Aluminum investment casting is a highly precise manufacturing process used for creating detailed parts from aluminum alloys. It involves pouring molten aluminum into a mold made from a pattern, typically created from wax or other materials. This method is essential in industries like aerospace, automotive, and medical devices, where precision and strength are critical. In this article, we’ll explore how the aluminum investment casting process works, its benefits, and why it’s a preferred method for producing high-quality aluminum components.
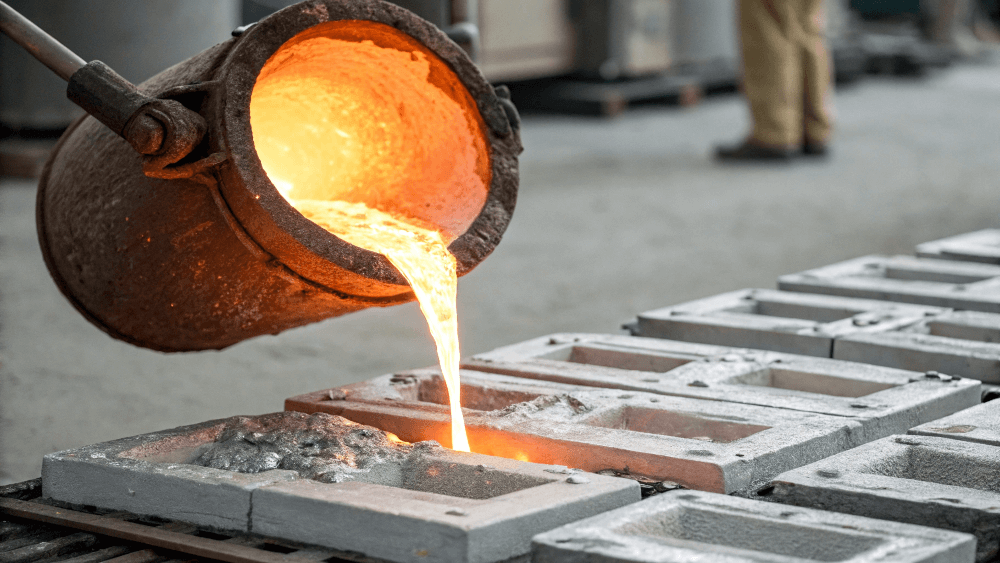
1. What is Aluminum Investment Casting?
When looking to create precise and durable aluminum parts, aluminum investment casting is a go-to solution. This process is widely used across various industries, including aerospace and automotive, due to its ability to deliver complex shapes with tight tolerances. So, what exactly is aluminum investment casting? Well, it’s a type of metal casting where a molten aluminum alloy is poured into a pre-made mold to form a part.
The process begins with creating a pattern, often from wax, which is later coated in a ceramic material. After the pattern is formed, it’s coated in a fine ceramic material to create the mold. This coating hardens over time, and once it’s fully set, the mold is heated to remove the wax, leaving a cavity that matches the shape of the original pattern.
Next, molten aluminum is poured into the cavity created by the shell. The temperature and flow of the molten metal are controlled to prevent defects. After the metal has cooled and solidified, the ceramic shell is broken away, leaving behind the aluminum casting.
But here’s the kicker: The aluminum investment casting process not only allows for intricate designs but also enhances the material properties of the finished component, making it strong and lightweight. This process is particularly valuable when manufacturing components that are critical in industries requiring high performance, such as aerospace, automotive, and medical equipment.
Table 1: Advantages of Aluminum Investment Casting
Advantage | Description |
---|---|
High Precision | Ability to produce parts with tight tolerances and intricate details. |
Durability | Aluminum castings are known for their strength and resistance to corrosion. |
Cost-Effective | Reduced waste and the need for fewer post-production processes make it an efficient choice. |
Complexity | Capable of producing highly complex shapes that would be difficult or impossible with other methods. |
2. How Does the Aluminum Investment Casting Process Work?
Ready for the good part? The aluminum investment casting process may seem complex, but it follows a series of precise steps that ensure the final product meets stringent specifications. Let’s break it down.
The process begins with the creation of a model or pattern, often using wax. This pattern is typically a replica of the component to be cast. After the pattern is formed, it’s coated in a fine ceramic material to create the mold. Once the coating has hardened, the mold is heated to remove the wax, leaving a cavity.
Next, molten aluminum is poured into the cavity created by the shell. The temperature and flow of the molten metal are controlled to prevent defects. After the metal has cooled and solidified, the ceramic shell is broken away, leaving behind the aluminum casting.
This is where it gets interesting: The mold must be designed to handle the thermal expansion of the molten aluminum. Engineers must account for this factor when designing molds for investment casting to ensure the finished part meets all specifications.
Table 2: Steps in Aluminum Investment Casting Process
Step | Description |
---|---|
Pattern Creation | A wax pattern is created using precision tools to match the part design. |
Shell Formation | The wax pattern is coated with ceramic to create a hard mold. |
Wax Removal | The mold is heated to remove the wax, leaving a cavity. |
Metal Pouring | Molten aluminum is poured into the cavity to form the part. |
Shell Removal | The ceramic shell is broken away once the metal has solidified. |
3. What Are the Benefits of Aluminum Investment Casting?
What’s the real story behind aluminum investment casting? Let’s look at the numerous benefits that make it the preferred choice for high-precision components.
Aluminum investment casting offers several key advantages. First, it provides unparalleled precision. Parts can be manufactured with extremely tight tolerances, which is essential for industries where even slight deviations can lead to failure. This is particularly important in aerospace, automotive, and medical sectors, where safety and performance are paramount.
Next, investment casting allows for complex shapes that might be difficult or impossible to achieve with other methods. Complex geometries, intricate designs, and internal features can all be cast in one go, reducing the need for additional machining or assembly.
But here’s the kicker: Another major benefit of aluminum investment casting is material efficiency. Since the casting process creates minimal waste compared to other methods, it reduces overall material costs and environmental impact. Additionally, aluminum itself is lightweight yet strong, making it ideal for industries that require durable yet lightweight parts.
Table 3: Key Benefits of Aluminum Investment Casting
Benefit | Description |
---|---|
Precision | Tight tolerances and intricate details can be achieved. |
Complex Shapes | The method allows for highly complex designs and geometries. |
Material Efficiency | Less waste compared to other casting methods. |
Lightweight Strength | Aluminum offers strength without the added weight. |
4. What Types of Aluminum Are Used in Investment Casting?
The key to high-quality aluminum castings lies in choosing the right type of aluminum alloy. So, how do you pick the right alloy for your casting project? It all depends on the application and the desired properties of the finished part.
Aluminum alloys for investment casting are typically categorized into different series based on their composition and properties. The most commonly used alloys are from the 300, 400, and 500 series, as they offer a good balance of strength, ductility, and corrosion resistance. Each alloy has its own advantages, so selecting the right one requires understanding the specific needs of your application.
For example, the 356 alloy is one of the most widely used in aluminum investment casting due to its excellent castability, strength, and resistance to corrosion. It’s ideal for applications in automotive and aerospace sectors. Similarly, the 713 alloy is often used for high-strength applications that require better heat resistance.
Table 4: Common Aluminum Alloys for Investment Casting
Alloy | Applications | Properties |
---|---|---|
356 | Aerospace, automotive, medical devices | High strength, corrosion resistance |
713 | High-stress components | High heat resistance, strength |
A356 | Automotive, aerospace, industrial parts | Excellent castability, fatigue resistance |
5. How Does Aluminum Investment Casting Compare to Other Casting Methods?
So, why choose aluminum investment casting over other casting methods? The answer lies in the unique capabilities this method offers.
Aluminum investment casting differs from other methods like sand casting or die casting in several ways. Sand casting is more cost-effective for larger parts but doesn’t offer the same level of precision or complexity. Die casting, on the other hand, is faster and better suited for mass production, but it’s typically limited to simpler shapes.
In comparison, aluminum investment casting stands out due to its ability to create highly detailed and complex parts without the need for extensive post-processing. The investment casting method allows for greater design flexibility and higher-quality finishes, which is why it’s commonly used in industries where performance and precision are critical.
Table 5: Comparison of Aluminum Casting Methods
Casting Method | Advantages | Limitations |
---|---|---|
Investment Casting | High precision, complex shapes, good finish | Higher upfront costs |
Sand Casting | Low cost for large parts, simple molds | Lower precision, rough finish |
Die Casting | Fast production, good for high volumes | Limited to simpler shapes, higher tooling costs |
6. What Are the Common Applications of Aluminum Investment Casting?
Aluminum investment casting is used in a wide range of industries where strength, precision, and reliability are crucial. Let’s dive into some of the most common applications.
In the aerospace industry, aluminum investment casting is used to produce parts like engine components, turbine blades, and brackets. These components require high strength-to-weight ratios and must perform under extreme conditions, making aluminum’s lightweight yet durable properties a perfect fit.
Similarly, the automotive industry uses aluminum investment casting to manufacture parts such as engine blocks, wheels, and suspension components. These parts need to be both strong and lightweight to improve vehicle performance and fuel efficiency.
But here’s the kicker: Aluminum investment casting is also used in the medical industry for precision equipment such as surgical instruments and medical devices. These components need to meet stringent standards for durability and safety, making investment casting an ideal method for production.
Table 6: Applications of Aluminum Investment Casting
Industry | Applications | Benefits |
---|---|---|
Aerospace | Engine components, turbine blades, brackets | High strength-to-weight ratio, performance under extreme conditions |
Automotive | Engine blocks, wheels, suspension components | Lightweight, strong parts for improved fuel efficiency and performance |
Medical Devices | Surgical instruments, medical components | High precision and safety standards |
Industrial | Machinery parts, gears, valves | High strength and durability for industrial use |
7. How Do You Choose the Right Supplier for Aluminum Investment Casting?
Choosing the right supplier for your aluminum investment casting needs is crucial for ensuring the quality and reliability of the finished product. But how do you find the right one?
First, look for suppliers with experience in your industry. For example, if you’re in aerospace, you’ll want a supplier that specializes in high-precision, high-performance parts. Make sure to check their track record with other clients and assess whether their expertise aligns with your specific requirements.
Next, consider the supplier’s quality assurance processes. A good supplier should have certifications like ISO 9001 to demonstrate their commitment to quality. Also, ensure they have robust testing and inspection procedures in place to catch any potential defects before delivery.
Finally, be sure to ask about their lead times and flexibility. You’ll want a supplier who can meet your production timelines and handle any unforeseen changes or demands.
Table 7: Criteria for Choosing an Aluminum Investment Casting Supplier
Criteria | Description |
---|---|
Industry Experience | Supplier should have experience in your specific industry. |
Quality Assurance | Check for certifications such as ISO 9001 and quality processes. |
Lead Time | Ensure the supplier can meet your production schedules. |
Flexibility | Supplier should be adaptable to changes in demand or design. |
8. What Are the Challenges in Aluminum Investment Casting?
When it comes to aluminum investment casting, it’s not all smooth sailing. While the process offers numerous benefits, there are several challenges that manufacturers must overcome to achieve high-quality results. But here’s the kicker: the challenges faced during investment casting can often be managed with the right precautions and adjustments.
One of the most common challenges in aluminum investment casting is dealing with mold defects. These defects can occur during the shell formation or when the molten aluminum doesn’t flow evenly into the mold. Incomplete mold filling, misalignment, or porosity issues can all affect the final part quality. To mitigate these issues, manufacturers must carefully control the mold temperature and the pouring speed of molten aluminum.
Another issue that often arises is shrinkage. As aluminum cools, it contracts, which can lead to voids or cracks in the finished part. Shrinkage must be accounted for when designing the pattern, ensuring that the mold is properly prepared to compensate for this contraction. Specialized computer simulations and modeling can help predict and minimize these risks.
But here’s where it gets interesting: post-casting treatments are another critical aspect of overcoming challenges in aluminum investment casting. Heat treatments like aging or annealing are often used to improve the mechanical properties of the castings, such as strength and hardness, helping to ensure they meet the required specifications.
Table 8: Common Challenges in Aluminum Investment Casting
Challenge | Description | Solution |
---|---|---|
Mold Defects | Issues like cracks or incomplete fillings in the mold | Careful mold design, temperature control, and pouring speed |
Shrinkage | Metal contraction during cooling, leading to defects | Design adjustments, mold preparation, and simulations |
Porosity | Tiny holes or cavities in the final part | Improved alloy selection and post-casting treatments |
Material Contamination | Impurities in the aluminum can affect quality | Proper cleaning and handling of materials |
Complexity | High precision and complex shapes can be difficult | Advanced tooling and design expertise |
9. How Can Aluminum Investment Casting Help with Product Development?
Aluminum investment casting is not only ideal for large-scale production but can also play a vital role in product development. So, what’s the real story? Let’s look at how it facilitates rapid prototyping and low-volume production.
One of the key advantages of aluminum investment casting is its ability to produce intricate prototypes that can be tested for form, fit, and function before committing to mass production. Designers can quickly iterate on their designs, ensuring they meet all the necessary requirements for performance, durability, and safety.
For small businesses or startups, aluminum investment casting is a game changer. It allows you to produce high-quality, low-volume parts without the significant upfront costs associated with traditional manufacturing methods. This means companies can launch new products with minimal investment, providing flexibility and agility in their production processes.
And here’s the kicker: the investment casting process is also perfect for creating customized parts. Whether it’s a unique design or a limited-edition item, the casting process offers the flexibility to cater to specific product requirements, which is often hard to achieve with other methods like injection molding or stamping.
Table 9: Benefits of Aluminum Investment Casting for Product Development
Benefit | Description |
---|---|
Rapid Prototyping | Quickly produce prototypes for testing and validation. |
Low-Volume Production | Enables low-volume runs without excessive costs. |
Customization | High flexibility for custom designs and unique parts. |
Cost-Efficiency | Reduced initial tooling and setup costs compared to other methods. |
Quick Turnaround | Faster production times compared to traditional manufacturing methods. |
10. What Are the Environmental Considerations in Aluminum Investment Casting?
Aluminum is a widely used and environmentally friendly material, but it’s important to understand the environmental implications of the investment casting process. Here’s what you need to know.
First, the aluminum alloy used in casting is highly recyclable. In fact, aluminum is one of the most recycled metals in the world, and it retains its properties after recycling, which makes it an excellent sustainable choice. Many aluminum foundries are now incorporating recycled aluminum into their casting processes, reducing the need for virgin materials and lowering the environmental impact.
However, the casting process itself can have some environmental impacts, primarily due to energy consumption. The melting of aluminum requires a significant amount of energy, particularly in large-scale operations. That being said, newer technologies and more energy-efficient furnaces are helping to reduce energy consumption in casting operations.
But here’s the kicker: aluminum investment casting also reduces material waste compared to traditional methods like sand casting. The precision of the process allows for minimal scrap, which is not only environmentally beneficial but also reduces overall material costs.
Table 10: Environmental Considerations in Aluminum Investment Casting
Consideration | Impact | Mitigation |
---|---|---|
Energy Consumption | High energy requirements to melt aluminum | Use of energy-efficient furnaces and renewable energy sources |
Recyclability | Aluminum is highly recyclable, reducing material waste | Use of recycled aluminum to reduce raw material demand |
Waste Reduction | Minimal scrap and waste compared to other methods | Precise mold design and efficient casting techniques |
Emission Control | Potential emissions during casting process | Improved ventilation systems and cleaner technologies |
11. What Are the Costs Associated with Aluminum Investment Casting?
When considering aluminum investment casting, cost is always a critical factor. The process itself can be more expensive than alternatives like sand casting or die casting, but it offers significant long-term benefits in terms of quality and precision.
The initial investment in tooling and setup can be higher than with other methods, especially for more complex designs. However, the high precision and minimal post-casting work required help reduce overall costs in the long run. Additionally, the material efficiency of aluminum investment casting ensures that there’s minimal waste, which can further reduce costs.
But here’s the kicker: when you factor in the longer-term savings from reduced post-production processes, fewer reworks, and higher-quality parts, the overall cost of investment casting becomes more competitive compared to other casting methods. For businesses that need high-quality parts with complex geometries, this method offers a cost-effective solution in the long run.
Table 11: Costs Involved in Aluminum Investment Casting
Cost Factor | Description |
---|---|
Tooling Costs | Higher initial investment for pattern and mold creation. |
Material Costs | Cost of aluminum alloy, which can vary depending on the alloy used. |
Labor Costs | Labor involved in the casting process, including mold creation and metal pouring. |
Production Volume | Investment casting is cost-effective for low- to medium-volume production. |
Post-Production Costs | Minimal finishing work required, which can help save costs. |
12. How Can You Improve the Quality of Aluminum Investment Castings?
Achieving the highest quality in aluminum investment casting is essential for producing parts that meet strict standards. The key to this is a well-managed production process that involves both meticulous planning and stringent quality control.
One of the most effective ways to improve casting quality is by using the right materials. The choice of aluminum alloy plays a major role in determining the overall strength, ductility, and resistance of the final part. Additionally, employing advanced modeling techniques can help predict potential defects before they even occur, allowing for early intervention.
But here’s the kicker: quality control doesn’t stop at material selection. Post-casting treatments such as heat treating, surface polishing, and stress relieving can improve mechanical properties, ensuring that the final part meets the required specifications.
Table 12: Techniques to Improve Aluminum Investment Casting Quality
Technique | Description |
---|---|
Material Selection | Choosing the right alloy to meet application requirements. |
Advanced Simulation | Using modeling software to predict defects and optimize the casting process. |
Post-Casting Treatments | Heat treatments, stress relieving, and surface polishing to enhance quality. |
Strict Quality Control | Implementing rigorous inspection and testing procedures at every stage. |
13. What Are the Latest Trends in Aluminum Investment Casting?
Aluminum investment casting continues to evolve as new technologies and techniques emerge. So, what’s the real story behind the latest trends?
One of the most notable trends is the integration of 3D printing (additive manufacturing) in the casting process. 3D printing allows for more complex designs and quicker pattern creation, reducing the time and costs associated with traditional mold-making.
Another trend is the increased use of recycled aluminum. As industries become more focused on sustainability, there is a growing demand for eco-friendly casting processes. Recycled aluminum not only reduces the environmental impact but also lowers material costs, making it a win-win for both manufacturers and customers.
And here’s where it gets interesting: advancements in smart manufacturing and automation are helping improve efficiency in casting operations. Automated systems for pouring, cooling, and inspection are streamlining the process, reducing human error, and improving overall casting quality.
Table 13: Latest Trends in Aluminum Investment Casting
Trend | Description |
---|---|
3D Printing | Use of additive manufacturing for faster pattern creation. |
Recycled Aluminum | Increased use of recycled aluminum to reduce costs and environmental impact. |
Smart Manufacturing | Automation in the casting process to improve efficiency and quality. |
Material Innovation | Development of new aluminum alloys with better performance characteristics. |
14. How Can Aluminum Investment Casting Benefit Small Businesses?
Aluminum investment casting isn’t just for large corporations. Small businesses can also reap the benefits of this high-precision manufacturing process. So, what’s the catch?
For small businesses, aluminum investment casting offers a way to produce high-quality, customized parts without the need for expensive machinery or tooling. The ability to create complex, low-volume runs makes it ideal for startups and entrepreneurs who need high-quality components without the upfront costs of mass production.
And here’s the kicker: For businesses that need to produce prototypes or limited-edition products, aluminum investment casting provides a cost-effective solution that allows them to test designs and bring innovative products to market quickly.
Table 14: Benefits of Aluminum Investment Casting for Small Businesses
Benefit | Description |
---|---|
Low-Volume Production | Ability to produce small batches of custom parts without high upfront costs. |
Prototyping | Quick turnaround for prototypes and limited-edition runs. |
Cost-Efficient | Reduced costs due to minimal tooling and material waste. |
Customization | Flexibility to create unique designs for specific needs. |
15. How to Get Started with Aluminum Investment Casting?
Ready to take the plunge into aluminum investment casting? Getting started may seem daunting, but with the right approach, it’s a straightforward process.
Start by identifying your needs. Whether you’re looking for prototyping, low-volume production, or complex parts, the first step is to define the scope of your project. Next, find a supplier with experience in aluminum investment casting who can meet your specifications and timelines. Be sure to ask about their previous projects and capabilities.
Finally, collaborate closely with your supplier to refine your designs, choose the right materials, and finalize production schedules. The key is to maintain clear communication throughout the process to ensure the best possible outcome.
Table 15: Steps to Get Started with Aluminum Investment Casting
Step | Description |
---|---|
Define Your Needs | Determine the type of casting required and the quantity. |
Find the Right Supplier | Choose a supplier with experience in your industry. |
Finalize Your Design | Work with the supplier to ensure the design meets specifications. |
Choose Materials | Select the right aluminum alloy for your project. |
Conclusion
In conclusion, aluminum investment casting is a versatile and cost-effective method for producing precise, high-quality parts across industries like aerospace, automotive, and medical devices. The process offers numerous advantages, including precision, durability, and the ability to produce complex shapes with minimal waste. While there are challenges to consider, such as mold defects and shrinkage, these can be managed with the right techniques and expertise.
By understanding the benefits, selecting the right supplier, and leveraging the latest trends and technologies, businesses of all sizes can harness the power of aluminum investment casting to develop products that meet their exact specifications. Whether you’re prototyping, creating low-volume runs, or developing complex components, aluminum investment casting offers a reliable and efficient solution for your manufacturing needs.
FAQ Section
Q1: What is aluminum investment casting?
Aluminum investment casting is a manufacturing process where molten aluminum is poured into a mold to create precise parts, widely used in industries like aerospace, automotive, and medical devices.
Q2: How does the aluminum investment casting process work?
The process involves creating a pattern from wax, coating it in a ceramic shell, removing the wax, and pouring molten aluminum into the mold. Once cooled, the ceramic shell is broken away to reveal the final part.
Q3: What are the benefits of aluminum investment casting?
The main benefits include high precision, the ability to create complex shapes, material efficiency, and the production of lightweight yet strong parts.
Q4: How do I choose the right supplier for aluminum investment casting?
Select a supplier with experience in your industry, quality certifications, and reliable testing procedures. Ensure they can meet your production timelines and handle potential changes.
Q5: What are the common applications of aluminum investment casting?
Aluminum investment casting is used in industries like aerospace, automotive, and medical devices to produce parts that require high precision, strength, and durability.