Die casting is a crucial manufacturing process in various industries, allowing for the creation of precise and durable metal parts. However, many people are unaware of how the die casting process works and the different types, advantages, and applications it holds. Understanding these aspects can help businesses make informed decisions on using die casting in their production.
Die casting is a manufacturing process that involves injecting molten metal into a mold at high pressure to create metal parts. It is commonly used in industries such as automotive, electronics, and consumer goods manufacturing. The process delivers high-quality, precise, and durable metal parts at scale.
As we dive deeper into the process, we will explore how die casting can benefit your business and why it’s a preferred method for high-volume metal parts production.
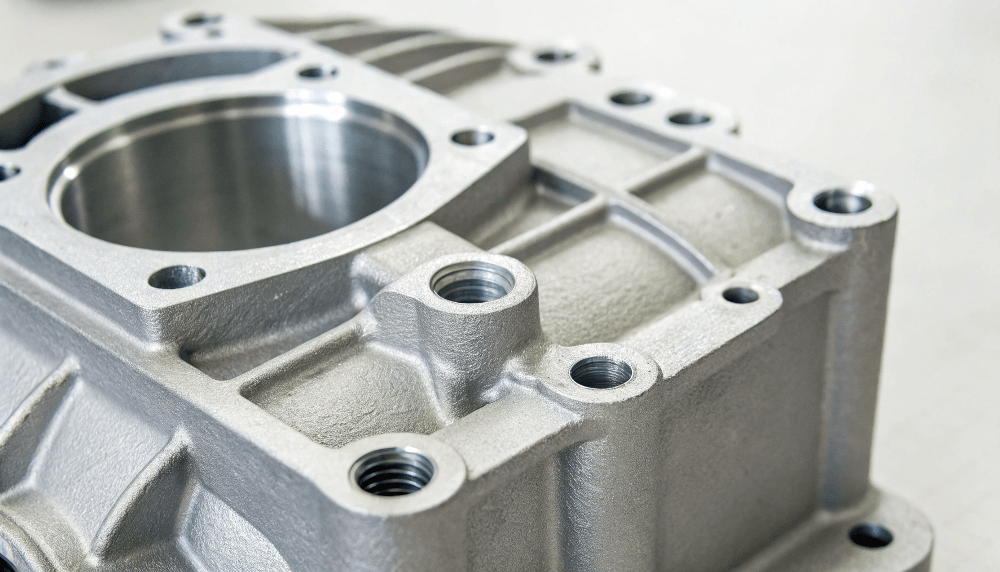
1. What is the Die Casting Process?
The die casting process is crucial for producing parts with exceptional precision and high quality. By understanding how it works, businesses can harness the power of this technique for optimal results.
The die casting process involves injecting molten metal into a mold under high pressure, allowing it to cool and solidify into the desired shape. This method ensures a consistent and high-quality finish on parts that are often complex and intricate.
Die casting is used in numerous industries for its ability to produce parts with high tolerance levels, strength, and detailed features. In this section, we will explore the step-by-step process involved in die casting, the materials used, and the machines that drive this efficient method.
Step-by-Step Process of Die Casting
The die casting process involves several key steps, each contributing to the final product’s quality. These steps are outlined below:
Step | Process Description |
---|---|
1 | Melting the Metal: The process begins by heating the selected metal alloy until it becomes molten. |
2 | Injection into the Die: The molten metal is injected into a die (mold) under high pressure. |
3 | Cooling: Once the metal fills the mold, it cools and solidifies, taking the shape of the die. |
4 | Ejection: After cooling, the die is opened, and the solidified part is ejected. |
5 | Trimming: Any excess material or flash is trimmed from the part for a clean finish. |
Materials Used in Die Casting
Die casting typically uses alloys that have excellent flow properties and can withstand high pressures. Some common materials include:
Material | Properties |
---|---|
Zinc Alloys | Good strength and excellent corrosion resistance, commonly used for small parts. |
Aluminum Alloys | Lightweight and durable, suitable for automotive and aerospace applications. |
Magnesium Alloys | The lightest of the die-casting alloys, used in applications where weight is a critical factor. |
Machines Used in Die Casting
There are two main types of die casting machines used, and each serves different purposes:
Machine Type | Description |
---|---|
Cold Chamber Die Casting Machine | Used for metals with high melting points, such as aluminum alloys. |
Hot Chamber Die Casting Machine | Used for metals with lower melting points, such as zinc alloys. |
By understanding the materials and machines used, businesses can choose the right die casting process for their specific needs.
2. What Are the Different Types of Die Casting?
Die casting is not a one-size-fits-all process. There are several different types, each suitable for specific applications. Knowing which type to use can help businesses optimize production and reduce costs.
There are three main types of die casting: high-pressure die casting, low-pressure die casting, and gravity die casting. Each type has distinct advantages based on the materials and production volumes involved.
High-Pressure Die Casting
This is the most commonly used die casting method. High-pressure die casting involves injecting molten metal into the mold under high pressure. This method is fast and efficient, ideal for mass production of small to medium-sized parts.
Low-Pressure Die Casting
Low-pressure die casting uses lower injection pressures and is typically used for larger parts that require a more controlled flow of molten metal. This method is often used in industries such as automotive and aerospace for producing complex parts.
Gravity Die Casting
Gravity die casting, or permanent mold casting, involves pouring molten metal into a mold under the force of gravity. It is used for larger parts where high pressure is not necessary.
Die Casting Type | Advantages | Applications |
---|---|---|
High-Pressure | Fast, precise, and suitable for mass production | Small to medium-sized parts, automotive, consumer electronics |
Low-Pressure | Controlled metal flow, suitable for larger parts | Automotive, aerospace, industrial parts |
Gravity Die | Cost-effective, for large parts with simple designs | Large parts in automotive, construction |
3. What Are the Advantages of Die Casting?
Die casting offers several advantages over other manufacturing methods. Understanding these benefits can help businesses decide if die casting is the right choice for their production needs.
The main advantages of die casting include precision, speed, and cost-effectiveness. These benefits make it a preferred method for high-volume production in industries like automotive, aerospace, and electronics.
Precision and Accuracy
Die casting allows for the production of parts with high precision and tight tolerances, making it ideal for applications that require exact dimensions and detailed features.
Speed and Efficiency
The die casting process is highly efficient, enabling the production of large quantities of parts in a short time. This makes it suitable for industries that need to meet high demand and tight deadlines.
Cost-Effectiveness
Despite its high initial tooling cost, die casting is cost-effective for large-scale production. The reduced need for secondary operations and high-speed production help lower overall manufacturing costs.
Advantage | Description |
---|---|
Precision | High tolerances and detailed parts |
Speed | Fast production rates, ideal for high-volume runs |
Cost-Effectiveness | Low unit costs with large quantities |
4. What Applications Does Die Casting Have?
Die casting is widely used in various industries for the production of parts that require high strength, durability, and precision.
Die casting is used in a wide range of industries, including automotive, aerospace, and consumer electronics. Its ability to produce complex and durable parts makes it an essential technique in modern manufacturing.
Automotive Industry
The automotive industry uses die casting for producing parts like engine blocks, transmission cases, and brake components. The precision and strength of die-cast parts help improve the performance and safety of vehicles.
Aerospace Industry
Die casting is used in the aerospace industry to create lightweight yet strong components such as brackets, housings, and fuel system parts. The high-quality finish and durability of die-cast parts are crucial in this sector.
Electronics Manufacturing
In electronics, die casting is used to create housings for devices like smartphones, laptops, and TVs. The process ensures the components are precise and heat resistant.
Industry | Application | Benefits |
---|---|---|
Automotive | Engine blocks, transmission cases | High strength, precise tolerances |
Aerospace | Brackets, housings, fuel system parts | Lightweight, durable components |
Electronics | Device housings, heat sinks | Precision, heat resistance |
5. How Does Die Casting Compare to Other Manufacturing Methods?
Die casting is not the only option available when it comes to producing metal parts. It’s important to understand how it compares to other manufacturing methods, such as injection molding, sand casting, and investment casting. This comparison will help businesses decide which method is the best fit for their needs.
Die casting offers several distinct advantages over other manufacturing methods, particularly in terms of speed, precision, and cost-effectiveness. However, there are situations where other casting methods may be more suitable based on the product’s size, complexity, and material requirements.
Die Casting vs. Injection Molding
Injection molding and die casting are both used for mass production of parts, but they differ in the materials they use and the types of parts they can produce.
Feature | Die Casting | Injection Molding |
---|---|---|
Materials | Metals (zinc, aluminum, magnesium) | Plastics, rubber |
Precision | High precision with tight tolerances | High precision with tight tolerances |
Part Size | Suitable for small to medium-sized parts | Suitable for small to medium-sized parts |
Speed | Fast production with high output | Fast production with high output |
Cost | Higher initial tooling costs | Lower initial tooling costs |
Applications | Automotive, aerospace, electronics | Consumer goods, medical devices, packaging |
Die Casting vs. Sand Casting
Sand casting is a traditional casting method that uses sand to create molds for metal parts. While sand casting can be cost-effective for producing large parts, it lacks the precision and speed of die casting.
Feature | Die Casting | Sand Casting |
---|---|---|
Materials | Metals (zinc, aluminum, magnesium) | Metals (iron, steel, aluminum) |
Precision | High precision with tight tolerances | Lower precision, rougher finish |
Part Size | Small to medium-sized parts | Larger parts with simple designs |
Speed | Fast production with high output | Slower production with higher labor costs |
Cost | Higher initial tooling costs, lower unit costs | Lower initial tooling costs, higher unit costs |
Applications | Automotive, aerospace, electronics | Large components like engine blocks, pump housings |
Die Casting vs. Investment Casting
Investment casting, also known as lost-wax casting, is often used for producing parts with intricate designs and fine details. It offers higher precision than sand casting, but the process is slower and more expensive.
Feature | Die Casting | Investment Casting |
---|---|---|
Materials | Metals (zinc, aluminum, magnesium) | Metals (steel, stainless steel, bronze) |
Precision | High precision with tight tolerances | Very high precision with fine details |
Part Size | Small to medium-sized parts | Small to medium-sized parts with complex shapes |
Speed | Fast production with high output | Slower production due to multiple steps |
Cost | Higher initial tooling costs, lower unit costs | Higher initial costs and unit costs |
Applications | Automotive, aerospace, electronics | Aerospace, medical devices, jewelry |
6. What Materials Are Used in Die Casting?
The choice of material is crucial in die casting, as it determines the properties, strength, and durability of the final product. Different metals and alloys are used based on the application requirements, each offering unique benefits.
Common die casting materials include zinc, aluminum, and magnesium alloys, with each offering distinct advantages depending on the application. These materials are chosen for their ability to flow easily into molds, resistance to corrosion, and strength-to-weight ratio.
Zinc Alloys
Zinc alloys are widely used in die casting due to their excellent flow properties and durability. They are commonly used in automotive, electronics, and consumer goods manufacturing.
Aluminum Alloys
Aluminum alloys are lightweight, strong, and highly resistant to corrosion. They are used in a variety of industries, including automotive, aerospace, and electronics.
Magnesium Alloys
Magnesium alloys are the lightest of the die-casting materials. They are typically used in applications where weight is a critical factor, such as in the automotive and aerospace industries.
Material | Properties | Applications |
---|---|---|
Zinc Alloys | Good strength, corrosion resistance, and excellent casting flow | Automotive, electronics, consumer goods |
Aluminum Alloys | Lightweight, strong, corrosion-resistant | Automotive, aerospace, electronics |
Magnesium Alloys | Lightest, good strength-to-weight ratio | Automotive, aerospace, military |
7. How Does the Die Casting Machine Work?
Die casting machines are essential to the process, using either cold or hot chamber designs depending on the material being cast. These machines work by injecting molten metal into a die under high pressure, where it cools and solidifies.
Die casting machines are crucial for ensuring the quality and consistency of the parts produced. Understanding how these machines work will help businesses optimize their die casting operations and improve production efficiency.
Cold Chamber Die Casting Machines
Cold chamber die casting machines are used for materials with high melting points, such as aluminum alloys. The molten metal is poured into the chamber manually, where it is then injected into the die under high pressure.
Hot Chamber Die Casting Machines
Hot chamber die casting machines are used for materials with lower melting points, such as zinc alloys. In this type of machine, the molten metal is maintained in the chamber, and the injection process is more continuous.
Machine Type | Description | Common Uses |
---|---|---|
Cold Chamber | Manual feeding of molten metal into the chamber | Aluminum, magnesium alloys |
Hot Chamber | Continuous molten metal injection into the chamber | Zinc alloys, lead-based alloys |
8. What Are the Challenges of Die Casting?
Despite its many advantages, die casting presents some challenges that businesses need to consider. These challenges range from technical issues to economic factors that could affect the overall efficiency of production.
The most common challenges in die casting include porosity, incomplete filling of the mold, and die wear. These issues can affect the quality of the parts produced and increase production costs.
Common Die Casting Problems
Problem | Cause | Solution |
---|---|---|
Porosity | Air trapped in the molten metal during casting | Improve injection speed, use vacuum-assisted die casting |
Incomplete Filling | Low injection pressure or improper mold design | Increase pressure, optimize mold design |
Die Wear | Frequent production cycles causing damage to the die | Regular maintenance, use high-quality die materials |
9. What Are the Environmental Impacts of Die Casting?
Die casting, like any manufacturing process, has an environmental impact. From energy consumption to material waste, businesses must be mindful of the ecological footprint their operations leave behind.
The environmental impacts of die casting can be managed through proper waste disposal, energy-efficient machines, and recycling efforts. Many die casting companies are working to reduce their carbon footprint by implementing sustainable practices.
Energy Consumption in Die Casting
Die casting machines require significant energy to melt and inject the metal into molds. However, newer, more energy-efficient machines are helping reduce energy consumption and lower operational costs.
Recycling in Die Casting
Recycling scrap metal from the die casting process is an important step in reducing waste. Recycled materials are often used to create new die-cast parts, helping to conserve natural resources.
Environmental Factor | Impact | Mitigation Strategies |
---|---|---|
Energy Consumption | High energy use for metal melting and injection | Use energy-efficient die casting machines |
Waste Management | Scrap metal and waste generated during production | Implement recycling programs and reduce waste |
Carbon Emissions | Emissions from high-energy processes | Adopt green technologies and renewable energy sources |
By understanding these environmental challenges, businesses can take proactive measures to reduce their ecological impact while maintaining production efficiency.
10. How Do You Ensure Quality in Die Casting?
Ensuring the quality of die-cast parts is essential for businesses aiming to produce reliable and high-performance components. High-quality die casting requires strict quality control measures throughout the production process.
Quality in die casting is ensured by performing thorough inspections and using advanced technologies to detect defects. This involves checking for issues like porosity, cracks, and dimensional accuracy.
Inspection Techniques for Die-Cast Parts
There are various inspection methods used to ensure the quality of die-cast parts. These methods include visual inspection, X-ray inspection, and dimensional measurement.
Inspection Method | Description | Applications |
---|---|---|
Visual Inspection | A simple visual check to spot surface defects | Surface finish, obvious cracks, and deformities |
X-ray Inspection | Detects internal defects such as porosity or air pockets | High-precision components, aerospace, automotive |
Dimensional Measurement | Measures the dimensions of the part against a blueprint | Ensures the part meets the specified tolerances |
Importance of Die Life and Maintenance
Die life is a key factor in maintaining consistent quality and minimizing production downtime. Regular maintenance and proper die treatment can extend die life and ensure smooth operations.
Maintenance Type | Frequency | Benefit |
---|---|---|
Die Lubrication | Regular lubrication to reduce wear | Prevents sticking, reduces wear on molds |
Die Cleaning | Periodic cleaning of the die | Removes residue and ensures clean, accurate casts |
Die Repair | As needed based on inspection | Extends die life, prevents costly downtime |
11. What Are the Costs Involved in Die Casting?
Die casting offers cost-efficiency in high-volume production, but there are several cost factors to consider. Businesses need to understand these costs to assess whether die casting is the best option for their needs.
The costs involved in die casting include initial tooling, material costs, and labor costs. The complexity of the part, the material used, and the volume of production can also impact the overall cost.
Cost Breakdown of Die Casting
Cost Factor | Description | Impact on Cost |
---|---|---|
Tooling Costs | Initial cost to design and manufacture the die | High upfront cost, amortized over high-volume production |
Material Costs | Cost of the metal alloy used for casting | Varies based on material type (e.g., aluminum, zinc) |
Labor Costs | Wages for machine operators and quality control staff | Higher for skilled labor, lower for automated systems |
How Die Size and Complexity Affect Cost
The size and complexity of the die-cast part play a significant role in determining the cost. Larger or more complex parts require more intricate dies and longer production times, leading to higher costs.
Part Size | Complexity | Cost Impact |
---|---|---|
Small & Simple | Basic design | Lower tooling and production costs |
Large & Complex | Intricate features, multiple cavities | Higher tooling costs, longer production time |
12. How to Choose the Right Die Casting Supplier?
Choosing the right supplier is essential to ensure the quality and timely delivery of die-cast parts. There are several factors to consider when selecting a die casting supplier.
Choosing the right supplier involves evaluating their experience, capabilities, and reputation. Businesses should look for suppliers with a strong track record in delivering high-quality, cost-effective parts on time.
Factors to Consider When Choosing a Supplier
Factor | Description | Why It Matters |
---|---|---|
Experience | Look for suppliers with years of experience in die casting | More experience means better understanding of processes and fewer errors |
Capabilities | Assess whether the supplier can handle your production volume and complexity | Ensures the supplier can meet your specific needs |
Reputation | Check customer reviews and past work | A reputable supplier is more likely to deliver quality results |
Location | Consider the supplier’s location for shipping and delivery logistics | Shorter distances reduce shipping costs and lead time |
Red Flags to Watch for in Die Casting Suppliers
Some warning signs can indicate potential issues with a die casting supplier. These include poor communication, lack of experience in your industry, and an unwillingness to provide samples or references.
Red Flag | Why It’s a Concern |
---|---|
Poor Communication | Could lead to misunderstandings and delays |
Lack of Experience in Your Industry | The supplier may not understand the specific challenges your parts require |
Unwillingness to Provide Samples or References | Indicates a lack of transparency or confidence in their work |
13. What is the Future of Die Casting?
The future of die casting is shaped by advancements in technology, automation, and material science. Understanding these trends can help businesses stay competitive and optimize their die casting operations.
The die casting industry is evolving with the introduction of automation, AI-driven processes, and new materials that improve efficiency and sustainability. These trends are expected to drive growth and innovation in the coming years.
Trends in Die Casting Technology
Trend | Description | Potential Impact |
---|---|---|
Automation | Use of robotic arms and AI to streamline production | Reduced labor costs, faster production, higher consistency |
3D Printing for Tooling | Utilizing 3D printing to create die molds and components | More flexibility in design, faster prototyping |
Advanced Materials | Use of new alloys and composites | Improved performance, lightweight, more durable parts |
Role of Automation in Die Casting
Automation is revolutionizing die casting by replacing manual labor with robots and AI. This improves production speed and reduces errors, resulting in lower costs and faster turnaround times.
Automation Level | Application | Benefits |
---|---|---|
Low-Level Automation | Use of machines with minimal human interaction | Lower costs, faster production |
High-Level Automation | Full robotic systems with AI and machine learning | High precision, faster cycles, minimal human error |
14. How to Get Started with Die Casting for Your Business?
If you’re considering die casting for your business, it’s important to take the right steps to integrate this process effectively. Understanding the initial requirements and setting up proper operations will help ensure smooth implementation.
Getting started with die casting involves selecting the right equipment, training your staff, and finding a reliable supplier. It’s also crucial to test the process on a small scale before committing to large-scale production.
Steps to Implement Die Casting in Your Business
Step | Description | Importance |
---|---|---|
Research and Evaluate | Understand the die casting process and its benefits for your product | Helps determine if die casting is suitable for your needs |
Select the Right Equipment | Choose the appropriate die casting machine and molds | Ensures efficient production and quality output |
Partner with a Supplier | Work with an experienced die casting supplier | Ensures the quality and consistency of the parts produced |
Test Small-Scale Production | Run trials to ensure the process meets your expectations | Identifies potential issues before large-scale production |
15. How to Optimize Die Casting for Maximum Efficiency?
Optimizing die casting operations can lead to significant cost savings and improved production speed. By adopting best practices and continuously refining the process, businesses can increase the efficiency of their die casting operations.
Optimizing die casting involves using the right equipment, improving the quality control process, and reducing material waste. Regular training and process improvements can also lead to higher productivity and lower costs.
Best Practices for Die Casting Optimization
Practice | Description | Benefit |
---|---|---|
Routine Maintenance | Regularly maintain die casting machines to prevent breakdowns | Reduces downtime, improves machine longevity |
Employee Training | Train employees on best practices and new technologies | Ensures efficiency, reduces errors |
Material Management | Optimize material use to reduce waste | Reduces material costs, improves sustainability |
By focusing on these optimization strategies, businesses can enhance their die casting operations, resulting in cost savings and better quality control.
Conclusion
Die casting is a versatile and efficient manufacturing process that offers numerous benefits for businesses in various industries. By understanding the die casting process, types, advantages, and applications, you can make informed decisions about integrating this technique into your production line. Whether you’re in the automotive, aerospace, or electronics industries, die casting provides the precision, efficiency, and cost-effectiveness needed for high-quality production.
FAQ Section
Q1: What is die casting?
Die casting is a manufacturing process where molten metal is injected into a mold under high pressure to produce parts with high precision.
Q2: How does the die casting process work?
The process involves melting metal, injecting it into a mold under pressure, cooling it to solidify, and then ejecting the part.
Q3: What are the types of die casting?
The main types of die casting are high-pressure, low-pressure, and gravity die casting. Each type is used for specific applications based on the size and complexity of the parts.
Q4: What materials are used in die casting?
Common materials include zinc, aluminum, and magnesium alloys, which offer different properties like strength, durability, and lightweight.
Q5: What are the advantages of using die casting?
Die casting offers advantages such as high precision, speed, and cost-effectiveness, making it ideal for mass production of durable parts.