Heat-resistant metals have seen a significant evolution over the years. These metals, known for their ability to withstand extreme temperatures, are now integral to several high-demand industries, including aerospace, automotive, and electronics. With technological advancements, the properties of these metals have undergone continuous improvement. From innovations in alloys to the development of advanced manufacturing techniques, the heat-resistant metals of today are far superior to those used in the past. Let’s dive into these recent innovations and explore how they are shaping the future of industries that rely on these materials.
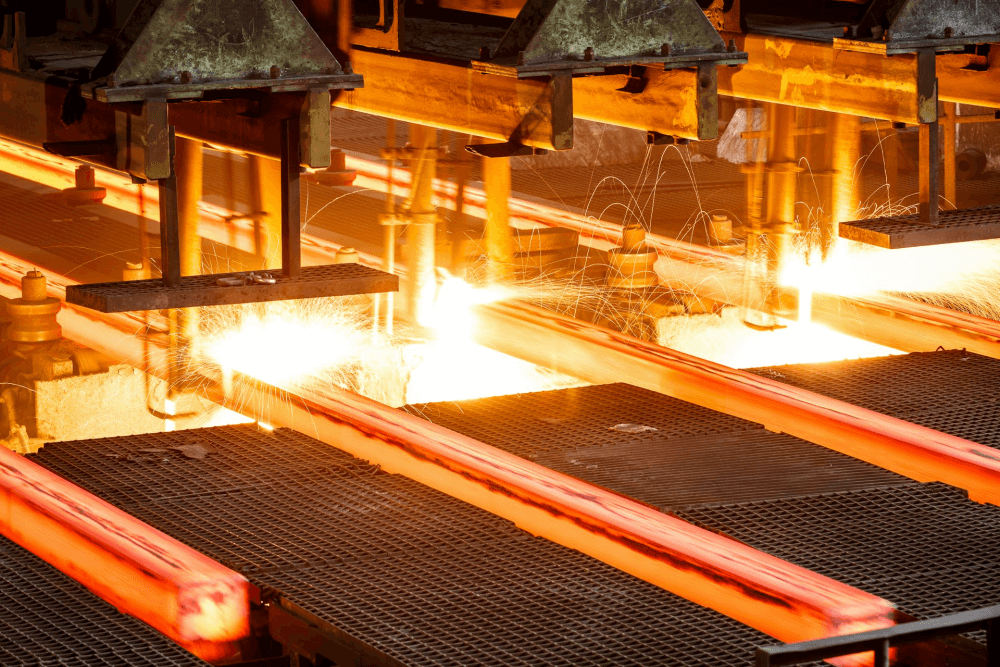
1. Introduction to Heat-Resistant Metals
Heat-resistant metals are critical materials that help industries operate efficiently in high-temperature environments. They’re used in applications that require metals to perform under stress, temperature fluctuations, and potential corrosion, such as in engines, turbines, and high-performance machinery. These metals include alloys of titanium, tungsten, and nickel, which can endure extreme conditions without losing their strength or performance.
What’s the real story? As industries demand more advanced and reliable materials, recent innovations in heat-resistant metals have focused on enhancing their thermal properties, resistance to oxidation, and overall strength. These innovations are essential for pushing the boundaries of industrial design, improving safety, and enhancing the longevity of machinery.
Heat-resistant metals are becoming more efficient, and the latest innovations aim to make them more durable, cost-effective, and versatile. Industries that rely on high temperatures now have access to improved alloys that can better withstand the stresses of their environments.
2. Understanding the Properties of Heat-Resistant Metals
Heat-resistant metals are defined by their ability to maintain structural integrity even at elevated temperatures. But here’s the kicker—what makes a metal heat-resistant isn’t just the base material but also how it’s treated and processed. A typical heat-resistant metal should have a high melting point, resistance to thermal expansion, and the ability to resist oxidation.
Common materials like titanium, tungsten, and certain types of stainless steel alloys are used because they possess the unique combination of strength and durability required for extreme environments. These metals can withstand temperatures exceeding 1,000°C without weakening, which is essential for industries like aerospace and energy production.
In terms of composition, many heat-resistant alloys are made from a combination of metals that work together to enhance the material’s properties. For example, titanium alloys are used in the aerospace industry due to their ability to resist corrosion and heat, while nickel-based alloys are used in power plants for their high-temperature tolerance.
3. Recent Breakthroughs in Heat-Resistant Alloys
Ready for the good part? Recent breakthroughs in heat-resistant alloys are making significant waves across industries. New formulations of titanium, nickel, and cobalt alloys are being developed to offer even higher resistance to temperature and mechanical stress. These materials are also becoming more lightweight and cost-effective, making them ideal for aerospace and automotive applications.
Recent advancements also include the integration of nanotechnology in heat-resistant alloys. By manipulating the microstructure of these materials, engineers can significantly improve their thermal stability and performance under extreme conditions. These innovations make it possible for metals to handle even greater temperature gradients, something that was previously a limitation.
As industries demand more from their heat-resistant materials, these innovations are helping them to achieve higher levels of efficiency and performance, enabling manufacturers to produce lighter, stronger, and more durable components.
Metal Alloy | Maximum Temperature (°C) | Common Applications | Properties |
---|---|---|---|
Titanium Alloys | 1,200°C | Aerospace, Chemical Plants | Lightweight, Corrosion-Resistant |
Nickel Alloys | 1,300°C | Power Generation, Turbines | High-Temperature Resistance |
Cobalt Alloys | 1,400°C | Industrial Gas Turbines | Strong, Wear-Resistant |
4. The Role of Heat-Resistant Metals in Aerospace
The aerospace industry demands the highest performance from materials. But here’s the kicker—heat-resistant metals are a crucial part of this equation. Aircraft and spacecraft components need to be able to withstand extreme heat generated during flight and re-entry without compromising structural integrity. Heat-resistant metals like titanium alloys are often used in engine components and airframes because they provide the necessary strength and durability at high temperatures.
Heat-resistant alloys in aerospace also contribute to improving fuel efficiency. By using lighter materials that can handle higher temperatures, aircraft can be designed to operate more efficiently, reducing fuel consumption and emissions. These advancements are essential as the aerospace industry moves toward more sustainable and eco-friendly practices.
5. Heat-Resistant Metals in Automotive Engineering
What’s the real story? In automotive engineering, heat-resistant metals are essential for performance engines, exhaust systems, and catalytic converters. These components need to withstand the intense heat generated during vehicle operation without degrading or losing efficiency. The rise in high-performance sports cars and electric vehicles has also led to a surge in demand for advanced heat-resistant alloys that can improve engine performance and extend component lifespans.
Innovations in automotive engineering have led to the development of alloys that combine heat resistance with lightweight properties, which enhances fuel efficiency and overall vehicle performance. These metals are particularly important for turbochargers and engine blocks, where maintaining high performance at extreme temperatures is crucial.
6. The Impact of Heat-Resistant Metals in Electronics and Energy
Heat-resistant materials are now making waves in the world of electronics and energy. Here’s the twist—heat management in electronics has become more critical than ever. With electronics becoming smaller and more powerful, managing heat within devices like smartphones, laptops, and power electronics is a growing concern. Heat-resistant metals, especially those used in heat sinks and cooling systems, play a vital role in preventing overheating.
In energy sectors, heat-resistant metals are critical for power generation, particularly in nuclear reactors and renewable energy technologies. These alloys ensure that equipment can operate at high temperatures without compromising safety or efficiency. With the push towards more sustainable energy solutions, these innovations are paving the way for more reliable and efficient energy production.
Industry | Applications | Metal Used | Key Property |
---|---|---|---|
Electronics | Heat Sinks, Circuit Boards | Copper, Aluminum | High Thermal Conductivity |
Energy Production | Nuclear Reactors, Power Plants | Cobalt, Nickel | High-Temperature Resistance |
Renewable Energy | Solar Panels, Wind Turbines | Titanium Alloys | Corrosion-Resistant |
7. Manufacturing Techniques for Heat-Resistant Metals
What’s the real story? The evolution of manufacturing techniques has been integral to the development of advanced heat-resistant metals. Modern processes such as powder metallurgy and additive manufacturing (3D printing) have opened new doors for creating highly specialized heat-resistant components that were once impossible to make. These methods allow for the production of intricate designs and more efficient materials.
Powder metallurgy, in particular, is used to create alloys with uniform properties, which improves the overall quality and performance of heat-resistant metals. Additive manufacturing, on the other hand, is allowing for the creation of complex geometries that can better withstand heat and stress, which is ideal for applications in aerospace and energy sectors.
8. Why Are Recent Innovations Important for the Future?
Recent innovations in heat-resistant metals are crucial for meeting the growing demands of industries around the world. These advancements enable companies to build products that are not only stronger and more durable but also lighter and more energy-efficient. This is where it gets interesting—innovations in heat-resistant metals contribute to the development of more sustainable industrial processes, which is a priority for many organizations aiming to reduce their environmental impact.
Moreover, these innovations help in reducing costs over time. While the initial investment in new materials and manufacturing techniques may be high, the long-term savings through improved product performance and reduced maintenance costs make these innovations worthwhile.
9. How Heat-Resistant Metals Are Tested and Evaluated
Ready for the good part? Testing and evaluation are essential steps in ensuring that heat-resistant metals meet the necessary standards for high-performance applications. Metals are tested for their ability to withstand thermal cycling, oxidation, and mechanical stress at high temperatures. These tests simulate real-world conditions to verify whether a metal can maintain its integrity in challenging environments.
Furthermore, manufacturers follow stringent regulations and industry standards to ensure that heat-resistant metals perform reliably over time. This ensures safety in industries like aerospace and automotive, where equipment failure due to material degradation can have serious consequences.
10. Innovations in Heat-Resistant Coatings and Surface Treatments
Recent innovations aren’t just happening at the base metal level. Surface treatments and coatings have also undergone significant advancements. Heat-resistant coatings, such as thermal barrier coatings, are used to protect metals from oxidation and thermal damage, extending the lifespan of critical components.
These coatings are applied to materials exposed to extreme conditions, such as turbine blades and engine parts, to ensure they perform optimally for longer. The ability to improve the thermal stability of components through surface treatment allows for more efficient designs and better overall performance.
Coating Type | Application | Benefits |
---|---|---|
Thermal Barrier Coating | Gas Turbines, Jet Engines | Increases Heat Resistance, Longevity |
Ceramic Coating | High-Temperature Surfaces | Reduces Oxidation, Increases Durability |
Nickel Plating | Industrial Equipment | Enhances Corrosion Resistance |
11. Applications of Recent Innovations in Heat-Resistant Metals
Ready for the good part? The applications of these advanced heat-resistant metals are vast and varied. Industries such as aerospace, automotive, power generation, and defense rely heavily on these materials to maintain high performance in their equipment. These innovations have led to the development of lighter, stronger, and more durable components that enhance overall efficiency and reduce the risk of failure.
From high-performance engines to space exploration, these metals are enabling the creation of more advanced technologies. As the demand for reliability and efficiency increases, the applications for these metals are only going to expand further.
12. Challenges in the Development and Use of Heat-Resistant Metals
What’s the catch? While the advancements in heat-resistant metals are promising, the development of these materials comes with its own set of challenges. High production costs remain a significant barrier to widespread adoption of some of the more advanced alloys. Additionally, scaling up new manufacturing techniques, like additive manufacturing, presents challenges in terms of consistency and cost-efficiency.
Moreover, achieving the desired heat resistance in large-scale applications can be tricky. Even with recent innovations, many manufacturers are still working on improving the scalability of these materials for mass production.
13. The Future of Heat-Resistant Metals: What’s Next?
What’s next for heat-resistant metals? The future of these materials looks bright, with ongoing research focused on improving their performance even further. New materials with higher temperature tolerances, better corrosion resistance, and more efficient production methods are on the horizon. Innovations in nanotechnology, along with artificial intelligence in material discovery, will continue to push the boundaries of what’s possible.
Moreover, the development of hybrid materials, which combine different properties to meet specific industrial needs, will open up new avenues for heat-resistant materials in areas such as advanced manufacturing and energy storage.
14. How Companies Are Adopting Heat-Resistant Metal Innovations
As industries embrace these innovations, companies are reaping the benefits of adopting advanced heat-resistant metals in their products. From aerospace giants to energy corporations, the adoption of these materials is helping businesses maintain their competitive edge. The ability to offer products that are more durable, energy-efficient, and cost-effective gives these companies a distinct advantage in the marketplace.
Real-world examples of companies that have adopted heat-resistant metal innovations include major aerospace manufacturers who use advanced alloys in turbine engines, and automotive companies utilizing lightweight heat-resistant metals to improve fuel efficiency.
15. Conclusion: The Significance of Recent Innovations in Heat-Resistant Metals
In conclusion, recent innovations in the properties of heat-resistant metals are driving forward significant advancements in multiple industries. These materials are becoming stronger, lighter, and more efficient, paving the way for future technological innovations. As industries continue to demand more from their materials, heat-resistant metals will play an even greater role in shaping the future of manufacturing, aerospace, energy, and beyond.
FAQ Section
Q1: What are heat-resistant metals?
Heat-resistant metals are alloys or materials specifically designed to maintain their mechanical properties and structure at high temperatures. These metals are commonly used in industries where parts are exposed to extreme heat, such as aerospace, automotive, and energy production.
Q2: How do heat-resistant metals work?
Heat-resistant metals work by maintaining their strength, stability, and durability even under high-temperature conditions. Their ability to resist thermal expansion and corrosion ensures they perform optimally in extreme environments.
Q3: What are some examples of heat-resistant metals?
Examples of heat-resistant metals include titanium, tungsten, nickel-based alloys, and steel alloys. These metals are known for their high melting points, thermal stability, and resistance to oxidation.
Q4: How are heat-resistant metals tested for quality?
Heat-resistant metals are tested through various methods, such as thermal cycling, tensile strength tests, and high-temperature exposure tests. These tests ensure that the metals can withstand extreme conditions without losing their integrity.
Q5: Why are innovations in heat-resistant metals important for industries?
Innovations in heat-resistant metals lead to improved performance, efficiency, and safety in industrial applications. These advancements can reduce production costs, enhance product longevity, and enable the development of new technologies that require high-temperature resistance.