Sand casting aluminum is a widely used process for producing aluminum parts that are durable, reliable, and cost-effective. It’s an essential technique for manufacturing a wide range of components, from automotive parts to industrial machinery components. This article will dive into the ins and outs of sand casting aluminum, explaining its significance, how the process works, and what advantages it offers compared to other casting methods. By the end of this article, you will have a clear understanding of the process and its applications in various industries.
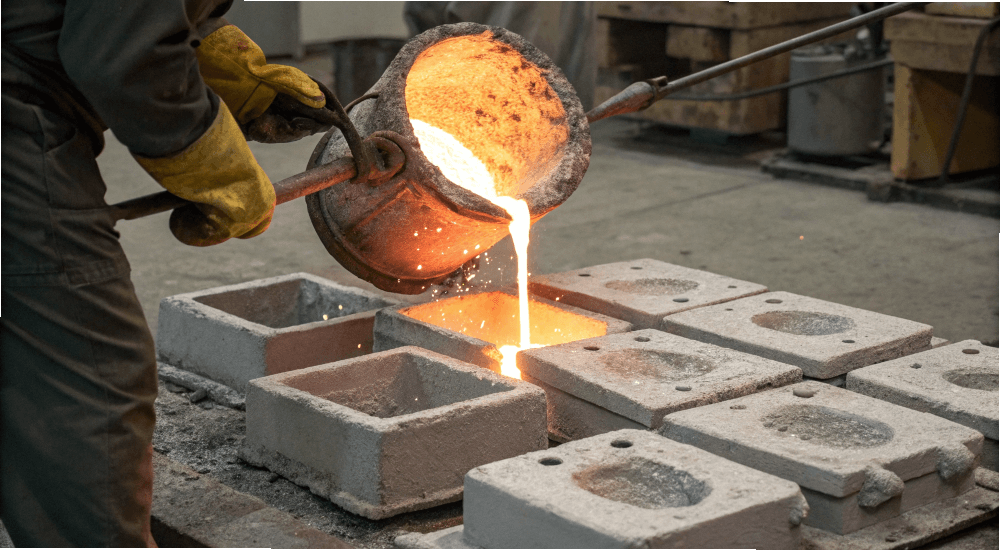
1. What is Sand Casting Aluminum?
Sand casting aluminum is a casting process where molten aluminum is poured into a mold made of sand to create solid aluminum parts. This process has been used for centuries and continues to be a preferred method for producing metal parts, especially in industries that require durable components in large quantities.
But here’s the kicker… it is one of the most versatile and cost-effective ways to produce metal parts. The simplicity of sand casting allows manufacturers to create parts of varying shapes and sizes with high precision. For those looking to produce aluminum components efficiently, this method is indispensable.
The process begins with the creation of a mold made of sand mixed with clay and water. The sand is packed tightly around a pattern of the part to be created. The pattern is then removed, leaving a cavity in the sand that forms the shape of the desired part. Molten aluminum is poured into this cavity, and once it cools and hardens, the mold is broken to reveal the final product.
What’s the real story? Sand casting offers several advantages, such as low tooling costs, the ability to create complex shapes, and flexibility with different alloys. It is especially useful when manufacturing aluminum parts in bulk.
Table 1: Overview of Sand Casting Process
Step | Description |
---|---|
Pattern Creation | A pattern is created, usually from metal or wax. |
Mold Formation | Sand is packed around the pattern to form the mold. |
Pouring Aluminum | Molten aluminum is poured into the mold cavity. |
Cooling and Solidifying | The aluminum cools and solidifies in the mold. |
Mold Removal | The sand mold is broken to reveal the casting. |
2. Why is Sand Casting Used for Aluminum?
Why choose sand casting for aluminum production? The answer lies in the unique advantages it provides over other casting methods. Sand casting aluminum is widely adopted because of its ability to handle large volumes of production, its versatility in terms of part complexity, and its suitability for large or small component sizes.
The most compelling reason for using sand casting aluminum is cost-efficiency. The materials needed to make the sand molds are relatively inexpensive, and the process itself requires minimal setup. This makes it an ideal choice for manufacturers who need to produce large batches of parts without breaking the bank.
Ready for the good part? Sand casting aluminum is also excellent for creating parts with intricate designs. Unlike other methods, such as die casting, which may struggle with highly detailed or complex shapes, sand casting allows manufacturers to create a variety of designs with fewer restrictions.
One of the key benefits is the ability to use different aluminum alloys, which enhances the casting’s properties. Depending on the alloy chosen, the aluminum can be optimized for strength, corrosion resistance, and weight. This makes sand casting a highly adaptable method for industries like automotive, aerospace, and general manufacturing.
Table 2: Key Benefits of Sand Casting Aluminum
Benefit | Description |
---|---|
Low Tooling Costs | Sand casting molds are relatively inexpensive to create. |
High Design Flexibility | Can produce parts with complex designs that other methods cannot. |
Alloy Versatility | Various aluminum alloys can be used for different properties. |
Suitable for Large Production | Ideal for producing large batches of parts efficiently. |
3. How Does Sand Casting Aluminum Work?
The process of sand casting aluminum involves several key steps that ensure the creation of precise, high-quality parts. The first step is to create a pattern of the desired component. This pattern is usually made from a material like metal or wax and is coated in sand mixed with a binder. The sand is then packed around the pattern to form a mold.
This is where it gets interesting… The mold is heated to a high temperature, and molten aluminum is poured into the cavity formed by the mold. The aluminum takes the shape of the cavity and begins to cool. Once the aluminum has solidified, the mold is broken to remove the casted part.
Key components in the sand casting process include the pattern, the sand mold, and the molten aluminum. These elements must work together to create a final product with minimal defects. Once the part has been removed from the mold, it is cleaned and finished, often requiring additional work such as machining or painting to meet the necessary specifications.
What’s the real story? The ability to cast aluminum into complex shapes and the relatively low cost of the process makes sand casting a preferred choice for many industries. It’s a reliable method that offers flexibility and high productivity, which is why it remains a key technique in metalworking.
Table 3: Sand Casting Aluminum Process Breakdown
Step | Equipment Needed | Time Required |
---|---|---|
Pattern Creation | Metal or Wax Pattern | Varies by part size |
Mold Formation | Sand, Clay, Binder | 1-2 hours depending on part complexity |
Pouring and Cooling | Ladle, Pouring Cup | 10-30 minutes depending on part size |
Solidification and Removal | Sand Molds | Several hours for cooling |
Finishing and Cleaning | Hand Tools, Machining | 1-2 hours |
4. What Materials are Used in Sand Casting Aluminum?
When it comes to sand casting aluminum, the materials used are critical in determining the strength and precision of the final product. The sand mold is typically made from a mixture of silica sand, clay, and water. This combination allows the mold to retain its shape under the intense heat of the molten aluminum while maintaining flexibility.
What’s the real story? The quality of the sand used plays a huge role in the success of the casting process. Poor-quality sand can result in defects in the final product, such as cracks or inconsistencies in the shape. To ensure optimal results, manufacturers often use high-quality, well-graded sand that is properly mixed with binders to enhance its strength.
Aluminum alloys are also a key component of sand casting. These alloys consist of aluminum combined with other metals, such as copper, silicon, and magnesium, to enhance the material’s strength, resistance to corrosion, and overall performance. The specific alloy used will depend on the application and desired properties of the finished product.
Here’s the kicker… With the right sand and aluminum alloy, manufacturers can produce parts that meet strict specifications for strength, durability, and surface finish, making sand casting a reliable method for a wide range of industries.
Table 4: Common Materials Used in Sand Casting Aluminum
Material | Purpose | Example Alloys |
---|---|---|
Silica Sand | Primary mold material | ASTM A356, A380, A319 |
Clay and Water | Binder for sand molds | N/A |
Aluminum Alloys | Casting material | 356.0, 319.0, A380 |
Additives/Binders | Enhance mold strength | Bentonite, Water Glass |
5. What Equipment is Needed for Sand Casting Aluminum?
The equipment needed for sand casting aluminum includes several key components that work together to create high-quality molds and castings. First and foremost, manufacturers need a pattern, which is a replica of the part they want to cast. Patterns are typically made from metal, wax, or a similar material that can withstand high temperatures.
What’s the real story? Molds are made from sand that’s mixed with a binder, and special equipment is used to pack the sand tightly around the pattern to form the mold cavity. Once the pattern is removed, molten aluminum is poured into the mold using a pouring cup or ladle. Cooling equipment is also necessary to ensure the aluminum solidifies in the mold.
In addition to the basic equipment, manufacturers often use advanced tools like automatic sand mixers, metal pouring systems, and shake-out machines to speed up the process and improve precision. These tools help maintain consistency in the molds and castings, which is essential for ensuring that every part meets the required specifications.
Ready for the good part? Advances in technology have made the sand casting process more efficient, allowing for faster production times and improved quality control. Automation has made it easier to produce parts with greater accuracy, reducing the chance of defects and increasing overall productivity.
Table 5: Equipment Used in Sand Casting Aluminum
Equipment | Purpose | Function |
---|---|---|
Pattern | Part replica | Used to create the mold |
Sand Molding Machine | Sand packing | Packs sand tightly around pattern |
Pouring Equipment | Molten aluminum transfer | Transfers aluminum into mold |
Shake-Out Equipment | Mold removal | Removes broken sand mold post-casting |
Cooling System | Solidification control | Regulates cooling time and temperature |
6. What are the Advantages of Sand Casting Aluminum?
The advantages of sand casting aluminum are numerous, and they make this process highly attractive to manufacturers in various industries. One of the biggest benefits is the low cost of the materials and equipment involved. Sand molds are inexpensive to create, and the overall process requires minimal setup, making it an affordable solution for large-scale production.
But here’s the kicker… Sand casting is highly versatile. It can be used to produce parts of nearly any size or complexity, making it an ideal choice for industries that require both small and large components. Whether you’re producing intricate automotive parts or large industrial machinery components, sand casting can handle the job.
The ability to use different aluminum alloys also adds to the process’s flexibility. By selecting the right alloy, manufacturers can tailor the properties of the final product, including strength, weight, and resistance to corrosion. This makes sand casting a go-to method for industries like aerospace, automotive, and energy.
What’s the real story? Sand casting aluminum offers unmatched adaptability, low tooling costs, and the ability to create complex shapes, which is why it continues to be one of the most widely used casting methods in the world.
Table 6: Key Advantages of Sand Casting Aluminum
Advantage | Description |
---|---|
Cost-Effective | Low tooling and material costs |
High Versatility | Ideal for creating a variety of part sizes and complexities |
Alloy Customization | Different aluminum alloys can be used for specific properties |
Large-Scale Production | Efficient for large production runs |
7. What are the Challenges of Sand Casting Aluminum?
While sand casting aluminum offers many advantages, it is not without its challenges. One of the primary drawbacks of this method is its limitation in terms of precision. Unlike other casting methods such as die casting, sand casting may not be able to produce parts with extremely tight tolerances, which can be problematic for industries that require high-precision components.
Ready for the good part? Surface finish issues are another common challenge. The rough texture left on the cast part after it’s removed from the sand mold may require additional machining or surface treatment to meet the required finish specifications. This can add extra time and cost to the production process.
Another issue is the possibility of defects during the casting process, such as air pockets, cracks, or incomplete filling of the mold. While these defects can often be mitigated with proper mold design and careful attention during the pouring process, they are still a risk.
What’s the real story? While sand casting aluminum has its limitations, the benefits often outweigh the drawbacks, especially for large-scale production runs or when cost efficiency is a priority.
Table 7: Common Challenges in Sand Casting Aluminum
Challenge | Impact | Mitigation Strategies |
---|---|---|
Precision Limitations | Parts may not meet tight tolerances | Use improved mold design and post-casting machining |
Surface Finish Issues | Rough surface requires extra work | Additional machining or surface treatment |
Defects (cracks, air pockets) | Can affect part integrity and strength | Careful mold preparation and pouring control |
8. How is the Quality of Sand Cast Aluminum Ensured?
Ensuring the quality of sand cast aluminum requires careful attention to detail and the use of various inspection and testing methods. One of the most important steps in ensuring quality is selecting the right materials, such as high-quality sand and aluminum alloys. These materials must be free from impurities to ensure that the final casting is strong and free from defects.
Here’s the kicker… Inspection methods like X-ray testing, ultrasonic testing, and visual inspections are commonly used to detect any internal or surface defects. These tests can identify issues like porosity, cracks, or misalignment that may not be visible to the naked eye.
Manufacturers also use quality control processes throughout the production process to ensure that the mold and casting meet the necessary specifications. This includes measuring the thickness of the mold, checking the temperature of the molten aluminum, and ensuring that the mold is properly vented.
What’s the real story? By using advanced inspection techniques and implementing stringent quality control measures, manufacturers can ensure that sand cast aluminum parts meet the highest standards of quality and reliability.
Table 8: Quality Control Techniques in Sand Casting Aluminum
Technique | Description | Purpose |
---|---|---|
X-Ray Testing | Uses radiation to inspect internal structures | Detects internal defects such as voids and cracks |
Ultrasonic Testing | Uses sound waves to examine material integrity | Identifies internal cracks and material inconsistencies |
Visual Inspection | Direct visual inspection of the casting | Identifies surface defects like cracks or misalignment |
Temperature Monitoring | Monitoring the molten aluminum’s temperature | Ensures proper pouring and solidification |
9. How Long Does Sand Casting Aluminum Take?
The time required for sand casting aluminum depends on several factors, including the size and complexity of the part being cast, the design of the mold, and the cooling time required for the aluminum. On average, the entire process—from mold creation to the removal of the final casting—can take anywhere from several hours to a few days.
What’s the real story? Sand casting aluminum is a relatively fast process compared to other casting methods, but the cooling time can significantly affect the overall production time. Large parts or those with intricate details may require longer cooling periods to ensure that the aluminum solidifies evenly and without defects.
Manufacturers often work to optimize the cooling process to reduce cycle times and improve overall efficiency. This can include using advanced cooling systems or optimizing the mold design to allow for faster heat dissipation.
Here’s the kicker… With the right equipment and careful planning, sand casting aluminum can be a highly efficient process, especially for large production runs.
Table 9: Sand Casting Aluminum Production Time
Step | Average Time | Factors Affecting Time |
---|---|---|
Pattern Creation | Several hours | Part complexity and material used |
Mold Formation | 1-2 hours | Size and shape of the part |
Pouring and Cooling | 10-30 minutes | Size of the part |
Solidification and Removal | Several hours | Cooling time required for part |
Finishing and Cleaning | 1-2 hours | Machining and surface treatments needed |
10. What are the Key Applications of Sand Cast Aluminum?
Sand cast aluminum is used in a wide range of applications, particularly in industries that require durable, high-quality components. One of the most common uses is in the automotive industry, where sand casting is used to create engine blocks, transmission housings, and other critical parts. These components must be strong and lightweight, making aluminum the ideal material for the job.
What’s the real story? The aerospace industry also uses sand casting aluminum to produce parts such as turbine blades, landing gear components, and structural parts. Aluminum’s lightweight nature and strength make it an ideal choice for these high-performance applications.
In addition to automotive and aerospace, sand cast aluminum is used in industries like energy, industrial equipment manufacturing, and even consumer goods. From pump housings to large machinery parts, sand casting is an essential method for producing aluminum components across many sectors.
Ready for the good part? Sand casting aluminum continues to be a versatile and reliable solution for creating parts that meet the rigorous demands of a wide range of industries.
Table 10: Key Applications of Sand Cast Aluminum
Industry | Application | Example Components |
---|---|---|
Automotive | Engine blocks, transmission housings | Engine blocks, cylinder heads |
Aerospace | Turbine blades, landing gear | Turbine blades, structural parts |
Energy | Pump housings, valve bodies | Industrial pump casings, valve housings |
Industrial Equipment | Machinery parts | Gears, housings, frame components |
Consumer Goods | Home appliances, electrical enclosures | Stove parts, electrical covers |
11. What is the Cost of Sand Casting Aluminum?
The cost of sand casting aluminum depends on several factors, including the complexity of the part being produced, the size of the production run, and the specific materials used. One of the biggest advantages of sand casting is its cost-efficiency, especially for large production runs or when producing relatively simple parts.
But here’s the kicker… The cost of sand casting aluminum can increase if the part requires a high level of precision, if there are issues with defects during production, or if additional machining or surface treatments are required to meet the part’s specifications.
On average, sand casting aluminum can be an affordable option for manufacturers, with lower tooling costs compared to methods like die casting. However, manufacturers must also account for the costs of labor, materials, and quality control measures.
What’s the real story? Despite some potential added costs for complex parts or additional processing, sand casting aluminum remains one of the most cost-effective methods for producing aluminum parts.
Table 11: Cost Breakdown of Sand Casting Aluminum
Factor | Estimated Cost Impact |
---|---|
Tooling and Setup Costs | Low (compared to die casting) |
Labor Costs | Moderate, dependent on part complexity |
Material Costs | Varies by aluminum alloy used |
Quality Control Costs | Moderate, but essential for high-quality production |
12. How Can Sand Cast Aluminum Be Improved?
While sand casting aluminum is already an efficient and reliable process, there are several ways to improve it. One area of improvement is in the mold design. New techniques and innovations in mold design have made it possible to reduce defects and improve the surface finish of the final product.
Here’s the kicker… Advances in sand mixing technology and automation have also led to improvements in efficiency and consistency. With better equipment and automation, manufacturers can produce higher-quality parts faster and at lower costs.
Another key area of improvement is in alloy development. New aluminum alloys with enhanced properties are constantly being developed, allowing manufacturers to create parts that are stronger, more durable, and more resistant to wear and tear.
What’s the real story? With continued advancements in technology and materials, sand casting aluminum will only continue to improve, offering even greater benefits to manufacturers and industries that rely on it.
Table 12: Innovations in Sand Casting Aluminum
Innovation | Description | Benefits |
---|---|---|
Mold Design Improvements | New techniques for mold creation | Reduced defects and improved precision |
Automation | Use of automated equipment | Increased production efficiency |
New Aluminum Alloys | Development of advanced alloys | Stronger, more durable parts |
13. How Do You Choose the Right Sand Casting Aluminum Supplier?
Choosing the right sand casting aluminum supplier is critical to ensuring the quality and consistency of the parts you receive. The first step is to evaluate the supplier’s experience and capabilities. Look for a supplier with a proven track record of producing high-quality aluminum castings and who understands your industry’s specific needs.
What’s the real story? Quality control is another key factor when choosing a supplier. Make sure the supplier has a comprehensive quality control process in place to detect and prevent defects. Ask about their testing methods, certifications, and experience with the materials and alloys you require.
It’s also important to consider lead times and delivery schedules. You want a supplier who can meet your production deadlines and deliver parts on time.
Ready for the good part? By evaluating these factors, you can select a sand casting aluminum supplier who will help you meet your production goals and ensure the highest quality standards.
Table 13: Key Considerations When Choosing a Sand Casting Aluminum Supplier
Consideration | Importance | How to Evaluate |
---|---|---|
Supplier Experience | Ensures quality and reliability | Check for industry experience and reviews |
Quality Control | Critical for defect prevention | Inquire about testing and certification processes |
Lead Times and Delivery | Ensures timely production | Ask for specific delivery schedules and past performance |
Materials and Alloys | Affects casting properties | Confirm availability of required alloys and materials |
14. What Safety Measures are Needed in Sand Casting Aluminum?
Safety is a top priority in any manufacturing process, and sand casting aluminum is no exception. Workers in sand casting facilities must follow strict safety protocols to avoid accidents and injuries. The molten aluminum used in sand casting can reach temperatures of over 1,200°F, so safety gear such as heat-resistant gloves, face shields, and protective clothing is essential.
But here’s the kicker… Proper ventilation is also important, as molten aluminum can release toxic fumes during the casting process. Workers must be protected from inhaling these fumes, which is why many sand casting facilities are equipped with ventilation systems designed to remove hazardous fumes from the air.
In addition to personal protective equipment, facilities must be equipped with fire safety equipment, such as fire extinguishers and emergency exits, in case of an accident. Training programs and safety drills should also be conducted regularly to ensure workers are prepared for emergencies.
What’s the real story? Safety measures are vital to ensuring a safe working environment and preventing accidents that could jeopardize the health of workers or damage equipment.
Table 14: Essential Safety Measures in Sand Casting Aluminum
Safety Measure | Purpose | Equipment Needed |
---|---|---|
Personal Protective Gear | Protects workers from burns | Heat-resistant gloves, face shields, clothing |
Ventilation Systems | Removes toxic fumes | Industrial ventilation units |
Fire Safety | Prevents fires and accidents | Fire extinguishers, emergency exits |
Safety Training | Prepares workers for emergencies | Regular safety drills, first aid training |
15. What Future Trends are Emerging in Sand Casting Aluminum?
The future of sand casting aluminum looks bright, with several emerging trends shaping the way this process is carried out. One trend is the increasing use of automation in sand casting facilities. By incorporating automated equipment, manufacturers can improve the speed and accuracy of the casting process, reducing labor costs and increasing overall efficiency.
What’s the real story? Sustainability is another growing trend in sand casting aluminum. As industries become more environmentally conscious, manufacturers are looking for ways to reduce waste and minimize energy consumption during the casting process. Innovations in mold materials and recycling practices are helping to make sand casting more sustainable.
Another trend is the continued development of new aluminum alloys that offer enhanced performance and durability. As technology advances, these alloys will enable manufacturers to create even stronger and more reliable parts for a wide range of applications.
Here’s the kicker… As sand casting aluminum continues to evolve, we can expect even more advancements in technology, sustainability, and efficiency, making this process an even more attractive option for manufacturers worldwide.
Table 15: Future Trends in Sand Casting Aluminum
Trend | Description | Impact on the Industry |
---|---|---|
Automation | Increased use of automated processes | Faster production, fewer errors |
Sustainability | Focus on reducing waste and energy use | Eco-friendly practices, cost savings |
New Aluminum Alloys | Development of stronger alloys | Enhanced performance and durability |
FAQ Section
Q1: What is sand casting aluminum?
Sand casting aluminum is a process where molten aluminum is poured into a sand mold to create solid aluminum parts. This method is cost-effective, versatile, and widely used in various industries.
Q2: How does sand casting aluminum work?
The sand casting process involves creating a mold from sand, pouring molten aluminum into the mold, and allowing it to cool and harden. The mold is then broken to reveal the final aluminum casting.
Q3: What are the advantages of sand casting aluminum?
Some advantages of sand casting aluminum include low tooling costs, the ability to create complex shapes, and the versatility to use different aluminum alloys for enhanced strength and durability.
Q4: How long does it take to sand cast aluminum?
The time required for sand casting aluminum depends on factors like part size and complexity. On average, the process can take anywhere from several hours to a few days.
Q5: How can sand cast aluminum be improved?
Sand cast aluminum can be improved through advancements in mold design, alloy development, and automation, which enhance efficiency, reduce defects, and improve surface finishes.