Aluminum alloy die casting is a key process in the manufacturing industry, especially for producing durable, lightweight, and high-strength parts for various industries. The question of which aluminum alloy is best suited for your project depends on several factors, including the required strength, corrosion resistance, and thermal conductivity. In this article, we will explore the ins and outs of aluminum alloy die casting, offering guidance on choosing the right alloy and explaining its applications across different industries. Let’s dive in and understand why aluminum alloy die casting should be your go-to method for manufacturing parts.
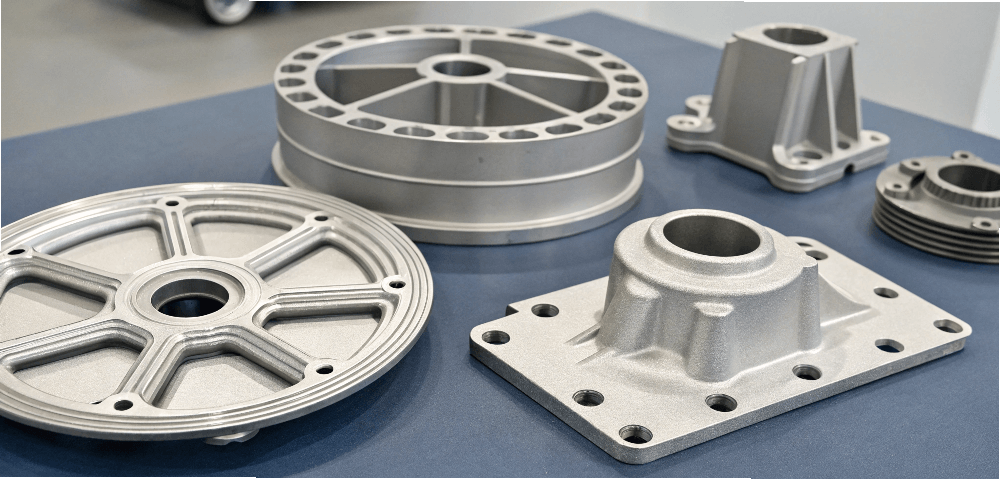
1. What is Aluminum Alloy Die Casting?
Aluminum alloy die casting is a manufacturing process where molten aluminum is injected into a mold at high pressure to create precise, complex shapes. But here’s the kicker: aluminum alloys are chosen for die casting because they offer a unique combination of lightness, strength, and excellent corrosion resistance, making them perfect for industries such as automotive, aerospace, and electronics.
The process starts with preparing the aluminum alloy, which is typically a mixture of aluminum and other metals like silicon, copper, and magnesium. What’s the real story? These added metals enhance the material’s properties, such as strength, hardness, and thermal conductivity. Once the alloy is molten, it is injected into a steel mold under high pressure, which ensures that the mold cavity is filled rapidly and the final part has the precise shape.
Die casting offers several advantages over other manufacturing methods. It allows for complex shapes, reducing the need for additional machining, and it can be used for high-volume production, making it a cost-effective solution for large-scale projects. Ready for the good part? Aluminum alloy die casting also provides a high level of repeatability, meaning parts can be produced consistently with minimal variations in dimensions.
Characteristic | Aluminum Alloy Die Casting | Other Casting Methods |
---|---|---|
Material | Aluminum alloys (e.g., A380, A360) | Various (steel, iron) |
Precision | High precision with tight tolerances | Varies (less precise) |
Strength | Strong, lightweight | Generally heavier |
Corrosion Resistance | Excellent | Varies by material |
Production Speed | Fast (seconds per cycle) | Slower in most cases |
2. Why Choose Aluminum Alloys for Die Casting?
When it comes to choosing materials for die casting, aluminum alloys are often the preferred choice. Here’s the deal: aluminum is lightweight yet strong, offering a great balance between performance and cost. It’s also highly corrosion-resistant, making it suitable for applications in harsh environments, such as marine and automotive industries.
Aluminum alloys also boast excellent thermal and electrical conductivity, which makes them perfect for use in electronics and electrical components. Furthermore, aluminum is abundant and recyclable, contributing to its environmental appeal. This makes aluminum alloy die casting an attractive choice for companies looking to produce high-performance, eco-friendly products.
What’s the catch? Although aluminum alloys are incredibly versatile, selecting the right alloy for your project is crucial. Different alloys offer varying levels of strength, heat resistance, and corrosion resistance, so it’s essential to understand the specific requirements of your project before choosing an alloy.
Aluminum alloy die casting is also a cost-effective option for mass production. Thanks to the efficiency of the process, aluminum die casting can be done quickly and with minimal waste. The molds used in the process are durable, allowing for thousands of parts to be produced from a single mold, making it ideal for projects that require high-volume production.
Benefit | Aluminum Alloy Die Casting | Other Materials |
---|---|---|
Weight | Lightweight and strong | Varies (heavier) |
Corrosion Resistance | Excellent | Varies |
Recyclability | 100% recyclable | Not always recyclable |
Thermal Conductivity | High | Varies |
Cost-Effectiveness | High for high-volume production | Typically higher |
3. How Does Aluminum Alloy Die Casting Work?
The process of aluminum alloy die casting is relatively straightforward, but it requires precise control over several variables to ensure high-quality parts. But here’s the kicker: mastering the technique involves understanding the nuances of temperature, pressure, and mold design.
The first step in the process is the preparation of the aluminum alloy. Aluminum is melted in a furnace until it reaches a liquid state. The molten aluminum is then injected into a mold at high pressure, using a die-casting machine. This is where it gets interesting: the mold, which is made of steel, ensures that the aluminum takes the shape of the desired part. The pressure used during injection helps to achieve high precision and a smooth surface finish.
After the aluminum is injected into the mold, it begins to cool and solidify. Once the part has cooled sufficiently, the mold is opened, and the part is removed. This process allows for the rapid production of complex parts with excellent dimensional accuracy. Ready for the good part? The entire process typically takes just a few seconds to a minute per cycle, depending on the size and complexity of the part.
The final step involves inspecting the part for any defects, such as air bubbles or incomplete filling of the mold. This is where quality control comes into play. Manufacturers often conduct various tests, such as pressure tests, X-ray inspections, or visual checks, to ensure that the final product meets the required standards.
Step | Details |
---|---|
Molten Aluminum Injection | Injected into steel mold at high pressure |
Cooling and Solidifying | Rapid cooling to maintain precision |
Mold Removal | Mold is opened and the part is extracted |
Inspection | Visual or non-destructive testing (X-ray, pressure) |
Cycle Time | Typically seconds to a minute per cycle |
4. What are the Types of Aluminum Alloys Used in Die Casting?
Not all aluminum alloys are created equal, and each type has its own unique set of properties that make it suitable for specific applications. You might be wondering: what are the best alloys to use for die casting? Let’s explore some of the most common aluminum alloys used in die casting.
One of the most widely used alloys is A380, which is a general-purpose aluminum alloy. A380 offers a great combination of strength, wear resistance, and fluidity, making it ideal for applications like automotive parts, housing components, and appliances. What’s the real story? A380 is commonly used for die casting because it can be poured easily into molds and provides high-quality surface finishes.
Another popular alloy is A360, which is known for its excellent corrosion resistance, making it perfect for parts exposed to harsh environmental conditions, such as marine or outdoor equipment. But here’s the kicker: A360 also has good casting characteristics, allowing for the production of thin-walled components with high precision.
A413 is another alloy that is often used for die casting due to its excellent fluidity and resistance to thermal expansion. This is where it gets interesting: A413 is frequently used for producing parts like engine components and electrical enclosures, where durability and heat resistance are critical.
Alloy Type | Key Characteristics | Common Applications |
---|---|---|
A380 | Strength, wear resistance, good fluidity | Automotive parts, housing, appliances |
A360 | Excellent corrosion resistance, casting precision | Marine, outdoor equipment |
A413 | Excellent fluidity, thermal expansion resistance | Engine components, electrical enclosures |
5. What Factors Should You Consider When Choosing an Aluminum Alloy?
Choosing the right aluminum alloy for your die casting project is crucial. What’s the real story? A poor choice of alloy can lead to weak parts, increased production costs, and even failures in the field. Here are some key factors to consider when selecting an aluminum alloy.
First, consider the mechanical properties required for the final part. If strength is a primary concern, you may want to opt for an alloy like A380, which offers a good balance of strength and ductility. If the part will be exposed to extreme temperatures or harsh environments, alloys like A360 or A413 may be more appropriate due to their superior corrosion resistance and heat resistance.
What’s the catch? You’ll also need to factor in the cost of the alloy. While high-performance alloys may offer superior properties, they can also be more expensive. It’s important to balance performance with budget constraints to ensure that your project remains cost-effective.
Another factor to consider is the alloy’s fluidity. Alloys with high fluidity, such as A380, are easier to inject into molds and produce finer details. However, alloys with lower fluidity may require more pressure during injection and can result in rougher surface finishes.
Finally, consider the intended application of the part. Will it be used in the automotive industry? In aerospace? Understanding the specific requirements of your application will help you make the best choice of alloy.
Factor | Description | Alloy Examples |
---|---|---|
Strength Requirements | Need for high strength and ductility | A380, A413 |
Environmental Exposure | Resistance to corrosion and heat | A360, A413 |
Fluidity | Ability of alloy to flow into intricate molds | A380 |
Cost | Budget constraints and alloy price variations | A380 (more cost-effective) |
6. How Does Aluminum Alloy Die Casting Compare to Other Casting Methods?
Aluminum alloy die casting offers several advantages over other casting methods, making it a popular choice in many industries. So, how does it stack up against other methods? Let’s compare aluminum alloy die casting with sand casting, permanent mold casting, and investment casting.
Sand casting is a traditional method where molten metal is poured into a sand mold. While sand casting is versatile and cost-effective, it can’t achieve the same level of precision as die casting. What’s the catch? Sand casting often results in rougher surface finishes and larger tolerances, making it less suitable for parts that require high accuracy.
Permanent mold casting, on the other hand, uses a metal mold, similar to die casting, but the process is slower, and the molds are generally reusable. Here’s the deal: while permanent mold casting is more precise than sand casting, it’s still not as fast or cost-effective as aluminum alloy die casting for high-volume production.
Investment casting is another method used for producing high-precision parts. But here’s the kicker: while investment casting offers exceptional detail and surface finish, it’s typically more expensive and slower than aluminum alloy die casting. This makes aluminum die casting a more affordable option for many manufacturers.
What’s the real story? When comparing these methods, aluminum alloy die casting stands out for its speed, precision, and cost-effectiveness, especially for large production runs.
Casting Method | Advantages | Disadvantages |
---|---|---|
Aluminum Die Casting | Precision, high-volume production, fast | Initial mold cost |
Sand Casting | Versatile, cost-effective | Lower precision, rougher finishes |
Permanent Mold Casting | Better precision than sand casting | Slower, higher upfront cost |
Investment Casting | Excellent surface finish, detail | Expensive, slower production |
7. How Can You Ensure the Quality of Your Aluminum Die Castings?
Ensuring the quality of your aluminum die castings is essential for meeting the required specifications and avoiding costly mistakes. Here’s the deal: quality control should be integrated into every step of the die casting process to ensure that the final product meets all necessary standards.
One important aspect of quality control is mold design. The design of the mold plays a critical role in ensuring the accuracy and consistency of the parts produced. What’s the catch? Poorly designed molds can lead to defects like incomplete filling, surface imperfections, and dimensional variations.
Another key aspect of quality control is temperature management. This is where it gets interesting: the temperature of the molten aluminum must be carefully controlled to ensure that the metal flows properly into the mold and solidifies at the right rate. If the temperature is too low, the aluminum may not fill the mold properly, while if it’s too high, the alloy may degrade and result in weak parts.
Visual inspections and testing are also essential. Manufacturers should check for defects like cracks, air bubbles, or incomplete fills. Ready for the good part? Non-destructive testing methods, such as X-ray inspections, can also be used to detect internal defects that might not be visible to the naked eye.
What’s the catch? While achieving high-quality die castings requires careful attention to detail at every stage, the payoff is well worth the effort. High-quality aluminum die castings lead to better performance, fewer defects, and greater customer satisfaction.
Quality Control Step | Details |
---|---|
Mold Design | Ensures accuracy and consistency |
Temperature Control | Maintains proper flow and solidification |
Inspection | Visual checks and non-destructive testing |
Final Testing | Ensures strength, durability, and compliance |
8. What Industries Benefit from Aluminum Alloy Die Casting?
Aluminum alloy die casting is used across many industries due to its versatility, strength, and cost-effectiveness. What’s the real story? Let’s take a look at some of the industries that benefit the most from this process.
In the automotive industry, aluminum die casting is used to produce lightweight, high-strength parts like engine blocks, transmission cases, and chassis parts. But here’s the kicker: aluminum parts help reduce vehicle weight, improving fuel efficiency and performance.
The aerospace and defense industries also rely heavily on aluminum die casting for producing parts that require both strength and lightness. Components like aircraft frames, engine parts, and housings benefit from aluminum’s high strength-to-weight ratio and excellent corrosion resistance.
In electronics, aluminum die casting is used to produce durable and efficient housings for devices like smartphones, laptops, and power supplies. This is where it gets interesting: aluminum’s excellent thermal conductivity helps dissipate heat, making it ideal for electronic components that generate heat.
Ready for the good part? Even industries like telecommunications, construction, and medical devices use aluminum die casting to create components that are both reliable and cost-effective.
Industry | Key Applications | Benefits of Aluminum Die Casting |
---|---|---|
Automotive | Engine blocks, transmission cases, chassis | Weight reduction, fuel efficiency |
Aerospace | Aircraft frames, engine components | Strength, lightness, corrosion resistance |
Electronics | Device housings, power supplies | Thermal conductivity, durability |
Medical Devices | Surgical instruments, diagnostic equipment | Precision, strength, reliability |
9. How to Select the Right Aluminum Alloy Die Casting Supplier?
Choosing the right supplier for your aluminum alloy die casting needs is crucial to the success of your project. What’s the real story? A good supplier will help you get the best results while maintaining cost-effectiveness and meeting deadlines.
When evaluating potential suppliers, look for companies that have experience with the specific type of die casting required for your project. What’s the catch? A supplier with expertise in your industry can help you avoid common mistakes and offer valuable insights into the process.
You’ll also want to assess the supplier’s ability to meet your volume requirements. But here’s the kicker: high-quality aluminum die casting is often done in large batches, so working with a supplier who can scale production efficiently is important.
Finally, don’t forget to consider the supplier’s reputation for quality and customer service. Ready for the good part? A reliable supplier will work closely with you throughout the process to ensure that your parts meet the required specifications and are delivered on time.
Evaluation Criteria | Details |
---|---|
Experience | Expertise in die casting for your industry |
Volume Capability | Ability to meet production volume |
Quality Assurance | Reputation for high-quality outputs |
Customer Service | Responsive communication, on-time delivery |
10. What Are the Environmental Benefits of Aluminum Alloy Die Casting?
When considering manufacturing methods, environmental sustainability is becoming more and more important. Here’s the deal: aluminum alloy die casting offers a number of environmental benefits that make it a smart choice for businesses focused on reducing their ecological footprint.
One of the main advantages of aluminum is its recyclability. What’s the real story? Aluminum is one of the most recycled materials in the world, with the metal able to be reused indefinitely without losing its properties. This means that aluminum die casting can be part of a closed-loop system, where scrap material is recycled back into production, reducing waste and conserving natural resources.
But here’s the kicker: the aluminum die casting process itself is energy-efficient compared to other casting methods. For example, aluminum melts at a lower temperature than steel, which means that less energy is required to heat the material. Additionally, the high precision and repeatability of the die casting process result in less waste material, making it more efficient than other manufacturing methods like sand casting or investment casting.
Aluminum also has excellent corrosion resistance, which means products made from it tend to last longer. This is where it gets interesting: parts made from aluminum alloys can withstand harsh environmental conditions, reducing the need for replacements and contributing to a more sustainable product life cycle.
Finally, by reducing the need for additional coatings or finishes, aluminum alloy die casting helps reduce the environmental impact of post-production processes. This makes aluminum die casting a truly sustainable manufacturing method for a wide range of industries.
Environmental Benefit | Impact | Details |
---|---|---|
Recyclability | Reduced waste and resource conservation | Aluminum can be recycled indefinitely |
Energy Efficiency | Lower energy consumption | Melts at lower temperatures than steel |
Durability | Longer product lifespan | Excellent resistance to corrosion |
Reduced Waste | Minimizes production waste | High precision, less material waste |
Post-Production | Eco-friendly manufacturing processes | Less need for finishing and coatings |
11. What Are the Cost Factors in Aluminum Alloy Die Casting?
Cost is always a critical consideration in any manufacturing process. But here’s the kicker: while aluminum alloy die casting is known for being cost-effective, several factors influence its overall cost. Understanding these factors can help you make smarter decisions about your project’s budget.
The first factor is the material cost. What’s the real story? Aluminum alloys vary in price depending on their composition. For instance, premium alloys that offer superior properties such as high corrosion resistance or strength can be more expensive than general-purpose alloys like A380.
Another significant factor is mold design. Here’s the deal: creating high-quality, durable molds requires precision, which can add to the upfront costs of the project. However, well-designed molds ensure that the die casting process is efficient, reducing waste and making it more cost-effective in the long run.
What’s the catch? Labor costs also play a role in the overall price. While die casting is a highly automated process, skilled workers are still required to manage the equipment, conduct inspections, and perform maintenance. The complexity of the part being produced also affects labor costs, with more intricate designs requiring additional time and effort.
Finally, production volume is a critical factor. This is where it gets interesting: die casting becomes more cost-effective as the production volume increases. The more parts you order, the lower the cost per unit becomes. This is why aluminum die casting is especially well-suited for high-volume production runs.
Cost Factor | Details | Impact on Pricing |
---|---|---|
Material Cost | Varies based on alloy composition | Premium alloys increase material cost |
Mold Design | Custom molds add initial cost, but efficiency increases | Initial cost but reduces waste over time |
Labor Costs | Skilled labor for setup, maintenance, inspection | Complex parts lead to higher labor costs |
Production Volume | Large batches reduce cost per unit | High-volume production makes it cost-effective |
12. What Are the Latest Trends in Aluminum Alloy Die Casting?
The aluminum alloy die casting industry is constantly evolving, driven by advancements in technology and changing market demands. You might be wondering: what are the latest trends in the industry that could impact your project? Let’s explore some of the innovations shaping the future of aluminum die casting.
One significant trend is the rise of 3D printing for mold design. What’s the real story? 3D printing allows manufacturers to create more complex and intricate mold designs faster and at a lower cost compared to traditional methods. This can lead to more efficient die casting processes and the ability to produce parts with more detailed features.
Another trend is the development of new, high-performance alloys. Ready for the good part? Manufacturers are continually experimenting with new aluminum alloys to improve strength, corrosion resistance, and thermal performance. These alloys can expand the range of applications for aluminum die casting, making it an even more attractive option for industries like aerospace and automotive.
Additionally, there is a growing focus on sustainability. As mentioned earlier, aluminum is highly recyclable, and the aluminum die casting process is becoming increasingly eco-friendly. Manufacturers are working to reduce waste, improve energy efficiency, and minimize the environmental impact of their operations. But here’s the kicker: companies are now looking at ways to recycle aluminum more effectively, turning scrap material back into high-quality products without compromising performance.
Finally, automation and smart manufacturing are making their way into the aluminum die casting industry. The use of AI and machine learning is allowing manufacturers to optimize production processes, identify defects earlier, and predict maintenance needs, ultimately improving efficiency and reducing costs.
Trend | Description | Impact |
---|---|---|
3D Printing for Mold Design | Faster, more complex mold designs through 3D printing | Reduces mold costs and production time |
High-Performance Alloys | New alloys for enhanced strength, corrosion resistance | Expands application possibilities |
Sustainability Focus | Eco-friendly production, recycling, energy efficiency | Reduces environmental impact, improves brand image |
Automation & Smart Manufacturing | AI, machine learning optimizing processes | Increases production efficiency, reduces costs |
13. How Long Does It Take to Produce Aluminum Die Castings?
Time is money in manufacturing, and the speed at which aluminum die castings can be produced is an important consideration for many projects. Here’s the deal: the die casting process itself is remarkably fast, with each cycle typically taking only a few seconds to a minute depending on the complexity and size of the part. What’s the real story? A typical die casting cycle includes the injection of molten aluminum into the mold, cooling, and ejection, all of which can be completed quickly.
However, the overall production timeline depends on several factors. What’s the catch? One of the main factors is the design of the part. If the part has complex geometry, it may require longer cooling times or additional steps, which can extend the overall production time. Another factor to consider is the preparation of the mold. This is where it gets interesting: designing and manufacturing the mold can take time, especially for parts with intricate details.
If you’re working with a high-volume production run, the lead time is typically reduced because molds are already in place and the die casting process can be repeated without delay. However, new molds or custom designs may require longer setup times, which can extend the overall timeline.
Ready for the good part? Even with these variables, aluminum die casting is still one of the fastest manufacturing methods for producing complex, high-quality parts.
Factor | Time Impact | Details |
---|---|---|
Part Design | Complex designs may take longer | Intricate geometry requires extended cooling times |
Mold Preparation | Custom molds extend setup time | New molds require time to design and manufacture |
Production Volume | Higher volumes reduce per-unit time | Efficient for large runs |
Cycle Time | Fast cycles, generally 10-60 seconds | Depending on part complexity and size |
14. What Are Common Applications of Aluminum Alloy Die Castings?
Aluminum alloy die casting is used in a wide range of industries due to its versatility and ability to produce lightweight, durable, and cost-effective parts. What’s the real story? Let’s take a look at some of the most common applications of aluminum die castings.
In the automotive industry, aluminum die casting is used to produce lightweight, high-strength parts like engine blocks, transmission cases, and chassis parts. But here’s the kicker: aluminum parts help reduce vehicle weight, improving fuel efficiency and performance.
The aerospace sector also relies heavily on aluminum die casting for producing lightweight and durable parts for aircraft and spacecraft. Components like aircraft frames, engine parts, and housings benefit from aluminum’s high strength-to-weight ratio and excellent corrosion resistance.
In electronics, aluminum die casting is used to produce durable and efficient housings for devices like smartphones, laptops, and power supplies. This is where it gets interesting: aluminum’s excellent thermal conductivity helps dissipate heat, making it ideal for electronic components that generate heat.
Ready for the good part? Even industries like telecommunications, construction, and medical devices use aluminum die casting to create components that are both reliable and cost-effective.
Industry | Key Applications | Benefits of Aluminum Die Casting |
---|---|---|
Automotive | Engine blocks, transmission cases, chassis | Weight reduction, fuel efficiency |
Aerospace | Aircraft frames, engine components | Strength, lightness, corrosion resistance |
Electronics | Device housings, power supplies | Thermal conductivity, durability |
Medical Devices | Surgical instruments, diagnostic equipment | Precision, strength, reliability |
15. What Are the Key Benefits of Choosing Aluminum Alloy Die Casting for Your Project?
Choosing aluminum alloy die casting for your project offers a wide array of benefits that make it a top choice for many industries. What’s the real story? Let’s recap the key reasons why aluminum die casting is an excellent choice for your manufacturing needs.
First, aluminum alloys are lightweight yet strong, offering a great combination of performance and cost. This makes aluminum die casting ideal for applications where strength and weight reduction are important, such as in automotive and aerospace industries. But here’s the kicker: aluminum also has excellent corrosion resistance, ensuring that parts made from it will last longer and require less maintenance.
Aluminum die casting also offers great precision, which means that you can produce parts with very tight tolerances and excellent surface finishes. Ready for the good part? The ability to produce parts with such high accuracy reduces the need for additional machining, saving both time and money.
What’s the catch? Aluminum alloy die casting is a cost-effective solution, especially for high-volume production runs. The process is fast, and molds can be used to produce thousands of parts, making it an ideal choice for mass production.
Finally, aluminum die casting is a sustainable manufacturing method, thanks to aluminum’s recyclability and the energy-efficient nature of the process. This makes it a smart choice for companies looking to reduce their environmental impact while maintaining high-quality standards.
Benefit | Details | Impact |
---|---|---|
Lightweight yet Strong | Great combination of strength and lightness | Ideal for automotive, aerospace applications |
Corrosion Resistance | Ensures longer lifespan and less maintenance | Reduces long-term costs |
Precision | High accuracy with tight tolerances | Reduces need for additional machining |
Cost-Effectiveness | Especially beneficial for high-volume runs | Reduces unit cost in mass production |
Sustainability | Recyclable material and energy-efficient process | Eco-friendly, reduces waste |
FAQ Section
Q1: What is aluminum alloy die casting?
Aluminum alloy die casting is a manufacturing process in which molten aluminum is injected into a steel mold under high pressure to create detailed and high-strength parts.
Q2: How does aluminum alloy die casting work?
The process involves melting aluminum, injecting it into a mold at high pressure, and allowing it to cool and solidify. The part is then removed and inspected for defects.
Q3: What types of aluminum alloys are used in die casting?
Common alloys used in die casting include A380, A360, and A413. Each offers unique properties such as corrosion resistance, strength, and fluidity, making them suitable for various applications.
Q4: How can I choose the right aluminum alloy for my project?
Consider factors such as the required strength, corrosion resistance, and budget. Each alloy has specific characteristics, so understanding your project’s needs will help you make the best choice.
Q5: What industries use aluminum alloy die casting?
Industries such as automotive, aerospace, electronics, and telecommunications use aluminum die casting for its strength, durability, and cost-effectiveness in producing precision parts.