Shrinkage in cast metals refers to the reduction in volume that occurs when molten metal cools and solidifies in a mold. The metal contracts as it solidifies, which can lead to defects such as porosity, cracks, and dimensional inaccuracies. Understanding the causes and implications of shrinkage is crucial for manufacturers aiming to produce high-quality castings that meet specifications.
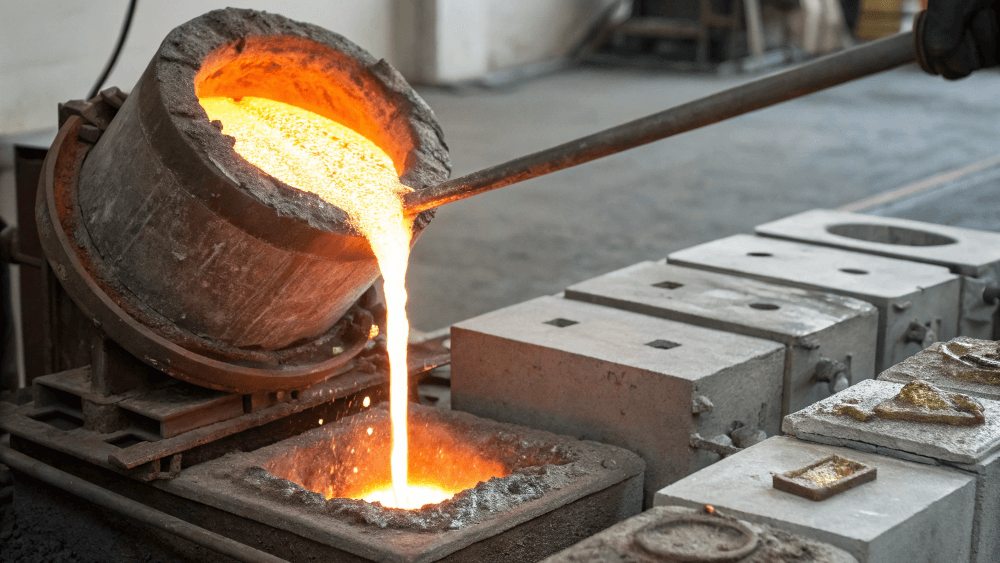
Here’s the kicker: shrinkage isn’t just a random event in the casting process—it’s influenced by several factors, including the alloy composition, cooling rate, and mold design. By understanding these factors, manufacturers can take steps to minimize shrinkage and ensure better casting quality.
Below is a table that breaks down the common causes of shrinkage:
Causes of Shrinkage in Cast Metals
Cause | Description |
---|---|
Alloy Composition | Different alloys shrink at different rates based on their melting points and cooling properties. |
Cooling Rate | Rapid cooling leads to uneven shrinkage, while slow cooling may result in excessive shrinkage. |
Mold Material | The type of mold material affects how heat is absorbed and how evenly the metal solidifies. |
1. What is Shrinkage in Cast Metals?
Shrinkage in cast metals occurs when the molten metal cools and solidifies, reducing in volume and potentially creating voids or gaps in the final product. These voids, or porosity, can cause weakness in the material. Additionally, uneven shrinkage can result in cracks or dimensional inaccuracies.
What’s the real story? If shrinkage isn’t properly managed, it can lead to defective castings that fall short of specifications, affecting the overall quality and reliability of the metal product. Manufacturers need to be aware of the causes and take proactive steps to prevent shrinkage issues.
Here’s a breakdown of the common types of shrinkage in metal casting:
Types of Shrinkage in Cast Metals
Type | Description |
---|---|
Porosity Shrinkage | This occurs when the metal doesn’t fill the mold completely during cooling, leaving voids in the casting. |
Solidification Shrinkage | Happens as the metal cools and changes state from liquid to solid, causing contraction in the mold. |
Micro-Shrinkage | Subtle shrinkage that occurs at a microscopic level, affecting the internal structure and strength of the metal. |
2. How Does Shrinkage Affect Metal Casting?
Shrinkage in metal casting can have significant consequences on both the quality and strength of the final product. The primary concern is the creation of voids or gaps in the material, which can weaken it structurally. These defects are usually the result of porosity shrinkage and lead to lower tensile strength, making the material more susceptible to breaking under stress.
What’s the real story? Shrinkage can also cause dimensional inaccuracies, meaning the final casting doesn’t meet the required measurements. This can be particularly problematic in industries where precise specifications are essential, such as aerospace, automotive, and medical manufacturing.
Let’s take a look at how shrinkage affects different types of casting materials:
Shrinkage Effects on Metal Casting
Effect | Description |
---|---|
Porosity and Weakening | Voids or holes in the casting reduce the metal’s strength and make it prone to failure. |
Dimensional Inaccuracy | Shrinkage can cause the final product to be too large or too small, leading to fit issues. |
Reduced Mechanical Strength | Shrinkage can result in a reduction of the material’s mechanical properties, including tensile strength. |
3. What Are the Common Types of Shrinkage in Casting?
There are several types of shrinkage that can occur during the casting process, and understanding each one is critical for identifying and mitigating potential defects in the final product.
Ready for the good part? By recognizing the type of shrinkage in a casting, manufacturers can adjust their process to target the specific issue. Here’s an overview of the different types of shrinkage you may encounter:
Common Types of Shrinkage in Metal Casting
Type | Description |
---|---|
Porosity Shrinkage | Voids or air pockets form within the cast due to uneven cooling rates or insufficient metal to fill the mold. |
Solidification Shrinkage | Occurs when the molten metal solidifies and shrinks, typically seen in thick sections of a casting. |
Micro-Shrinkage | Shrinkage that occurs at a microscopic level, often undetected but still impacting the overall strength of metal. |
4. How Can Shrinkage Be Prevented in Cast Metals?
Reducing shrinkage in metal casting is essential to produce high-quality castings that meet industry standards. Manufacturers can take several steps to control shrinkage during the casting process. These steps include proper mold design, controlling the cooling rate, and selecting the right alloy compositions.
Here’s the kicker: the proper design of gating and riser systems ensures that the molten metal flows evenly into the mold, filling the cavity without forming air pockets or voids. By improving these systems, manufacturers can prevent shrinkage defects and avoid costly rework.
Below is a table summarizing the most effective methods for preventing shrinkage:
Methods to Prevent Shrinkage in Cast Metals
Method | Description |
---|---|
Proper Mold Design | Using well-designed gating and riser systems ensures molten metal flows evenly into the mold. |
Controlling Cooling Rate | Ensuring that the metal cools at a consistent rate reduces solidification shrinkage. |
Alloy Composition Adjustment | Adjusting the alloy composition helps manage the metal’s behavior during cooling and solidification. |
5. What Are the Causes of Shrinkage in Cast Metals?
Shrinkage in cast metals is caused by several factors, including cooling rates, alloy composition, and mold material. Understanding these factors can help manufacturers control shrinkage and produce high-quality castings.
What’s the real story? Alloy composition is one of the most significant factors influencing shrinkage. Different metals shrink at different rates, so understanding the specific behavior of each material is critical for managing shrinkage. Cooling rate is another important factor. If the cooling rate is too fast or too slow, it can result in uneven solidification and cause shrinkage.
Here’s a table summarizing the primary causes of shrinkage in metal casting:
Causes of Shrinkage in Cast Metals
Cause | Impact on Shrinkage |
---|---|
Alloy Composition | Different alloys shrink at different rates depending on the metal’s composition and properties. |
Cooling Rate | Rapid cooling can cause uneven solidification, leading to more shrinkage. Slower cooling can result in larger shrinkage. |
Mold Material | The material of the mold affects how quickly the metal cools, with some materials causing faster solidification and shrinkage. |
6. How Does Alloy Composition Impact Shrinkage?
The composition of the alloy plays a crucial role in shrinkage. Alloys with a high percentage of certain elements like carbon or silicon tend to shrink more than others. Understanding the role of alloy composition can help manufacturers select materials that are less prone to shrinkage.
What’s the real story? Alloys like aluminum and steel behave differently when subjected to the cooling process. For example, aluminum has a higher coefficient of thermal expansion, which means it will shrink more than steel during solidification. By adjusting the alloy composition, manufacturers can better control the shrinkage rate and reduce the likelihood of defects.
Here’s a table showing how alloy composition impacts shrinkage:
Alloy Composition and Shrinkage
Alloy Composition | Shrinkage Rate | Example Alloy |
---|---|---|
High Carbon Content | Higher Shrinkage | Cast iron |
High Silicon Content | Moderate Shrinkage | Aluminum alloys |
Low Carbon Content | Lower Shrinkage | Steel |
7. What Role Does Cooling Rate Play in Shrinkage?
Cooling rate is one of the most influential factors when it comes to shrinkage. The rate at which molten metal cools and solidifies can determine the type and extent of shrinkage in the final casting. A fast cooling rate can lead to solidification shrinkage, whereas a slow cooling rate may result in more porosity.
Ready for the good part? By controlling the cooling rate, manufacturers can achieve more uniform shrinkage and prevent the formation of cracks or voids. This can be accomplished by using chillers or adjusting the mold material to regulate the temperature more effectively.
Here’s a table summarizing the impact of cooling rate on shrinkage:
Cooling Rate and Shrinkage
Cooling Rate | Type of Shrinkage | Effect on Cast Metal |
---|---|---|
Fast Cooling | Solidification Shrinkage | More porosity and cracks |
Slow Cooling | Uniform Shrinkage | Better dimensional accuracy |
8. How Does Mold Design Influence Shrinkage?
The design of the mold plays a significant role in preventing shrinkage. A well-designed mold ensures the molten metal flows evenly and fills the cavity properly, which minimizes the chances of shrinkage. Gating systems, risers, and vents all contribute to how the metal solidifies and how shrinkage is managed.
What’s the real story? By designing the mold to allow for proper metal flow, manufacturers can reduce the risk of porosity and solidification shrinkage. A poorly designed mold can lead to excess shrinkage, resulting in defects.
Below is a table summarizing how mold design influences shrinkage:
Mold Design and Shrinkage
Mold Design Element | Influence on Shrinkage | Impact on Casting Quality |
---|---|---|
Gating System | Controls the flow of molten metal into the mold | Reduces porosity and voids |
Riser Design | Provides additional metal to compensate for shrinkage | Prevents shrinkage defects |
Venting | Allows gases to escape during solidification | Reduces trapped air pockets |
9. Can Shrinkage Be Measured in Cast Metals?
Measuring shrinkage in cast metals is an essential part of quality control during the casting process. Without proper measurement, manufacturers may fail to detect shrinkage-related defects that can lead to product failures or rework costs. Shrinkage can be measured using both destructive and non-destructive methods. Non-destructive testing (NDT) methods are the most commonly used as they allow for evaluation without damaging the casting.
What’s the real story? Non-destructive testing methods such as ultrasonic testing, X-ray imaging, and CT scanning are all effective ways to detect internal voids or porosity caused by shrinkage. These methods can provide a detailed view of the casting, allowing manufacturers to pinpoint exactly where the shrinkage occurred.
Here’s a table summarizing the common shrinkage measurement methods:
Shrinkage Measurement Methods
Measurement Method | Description | Pros and Cons |
---|---|---|
Ultrasonic Testing | Uses sound waves to detect internal defects like porosity or voids caused by shrinkage. | Non-destructive, effective, but can be complex to interpret. |
X-ray Imaging | Provides detailed images of the internal structure of the casting. | Very detailed, but can be expensive and time-consuming. |
CT Scanning | Uses computed tomography to create 3D images of the casting’s internal structure. | Highly detailed and accurate, but requires expensive equipment. |
10. How Does Shrinkage Lead to Casting Defects?
Shrinkage is the leading cause of casting defects, especially when it occurs unevenly during the cooling phase. Shrinkage defects can include porosity, cracks, and dimensional inaccuracies. Porosity occurs when gas pockets form inside the casting, weakening the structure and reducing its ability to withstand stress. Dimensional inaccuracies occur when the final casting does not meet the intended measurements due to the uneven contraction of the metal.
What’s the real story? Cracks can form when internal stresses exceed the material’s strength due to uneven shrinkage. These cracks may not always be visible at first, but over time they can compromise the structural integrity of the casting. When shrinkage occurs in critical areas, it can render the casting unusable or unsafe for its intended purpose.
Here’s a table that outlines the most common shrinkage-related defects:
Common Shrinkage-Related Defects
Defect Type | Description | Impact on Casting |
---|---|---|
Porosity | Gas pockets form inside the casting due to insufficient metal flow or cooling inconsistencies. | Weakens the material, reducing strength and durability. |
Cracks | Shrinkage-induced stresses can cause cracks in the casting, especially in thinner sections. | Cracks compromise casting integrity and lead to failure. |
Dimensional Inaccuracy | Shrinkage causes the casting to be too large or small, leading to fit issues with other components. | Inaccurate dimensions can affect assembly and performance. |
11. What Are the Solutions for Shrinkage Defects?
Several solutions exist to address shrinkage defects, but the best approach depends on the type and severity of the defect. If shrinkage is detected, reworking or repairing the casting may be required, though prevention is always the preferred approach. By using proper design techniques, controlling cooling rates, and adjusting alloy compositions, manufacturers can significantly reduce the likelihood of shrinkage defects.
But here’s the kicker: Computer simulations play a crucial role in reducing shrinkage defects. By simulating the entire casting process before production begins, manufacturers can predict areas where shrinkage is likely to occur and make adjustments to the design. This proactive approach can save time and money, ensuring that the final casting is free from shrinkage defects.
Here’s a table summarizing the key solutions for shrinkage defects:
Solutions for Shrinkage Defects
Solution | Description | Pros and Cons |
---|---|---|
Computer Simulations | Simulating the casting process helps predict and correct shrinkage defects before production. | Proactive, saves time, but requires sophisticated software. |
Reworking Defective Castings | Rework involves welding or using filler material to repair defects caused by shrinkage. | Effective, but time-consuming and costly. |
Optimized Mold Design | Improving the mold design, including gating systems and risers, reduces shrinkage defects. | Highly effective, but may require redesigning existing molds. |
12. How Can 3D Printing Help Reduce Shrinkage?
3D printing, also known as additive manufacturing, has emerged as an effective tool for reducing shrinkage in metal casting. The ability to create highly accurate and complex mold designs with 3D printing can significantly reduce the likelihood of shrinkage defects. Traditional molding methods often struggle with precise geometric designs, leading to uneven metal flow and shrinkage.
Ready for the good part? With 3D printing, manufacturers can produce molds with internal channels or designs that are difficult to achieve using traditional methods. This allows for better control over the cooling rate and metal flow, which can significantly reduce the occurrence of shrinkage.
Here’s a table showing how 3D printing helps reduce shrinkage:
3D Printing and Shrinkage Control
3D Printing Advantage | Description | Benefit to Shrinkage Control |
---|---|---|
Complex Mold Designs | 3D printing allows for intricate mold designs with internal channels or cooling pathways. | More precise control over metal flow and cooling. |
Rapid Prototyping | 3D printing enables fast creation and testing of prototype molds before mass production. | Faster detection of potential shrinkage issues, reducing rework. |
Custom Cooling Systems | 3D-printed molds can include custom cooling channels to regulate the cooling rate more effectively. | More even cooling, preventing shrinkage defects. |
13. How Can You Avoid Shrinkage in Different Casting Processes?
Each type of casting process presents unique challenges when it comes to shrinkage. Understanding how to minimize shrinkage in each casting method is crucial for producing high-quality products. Different techniques and strategies need to be applied depending on whether you are working with sand casting, investment casting, or die casting.
Here’s the kicker: By customizing the approach to shrinkage control for each casting method, manufacturers can significantly reduce defects and improve overall quality. Here’s a comparison of the methods used to control shrinkage in different casting processes:
Shrinkage Control by Casting Process
Casting Process | Shrinkage Control Technique | Benefits |
---|---|---|
Sand Casting | Use of risers, gating systems, and controlled cooling. | Better metal flow and reduced shrinkage. |
Investment Casting | Use of high-quality mold materials and precise temperature control. | Reduced porosity and more accurate dimensions. |
Die Casting | High-pressure injection and controlled cooling systems. | Minimizes shrinkage through rapid cooling and metal flow control. |
14. What Are the Latest Trends in Shrinkage Control?
The manufacturing industry is continually evolving, and so are the methods for controlling shrinkage in metal casting. Technological advances, particularly in simulation technology and 3D printing, are revolutionizing how shrinkage is managed. New mold materials, smart casting systems, and additive manufacturing techniques are pushing the boundaries of what’s possible in shrinkage reduction.
What’s the real story? With advancements in technology, manufacturers now have access to more accurate and cost-effective ways to control shrinkage. For instance, smart casting systems use sensors to monitor temperature and pressure in real-time, allowing adjustments to be made during the casting process to minimize shrinkage defects.
Here’s a table summarizing some of the latest trends in shrinkage control:
Latest Trends in Shrinkage Control
Trend | Description | Benefits |
---|---|---|
Smart Casting Systems | Sensors and real-time data are used to monitor the casting process and adjust variables. | More precise control over temperature and pressure. |
Advanced Mold Materials | New mold materials, such as ceramics and composites, are used for better heat resistance. | Reduced shrinkage through improved thermal properties. |
Additive Manufacturing | 3D printing is used for rapid prototyping and creating complex molds with custom features. | Improved mold design, better cooling, and less shrinkage. |
15. What Are the Benefits of Minimizing Shrinkage in Castings?
Minimizing shrinkage in metal castings offers several key benefits that can improve product quality, reduce manufacturing costs, and enhance overall efficiency. By controlling shrinkage, manufacturers can produce stronger, more durable castings that meet the required specifications and perform well under stress.
Ready for the good part? Minimizing shrinkage can lead to cost savings due to fewer defective castings and reduced rework. It can also improve dimensional accuracy, ensuring that the final product meets the precise specifications needed for assembly and functionality.
Here’s a table summarizing the benefits of minimizing shrinkage in casting:
Benefits of Minimizing Shrinkage
Benefit | Description |
---|---|
Enhanced Durability | Reduced shrinkage leads to stronger, more durable castings that perform well under stress. |
Improved Dimensional Accuracy | Minimizing shrinkage ensures that castings meet the required size and fit specifications. |
Cost Savings | Fewer defective castings mean reduced costs from rework, scrap, and production delays. |
FAQ Section
Q1: What is shrinkage in cast metals?
Shrinkage in cast metals is the reduction in volume that occurs as molten metal cools and solidifies, causing contraction in the mold.
Q2: How does shrinkage work in metal casting?
Shrinkage happens when the liquid metal solidifies and contracts, leaving behind voids or gaps in the cast.
Q3: What types of shrinkage are most common in casting?
The most common types of shrinkage are porosity shrinkage, solidification shrinkage, and micro-shrinkage, each affecting the final product differently.
Q4: How can shrinkage in cast metals be minimized?
Shrinkage can be minimized by optimizing mold design, controlling the cooling rate, and using specific alloy compositions to manage the shrinkage.
Q5: Can shrinkage be measured in cast metals?
Yes, shrinkage can be measured using various techniques, including non-destructive testing (NDT) and specialized tools designed for shrinkage detection.