High-temperature alloys are materials designed to withstand extreme conditions, such as intense heat, pressure, and harsh chemical environments. These alloys play a crucial role in various industries by enhancing performance, safety, and efficiency in applications where traditional metals may fail. From aerospace to power generation, the utility of high-temperature alloys spans multiple sectors. In this article, we will explore what high-temperature alloys are, why they are essential, and which industries are taking full advantage of their properties. Ready for the good part? Let’s dive into the key industries utilizing high-temperature alloys and why they’re so important.
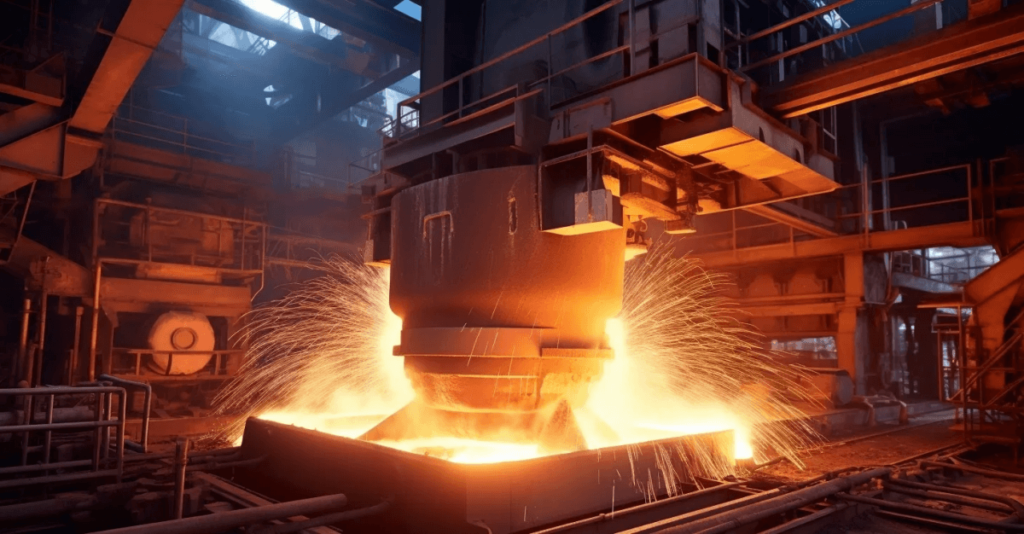
1. Introduction to High-Temperature Alloys
High-temperature alloys are critical materials used in industries requiring components to function in high-heat and high-stress environments. They are specifically designed to maintain strength, resistance to corrosion, and overall durability under conditions where most materials would fail. What’s the real story? These alloys play an indispensable role in ensuring the reliability and safety of industrial operations. Let’s explore why these alloys are such a game-changer.
These alloys typically consist of metals such as nickel, cobalt, and iron, and their compositions are engineered to withstand prolonged exposure to elevated temperatures. Whether it’s in aerospace, energy generation, or automotive manufacturing, high-temperature alloys serve as a reliable solution to ensure equipment doesn’t degrade under intense conditions.
Table 1: Key Properties of High-Temperature Alloys
Property | Description |
---|---|
High melting point | Ensures materials remain intact at high temperatures |
Corrosion resistance | Protects against oxidation and chemical damage |
Strength at temperature | Maintains mechanical strength at elevated temperatures |
Creep resistance | Resists deformation under constant stress over time |
The high-performance capabilities of high-temperature alloys are essential to industries like aerospace, where every component needs to operate efficiently and without failure. In the next sections, we’ll delve deeper into the specific industries benefiting from these alloys.
2. What Are High-Temperature Alloys?
High-temperature alloys are engineered to withstand temperatures that would cause most metals to soften or degrade. But here’s the kicker – these materials don’t just resist high heat. They are also designed to endure chemical reactions, mechanical stresses, and thermal cycling. Common examples include nickel-based superalloys, which are used for turbine blades in jet engines and gas turbines.
The composition of these alloys is crucial. Metals like nickel and cobalt offer the necessary strength and oxidation resistance at elevated temperatures, while additives like chromium enhance corrosion resistance. What’s more? These alloys are specifically tailored for each industry’s needs, ensuring that performance is maximized across various applications.
Table 2: Common High-Temperature Alloys
Alloy Type | Composition | Common Uses |
---|---|---|
Nickel-based alloys | Nickel, chromium, iron | Jet engines, power turbines, heat exchangers |
Cobalt-based alloys | Cobalt, chromium, nickel | Chemical processing, aerospace applications |
Iron-based alloys | Iron, chromium, nickel | Automotive, industrial machinery |
These alloys offer unparalleled benefits, making them indispensable for industries operating under extreme conditions. The real magic of these alloys is in their ability to keep working long after traditional materials would have failed.
3. Why Are High-Temperature Alloys Important in Manufacturing?
High-temperature alloys provide essential benefits in manufacturing processes that involve intense heat. Ready for the good part? These materials maintain performance and reliability, even under extreme conditions. In industries such as power generation, aerospace, and automotive manufacturing, the need for materials that can withstand high temperatures while maintaining strength and durability is crucial.
In power plants, for example, turbines and reactors operate at extremely high temperatures. High-temperature alloys ensure that components don’t fail under pressure, thus contributing to the safety and efficiency of the plant. These alloys also help in reducing downtime by increasing the lifespan of critical components, which ultimately lowers maintenance costs and enhances productivity.
Table 3: Applications of High-Temperature Alloys in Manufacturing
Industry | Application | Benefit |
---|---|---|
Power generation | Turbines, reactors, heat exchangers | Higher efficiency, longer lifespan |
Aerospace | Jet engine components, turbines, exhaust systems | Improved fuel efficiency, safety |
Automotive | Engine parts, exhaust systems | Enhanced performance and longevity |
What’s the real story? Without high-temperature alloys, these industries would face frequent breakdowns and high operational costs. These materials are integral to maintaining seamless operations in high-stress environments.
4. Industries Utilizing High-Temperature Alloys
The versatility of high-temperature alloys means they are used across a wide array of industries. What’s the real story? High-temperature alloys are critical to industries that operate under extreme conditions, such as aerospace, power generation, automotive manufacturing, and more. In this section, we’ll take a closer look at these industries and their applications of high-temperature alloys.
High-temperature alloys are used in aerospace for engine components, in power plants for turbines, and in automotive engines for improved performance. The ability of these materials to resist thermal degradation, oxidation, and wear makes them highly valued in any sector where heat is a constant challenge.
Table 4: Top Industries Using High-Temperature Alloys
Industry | Key Applications | Reasons for Use |
---|---|---|
Aerospace | Jet engines, turbine blades, exhaust systems | Heat resistance, strength under pressure |
Power generation | Boilers, turbines, reactors | High efficiency, durability |
Automotive | Engine blocks, exhaust manifolds, catalytic converters | Performance enhancement, heat resistance |
Chemical processing | Reactors, distillation columns, piping systems | Corrosion resistance, high-temperature stability |
High-temperature alloys are crucial for enabling technological advancements in these industries, ensuring that machinery performs at its peak for extended periods.
5. Aerospace and Aviation
Aerospace and aviation industries are some of the most significant consumers of high-temperature alloys. Here’s the kicker – jet engines and turbine systems require materials that can withstand intense heat and pressure. High-temperature alloys, particularly nickel-based superalloys, are used for critical components like turbine blades, which experience extreme thermal loads during flight.
The need for materials that maintain their strength, resistance to corrosion, and overall durability at high temperatures cannot be overstated. These alloys ensure that engines remain operational even under the intense heat generated during takeoff and flight. What’s the real story? Without high-temperature alloys, modern aircraft engines simply wouldn’t perform efficiently.
Table 5: Aerospace Applications of High-Temperature Alloys
Component | Alloy Type | Benefits |
---|---|---|
Turbine blades | Nickel-based superalloys | High strength, oxidation resistance, and longevity |
Exhaust systems | Cobalt-based alloys | Durability under high-heat conditions |
Engine components | Iron-based alloys | Strength at high temperatures and corrosion resistance |
These alloys play a vital role in the development of more efficient, reliable, and safe aerospace technologies.
6. Power Generation and Energy
In the power generation sector, high-temperature alloys are essential for ensuring efficiency and safety. This is where it gets interesting – these alloys are used in turbines, reactors, and boilers, which all operate at elevated temperatures. They prevent material degradation, ensuring that critical equipment doesn’t fail under extreme heat and pressure.
The increased efficiency brought about by high-temperature alloys means that power plants can generate more energy with fewer resources. Ready for the good part? These alloys contribute to the longevity of turbines and reactors, reducing downtime and the need for costly repairs or replacements.
Table 6: Power Generation Applications of High-Temperature Alloys
Component | Alloy Type | Role |
---|---|---|
Gas turbines | Nickel-based alloys | High strength, long lifespan |
Reactors | Cobalt-based alloys | Heat and corrosion resistance |
Boilers | Iron-based alloys | Durability, resistance to thermal cycling |
High-temperature alloys are an essential part of modernizing energy production systems, enabling them to meet the growing demand for reliable and sustainable power generation.
7. Automotive Industry
The automotive industry benefits greatly from high-temperature alloys, particularly for components in engines and exhaust systems. Here’s the kicker – as engines become more powerful and efficient, the need for materials that can withstand higher operating temperatures becomes even more critical. High-temperature alloys improve the performance and durability of components such as exhaust manifolds, engine blocks, and catalytic converters.
By using these alloys, automotive manufacturers can enhance the efficiency of vehicles, reduce emissions, and extend the lifespan of engine components. What’s the real story? Without these alloys, modern automotive engineering would not be able to push the boundaries of performance.
Table 7: Automotive Applications of High-Temperature Alloys
Component | Alloy Type | Benefits |
---|---|---|
Exhaust systems | Nickel-based alloys | Improved performance and reduced emissions |
Engine components | Cobalt-based alloys | Enhanced heat resistance and durability |
Catalytic converters | Iron-based alloys | Corrosion resistance and longevity |
These alloys make it possible for automotive companies to deliver cars with better fuel efficiency and longer-lasting performance.
8. Chemical and Petrochemical Industries
High-temperature alloys are also crucial in the chemical and petrochemical industries, where they are used in reactors, heat exchangers, and piping systems. What’s the real story? These alloys are vital for ensuring that chemical reactions can occur at high temperatures without risking material failure. In petrochemical applications, where corrosive and high-heat environments are common, high-temperature alloys play a key role in maintaining system integrity.
For example, superalloys can withstand the corrosive effects of acids and gases that are often present in petrochemical plants. Ready for the good part? These materials help keep chemical plants running smoothly, reducing downtime and maintenance costs.
Table 8: Chemical and Petrochemical Applications of High-Temperature Alloys
Component | Alloy Type | Benefits |
---|---|---|
Reactors | Nickel-based alloys | High resistance to corrosion and high heat |
Heat exchangers | Cobalt-based alloys | Enhanced durability in harsh environments |
Piping systems | Iron-based alloys | Strength under thermal and chemical stress |
These alloys are key to ensuring the longevity and reliability of petrochemical and chemical plants, where efficiency is crucial.
9. Marine and Naval Industries
The marine and naval industries rely heavily on high-temperature alloys for their durability and resistance to corrosion in saltwater environments. This is where it gets interesting – ship engines, offshore platforms, and other marine components are subject to extreme conditions, including high temperatures and saltwater exposure. High-temperature alloys ensure these components stay intact, providing the necessary strength and resistance to corrosion.
In addition to their heat-resistant properties, these alloys also offer great mechanical strength, ensuring that critical marine components perform as expected under pressure. What’s the real story? These alloys are crucial for maintaining the safety and performance of maritime operations.
Table 9: Marine and Naval Applications of High-Temperature Alloys
Component | Alloy Type | Benefits |
---|---|---|
Marine engines | Nickel-based alloys | Durability, heat resistance, and corrosion resistance |
Offshore platforms | Cobalt-based alloys | Strength in extreme conditions |
Heat exchangers | Iron-based alloys | Resistance to corrosion and thermal cycling |
High-temperature alloys are essential for the development of reliable and efficient marine systems.
10. Other Industries Benefiting from High-Temperature Alloys
High-temperature alloys are not limited to the industries already mentioned. What’s the real story? These materials also benefit sectors like medical devices, military, defense, and semiconductor manufacturing. In the medical field, high-temperature alloys are used for surgical tools, implants, and equipment that require durability and resistance to thermal degradation. Similarly, in defense, high-temperature alloys play a role in weapon systems and military aircraft, ensuring performance and reliability.
Table 10: Additional Applications of High-Temperature Alloys
Industry | Application | Benefit |
---|---|---|
Medical | Surgical tools, implants | Durability and resistance to heat |
Military and defense | Weapon systems, military aircraft | Strength and reliability under extreme conditions |
Semiconductor | Manufacturing equipment | Performance at high temperatures |
These industries are increasingly relying on high-temperature alloys to maintain their operations and ensure product longevity.
11. The Challenges of Using High-Temperature Alloys
High-temperature alloys come with a range of challenges, which are important to consider when implementing them in various industries. Here’s the kicker – one of the biggest challenges is cost. These alloys can be expensive, both in terms of raw materials and manufacturing processes. Additionally, the high-performance characteristics of these alloys make them difficult to fabricate into precise shapes, often requiring specialized equipment.
Another challenge is the potential for long-term degradation. What’s the real story? Over time, even the best alloys may experience wear and tear due to continuous exposure to high temperatures. These factors can lead to increased maintenance and replacement costs.
Table 11: Challenges in Using High-Temperature Alloys
Challenge | Impact |
---|---|
High cost | Increased raw material and manufacturing costs |
Difficult fabrication | Need for specialized manufacturing processes |
Long-term degradation | Potential for wear and maintenance issues |
These challenges must be considered when incorporating high-temperature alloys into manufacturing systems.
12. Future of High-Temperature Alloys
The future of high-temperature alloys is promising. What’s the real story? As industries evolve and technology advances, the demand for more efficient, durable, and heat-resistant materials will only grow. Researchers are working on developing alloys with even better heat resistance, longer lifespan, and higher strength-to-weight ratios. Innovations in alloy compositions will pave the way for more cost-effective solutions in the future.
Table 12: Future Trends in High-Temperature Alloys
Trend | Expected Impact |
---|---|
Advanced compositions | Improved strength and efficiency |
Cost-effective alloys | Lower costs for high-performance applications |
Sustainable materials | Development of environmentally friendly alloys |
As these advancements unfold, high-temperature alloys will continue to play a central role in shaping industries.
13. Key Players in the High-Temperature Alloy Market
The market for high-temperature alloys is driven by a few key players who specialize in the production and innovation of these materials. Here’s the kicker – companies like General Electric, Honeywell, and Carpenter Technology are leading the charge in developing new alloy formulations and meeting the growing demand for heat-resistant materials.
Table 13: Key Players in the High-Temperature Alloy Market
Company | Focus Area | Contribution |
---|---|---|
General Electric | Aerospace, power generation | Development of advanced turbine alloys |
Honeywell | Aerospace, defense | High-performance alloys for engines |
Carpenter Technology | Automotive, industrial | Innovation in corrosion-resistant alloys |
These companies are pushing the boundaries of what’s possible with high-temperature alloys.
14. How Do High-Temperature Alloys Impact Global Industries?
The impact of high-temperature alloys on global industries cannot be overstated. Ready for the good part? These alloys have revolutionized industries by enabling the design and production of more efficient, durable, and powerful systems. As industries around the world continue to demand higher performance from their equipment, high-temperature alloys provide the necessary material properties to meet these needs.
Table 14: Global Impact of High-Temperature Alloys
Industry | Impact |
---|---|
Aerospace | More efficient, reliable engines and turbines |
Power generation | Increased energy output with less resource use |
Automotive | Longer-lasting, high-performance engine parts |
Chemical processing | More reliable reactors and heat exchangers |
High-temperature alloys are playing an ever-growing role in shaping industries across the globe, ensuring that systems run efficiently and safely.
15. Conclusion
In conclusion, high-temperature alloys are indispensable materials for a wide range of industries. What’s the real story? Without these alloys, industries such as aerospace, power generation, and automotive manufacturing would struggle to function efficiently and safely. As technology advances, the demand for these alloys will continue to grow, and innovations will ensure that they remain a key component of industrial success. Ready to explore the possibilities? The future of high-temperature alloys is here.
FAQ Section
Q1: What are high-temperature alloys?\
High-temperature alloys are materials designed to withstand high temperatures while maintaining their strength and durability. They are used in industries like aerospace, power generation, and automotive manufacturing.
Q2: How do high-temperature alloys benefit the aerospace industry?\
In aerospace, high-temperature alloys are used in engines and turbine blades to withstand extreme heat. They improve performance, fuel efficiency, and safety.
Q3: Why are high-temperature alloys used in power generation?\
High-temperature alloys are used in turbines, reactors, and boilers to ensure efficiency, reduce maintenance costs, and extend the lifespan of power generation equipment.
Q4: What challenges do industries face when using high-temperature alloys?\
The main challenges include the high cost of materials, difficult fabrication processes, and the potential for long-term degradation under constant exposure to high temperatures.
Q5: How is the use of high-temperature alloys evolving in the future?\
The future of high-temperature alloys involves advancements in alloy compositions, making them more efficient, cost-effective, and sustainable for emer