High-temperature alloys play a crucial role in industries that demand materials capable of withstanding extreme conditions. From aerospace to power generation, these alloys are used to ensure that machinery and engines operate efficiently and reliably. But, as technology advances, the properties of high-temperature alloys must evolve to meet new challenges. In this article, we will explore the future of these alloys, focusing on their evolving properties, key innovations, and their growing significance in various sectors.
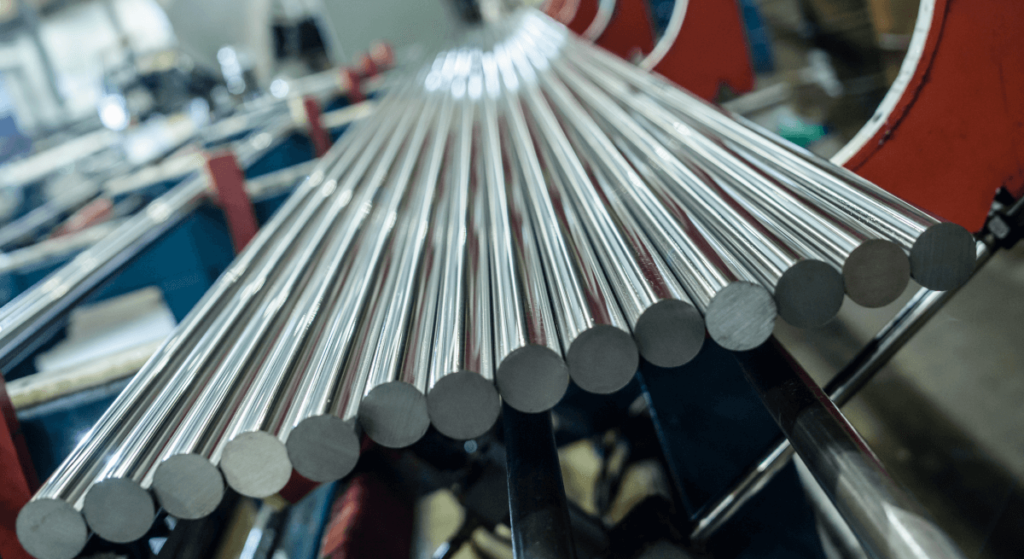
1. What Are High-Temperature Alloys?
High-temperature alloys are specialized materials designed to perform in environments where typical metals would fail. These alloys are engineered to withstand extreme heat, oxidation, and mechanical stresses without degrading. They are typically composed of nickel, cobalt, or iron-based compounds, which give them the strength and durability needed for high-performance applications.
But here’s the kicker—these alloys don’t just endure high temperatures; they also maintain their structural integrity over extended periods of exposure. High-temperature alloys are critical in industries where heat resistance is non-negotiable, such as in aerospace, automotive, and power generation. Without them, the reliability of many modern technologies would be compromised.
In aerospace, for example, turbines and engines rely on these alloys to function efficiently under extreme heat. In automotive applications, high-performance engines need materials that won’t warp or degrade under the pressures of rapid temperature fluctuations. In power plants, turbines and generators made from high-temperature alloys ensure that the energy produced remains consistent and efficient.
The demand for these materials will only grow as industries push the boundaries of heat tolerance and energy efficiency. Advances in metallurgy are pushing the limits of alloy performance, enabling manufacturers to create stronger, lighter, and more heat-resistant alloys.
Material Type | Common Elements | Typical Use | Key Characteristics |
---|---|---|---|
Nickel-based | Nickel, Chromium | Aerospace Engines | Excellent heat resistance |
Cobalt-based | Cobalt, Chromium | Power Generation | High strength at elevated temps |
Iron-based | Iron, Carbon | Automotive Engines | Cost-effective, good fatigue resistance |
2. Why Are High-Temperature Alloys Critical in Today’s Engineering?
In today’s engineering landscape, high-temperature alloys are indispensable. Ready for the good part? These materials allow industries to create more efficient, powerful, and long-lasting machines that operate under extreme heat and stress.
A key reason why these alloys are so critical is their ability to maintain mechanical strength even at high temperatures. This feature is essential for ensuring the longevity of components like turbine blades, which are subjected to both high temperatures and mechanical stresses during operation.
Another significant advantage of high-temperature alloys is their excellent resistance to oxidation and corrosion. These properties help to extend the life of critical components in harsh environments. Industries such as aerospace, automotive, and energy have relied on the unique properties of high-temperature alloys to improve performance while reducing maintenance costs.
But here’s the real story: As industries evolve, the demand for higher efficiency and longer-lasting components is only increasing. High-temperature alloys are crucial for meeting these expectations, offering unparalleled strength and resistance under the most extreme conditions.
Industry | Alloy Application | Benefit |
---|---|---|
Aerospace | Turbine engines | Increased fuel efficiency and power |
Automotive | Exhaust systems | Reduced corrosion and longer lifespan |
Energy | Power plants | Greater operational efficiency and safety |
3. When Will Innovations in High-Temperature Alloys Be Most Significant?
High-temperature alloys have always been at the forefront of innovation, and the pace of development is only accelerating. This is where it gets interesting… Innovations in materials science, manufacturing techniques, and alloy composition are leading to significant advancements.
Over the next decade, we can expect high-temperature alloys to undergo dramatic changes. Researchers are focused on developing alloys that can perform at even higher temperatures, offering better resistance to heat-related degradation. Additionally, newer manufacturing processes such as additive manufacturing (3D printing) are revolutionizing how these alloys are produced, allowing for greater precision and complexity in design.
These innovations are poised to benefit industries such as aerospace, where the need for high-performance materials capable of withstanding extreme environments is ever-growing. In automotive engineering, lighter, stronger alloys will contribute to more fuel-efficient vehicles. Similarly, power generation industries will benefit from alloys that extend the lifespan of turbines and reduce maintenance costs.
Alloy Innovation | Expected Outcome | Application Area |
---|---|---|
Higher heat resistance | Better performance under extreme heat | Aerospace, Energy |
Advanced manufacturing (3D printing) | Complex shapes, reduced waste | Automotive, Aerospace |
New material compositions | Longer lifespan, better resistance | Power Generation |
4. Where Are High-Temperature Alloys Used Most Extensively?
High-temperature alloys are used in many sectors where heat resistance is paramount. You might be wondering, which industries rely on these materials the most?
The aerospace industry is one of the largest consumers of high-temperature alloys, using them in turbine blades, engine components, and exhaust systems. These alloys are essential for ensuring the safety and efficiency of aircraft engines, where performance must be consistent even under extreme operating conditions.
In the automotive sector, high-temperature alloys are used in components such as exhaust systems and turbochargers, where heat resistance is crucial for durability and performance. Similarly, power generation plants rely heavily on high-temperature alloys in turbines, reactors, and boilers, where these materials must withstand intense heat for long periods.
With the rise of renewable energy, there’s also a growing demand for high-temperature alloys in technologies such as solar power and geothermal energy systems. These alloys help to ensure the long-term reliability of equipment exposed to high heat conditions.
Industry | Key Applications | Alloy Benefits |
---|---|---|
Aerospace | Turbine blades, engine parts | High heat resistance and strength |
Automotive | Exhaust systems, turbochargers | Enhanced durability, corrosion resistance |
Power Generation | Turbines, reactors | Long-term reliability, heat resistance |
Renewable Energy | Solar panels, geothermal systems | High-temperature endurance and efficiency |
5. How Do the Properties of High-Temperature Alloys Evolve Over Time?
Over time, the properties of high-temperature alloys evolve to meet the ever-changing demands of industry. Here’s the deal: As technology advances, so too must the materials used to build complex machinery. One of the primary challenges faced by high-temperature alloys is their susceptibility to oxidation, which can degrade their strength over time. However, researchers are developing new coatings and surface treatments that significantly improve the lifespan of these alloys.
Another area of improvement is in the composition of the alloys themselves. Engineers are constantly experimenting with new elements and additives that can enhance the properties of these alloys, such as adding rare earth metals or adjusting the alloy’s carbon content. These innovations result in alloys that are more resistant to thermal fatigue, corrosion, and mechanical stress.
Alloy Property | Current State | Future Trends |
---|---|---|
Oxidation resistance | Moderate | Advanced coatings and surface treatments |
Thermal fatigue | Limited at higher temperatures | Enhanced resistance with new alloys |
Strength under stress | High | Increased with new compositions |
6. What Are the Current Limitations of High-Temperature Alloys?
Despite their remarkable properties, high-temperature alloys are not without limitations. But here’s the kicker… While these alloys are built to endure extreme heat, they come with their own set of challenges that must be addressed to improve their performance.
One of the main limitations of high-temperature alloys is their cost. These materials are often expensive to produce due to the complexity of their composition and the manufacturing processes involved. Additionally, while they perform well under heat, they can suffer from thermal fatigue over time, particularly in applications where they are subjected to rapid temperature changes.
Another limitation is their weight. While newer alloys are lighter than their predecessors, many high-temperature alloys are still relatively heavy, which can be a drawback in applications such as aerospace, where weight reduction is critical. Engineers are working on developing lighter alloys without compromising on strength and heat resistance.
Limitation | Current Impact | Solutions Being Developed |
---|---|---|
Cost | High production costs | Advanced manufacturing techniques |
Thermal fatigue | Gradual degradation over time | Better heat-resistant coatings |
Weight | Heavy materials for aerospace | Development of lighter alloys |
7. How Are Researchers and Engineers Improving High-Temperature Alloys?
Researchers are always striving to improve high-temperature alloys. What’s the real story? Innovations in materials science are leading to the development of alloys that can withstand even higher temperatures and offer better durability.
One of the most exciting advancements is in the area of nanotechnology, where tiny particles are added to high-temperature alloys to enhance their heat resistance and strength. This process enables the creation of alloys that are more resistant to oxidation, thermal cycling, and other forms of degradation.
Another significant development is the use of additive manufacturing, or 3D printing, which allows for the creation of highly complex shapes that traditional manufacturing methods cannot achieve. This technology enables the creation of more efficient, customized alloys that meet the specific needs of industries such as aerospace and automotive.
Innovation | Impact on Alloys | Industry Applications |
---|---|---|
Nanotechnology | Improved heat resistance | Aerospace, Energy |
Additive manufacturing | Custom shapes, reduced waste | Automotive, Aerospace |
8. What Are the Key Materials That Could Change the Future of High-Temperature Alloys?
As technology progresses, new materials are being incorporated into high-temperature alloys. Ready for the good part? These materials have the potential to revolutionize the performance of high-temperature alloys, making them more efficient and durable.
Rare earth metals are one area of focus. These materials offer unique properties, such as high resistance to oxidation and excellent mechanical strength at elevated temperatures. By incorporating rare earth metals into high-temperature alloys, researchers hope to create alloys that can perform at even higher temperatures and for longer periods.
Another exciting development is the use of advanced coatings and surface treatments that can significantly improve the performance of existing high-temperature alloys. These coatings provide an additional layer of protection against oxidation and wear, extending the lifespan of the alloy and improving its overall performance.
Material | Benefit | Potential Use Cases |
---|---|---|
Rare earth metals | High temperature resistance | Aerospace, Energy |
Advanced coatings | Enhanced lifespan and performance | Automotive, Power Generation |
9. How Does Sustainability Influence the Development of High-Temperature Alloys?
In today’s world, sustainability is a key consideration in material development. This is where it gets interesting… The development of high-temperature alloys is no exception. As industries move toward more sustainable practices, the demand for alloys that are not only efficient but also environmentally friendly is growing.
Researchers are focusing on creating alloys that can withstand higher temperatures while using fewer resources in their production. Additionally, there is a push for reducing the carbon footprint of alloy production processes by utilizing greener technologies and materials.
Sustainability also plays a role in improving the recyclability of high-temperature alloys. Alloys that can be reused and recycled without losing their strength and performance properties are essential for creating a more sustainable industrial ecosystem.
Sustainability Focus | Current Efforts | Future Directions |
---|---|---|
Reduced carbon footprint | Green manufacturing practices | Use of sustainable materials |
Enhanced recyclability | Focus on reusability | Development of eco-friendly alloys |
10. What Are the Future Trends in High-Temperature Alloy Applications?
Looking ahead, high-temperature alloys will play an even more significant role in industries such as aerospace, automotive, and energy. You might be wondering, what are the trends driving the demand for these alloys in the future?
One trend is the increasing use of high-temperature alloys in renewable energy technologies. As power plants and wind turbines become more efficient, the demand for alloys that can withstand higher temperatures will grow. Similarly, as electric vehicles become more mainstream, high-temperature alloys will be used to improve the performance and longevity of batteries and power systems.
Another trend is the continued miniaturization of components in industries like aerospace and automotive. As systems become more compact, the need for stronger, lighter high-temperature alloys will increase.
Trend | Driving Factors | Industry Impact |
---|---|---|
Renewable energy | Energy efficiency demands | Increased demand for heat-resistant alloys |
Electric vehicles | Power efficiency | Improved battery performance and longevity |
11. How Will the Demand for High-Temperature Alloys Evolve in the Next Decade?
The next decade will see an explosion in demand for high-temperature alloys, driven by advancements in technology and the growing needs of industries. But here’s the kicker… As industries focus on improving efficiency and reducing maintenance costs, the demand for more advanced, durable alloys will increase.
The aerospace sector, for example, is set to see significant growth, with new materials required for next-generation aircraft engines and turbine systems. Similarly, in automotive and energy sectors, companies are looking for lighter, more heat-resistant alloys to improve vehicle performance and energy production efficiency.
With the rise of sustainable technologies and the demand for better performance, the market for high-temperature alloys will continue to expand. Companies must adapt to these trends to stay competitive.
Industry | Projected Growth | Alloy Demand Drivers |
---|---|---|
Aerospace | High growth in jet engine development | Need for stronger, heat-resistant materials |
Automotive | Growth in electric vehicle production | Demand for lightweight, durable alloys |
Energy | Expansion of renewable energy systems | More efficient, heat-resistant alloys |
12. What Is the Role of 3D Printing in the Future of High-Temperature Alloys?
3D printing is transforming the way we think about material manufacturing. This is where it gets interesting… Additive manufacturing (3D printing) is now being used to create high-temperature alloys with unprecedented precision and complexity.
With 3D printing, manufacturers can produce alloys in complex geometries that traditional manufacturing methods cannot achieve. This allows for lighter, stronger, and more customized parts for industries such as aerospace and automotive. Additionally, 3D printing reduces waste, improving the overall sustainability of alloy production.
The future of high-temperature alloys will likely involve a greater reliance on 3D printing to create customized, high-performance parts that meet the exact specifications required by modern industries.
3D Printing Benefit | Impact on High-Temperature Alloys | Industry Application |
---|---|---|
Customization | Complex geometries, reduced waste | Aerospace, Automotive |
Sustainability | Less material waste, energy efficiency | Power Generation |
13. How Do High-Temperature Alloys Compare to Alternative Materials?
High-temperature alloys are often compared to alternative materials such as ceramics, composites, and refractory metals. What’s the real story? High-temperature alloys tend to outperform these materials in many areas, but there are still situations where alternatives may be more suitable.
Ceramics, for example, have excellent heat resistance but can be brittle, making them unsuitable for applications that involve mechanical stress. Composites are lightweight and offer good heat resistance, but they often lack the strength of high-temperature alloys.
In the end, high-temperature alloys remain the material of choice for many high-performance applications, but engineers must carefully consider the specific needs of each project before making a decision.
Material | Strengths | Weaknesses |
---|---|---|
High-temperature alloys | Excellent heat resistance, strength | Relatively high weight and cost |
Ceramics | Excellent heat resistance | Brittle, less versatile |
Composites | Lightweight, good heat resistance | Lower strength, expensive |
14. Conclusion: The Future of High-Temperature Alloys – A Look Ahead
The future of high-temperature alloys is filled with promise. Ready for the good part? As industries continue to evolve, the demand for more durable, efficient, and sustainable materials will drive innovations in alloy technology. With the rise of 3D printing, the use of rare earth metals, and the focus on sustainability, the next decade will likely see high-temperature alloys outperforming even current expectations.
For businesses in industries such as aerospace, automotive, and energy, staying ahead of these trends is crucial to maintaining competitive advantage. The future of high-temperature alloys promises to be not only about better performance but also about a more sustainable and cost-effective approach to manufacturing.
Conclusion Focus | Future Developments | Industry Impact |
---|---|---|
Sustainability | Use of eco-friendly alloys | Reduced carbon footprint |
Customization | Growth in 3D printing | More efficient components |
FAQ Section
Q1: What are high-temperature alloys?
High-temperature alloys are specially designed materials that can withstand extreme heat without losing their strength or structural integrity. These alloys are essential in industries such as aerospace, automotive, and power generation.
Q2: How do high-temperature alloys perform under extreme conditions?
These alloys are engineered to maintain their mechanical properties, such as strength and resistance to thermal fatigue, even when exposed to extremely high temperatures.
Q3: Why are high-temperature alloys used in aerospace?
Aerospace applications require materials that can operate efficiently and safely under extreme conditions, such as high heat and mechanical stress. High-temperature alloys ensure the longevity and performance of turbine engines and other critical components.
Q4: How are high-temperature alloys improved for sustainability?
Researchers are developing new alloys with enhanced properties, such as better heat resistance and longer lifespans. These improvements reduce the need for frequent replacements and contribute to more sustainable industrial processes.
Q5: What are some emerging trends in high-temperature alloy applications?
Emerging trends include the increased use of high-temperature alloys in renewable energy technologies and electric vehicles. These materials are also being used in more advanced applications, such as additive manufacturing and 3D printing