Introduction
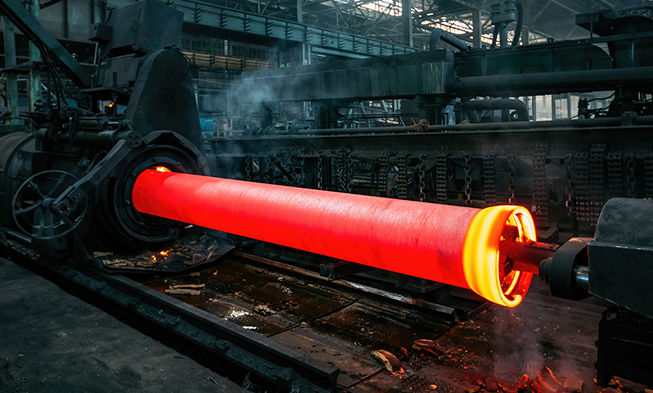
High-temperature casting plays an indispensable role in modern manufacturing, providing the framework for products that withstand extreme thermal environments. From aerospace turbines to industrial machinery, selecting the right materials ensures durability and performance under stress. However, identifying materials that endure intense heat, mechanical load, and chemical exposure remains a challenge. This article explores the properties, classifications, and applications of materials commonly used in high-temperature casting, offering detailed insights to help manufacturers make informed decisions. By understanding these materials and their characteristics, industries can optimize performance, reduce costs, and innovate responsibly in heat-intensive processes.
What Is High-Temperature Casting?
High-temperature casting is a manufacturing process where materials are melted and poured into molds to create complex parts capable of withstanding extreme temperatures. The process is vital in sectors like aerospace, automotive, and energy, where heat resistance and durability are paramount. But what sets it apart? The defining feature lies in its ability to produce components that perform under temperatures exceeding 1,000°C, a necessity in applications such as jet engines, industrial furnaces, and heat exchangers.
The procedure begins by selecting appropriate casting materials. These materials must possess specific properties, such as high melting points, thermal stability, and resistance to thermal shock. Metals and alloys like superalloys, ceramics, and refractory materials are frequent choices. The molten material is poured into a pre-formed mold that captures the intricate details required for high-performance applications. Once cooled and solidified, the cast component undergoes finishing processes like machining and surface treatments to meet precise specifications.
Industries favor high-temperature casting for its versatility and ability to create complex geometries that would be challenging or impossible with other methods. Turbine blades, for example, require tight tolerances and unique aerodynamic shapes that only advanced casting techniques can achieve. Moreover, the process accommodates various materials, each tailored to specific performance demands. For instance, the aerospace industry often employs superalloys due to their exceptional thermal and mechanical properties, while refractory materials are essential for components exposed to prolonged heat in industrial furnaces.
Despite its advantages, high-temperature casting comes with challenges. Materials must be carefully selected to avoid defects like cracking or warping during cooling. Advanced technologies like vacuum casting and computer-aided design now help mitigate these risks, ensuring consistent quality. High-temperature casting remains an essential tool for manufacturing, enabling innovations in fields requiring high-performance materials.
Key Properties of Materials Used in High-Temperature Casting
Choosing the right material for high-temperature casting depends heavily on understanding key properties that ensure reliability under extreme conditions. Heat resistance, mechanical strength, thermal expansion, and corrosion resistance are among the most critical factors.
Heat resistance defines a material’s ability to maintain structural integrity at elevated temperatures. In casting, materials like superalloys and ceramics are selected for their high melting points and thermal stability. These materials prevent deformation, ensuring that components perform as intended in applications such as gas turbines or exhaust manifolds.
Mechanical strength refers to a material’s capacity to withstand forces like tension, compression, and shear without failure. High-temperature applications often impose additional stress due to thermal expansion, requiring materials that remain robust under combined loads. Superalloys, with their enhanced mechanical properties, excel in such scenarios.
Thermal expansion measures the rate at which a material expands when heated. Inconsistent expansion can lead to warping or cracking, especially in components with tight tolerances. Engineers often analyze the coefficient of thermal expansion (CTE) to select materials compatible with specific applications. For instance, ceramics typically exhibit low CTE values, making them ideal for high-precision molds.
Corrosion resistance becomes crucial in environments involving heat and reactive elements like oxygen or sulfur. Oxidation can weaken materials, reducing their lifespan. Materials like nickel-based alloys include elements like chromium and aluminum, forming protective oxide layers to combat degradation.
Together, these properties define the suitability of materials for high-temperature casting. By understanding the interplay between these characteristics, manufacturers can optimize designs to ensure durability and performance in demanding applications.
Classification of Casting Materials
Materials used in high-temperature casting can be broadly classified into metals and alloys, ceramics, composites, and refractory materials. Each category offers unique advantages tailored to specific needs.
Metals and alloys dominate casting due to their excellent mechanical properties and versatility. Superalloys, including nickel and cobalt-based variants, stand out for their ability to perform in extreme environments. Aluminum alloys, while not as heat-resistant, are lightweight and valuable in automotive and aerospace applications.
Ceramics are often used for molds and components requiring exceptional heat resistance. Silica, alumina, and zirconia are common ceramic materials. Their low thermal conductivity and high melting points make them indispensable in industries like foundry and electronics.
Composites combine materials to achieve desired properties. Carbon-fiber composites and ceramic-matrix composites are prominent examples. These materials are lightweight, strong, and heat-resistant, making them ideal for advanced aerospace and defense applications.
Refractory materials, including fireclay and silica, are essential for lining furnaces and kilns. They withstand prolonged exposure to extreme heat, ensuring the structural integrity of industrial equipment. Understanding these classifications helps manufacturers select the right material for their unique requirements.
Metals and Alloys in High-Temperature Casting
Metals and alloys are the backbone of high-temperature casting due to their combination of mechanical strength and thermal performance. Aluminum, steel, superalloys, and titanium stand out as primary choices.
Aluminum alloys are prized for their lightweight nature and corrosion resistance. While their melting point is lower than superalloys, advancements in high-temperature aluminum alloys have expanded their applications in automotive and aerospace sectors.
Steel, particularly heat-resistant grades like stainless steel, is a staple in industrial casting. It offers strength and versatility, making it ideal for a range of components, from structural parts to machinery.
Superalloys, such as nickel and cobalt-based variants, excel in applications requiring extreme heat and stress resistance. These alloys are engineered to withstand oxidation and maintain their strength at elevated temperatures. They are widely used in jet engines, power plants, and chemical processing.
Titanium alloys, though expensive, combine high strength-to-weight ratios with excellent heat resistance. Aerospace industries rely on titanium for critical components like engine parts and airframes. By leveraging these materials, manufacturers achieve superior performance in demanding environments.
Ceramics as a Casting Material
Ceramics play a pivotal role in high-temperature casting, particularly in mold production and components requiring exceptional thermal stability. These materials, including silica, alumina, and zirconia, are known for their high melting points and resistance to thermal shock.
Silica is a common ceramic material due to its affordability and effectiveness in high-temperature molds. Alumina, with its higher thermal stability, is preferred for applications requiring greater durability. Zirconia, although more expensive, offers unparalleled resistance to thermal shock, making it ideal for extreme environments.
Ceramics are also employed in core production for precision casting, such as turbine blades. Their ability to maintain dimensional stability under heat makes them indispensable in creating intricate geometries.
Despite their advantages, ceramics are brittle and require careful handling. Advances in ceramic composites are addressing these limitations, expanding their use in high-temperature casting applications.
Refractory Materials: The Backbone of Heat Resistance
Refractory materials are critical to high-temperature casting, offering unparalleled heat resistance and durability in extreme environments. These materials are specifically designed to withstand prolonged exposure to temperatures exceeding 1,500°C without compromising structural integrity. Common refractory materials include fireclay, silica, alumina, and magnesium oxide, each serving unique roles in industrial applications.
Fireclay refractories, composed of hydrated aluminum silicates, are widely used due to their cost-effectiveness and versatility. They are commonly employed in furnace linings, kilns, and incinerators, where moderate thermal loads and chemical stability are essential. Silica-based refractories, with their high melting points and resistance to acidic slags, are ideal for glass manufacturing and coke ovens.
Alumina refractories, containing high levels of aluminum oxide, provide superior thermal and mechanical stability. These materials are suitable for demanding applications such as steel production, where resistance to wear and thermal shock is vital. Magnesium oxide, or magnesia, is another prominent refractory material, valued for its excellent resistance to basic slags and high thermal conductivity. It is commonly used in cement kilns and metallurgical processes.
Refractory materials also play a pivotal role in the casting molds themselves. In processes like investment casting, refractory coatings ensure smooth surface finishes and dimensional accuracy. The integration of advanced refractories into casting systems has significantly enhanced performance, extending the lifespan of industrial equipment and reducing maintenance costs.
Advances in refractory technology are pushing the boundaries of what these materials can achieve. Innovations such as nano-refractories and carbon-based composites are improving thermal resistance and reducing brittleness. By leveraging these developments, industries can optimize efficiency and ensure reliability in high-temperature casting operations.
Composites in High-Temperature Casting
Composites are revolutionizing high-temperature casting by combining the strengths of multiple materials to achieve superior performance. These materials blend fibers, matrices, and fillers to create components that are lightweight, strong, and capable of withstanding extreme heat.
Carbon-fiber composites are a prime example, offering exceptional strength-to-weight ratios and thermal stability. Used in aerospace and automotive industries, these materials enable the production of components like turbine blades and heat shields. Ceramic-matrix composites (CMCs), which combine ceramic fibers with ceramic matrices, take this performance a step further by providing resistance to oxidation and thermal shock.
A major advantage of composites is their design flexibility. Engineers can tailor composite structures to meet specific performance requirements, such as optimizing heat resistance or minimizing thermal expansion. For instance, hybrid composites that combine metal and ceramic properties are emerging as game-changers in high-temperature applications.
Despite their advantages, composites have challenges, including higher costs and complex manufacturing processes. However, advancements in 3D printing and automated manufacturing are making composites more accessible. By integrating composites into high-temperature casting, industries are achieving breakthroughs in performance, durability, and efficiency.
Innovative Materials in Modern Casting
The pursuit of better performance has led to the development of innovative materials that redefine high-temperature casting. Tungsten carbide and silicon carbide are two standout examples, known for their remarkable heat resistance and mechanical strength.
Tungsten carbide, a composite of tungsten and carbon, is renowned for its hardness and thermal conductivity. It is widely used in molds and cutting tools, where extreme durability and heat resistance are crucial. Silicon carbide, on the other hand, offers excellent thermal conductivity and oxidation resistance, making it ideal for components like furnace linings and heat exchangers.
Other innovations include high-entropy alloys (HEAs), which combine multiple principal elements to create materials with exceptional properties. HEAs are gaining traction in applications like jet engines and gas turbines, where traditional materials fall short.
The incorporation of nanotechnology is also transforming material performance. Nano-coatings and nano-composites are enhancing heat resistance, reducing weight, and improving wear resistance. These advancements are expanding the possibilities for high-temperature casting, enabling industries to push the limits of performance and efficiency.
Environmental and Economic Considerations
Sustainability is becoming a cornerstone in material selection for high-temperature casting. As industries strive to reduce their environmental footprint, the use of recyclable and eco-friendly materials is gaining momentum. Metals like aluminum and steel are highly recyclable, making them popular choices for sustainable manufacturing.
However, balancing cost and performance remains a challenge. Advanced materials like superalloys and composites often come with higher price tags, which can strain budgets. Manufacturers must evaluate the long-term benefits of these materials, such as reduced maintenance and improved durability, to justify the investment.
Energy efficiency is another critical factor. The production and processing of high-temperature materials often require significant energy inputs, contributing to carbon emissions. Innovations in manufacturing processes, such as low-energy sintering and additive manufacturing, are addressing these concerns by reducing energy consumption.
By prioritizing environmental and economic considerations, industries can make informed decisions that align with both performance goals and sustainability objectives.
Challenges in Using High-Temperature Materials
While high-temperature materials offer remarkable capabilities, their use presents several challenges. Material availability and sourcing are significant hurdles, as some advanced materials, like rare earth metals, are subject to geopolitical constraints and supply chain disruptions.
Compatibility with specific casting processes is another concern. Not all materials are suitable for every method, and choosing the wrong material can lead to defects like cracking or porosity. Advanced simulation software is now helping engineers predict material behavior and optimize process parameters.
Cost is a persistent challenge, particularly for industries operating on tight margins. While high-performance materials often deliver superior results, their initial costs can be prohibitive. Manufacturers must carefully weigh these costs against potential savings in maintenance and performance.
Despite these challenges, ongoing research and development are providing solutions. By addressing these issues, industries can unlock the full potential of high-temperature materials in casting applications.
Material Testing and Standards
Ensuring the reliability of high-temperature materials requires rigorous testing and adherence to industry standards. Tests for thermal and mechanical properties, such as tensile strength, thermal conductivity, and oxidation resistance, are essential for validating material performance.
Standards set by organizations like ASTM and ISO provide guidelines for material selection and testing. These standards ensure consistency and quality across industries, facilitating global collaboration and innovation.
By adhering to these standards, manufacturers can build trust with clients and ensure the success of high-temperature casting projects.
Conclusion
High-temperature casting relies on materials that combine heat resistance, mechanical strength, and environmental adaptability. From metals and ceramics to composites and innovative alloys, each material offers unique advantages for specific applications. As industries evolve, the integration of advanced materials and sustainable practices is paving the way for a future of efficiency, performance, and environmental responsibility. For manufacturers seeking to optimize their processes, understanding and leveraging these materials is the key to success. Explore new materials, consult experts, and lead the way in high-temperature casting innovation.
FAQ Section
1. What is the primary challenge in high-temperature casting?
Maintaining material integrity under extreme heat and stress.
2. Why are superalloys popular in high-temperature applications?
They offer excellent thermal stability, corrosion resistance, and mechanical strength.
3. How are ceramics used in casting?
Ceramics often serve as molds or liners due to their high melting points and resistance to thermal shock.
4. Are high-temperature materials environmentally friendly?
Many metals and ceramics can be recycled, but advanced materials like composites may have limitations.
5. What industries benefit the most from these materials?
Aerospace, automotive, industrial machinery, and energy sectors are the primary beneficiaries.