Reduced component life | Use of alloys with high tensile strength | Aerospace, automotive |
Fatigue Resistance | Component failure under stress | Enhanced alloy treatments | Power generation, aerospace |
Creep | Deformation over time | Improved material design and testing | High-performance industries |
10. The Future of High-Temperature Alloys
The future of high-temperature alloys is filled with innovation and growth. With advancements in additive manufacturing and nanotechnology, we’re seeing the development of alloys that offer even greater performance at higher temperatures.
What’s the good news? The continuous improvement of high-temperature alloys opens up new possibilities for industries that rely on these materials. In aerospace, for example, the development of lighter and stronger alloys will improve fuel efficiency and reduce costs.
Here’s the kicker: The ongoing research and development in high-temperature alloys mean that industries will continue to benefit from improved performance, better material longevity, and more efficient operations in the years to come.
Innovation | Potential Impact | Key Industries Affected |
---|---|---|
Additive Manufacturing | Enhanced material design flexibility | Aerospace, automotive |
Nanotechnology | Increased strength and durability | Power generation, aerospace |
New Alloy Compositions | Improved heat resistance | Energy, automotive, aerospace |
11. How to Choose the Right High-Temperature Alloy for Your Application
Choosing the right high-temperature alloy for your specific application is crucial for ensuring optimal performance and longevity. Here’s the deal: Different alloys offer various strengths, such as heat resistance, fatigue resistance, and corrosion resistance, making it essential to consider the specific requirements of your project.
You might be wondering, how do you choose the right material? It depends on the operating temperature, the stresses the material will face, and its exposure to corrosive elements. By carefully assessing these factors, you can select the alloy that best fits your needs.
Application | Required Properties | Recommended Alloy Type |
---|---|---|
Aerospace | High strength, heat resistance | Inconel, Titanium alloys |
Automotive | Lightweight, corrosion resistance | Titanium, stainless steel |
Power Generation | High heat resistance, durability | Inconel, Cobalt-based alloys |
12. Comparison of High-Temperature Alloys with Other Materials
When compared to other materials like ceramics, polymers, and traditional metals, high-temperature alloys offer superior performance in extreme conditions. This is where it gets interesting: Unlike ceramics, which are often brittle, and polymers, which degrade at high temperatures, high-temperature alloys provide a balance of strength, flexibility, and thermal stability.
What’s the real story? In many applications, high-temperature alloys outperform ceramics and polymers, especially when mechanical strength is required along with heat resistance. They’re also more reliable than traditional metals in environments where temperature fluctuations are extreme.
Material Type | Key Advantages | Key Disadvantages | Ideal Applications |
---|---|---|---|
High-Temperature Alloys | Strength, heat resistance, flexibility | Cost, manufacturing complexity | Aerospace, automotive |
Ceramics | Heat resistance, hardness | Brittle, can crack under stress | High-temperature applications |
Polymers | Lightweight, flexible | Degrades at high temperatures | Low to medium temperature uses |
13. Cost Considerations in High-Temperature Alloys
Here’s the deal: High-temperature alloys can be more expensive than other materials due to the complex manufacturing processes involved in their production. Factors like material selection, manufacturing techniques, and quality control can drive up costs.
But here’s the kicker: The investment in high-temperature alloys pays off in the long run due to their superior performance and durability, which can reduce maintenance and operational costs. When selecting an alloy, it’s crucial to balance cost with performance to ensure you’re getting the best value for your investment.
Alloy Type | Cost Range | Key Benefits | Long-Term Value |
---|---|---|---|
Nickel Alloys | High | Heat resistance, strength | Reduced maintenance costs |
Titanium Alloys | Moderate to High | Lightweight, corrosion resistance | Fuel efficiency in aerospace |
Cobalt Alloys | Moderate | Durability, corrosion resistance | Reliable performance in power generation |
14. Common Misconceptions About High-Temperature Alloys
There are several misconceptions about high-temperature alloys, especially concerning their cost and performance. You might be wondering, do these alloys really offer enough benefits to justify the price?
What’s the real story? Many people assume that all alloys are created equal and that high-temperature alloys are simply more expensive without offering much extra value. However, the reality is that these alloys provide unique advantages in performance, safety, and longevity that can significantly reduce costs in industries like aerospace and power generation.
Misconception | Truth | Impact on Industry |
---|---|---|
High-temperature alloys are too expensive | They provide long-term savings due to reliability | Reduced operational and maintenance costs |
All alloys are the same | High-temperature alloys are specifically designed for extreme conditions | Increased safety and performance in high-stress environments |
Only aerospace needs high-temperature alloys | Power generation and automotive also rely heavily on high-temperature alloys | Broader application across industries |
15. Conclusion
High-temperature alloys are indispensable materials that play a critical role in industries where performance and safety are paramount. From aerospace to power generation, these alloys ensure that components can withstand the extreme conditions they face. As technology continues to advance, we’ll see even greater innovations in alloy development, offering higher performance and reliability. What’s the real story? Choosing the right high-temperature alloy can lead to significant improvements in performance, efficiency, and safety. The future of high-temperature alloys looks bright, and the industries that rely on them will continue to see advancements that make their operations even more efficient.
FAQ Section
Q1: What are high-temperature alloys?
High-temperature alloys are specially engineered materials designed to perform in environments exposed to extreme heat. They offer high strength, corrosion resistance, and excellent mechanical properties even at elevated temperatures.
Q2: How are high-temperature alloys manufactured?
High-temperature alloys are manufactured using casting, forging, and powder metallurgy techniques. These processes ensure the alloys meet the performance standards required for extreme temperature applications.
Q3: Why are high-temperature alloys important in aerospace?
In aerospace, high-temperature alloys are crucial for the performance of jet engines, where components must withstand intense heat. These alloys maintain strength and resist corrosion, ensuring safety and efficiency in flight.
Q4: How do high-temperature alloys differ from other materials like ceramics or polymers?
Unlike ceramics, which are brittle, and polymers, which degrade under heat, high-temperature alloys provide a balance of strength, flexibility, and thermal stability, making them ideal for high-performance applications.
Q5: What challenges do engineers face when working with high-temperature alloys?
Engineers face challenges like material deformation, fatigue resistance, and creep under high temperatures. They must carefully select and design alloys to minimize these risks and ensure optimal performance over time