Introduction
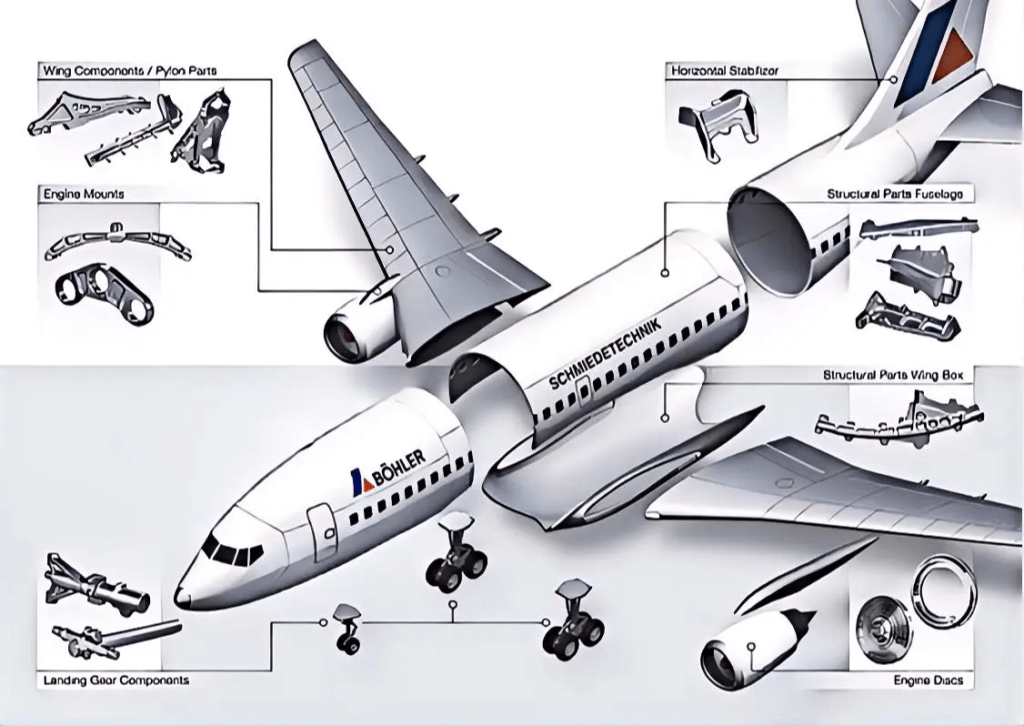
High-temperature alloys are the backbone of modern aerospace engineering, enabling innovation and safety in one of the most demanding environments imaginable. These materials are designed to endure extreme conditions, such as soaring temperatures and immense mechanical stress, without compromising performance. From jet engines to spacecraft, high-temperature alloys play a crucial role in maintaining efficiency and reliability. This article delves into the unique properties, applications, and future trends of high-temperature alloys, shedding light on why they are indispensable for the aerospace industry. Whether you are an engineer, researcher, or enthusiast, this guide will provide valuable insights.
What Are High-Temperature Alloys?
High-temperature alloys, often referred to as superalloys, are engineered materials designed to maintain superior mechanical strength and resistance to oxidation and corrosion at high temperatures. These alloys consist primarily of nickel, cobalt, or iron as their base elements, with other elements like chromium, aluminum, titanium, and molybdenum added to enhance performance. They are specifically tailored for applications where ordinary metals fail under heat and stress.
Nickel-based alloys are among the most widely used, known for their exceptional ability to resist deformation and maintain strength at temperatures exceeding 1,000°C. Cobalt-based alloys are prized for their high wear resistance, while iron-based alloys provide cost-effective solutions for less critical applications. Each type of alloy is selected based on the unique demands of the environment it will be used in, whether that’s in a turbine engine or a rocket nozzle.
The development of high-temperature alloys emerged from the need to improve the performance of engines and industrial machinery. Early advancements were driven by military aviation during World War II, where the push for faster, more reliable aircraft necessitated materials that could handle the heat of jet propulsion. Today, these alloys are integral not only to aerospace but also to power generation and automotive industries.
What sets high-temperature alloys apart from conventional materials is their microstructure. They are designed to form stable phases that resist creep, a type of deformation that occurs under prolonged exposure to heat and stress. This stability is achieved through precise control of grain size, phase composition, and alloying elements. These attributes make them essential for applications where failure is not an option.
The production of high-temperature alloys involves sophisticated processes, such as vacuum melting and powder metallurgy, to ensure purity and uniformity. These methods help eliminate impurities that could compromise the alloy’s performance. Additionally, advanced heat treatments are employed to optimize mechanical properties, such as tensile strength and fatigue resistance. Understanding the fundamental characteristics of these alloys provides a solid foundation for exploring their critical role in aerospace engineering.
Why Are High-Temperature Alloys Essential in Aerospace?
The aerospace industry operates in one of the harshest environments on Earth. Aircraft and spacecraft face extreme temperatures, high mechanical loads, and corrosive conditions that demand materials capable of enduring these challenges. High-temperature alloys meet these requirements by offering a unique combination of properties that ensure safety, performance, and reliability.
One of the most significant advantages of high-temperature alloys is their ability to withstand the extreme heat generated in jet engines. These engines operate at temperatures far beyond the melting point of conventional metals, requiring materials that can maintain strength and integrity. Turbine blades, for example, are exposed to temperatures exceeding 1,100°C while spinning at thousands of revolutions per minute. High-temperature alloys, particularly nickel-based ones, excel in this role, ensuring efficient combustion and thrust.
Another critical application is in the thermal protection systems of spacecraft. During re-entry, spacecraft experience intense aerodynamic heating, with temperatures reaching up to 1,650°C. High-temperature alloys provide the necessary thermal resistance to protect the structural integrity of the vehicle and its occupants. Materials like Inconel are often used for heat shields and other components that face direct exposure to such conditions.
Beyond temperature resistance, these alloys also offer exceptional mechanical strength and resistance to creep and fatigue. In aerospace applications, where components are subjected to repeated cycles of stress, the durability of high-temperature alloys ensures longevity and reduces the risk of catastrophic failure. This reliability is essential for both commercial aviation and space exploration, where human lives and significant investments are at stake.
The role of high-temperature alloys extends to environmental resistance. Aircraft and spacecraft operate in highly corrosive environments, from the salty, humid air encountered by commercial jets to the vacuum and radiation of space. The oxidation resistance of these alloys prevents degradation, ensuring consistent performance over time.
In addition to performance, high-temperature alloys contribute to the efficiency of aerospace systems. By enabling higher operating temperatures, they improve fuel combustion efficiency in engines, leading to reduced emissions and lower operational costs. As the industry continues to prioritize sustainability, the role of these materials in enabling greener technologies cannot be overstated.
History of High-Temperature Alloys in Aerospace
The journey of high-temperature alloys in aerospace began in the early 20th century, with advancements accelerating during World War II. The development of jet engines by pioneers like Sir Frank Whittle and Hans von Ohain highlighted the need for materials that could endure extreme heat and stress. Early engines relied on stainless steel, but as engine temperatures increased to improve performance, new materials were required.
The introduction of nickel-based alloys marked a turning point. These materials offered a significant leap in heat resistance, enabling jet engines to operate at higher temperatures and efficiencies. The 1950s saw the widespread adoption of high-temperature alloys in commercial aviation, driven by the demand for faster and more fuel-efficient aircraft.
The space race of the 1960s further pushed the boundaries of material science. Rockets and spacecraft required materials that could survive the intense heat of atmospheric re-entry and the harsh conditions of space. High-temperature alloys, such as Rene 41 and Hastelloy, played a pivotal role in missions like Apollo, where reliability was paramount.
In the decades that followed, continued innovation in material science led to the development of advanced alloys with improved properties. The advent of powder metallurgy allowed for greater control over alloy composition and microstructure, resulting in materials with enhanced strength and creep resistance. The use of computational modeling further accelerated the design of new alloys tailored for specific aerospace applications.
Today, high-temperature alloys remain at the forefront of aerospace technology. They are integral to the development of next-generation propulsion systems, such as those for hypersonic vehicles and reusable spacecraft. The history of these materials is a testament to the relentless pursuit of innovation in the face of ever-increasing challenges.
Core Properties of High-Temperature Alloys
High-temperature alloys are defined by a set of core properties that make them indispensable in aerospace applications. These include thermal stability, mechanical strength, oxidation resistance, and durability under cyclic loading. Understanding these properties helps illustrate why these materials outperform conventional metals in demanding environments.
Thermal stability is perhaps the most critical property of high-temperature alloys. At elevated temperatures, metals typically lose strength and become prone to deformation. High-temperature alloys, however, are engineered to maintain their mechanical integrity even at temperatures exceeding 1,000°C. This stability is achieved through precise alloying and heat treatment processes that optimize the microstructure.
Mechanical strength is another defining characteristic. High-temperature alloys can withstand immense loads without failure, even under extreme stress conditions. This property is particularly important in jet engines, where components like turbine blades and disks are subjected to both thermal and mechanical stresses. The use of alloying elements such as titanium and molybdenum enhances this strength, ensuring reliable performance.
Oxidation resistance is vital for applications where materials are exposed to corrosive environments, such as the high-pressure combustion chambers of engines. Elements like chromium and aluminum form protective oxide layers on the surface of the alloy, preventing further degradation. This resistance to oxidation and corrosion ensures the longevity of components, reducing maintenance costs and improving safety.
Finally, high-temperature alloys exhibit excellent fatigue and creep resistance. Fatigue resistance refers to the ability to endure repeated stress cycles without failure, while creep resistance ensures that the material does not deform over time under constant stress. These properties are crucial for components that experience long operating hours, such as turbine engines and spacecraft.
Each of these properties contributes to the overall performance of high-temperature alloys in aerospace. By combining these attributes, these materials enable engineers to design systems that are not only efficient but also safe and reliable. This comprehensive understanding of their properties underscores their indispensable role in the industry.
Key Applications in Aerospace
High-temperature alloys find their most prominent applications in aerospace due to their ability to withstand extreme conditions that no other material can endure. These alloys are pivotal in ensuring the safety, efficiency, and longevity of critical aerospace systems. From engines to spacecraft and structural components, they enable cutting-edge designs and advancements in aerospace technology.
One of the primary uses of high-temperature alloys in aerospace is in the construction of jet engines. These engines operate at incredibly high temperatures, often exceeding 1,100°C in the turbine section. Components such as turbine blades, combustion chambers, and exhaust nozzles are exposed to this extreme heat while simultaneously withstanding immense mechanical loads and rotational forces. High-temperature alloys like Inconel and Waspaloy are chosen for these components because of their unparalleled ability to maintain strength and resist creep under such conditions. The efficiency of jet engines largely depends on the materials used, as higher operating temperatures translate into improved fuel efficiency and reduced emissions.
In the realm of space exploration, high-temperature alloys are indispensable for designing thermal protection systems. During re-entry, spacecraft are subjected to intense aerodynamic heating, with temperatures reaching up to 1,650°C. Alloys like Hastelloy and Rene 41 are commonly used for heat shields and other components that experience direct thermal stress. These materials ensure the structural integrity of the spacecraft and protect its occupants or payloads during this critical phase of the mission.
High-temperature alloys are also used extensively in structural components that experience high levels of heat. For example, in modern hypersonic vehicles, the external surfaces and internal structures must withstand temperatures that result from friction with the atmosphere. These alloys not only provide the required thermal resistance but also contribute to the overall strength and lightweight nature of the structure, essential for high-speed travel.
Another significant application is in gas turbines used for power generation, which are closely related to aerospace technologies. The high-temperature alloys used in these turbines share similar performance demands, such as resistance to oxidation, corrosion, and mechanical degradation under heat. The ability to apply aerospace-grade materials to such technologies demonstrates the versatility and importance of these alloys.
In addition to their mechanical and thermal properties, high-temperature alloys contribute to the reliability and safety of aerospace systems. Their resistance to fatigue and corrosion ensures that critical components maintain their performance over long operational cycles. These qualities are particularly vital in commercial aviation, where any failure could have catastrophic consequences.
The versatility and reliability of high-temperature alloys make them an essential component in nearly every aspect of aerospace engineering. Whether in the blazing turbines of a jet engine or the scorching re-entry atmosphere of a spacecraft, these materials ensure that aerospace systems operate at their best, pushing the boundaries of what is possible in flight and exploration.
Popular High-Temperature Alloys in Aerospace
The aerospace industry relies on a specific set of high-temperature alloys known for their unique properties and proven performance in demanding conditions. Each alloy offers a distinct combination of thermal resistance, mechanical strength, and durability, tailored for particular applications. Among the most widely used are nickel-based alloys, cobalt-based alloys, and iron-based alloys.
Nickel-based alloys, such as Inconel, Hastelloy, and Waspaloy, are the most popular choice for high-temperature applications. These materials exhibit exceptional resistance to oxidation and maintain their mechanical properties at temperatures exceeding 1,000°C. For instance, Inconel 718 is commonly used in turbine blades and combustor components due to its excellent creep resistance and weldability. Hastelloy is another versatile nickel-based alloy, known for its corrosion resistance and strength, making it ideal for combustion liners and exhaust ducts.
Cobalt-based alloys, including those in the Stellite series, are valued for their wear resistance and high strength under extreme thermal conditions. These alloys are often used in engine parts subjected to heavy abrasion and stress, such as valve seats and fuel nozzles. The addition of chromium and tungsten in these alloys enhances their ability to resist deformation and corrosion.
Iron-based alloys, although less common in aerospace due to their lower temperature tolerance, provide cost-effective solutions for applications where temperatures are slightly less extreme. Alloys like A286 are frequently used in fasteners, casings, and structural supports that require good thermal stability and oxidation resistance without the high costs of nickel or cobalt alloys.
One notable innovation in this field is the development of single-crystal alloys, particularly in turbine blade manufacturing. Unlike conventional polycrystalline materials, single-crystal alloys eliminate grain boundaries, which are weak points in the material. This improvement significantly enhances the creep resistance and overall durability of the alloy, making it ideal for the most demanding aerospace applications.
The selection of a specific high-temperature alloy depends on the unique requirements of the application, such as the operating temperature, mechanical load, and exposure to corrosive environments. By carefully matching the alloy to the intended use, engineers can optimize the performance and efficiency of aerospace systems.
The continued development and refinement of high-temperature alloys ensure their relevance in advancing aerospace technology. As newer alloys are introduced and existing ones are improved, the industry will continue to benefit from these materials’ unparalleled capabilities.
The Role of Nickel-Based Alloys
Nickel-based alloys are often considered the cornerstone of high-temperature materials in aerospace engineering. Their superior thermal and mechanical properties make them indispensable for a wide range of critical applications. These alloys are used extensively in turbine engines, spacecraft, and other systems where extreme heat and stress are commonplace.
The remarkable performance of nickel-based alloys stems from their unique composition and microstructure. Nickel itself has an exceptional ability to form stable oxide layers, which protect the underlying material from oxidation and corrosion. By alloying nickel with elements such as chromium, molybdenum, and aluminum, engineers can further enhance these protective properties, ensuring durability in the harshest environments.
In jet engines, nickel-based alloys are the material of choice for turbine blades, discs, and combustors. These components must withstand temperatures approaching 1,100°C while maintaining their structural integrity under intense mechanical loads. Alloys like Inconel 625 and 718 are commonly used in these applications due to their excellent creep resistance and fatigue strength. Their ability to resist deformation over long periods ensures consistent performance and safety.
Nickel-based alloys also play a crucial role in space exploration. Components such as rocket nozzles and thermal shields are exposed to extreme temperatures and corrosive conditions during launch and re-entry. Hastelloy and Rene series alloys provide the necessary thermal resistance and mechanical strength for these critical systems. Their exceptional performance has been demonstrated in numerous space missions, underscoring their importance in achieving mission success.
Another key advantage of nickel-based alloys is their adaptability to advanced manufacturing processes. These materials are well-suited for precision casting, forging, and additive manufacturing, allowing engineers to produce complex components with high dimensional accuracy. This flexibility facilitates the design of innovative aerospace systems that push the boundaries of performance and efficiency.
As aerospace technologies evolve, the demand for high-performance materials like nickel-based alloys continues to grow. Ongoing research focuses on developing new compositions and manufacturing techniques to enhance their properties and expand their applications. The critical role of nickel-based alloys in enabling modern aerospace achievements cannot be overstated, making them a cornerstone of the industry’s success.
Manufacturing Processes for High-Temperature Alloys
The manufacturing of high-temperature alloys is an intricate process requiring precision and advanced techniques to meet aerospace standards. These methods are designed to ensure the uniformity, strength, and thermal resistance necessary for components that operate in extreme environments. Each step, from raw material preparation to the final product, is meticulously controlled.
One of the most common methods for producing high-temperature alloys is investment casting, also known as lost-wax casting. This process is particularly advantageous for creating turbine blades and other complex components. The procedure involves creating a detailed wax model of the desired part, which is then coated with a ceramic shell. Once the wax is melted away, molten alloy is poured into the cavity. After cooling, the ceramic shell is removed, leaving a precise metal component. Investment casting is valued for its ability to produce intricate shapes with minimal machining.
Forging is another widely used technique, particularly for components requiring high mechanical strength. In this process, alloy ingots are heated to a specific temperature and then shaped under high pressure. This method aligns the material’s grain structure, improving its strength and resistance to fatigue. Forged components, such as turbine disks and shafts, are critical for ensuring the reliability of aerospace systems.
Powder metallurgy is increasingly popular for high-temperature alloys due to its ability to produce materials with exceptional purity and uniformity. This method involves compressing powdered metal into a desired shape and then sintering it at high temperatures. Powder metallurgy allows for precise control over the alloy’s composition and microstructure, resulting in superior mechanical properties. It is particularly useful for manufacturing components like engine seals and thermal barriers.
Additive manufacturing (AM), or 3D printing, is a transformative approach in the aerospace industry. High-temperature alloys can be precisely deposited layer by layer to create complex geometries that were previously impossible or costly to achieve. This method is ideal for producing lightweight yet strong components, making it a game-changer for the industry. For instance, 3D-printed turbine blades can incorporate intricate cooling channels to improve efficiency.
To enhance the properties of high-temperature alloys, heat treatment processes are employed. Techniques such as solution annealing, precipitation hardening, and quenching optimize the material’s microstructure for specific performance characteristics. These treatments increase strength, toughness, and resistance to creep, ensuring the alloys perform reliably under aerospace conditions.
Each manufacturing process has its advantages and is selected based on the application requirements. As aerospace systems become more advanced, the precision and capabilities of these processes are continuously improved, ensuring high-temperature alloys remain at the forefront of material science.
Challenges in Using High-Temperature Alloys
While high-temperature alloys are indispensable in aerospace, their use comes with challenges that demand innovative solutions. These issues stem from the materials’ inherent properties, manufacturing complexity, and costs.
One of the primary challenges is high production costs. High-temperature alloys often contain expensive elements like nickel, cobalt, and titanium. The extraction and refinement of these materials require significant energy and resources, driving up costs. Furthermore, the advanced manufacturing techniques needed to shape and process these alloys add to the overall expense. For instance, the precision required in investment casting or powder metallurgy makes these methods labor-intensive and costly.
Another significant challenge is the difficulty in machining and fabrication. High-temperature alloys are incredibly tough, which makes them resistant to conventional machining methods. Tools wear out quickly when cutting these materials, leading to increased downtime and higher production costs. Specialized equipment and processes, such as electrical discharge machining (EDM), are often required, which adds complexity to the manufacturing workflow.
Material performance limitations also pose challenges. Although high-temperature alloys exhibit exceptional properties, they are not immune to degradation. Under prolonged exposure to extreme heat and stress, these materials can experience creep, oxidation, and thermal fatigue. While these effects are minimized through careful alloy design and heat treatments, they remain a concern for long-duration aerospace missions.
The environmental impact of high-temperature alloy production is another critical issue. Mining and refining the raw materials contribute to greenhouse gas emissions and resource depletion. Additionally, recycling high-temperature alloys can be challenging due to their complex compositions. Addressing these environmental concerns requires the development of more sustainable production and recycling methods.
Supply chain vulnerabilities further complicate the use of high-temperature alloys. The reliance on rare and strategically important elements, such as cobalt, makes the supply chain susceptible to geopolitical tensions and market fluctuations. This unpredictability can affect the availability and pricing of these materials, posing risks to aerospace manufacturers.
Despite these challenges, the aerospace industry continues to innovate. Research into alternative materials, such as ceramic-matrix composites, aims to complement or replace traditional high-temperature alloys in certain applications. Advances in additive manufacturing and material science also promise to reduce costs and overcome fabrication difficulties, ensuring these critical materials remain viable for future aerospace technologies.
How Do High-Temperature Alloys Improve Safety?
Safety is paramount in aerospace, and high-temperature alloys play a critical role in ensuring it. These materials are engineered to withstand extreme conditions, preventing catastrophic failures that could endanger lives and investments.
One of the primary ways high-temperature alloys improve safety is by resisting thermal degradation. In jet engines, components like turbine blades are exposed to intense heat and mechanical stress. High-temperature alloys retain their strength and stability under these conditions, reducing the risk of failure. For example, the creep resistance of these alloys ensures that critical parts maintain their shape and function over extended periods, even at elevated temperatures.
Oxidation and corrosion resistance are equally important for safety. In aerospace environments, materials are exposed to harsh conditions, including corrosive gases, salt, and moisture. The protective oxide layers formed by high-temperature alloys prevent degradation, ensuring components remain intact and functional. This property is especially critical for engines and exhaust systems, where failure could have catastrophic consequences.
High-temperature alloys also enhance safety by providing excellent fatigue resistance. Components in aerospace systems are subjected to repetitive stress cycles, such as the constant loading and unloading experienced during flight. Materials with poor fatigue resistance can develop cracks and eventually fail. High-temperature alloys are designed to resist such fatigue, ensuring the longevity and reliability of critical systems.
The use of high-temperature alloys extends to spacecraft, where safety is even more critical. During re-entry, spacecraft experience extreme thermal and mechanical stresses. High-temperature alloys protect the structural integrity of the vehicle, shielding it from aerodynamic heating and ensuring the safety of the crew or payload.
Another safety benefit comes from the predictable performance of high-temperature alloys. Their properties are well-documented and consistent, allowing engineers to design systems with confidence. This predictability reduces the likelihood of unexpected failures, which is crucial in aerospace applications where redundancy and reliability are essential.
In summary, high-temperature alloys are not just materials of choice for their performance; they are fundamental to the safety protocols of aerospace engineering. By enabling systems to operate reliably under the harshest conditions, these materials ensure that every flight, whether in the atmosphere or space, meets the highest safety standards.
Environmental Considerations
The aerospace industry increasingly focuses on sustainability, and high-temperature alloys play a role in reducing the environmental impact of aviation and space exploration. While these materials are essential for improving efficiency and performance, their production and use present environmental challenges that require thoughtful solutions.
One of the primary environmental concerns is the resource-intensive production process. High-temperature alloys rely on elements such as nickel, cobalt, and titanium, which require significant energy to mine, refine, and process. These steps contribute to greenhouse gas emissions, resource depletion, and habitat disruption. For example, the mining of cobalt has raised concerns about environmental degradation and ethical sourcing, as the extraction process often affects local ecosystems and communities.
Recycling high-temperature alloys is another critical challenge. While these materials are technically recyclable, their complex compositions make the process costly and energy-intensive. Separating valuable alloying elements, such as molybdenum and chromium, from other components requires advanced techniques. Developing efficient recycling methods is essential to reduce waste and ensure a sustainable supply of these critical materials.
Despite these challenges, high-temperature alloys contribute to environmental benefits during operation, particularly in aviation. By enabling engines to operate at higher temperatures, these alloys improve fuel efficiency, reducing carbon dioxide emissions. Advanced turbine designs that incorporate high-temperature alloys can achieve significant reductions in fuel burn, which directly translates to lower emissions per flight. As the industry aims to meet stringent environmental standards, such as the International Civil Aviation Organization’s (ICAO) Carbon Offsetting and Reduction Scheme for International Aviation (CORSIA), high-temperature alloys will remain a key enabler.
Another aspect of sustainability is the long lifespan of components made from high-temperature alloys. Their resistance to wear, corrosion, and fatigue means that parts require less frequent replacement, reducing the demand for raw materials and the environmental footprint associated with manufacturing new components. This durability aligns with the principles of a circular economy, where the focus is on maximizing the value of materials over their lifecycle.
Research into alternative materials and greener production methods is ongoing. Innovations such as additive manufacturing can reduce waste by producing components with minimal material loss. Additionally, exploring alternative alloying elements that are more abundant and environmentally friendly may help alleviate supply chain pressures.
In summary, while high-temperature alloys have an environmental impact during production, their contributions to efficiency, longevity, and emissions reduction make them an integral part of a sustainable aerospace industry. Balancing these benefits with continued innovation in recycling and greener manufacturing practices is critical to minimizing their ecological footprint.
Innovations in High-Temperature Alloys
Innovation in high-temperature alloys is vital for meeting the evolving demands of the aerospace industry. These materials must continuously improve to enable more efficient engines, withstand harsher conditions, and support the development of advanced technologies like hypersonic vehicles and reusable spacecraft.
One area of significant innovation is the development of new alloy compositions. Researchers are exploring materials that incorporate rare earth elements or nano-scale reinforcements to enhance thermal and mechanical properties. For example, alloys with higher levels of rhenium have shown exceptional creep resistance, making them ideal for high-stress applications like turbine blades. However, the scarcity and cost of such elements drive the need for alternative solutions, such as alloys designed to achieve similar performance with more abundant materials.
Coating technologies are another critical area of advancement. Thermal barrier coatings (TBCs) are applied to high-temperature alloys to improve their resistance to extreme heat. These coatings can extend the operating temperature range of components by hundreds of degrees, enabling more efficient engine designs. Innovations in TBCs include the use of nanostructured materials and advanced deposition techniques that improve adhesion and durability.
The advent of additive manufacturing (AM) has revolutionized how high-temperature alloys are utilized in aerospace. AM allows engineers to create complex geometries that were previously impossible or prohibitively expensive to produce using traditional methods. For example, 3D-printed turbine blades can incorporate intricate cooling channels that enhance thermal performance. Researchers are also developing AM-specific alloy formulations to optimize the properties of components produced through this method.
Another promising innovation is the use of computational modeling and artificial intelligence (AI) in alloy development. These tools enable scientists to simulate the behavior of new alloys under various conditions, accelerating the design process and reducing the need for costly experimentation. AI-driven optimization can identify the ideal combination of elements to achieve desired properties, paving the way for materials tailored to specific aerospace applications.
The focus on sustainability has also driven innovation. Efforts to develop alloys that require less energy-intensive production processes or incorporate recycled materials are gaining traction. Additionally, advancements in powder metallurgy and vacuum arc remelting have improved the efficiency and environmental impact of alloy manufacturing.
These innovations demonstrate the dynamic nature of high-temperature alloy development. By pushing the boundaries of material science, these advancements ensure that aerospace systems can meet the challenges of tomorrow while improving performance, safety, and sustainability.
Future Trends in Aerospace Materials
The future of aerospace materials is defined by the need for greater efficiency, sustainability, and resilience in the face of ever-increasing demands. High-temperature alloys, while continuing to play a central role, will evolve alongside complementary materials and cutting-edge technologies.
One of the most exciting trends is the development of materials for hypersonic vehicles. Hypersonic flight, which involves speeds exceeding Mach 5, generates extreme aerodynamic heating. High-temperature alloys will need to be paired with advanced ceramics and composite materials to handle these conditions. Researchers are exploring hybrid solutions that combine the thermal resistance of ceramics with the mechanical strength of superalloys.
Reusable spacecraft represent another area of growth. As the commercial space industry expands, the demand for cost-effective and durable materials increases. High-temperature alloys are critical for components like rocket engines and thermal shields, where reliability and reusability are paramount. Advances in alloy formulations and manufacturing techniques will be essential to support this emerging market.
Sustainability will remain a driving force in material development. The aerospace industry is investing in lightweight alloys and composites to reduce fuel consumption and emissions. High-temperature alloys that offer superior performance at lower weights will become increasingly valuable. Innovations in recycling and circular economy practices will also shape the future of these materials, ensuring a more sustainable supply chain.
The integration of smart materials and sensors into aerospace systems is another trend on the horizon. These materials can monitor their own performance, detecting signs of fatigue or damage in real time. High-temperature alloys with embedded sensors could enhance safety and maintenance efficiency, providing critical data on the condition of key components.
Lastly, the role of automation and AI in material science will continue to expand. Machine learning algorithms can analyze vast datasets to identify trends and optimize alloy compositions for specific applications. This technology will accelerate the development of next-generation materials, ensuring they meet the unique requirements of future aerospace systems.
The future of aerospace materials is a blend of tradition and innovation. High-temperature alloys will remain indispensable, but their evolution will be shaped by emerging technologies and changing industry priorities. By embracing these trends, the aerospace industry can achieve new levels of performance, sustainability, and capability.
Key Metrics for Evaluating High-Temperature Alloys
Evaluating high-temperature alloys for aerospace applications involves a thorough analysis of several key metrics that determine their suitability for specific tasks. These metrics include thermal stability, mechanical strength, oxidation resistance, and fatigue life, among others.
Thermal stability is one of the most critical metrics. Aerospace components often operate at temperatures that push materials to their limits. The ability of an alloy to maintain its properties, such as strength and hardness, at high temperatures is essential for ensuring reliable performance. This property is often measured through tests like stress-rupture and creep resistance evaluations.
Mechanical strength encompasses several aspects, including tensile strength, yield strength, and compressive strength. These metrics determine how much load a material can withstand before deforming or failing. High-temperature alloys are designed to excel in these areas, particularly under the combined stresses of heat and mechanical load experienced in aerospace systems.
Oxidation and corrosion resistance are also vital. Materials exposed to high temperatures in the presence of oxygen or corrosive substances can degrade rapidly. Alloys with elements like chromium and aluminum form protective oxide layers that prevent further oxidation, ensuring long-term durability. Testing these properties under simulated operating conditions helps predict real-world performance.
Fatigue resistance measures an alloy’s ability to withstand repeated stress cycles without developing cracks or failing. This property is particularly important for components like turbine blades, which experience continuous stress during operation. Fatigue testing involves subjecting materials to cyclic loading to assess their lifespan under realistic conditions.
Density and weight are additional considerations, especially for aerospace applications where every gram matters. High-temperature alloys must balance strength and performance with minimal weight to improve fuel efficiency and reduce overall system mass.
By thoroughly evaluating these metrics, engineers can select the best high-temperature alloy for each aerospace application, ensuring optimal performance, safety, and reliability.
Conclusion: Why High-Temperature Alloys Are Non-Negotiable in Aerospace
High-temperature alloys are the cornerstone of modern aerospace engineering, enabling systems to perform reliably in some of the most extreme environments. Their unique properties, including thermal stability, mechanical strength, and oxidation resistance, make them indispensable for applications ranging from jet engines to spacecraft. As the aerospace industry evolves, these materials will continue to drive innovation, ensuring efficiency, safety, and sustainability in flight and exploration. To stay at the forefront of aerospace advancements, investing in the development and application of high-temperature alloys remains essential.
FAQ
1. What temperatures can high-temperature alloys withstand?
They can endure temperatures exceeding 1,000°C, with some specialized alloys capable of handling up to 1,200°C or more.
2. Why are nickel-based alloys widely used in aerospace?
Nickel-based alloys offer exceptional thermal resistance, mechanical strength, and resistance to oxidation, making them ideal for high-stress and high-heat environments.
3. Are high-temperature alloys recyclable?
Yes, but recycling them is challenging due to their complex compositions. Advanced techniques are required to extract and reuse valuable elements.
4. How do high-temperature alloys contribute to sustainability?
They improve fuel efficiency, reduce emissions, and extend component lifespans, aligning with the industry’s push for greener technologies.
5. What industries beyond aerospace use high-temperature alloys?
They are also used in power generation, automotive industries, and industrial machinery where extreme heat and stress are present.