Manganese steel casting is one of the most versatile and durable alloys used in heavy industries. The unique properties of manganese steel make it ideal for tough applications that require resistance to wear and impact. But why should you choose it? Let’s explore its benefits and applications in detail.
Manganese steel is a high-strength material with exceptional toughness and wear resistance. Its alloys make it highly suitable for industries requiring durability under stress. Let’s dive deeper into its advantages and how it is used in various sectors.
Choosing the right material for your industrial needs can be a challenge, but manganese steel provides long-term solutions. Whether you’re in mining, construction, or automotive, its strength and durability set it apart.
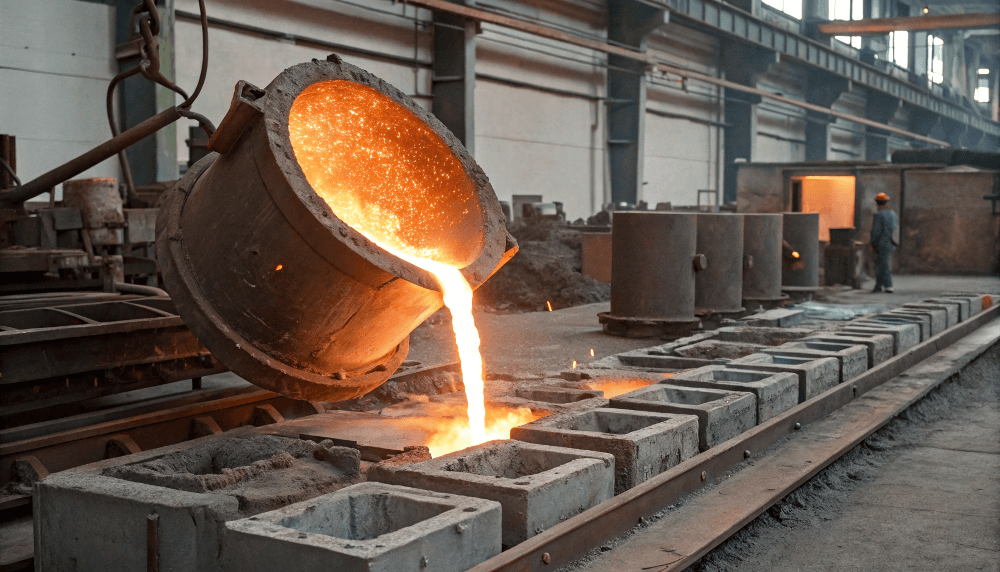
1. What is Manganese Steel Casting?
Manganese steel casting is the process of shaping molten manganese steel into specific forms for various uses. This material is known for its toughness and high wear resistance, making it perfect for heavy-duty applications in industries like mining and construction.
Manganese steel casting involves using high-manganese steel alloys, typically containing 12-14% manganese. This gives the steel its unique properties, which include exceptional impact resistance, toughness, and resistance to wear and abrasion. These properties make it the material of choice for machinery parts and tools used in environments where high stress and wear are a constant factor.
Key Characteristics of Manganese Steel
- High Manganese Content: Manganese steel typically contains 12-14% manganese, which increases toughness and durability.
- Wear Resistance: Manganese steel is well-known for its resistance to abrasion, making it ideal for high-wear environments.
- Toughness: It is highly impact-resistant, meaning it can withstand heavy shock loads without cracking or breaking.
Applications of Manganese Steel
Manganese steel casting is used in many industries, including:
- Mining: Crusher parts and liners
- Railroads: Railway track components and switches
- Heavy Equipment: Excavator buckets and digger teeth
Industry | Application | Benefits |
---|---|---|
Mining | Crusher parts and liners | Long-lasting resistance to wear, handling large quantities of material |
Railroads | Railway track components | High impact resistance under heavy traffic |
Heavy Equipment | Excavator buckets and teeth | Durability under extreme conditions, preventing frequent part replacement |
2. Why Choose Manganese Steel for Casting?
Manganese steel is chosen for its exceptional resistance to wear and tear. When looking for materials that can endure extreme environments, manganese steel casting is often the preferred option. Let’s look at some reasons why.
Manganese steel has numerous benefits over other materials. It’s particularly resistant to impact, meaning it can withstand tough working conditions without showing signs of cracking or deformation. Furthermore, it has a high tolerance for wear, making it an excellent choice for machinery and equipment that undergo heavy usage.
Benefits Over Other Materials
- Durability: Manganese steel lasts longer compared to regular carbon steel.
- Cost-Effectiveness: Due to its long lifespan, manganese steel reduces the need for frequent replacements, lowering overall costs.
- Improved Safety: Its toughness minimizes the risk of equipment failure under heavy stress, ensuring safety in high-risk operations.
Benefit | Manganese Steel | Regular Steel |
---|---|---|
Durability | High resistance to wear and impact | Can wear down quickly in high-stress environments |
Cost-Effectiveness | Long-lasting, reducing replacement needs | Requires more frequent replacement, increasing long-term costs |
Safety | Reduces risk of failure under stress | Prone to damage, increasing failure risks in tough conditions |
3. How is Manganese Steel Cast?
The process of casting manganese steel involves melting the alloy and pouring it into a mold to achieve the desired shape. This section explains how this is done and the technologies used in manganese steel casting foundries.
Manganese steel casting requires precision at every stage of the process. From melting to cooling, every step ensures that the final product has the required toughness and wear resistance. The casting process starts by heating the steel to its melting point and pouring it into molds. Once the steel solidifies, it is allowed to cool and undergoes heat treatment to further enhance its properties.
Steps in the Manganese Steel Casting Process
- Melting the Alloy: Manganese steel is melted in an electric arc furnace at temperatures over 1,500°C.
- Pouring into Molds: Once melted, the steel is poured into molds to form parts.
- Cooling and Heat Treatment: After the casting process, the steel is cooled and heat-treated to achieve optimal hardness and toughness.
Step | Description |
---|---|
Melting the Alloy | Steel is heated above 1,500°C in an electric arc furnace |
Pouring into Molds | Steel is poured into molds to take shape |
Cooling and Heat Treatment | Steel is cooled and heat-treated to enhance toughness |
4. What Are the Different Types of Manganese Steel Castings?
Manganese steel comes in various grades depending on its manganese content. High manganese steel castings are generally preferred for applications requiring maximum strength and wear resistance.
High manganese steel castings typically contain 12-14% manganese, providing the alloy with its strength and toughness. Other grades might contain slightly lower amounts of manganese, but these are suited for different industrial needs.
Types of Manganese Steel
- Hadfield Manganese Steel: The most common type, used for highly abrasive applications.
- Low Manganese Steel: Suitable for less severe conditions where high wear resistance is not required.
Type | Manganese Content | Common Applications |
---|---|---|
Hadfield Manganese | 12-14% | High-wear applications like mining equipment |
Low Manganese Steel | 6-10% | Used in less abrasive environments |
5. What Are the Common Uses of Manganese Steel Castings?
Manganese steel castings are widely used in various industries due to their toughness and wear resistance. This section explores the main applications of manganese steel and how it helps improve performance in demanding environments.
Manganese steel’s unique properties make it ideal for industries where heavy machinery and equipment are subject to constant wear and impact. In the mining industry, for example, it’s commonly used for crusher parts and liners, as well as for equipment like bucket teeth and liners. Its impact resistance and wear characteristics allow these parts to endure harsh conditions.
Key Industries and Applications
- Mining Industry: Manganese steel is used for crushers, crusher parts, and liners that handle abrasives and large materials.
- Railroad Industry: Manganese steel castings are used in railway track components, such as rail ends and switches, due to their high impact and abrasion resistance.
- Heavy Equipment: Excavators, shovels, and other heavy machinery rely on manganese steel castings for components such as bucket teeth, jaws, and pins.
- Automotive: Manganese steel is used in certain automotive components, including gears, shafts, and liners that require resistance to wear.
Industry | Application | Benefits |
---|---|---|
Mining | Crusher parts and liners | Superior impact resistance and extended wear life |
Railroad | Railway track components | Endures high-pressure contact and heavy traffic |
Heavy Equipment | Excavator buckets and teeth | Long-lasting performance under tough operating conditions |
Automotive | Gears and shafts | Durable under high-stress, high-wear applications |
6. How Does Manganese Steel Casting Improve Durability?
Manganese steel casting significantly enhances the durability of parts, making it ideal for high-stress applications. The toughness of manganese steel ensures that it can handle impacts and wear better than other materials, making it a top choice for industries requiring long-lasting solutions.
The inherent properties of manganese steel make it suitable for use in extreme conditions. Its high manganese content results in a strong material that resists cracking and breaking even under heavy shock loads. Additionally, it has an exceptional ability to resist wear, ensuring that components last longer and require fewer replacements.
Durability Features of Manganese Steel
- Impact Resistance: Manganese steel can absorb high-impact forces without cracking.
- Wear Resistance: It resists abrasion and retains its form even after prolonged exposure to harsh environments.
- Temperature Resistance: Manganese steel remains stable even in high-temperature conditions, adding to its longevity in industrial use.
Durability Feature | Manganese Steel Performance | Comparison to Other Materials |
---|---|---|
Impact Resistance | Can absorb heavy shock loads | Superior to carbon and alloy steels |
Wear Resistance | Excellent against abrasion | More resistant than stainless steel |
Temperature Resistance | Maintains strength at high temps | Less heat resistance than certain alloys |
7. What Factors Affect the Quality of Manganese Steel Castings?
The quality of manganese steel castings depends on several factors during the casting process. Understanding these factors can help optimize the production of high-quality castings that meet the required performance standards.
Several elements play a role in ensuring the durability and functionality of the castings. The quality of the raw materials, the precision in the casting process, and the heat treatment procedures all contribute to the final product’s performance. The inclusion of impurities or flaws during casting can lead to weak points in the steel, reducing its resistance to impact and wear.
Factors Influencing Quality
- Alloy Composition: The percentage of manganese and other alloying elements directly affects the strength and wear resistance.
- Casting Method: The use of high-quality molds and the proper cooling process are critical for ensuring consistent results.
- Heat Treatment: Proper heat treatment enhances the toughness and hardness of the castings, ensuring they meet the specifications.
Factor | Impact on Quality | Example Effect on Castings |
---|---|---|
Alloy Composition | Determines strength, toughness, and wear resistance | Higher manganese content improves durability |
Casting Method | Influences consistency and defect prevention | High-quality molds reduce defects like porosity |
Heat Treatment | Enhances hardness and resistance to wear | Incorrect heat treatment can lead to brittleness |
8. What Are the Advantages of Manganese Steel Casting Foundries?
Foundries that specialize in manganese steel casting offer several advantages, ensuring the production of high-quality components. These foundries utilize specialized knowledge and advanced technology to ensure the best possible outcome in casting processes.
Manganese steel casting foundries have access to cutting-edge equipment and a high level of expertise in handling complex steel alloys. This expertise allows them to produce precise, durable castings that meet the demands of industries like mining, automotive, and construction.
Key Advantages of Manganese Steel Foundries
- Expertise: Skilled technicians with in-depth knowledge of casting processes and manganese steel properties.
- Advanced Technology: Modern casting equipment ensures precision and consistency.
- Custom Solutions: Foundries offer tailored solutions based on specific customer needs.
Advantage | Description | Benefits to Customers |
---|---|---|
Expertise | Foundries employ technicians with specialized knowledge | High-quality and accurate casting products |
Advanced Technology | Use of modern casting equipment and automation | Enhanced precision, reduced errors, and consistency |
Custom Solutions | Ability to customize castings based on customer specifications | Provides tailored solutions to meet unique industrial needs |
9. How Do Manganese Steel Foundries Ensure Consistent Quality?
Consistency is key to the success of manganese steel castings, and foundries achieve this through a combination of high standards, advanced equipment, and rigorous quality control processes.
Foundries ensure the production of high-quality manganese steel castings by implementing strict quality control measures throughout the production process. From material selection to post-casting inspections, each step is carefully monitored to meet industry standards. Any deviations from the specified criteria are corrected before the product is sent out.
Quality Control Processes
- Material Inspection: Raw materials are thoroughly tested to ensure they meet specifications.
- Casting Inspection: Castings are inspected for defects such as cracks, porosity, or inclusions.
- Post-Casting Treatment: Heat treatment and finishing processes are performed to achieve optimal hardness and toughness.
Quality Control Step | Process | Benefit for Consistency |
---|---|---|
Material Inspection | Testing of raw materials before casting | Ensures alloy meets required specifications |
Casting Inspection | Inspection of castings for defects | Detects and corrects issues before finalizing |
Post-Casting Treatment | Heat treatment and finishing processes | Ensures consistent hardness and resistance |
10. What Should You Consider When Choosing a Manganese Steel Foundry?
Choosing the right manganese steel foundry is a crucial decision for ensuring the quality and durability of your castings. The foundry you select should meet certain criteria, ensuring that the production process runs smoothly and the final product meets your expectations.
When selecting a manganese steel foundry, consider their reputation, the quality of their facilities, and their ability to meet specific project requirements. Additionally, factor in the cost, lead time, and customization options they offer to determine the best fit for your needs.
Key Considerations When Choosing a Foundry
- Reputation: A foundry with a proven track record of high-quality work will provide more reliable results.
- Production Capabilities: Look for foundries that offer advanced technology and efficient production methods.
- Customization: Some foundries specialize in creating customized castings, which can be essential for unique applications.
Consideration | What to Look For | Importance |
---|---|---|
Reputation | Established track record of producing quality castings | Ensures reliable, high-quality results |
Production Capabilities | Availability of advanced technology and methods | Guarantees precision and efficient production |
Customization | Ability to create custom designs based on your needs | Provides flexibility for unique requirements |
11. How Does Manganese Steel Casting Compare to Other Casting Materials?
Manganese steel casting offers distinct advantages over other casting materials like carbon steel, stainless steel, and alloy steel. Understanding how it compares can help you make an informed decision based on your specific application needs.
Compared to other materials, manganese steel outperforms in terms of toughness and wear resistance, making it suitable for heavy-duty applications. While carbon steel is cheaper and more widely available, it lacks the impact and wear resistance that manganese steel offers. Stainless steel is more corrosion-resistant but doesn’t match the toughness of manganese steel in high-stress applications.
Manganese Steel vs Other Materials
- Carbon Steel: Manganese steel offers higher durability and resistance to wear.
- Stainless Steel: While stainless steel excels in corrosion resistance, manganese steel provides better performance under mechanical stress.
- Alloy Steel: Manganese steel provides superior impact resistance compared to alloy steel in similar applications.
Material | Strength and Toughness | Wear Resistance | Corrosion Resistance |
---|---|---|---|
Manganese Steel | Very High | Very High | Moderate |
Carbon Steel | Moderate | Low | Low |
Stainless Steel | High | Moderate | Very High |
Alloy Steel | High | Moderate | Moderate |
12. What Are the Common Challenges in Manganese Steel Casting?
Like any manufacturing process, there are challenges in producing high-quality manganese steel castings. Being aware of these challenges can help you understand the limitations and take preventive measures to improve the casting process.
Some common challenges include controlling porosity, managing shrinkage, and handling the high cooling rates required for manganese steel. These factors can lead to defects that compromise the quality of the final casting. Additionally, high-manganese alloys are prone to cracking if not handled properly during cooling.
Key Challenges in Manganese Steel Casting
- Porosity: Air pockets or holes in the casting can weaken the material.
- Shrinkage: Manganese steel shrinks as it cools, which can cause defects if not controlled properly.
- Cracking: If cooling rates are too fast or uneven, the material can crack.
Challenge | Cause | Impact |
---|---|---|
Porosity | Air trapped during pouring or cooling | Weakens the casting, leading to potential failures |
Shrinkage | Manganese steel shrinks as it cools | Causes dimensional inaccuracies in the final part |
Cracking | Rapid or uneven cooling rates | Leads to cracks, reducing the durability of the casting |
13. How Do Manganese Steel Foundries Achieve Precision in Casting?
Precision in manganese steel casting is essential for ensuring that parts meet required specifications and perform effectively. Foundries employ a combination of advanced technology, skilled labor, and stringent quality control processes to achieve this precision.
To ensure precision, foundries use computer-aided design (CAD) and computer-aided manufacturing (CAM) technologies. These tools help in designing accurate molds and casting processes. Additionally, skilled technicians monitor every step of the casting process to guarantee high-quality results.
Precision Techniques in Manganese Steel Foundries
- Computer-Aided Design (CAD): Used to create detailed and accurate models for molds.
- Computer-Aided Manufacturing (CAM): Ensures precision in the production process, minimizing errors.
- Post-Casting Finishing: Additional processes such as grinding and machining are performed to achieve precise dimensions.
Precision Technique | Description | Benefits |
---|---|---|
Computer-Aided Design (CAD) | Design of molds using advanced software | Ensures precise and accurate mold creation |
Computer-Aided Manufacturing (CAM) | Automation of the production process | Reduces errors and ensures uniformity in castings |
Post-Casting Finishing | Grinding, machining, and other finishing steps | Refines the casting and ensures accuracy in dimensions |
14. How Does the Manganese Steel Casting Process Impact Lead Time?
Lead time is an essential factor when deciding on a manganese steel casting foundry. The efficiency of the casting process and the foundry’s capacity to handle orders directly affect the time required for production and delivery.
Manganese steel casting lead times vary depending on the complexity of the parts, the foundry’s capacity, and the specific requirements of the order. While high-quality castings can take longer to produce due to the intricacies of the process, efficient foundries with modern equipment can expedite production without compromising quality.
Lead Time Factors
- Part Complexity: Complex parts require more time to design and cast.
- Foundry Capacity: The larger the foundry’s capacity, the quicker they can handle large orders.
- Customization: Custom designs often require additional time for design and production.
Lead Time Factor | Description | Impact on Lead Time |
---|---|---|
Part Complexity | More complex parts require intricate designs | Increases production time |
Foundry Capacity | Larger foundries can handle bigger orders faster | Shortens lead time for bulk orders |
Customization | Custom parts take additional time for design | May increase lead time depending on the complexity |
15. What Are the Environmental Considerations in Manganese Steel Casting?
Environmental impact is an important consideration when producing manganese steel castings. Foundries must follow certain environmental regulations to minimize their ecological footprint during the production process.
The production of manganese steel involves high energy consumption and the emission of pollutants, which is why many foundries are adopting more sustainable practices. Recycling scrap metal, reducing energy use, and implementing efficient waste management systems can help mitigate the environmental effects.
Environmental Considerations in Manganese Steel Casting
- Energy Consumption: High energy use is required for melting manganese steel.
- Pollutants and Waste: Emissions and waste products need to be managed to minimize environmental damage.
- Sustainable Practices: Recycling scrap metal and reducing emissions help foundries stay compliant with environmental regulations.
Environmental Factor | Impact | Mitigation Measures |
---|---|---|
Energy Consumption | High energy required for the casting process | Implementing energy-saving technologies |
Pollutants and Waste | Production emits pollutants and generates waste | Recycling scrap and using cleaner energy sources |
Sustainable Practices | Ensures minimal environmental damage | Investing in waste reduction and recycling programs |
Conclusion
Manganese steel casting is an essential process in the manufacturing of durable and tough components. Its remarkable properties, such as wear resistance and impact toughness, make it the go-to material for industries like mining, railways, and heavy machinery. By choosing manganese steel for your casting needs, you ensure long-lasting, high-quality components that will withstand even the harshest environments.
FAQ Section
- Q1: What is manganese steel casting?
Manganese steel casting involves using a high-manganese alloy to produce tough and durable components for industries like mining, automotive, and construction. - Q2: How does the manganese steel casting process work?
The process involves melting manganese steel alloy, pouring it into molds, and allowing it to cool and solidify. The casting then undergoes heat treatment to improve its toughness and wear resistance. - Q3: What are the benefits of using manganese steel for casting?
Manganese steel offers superior resistance to wear, high impact toughness, and long service life, making it ideal for harsh environments. - Q4: How do foundries ensure the quality of manganese steel castings?
Foundries ensure high-quality castings through strict quality control measures, including testing, inspections, and careful monitoring of the alloy composition during the casting process. - Q5: What are the common applications of manganese steel castings?
Manganese steel castings are used in mining, railroads, heavy machinery, and automotive industries, particularly for parts that need to withstand extreme stress and wear.