Investment casting is a key process in many industries, and aluminum plays a critical role in this field. When it comes to producing high-quality aluminum parts through investment casting, the selection of the right aluminum alloy is crucial. This article explores the different types of aluminum used in investment casting, why aluminum is favored for such purposes, and how these alloys are chosen and prepared to deliver optimal results. Whether you’re in aerospace, automotive, or consumer goods manufacturing, understanding the types of aluminum and their specific benefits can significantly enhance your casting process.
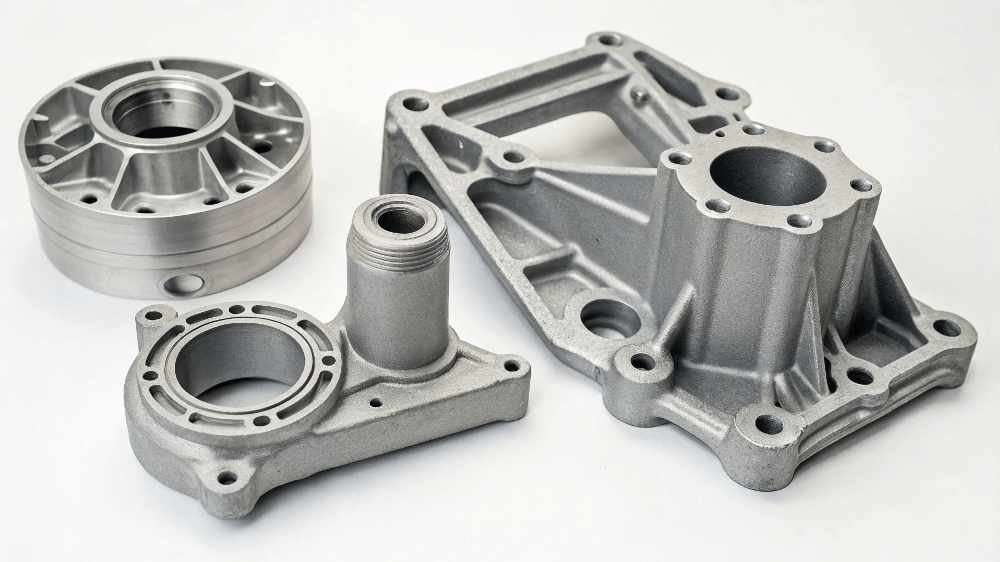
1. What is Investment Casting?
Investment casting is often called the “lost wax” process, and it’s one of the oldest methods of metal casting. The process involves creating a mold from a wax model of the part, coating it with a ceramic shell, and then melting the wax away. What’s the real story? The result is a hollow mold that can be filled with molten metal, typically aluminum for precision casting.
Investment casting offers numerous advantages over other casting techniques. It allows for the creation of highly intricate, detailed shapes that would be difficult or impossible to achieve with other methods like sand casting or die casting. The high precision and smooth surface finish make it ideal for industries that require complex parts. What sets aluminum apart is its favorable properties, making it one of the most common materials used in investment casting.
In investment casting, the choice of aluminum alloys is vital. Aluminum is light, strong, and highly corrosion-resistant, making it perfect for industries that need high-performance materials. Aluminum also possesses a relatively low melting point compared to other metals, making it easier to cast.
Investment Casting Process Step | Description |
---|---|
Wax Pattern Creation | A pattern is created from wax and shaped according to the part’s design. |
Ceramic Shell Formation | The wax pattern is coated with layers of ceramic material to form a mold. |
Wax Removal | The mold is heated, and the wax is melted and drained away. |
Metal Pouring | Molten aluminum is poured into the mold to create the casting. |
Cooling and Finishing | The mold is cooled, and the casting is cleaned and finished. |
2. Why is Aluminum Popular for Investment Casting?
Ready for the good part? The reason aluminum is a go-to material for investment casting lies in its remarkable properties. Aluminum alloys, compared to other metals like steel or iron, are lighter, which reduces overall part weight and increases efficiency. The reduced weight of aluminum parts is a crucial factor in industries like aerospace, where lighter components contribute directly to fuel efficiency and performance.
Aluminum also boasts excellent corrosion resistance, meaning it performs well in harsh environmental conditions, including marine and automotive applications. It’s also known for its high strength-to-weight ratio, which makes it strong enough to endure heavy loads while keeping weight down. What makes aluminum even more attractive is its exceptional castability, meaning it flows well into molds and creates highly detailed parts without the common casting defects.
But here’s the kicker—aluminum also has good thermal and electrical conductivity, making it suitable for applications that involve heat exchange or require components to conduct electricity. It’s not just about strength; it’s about versatility in how aluminum can be used across a variety of industries.
Property | Description | Benefit to Investment Casting |
---|---|---|
Strength-to-Weight Ratio | High strength combined with low weight. | Ideal for lightweight yet strong parts in aerospace and automotive. |
Corrosion Resistance | Naturally forms a protective oxide layer. | Suitable for harsh environments and marine applications. |
Castability | Excellent fluidity and easy flow into molds. | Allows for intricate details and precision casting. |
Thermal Conductivity | Good ability to transfer heat. | Perfect for heat exchangers and cooling systems. |
3. What Are the Common Types of Aluminum Used in Investment Casting?
So, which aluminum alloys are commonly used in investment casting? Let’s break down some of the most popular choices.
● 380 Aluminum Alloy – This alloy is widely used for its excellent castability and good corrosion resistance. It’s ideal for parts that require medium strength, such as engine components, housing, and transmission parts.
● 319 Aluminum Alloy – Known for its high strength, especially at elevated temperatures, the 319 alloy is often used in automotive applications. It offers good fluidity, which is key for creating complex, thin-walled parts.
● 356 Aluminum Alloy – A versatile alloy that balances strength and ductility, 356 is used in industries that require durability and resistance to cracking, such as aerospace.
● 4045 Aluminum Alloy – This alloy offers excellent thermal conductivity, which makes it ideal for heat exchangers and similar applications where heat transfer is a key concern.
● A380 Aluminum Alloy – Often used in die casting, A380 is known for its smooth surface finish and good strength. It is commonly used in automotive and consumer products.
Choosing the right aluminum alloy depends on the specific needs of the part, such as strength, ductility, and environmental resistance. Each alloy has its unique characteristics, which make it better suited for particular applications.
Alloy Type | Strength | Corrosion Resistance | Best Uses |
---|---|---|---|
380 Aluminum | Medium | High | Engine components, transmission parts |
319 Aluminum | High | Moderate | Automotive parts, structural components |
356 Aluminum | High | High | Aerospace, heavy machinery |
4045 Aluminum | Medium | High | Heat exchangers, automotive cooling parts |
A380 Aluminum | Medium | Moderate | Consumer products, die casting |
4. How Are Aluminum Alloys Chosen for Investment Casting?
What’s the real story behind alloy selection? Choosing the right aluminum alloy for investment casting involves considering several factors. One of the first aspects is the part’s required mechanical properties, such as strength, ductility, and impact resistance. For example, parts that need to withstand high temperatures, like engine components, often require high-strength alloys like 319 aluminum.
The casting process also dictates the choice of alloy. For intricate, detailed parts, a high-fluidity alloy is necessary to ensure the molten aluminum can flow into all corners of the mold without issues. Additionally, the part’s operating environment is a critical consideration—whether the component will be exposed to moisture, chemicals, or extreme temperatures.
What’s the kicker here? The key to a successful casting is balancing all these variables to select an alloy that offers the best performance for the application at hand. For instance, in automotive applications, strength, weight, and cost must all be weighed to make the optimal choice. Each type of aluminum alloy offers a different combination of these properties, so it’s important to understand the trade-offs and select accordingly.
Alloy Type | Primary Considerations | Best Applications |
---|---|---|
380 Aluminum | Good fluidity, medium strength | Engine components, housings |
319 Aluminum | High strength, heat resistance | Automotive, structural components |
356 Aluminum | High strength, good fluidity | Aerospace, critical structural parts |
4045 Aluminum | Excellent thermal conductivity | Heat exchangers, cooling systems |
A380 Aluminum | Smooth surface finish, medium strength | Automotive, consumer goods |
5. What Are the Key Properties of Aluminum for Investment Casting?
Aluminum’s properties are what make it an ideal material for investment casting. Ready to dive into some specifics? Here are the key properties that make aluminum so attractive for casting:
● High Strength-to-Weight Ratio – Aluminum offers great strength without the weight of steel or iron. This makes it invaluable in industries like aerospace, where weight reduction is crucial to improve fuel efficiency and performance.
● Excellent Corrosion Resistance – Aluminum naturally forms a protective oxide layer that helps prevent corrosion. This is vital in industries where components are exposed to moisture or corrosive environments, such as marine applications.
● Thermal and Electrical Conductivity – Aluminum’s ability to conduct heat and electricity makes it useful for parts in heat exchangers or electronic components.
● Castability and Fluidity – Aluminum alloys generally have good fluidity, meaning they can easily fill intricate molds. This is essential for creating complex geometries that might be too challenging for other metals.
These properties ensure that aluminum investment casting is a popular choice for industries seeking performance, reliability, and precision. Aluminum castings can perform under demanding conditions while maintaining their structural integrity, making it a go-to material for precision applications.
Property | Benefit to Investment Casting | Examples of Use |
---|---|---|
Strength-to-Weight Ratio | Provides strength without added weight. | Aerospace, automotive components |
Corrosion Resistance | Protects against moisture and chemicals. | Marine, outdoor equipment |
Thermal Conductivity | Efficient heat transfer. | Heat exchangers, automotive cooling |
Castability | Easy to pour into molds with intricate details. | Precision parts, complex geometries |
6. How is Aluminum Prepared for Investment Casting?
What’s the secret to preparing aluminum for investment casting? It starts with getting the aluminum alloy just right. Aluminum casting involves melting the alloy at high temperatures. The key is ensuring that the aluminum is free of impurities. For this, a careful purification process is followed to remove any contaminants that could affect the casting’s quality.
The next step is controlling the grain structure of the molten aluminum. Grain refinement is an important step in improving the mechanical properties of the final cast. Proper grain structure ensures that the casting is both strong and ductile, reducing the chances of defects such as cracking during cooling.
Once the aluminum is prepared, it is poured into molds made from wax patterns. These molds are coated with a ceramic shell, which hardens around the pattern. Afterward, the wax is melted away, and molten aluminum is poured into the cavity, filling the space left by the wax. The result is a highly detailed and precise casting.
Process Step | Description | Key Consideration |
---|---|---|
Melting | Aluminum is melted to the required temperature | Purification to remove impurities |
Grain Refinement | Improving the grain structure of the aluminum | Enhances mechanical properties |
Molding | Aluminum is poured into ceramic molds | Mold design and cooling rates |
7. What Are the Challenges in Aluminum Investment Casting?
So, what’s the challenge? While aluminum investment casting offers many advantages, it’s not without its hurdles. One of the primary challenges is controlling shrinkage and porosity during the cooling phase. Aluminum shrinks as it cools, which can lead to internal voids and defects if not managed properly. A poor cooling rate can cause cracks or warping in the castings.
Porosity is another common issue in aluminum investment casting. It occurs when gases become trapped inside the casting, leading to imperfections in the final product. This can significantly reduce the strength and durability of the cast part, which is a major concern for industries that require highly reliable components.
Furthermore, aluminum is prone to oxidation, especially at high temperatures. During casting, if the aluminum is exposed to air for too long, it can form an oxide layer that affects the casting quality. Controlling the atmosphere during the casting process is essential to prevent oxidation and ensure the aluminum flows properly into the mold.
Challenge | Cause | Solution |
---|---|---|
Shrinkage | Cooling causes aluminum to contract | Control cooling rates carefully |
Porosity | Trapped gases during pouring | Improve mold design and pouring process |
Oxidation | Exposure to air causes surface oxidation | Control casting atmosphere |
8. How Does Aluminum Investment Casting Benefit Different Industries?
Ready for the good part? Aluminum investment casting is widely used in various industries, thanks to its strength, durability, and versatility. Let’s look at some key sectors where aluminum casting is particularly beneficial:
● Aerospace – The aerospace industry benefits from aluminum’s high strength-to-weight ratio. Aluminum components are used in engines, airframes, and other critical parts where reducing weight is essential for improving fuel efficiency and performance.
● Automotive – In the automotive industry, aluminum parts reduce vehicle weight, contributing to better fuel economy and performance. Aluminum is used for engine components, transmission parts, and body panels.
● Consumer Goods – Aluminum castings are also used in consumer electronics, where lightweight and corrosion-resistant materials are needed for components like housings and brackets.
In each of these industries, aluminum investment casting provides manufacturers with high-quality, precision parts that perform well in demanding environments.
Industry | Aluminum Casting Applications | Key Benefits |
---|---|---|
Aerospace | Engine components, airframes | Light weight, high strength |
Automotive | Engine parts, transmission components | Weight reduction, fuel efficiency |
Consumer Goods | Electronics housings, brackets | Durability, corrosion resistance |
9. What Are the Common Defects in Aluminum Investment Casting?
Let’s face it: defects are always a concern in any manufacturing process. In aluminum investment casting, some of the most common defects include surface imperfections, dimensional inaccuracies, and internal voids or porosity. These defects can arise from poor mold design, inconsistent pouring temperatures, or improper cooling rates.
Surface defects may appear as rough textures, uneven surfaces, or blemishes. These imperfections can be caused by impurities in the mold or contamination during the casting process. Dimensional inaccuracies refer to parts not matching the desired measurements, often due to shrinkage or mold misalignment. Meanwhile, internal porosity can cause weak spots in the aluminum, which affect the part’s overall strength.
Common Defect | Cause | Solution |
---|---|---|
Surface Imperfections | Impurities or contamination | Proper mold cleaning and preparation |
Dimensional Inaccuracies | Shrinkage or mold misalignment | Improved mold design and temperature control |
Internal Porosity | Trapped gases in the aluminum | Optimized pouring and cooling rates |
10. How Can Aluminum Casting Defects Be Prevented?
This is where it gets interesting… While defects are inevitable to some extent, there are various ways to reduce them significantly. One of the most effective methods is improving mold design. Molds that are better designed allow the aluminum to flow more evenly, reducing the likelihood of imperfections.
Next, controlling the pouring temperature and pouring speed is critical. Pouring the molten aluminum at the right temperature ensures that the metal fills the mold properly without forming cracks or voids. Similarly, the pouring speed must be controlled to avoid introducing turbulence, which can trap air and create porosity.
Prevention Method | Description | Benefits |
---|---|---|
Mold Design | Improving the mold to ensure even flow | Reduces defects, enhances precision |
Pouring Temperature | Controlling temperature during pouring | Prevents cracks, porosity |
Pouring Speed | Optimizing the speed of pouring molten metal | Reduces turbulence, improves filling |
11. What Are the Advantages of Using Aluminum in Precision Casting?
Why does aluminum stand out in precision casting? Aluminum’s excellent castability makes it the ideal choice for parts requiring high precision. Because aluminum melts at a relatively low temperature, it can be poured into molds with fine details and intricate shapes. This makes aluminum investment casting ideal for industries that require complex parts, such as aerospace and medical devices.
In addition to its precision, aluminum’s strength and lightweight nature allow it to be used in applications where durability and reduced weight are key factors. Parts made from aluminum casting exhibit superior strength while keeping weight low, which is essential in high-performance industries.
Advantage | Description | Industry Applications |
---|---|---|
Castability | High ability to fill detailed molds | Aerospace, medical devices |
Strength-to-Weight | High strength with low weight | Automotive, aerospace |
Precision | Ability to create intricate parts | Aerospace, defense |
12. What Is the Role of Heat Treatment in Aluminum Investment Casting?
Heat treatment plays a crucial role in improving the mechanical properties of aluminum castings. After casting, aluminum parts are typically subjected to heat treatment processes to increase strength, hardness, and other properties. These processes include aging, annealing, and solution heat treatment.
For example, in the aerospace industry, parts are often heat-treated to improve their resistance to fatigue and corrosion. Heat treatment helps the aluminum parts meet the strict requirements for strength and durability in harsh environments.
Heat Treatment Type | Purpose | Effect on Aluminum Casting |
---|---|---|
Aging | Strengthening by heating and cooling | Increases hardness and strength |
Annealing | Softening the metal | Improves ductility and workability |
Solution Heat Treatment | Dispersing alloy elements evenly | Enhances resistance to corrosion |
13. How is the Aluminum Casting Process Monitored for Quality Control?
Quality control in aluminum casting is vital to ensure that the final parts meet strict standards. Nondestructive testing (NDT) is often employed to inspect the integrity of the casting. Common methods include ultrasonic testing, radiography, and X-ray inspection. These tests allow manufacturers to check for internal defects without damaging the part.
Moreover, casting temperature and cooling rate are continuously monitored. This ensures that the aluminum cools uniformly, which reduces the likelihood of defects like warping and shrinkage. By implementing these quality control measures, manufacturers can ensure that every part meets the required standards for performance and reliability.
Quality Control Measure | Description | Purpose |
---|---|---|
Ultrasonic Testing | Uses sound waves to detect internal defects | Identifies cracks or voids |
Radiography | Uses X-rays to inspect the casting | Detects internal imperfections |
Temperature Monitoring | Tracks pouring and cooling temperatures | Ensures uniform cooling |
14. How Does the Cost of Aluminum Compare to Other Metals for Investment Casting?
What’s the deal with aluminum pricing? Compared to other metals like steel and titanium, aluminum is relatively cost-effective for casting. This is a key factor in industries like automotive and consumer electronics, where cost efficiency is crucial. Aluminum also offers superior performance without the higher costs associated with other metals, making it a top choice for manufacturers looking to balance quality and affordability.
However, it’s important to consider that the overall cost of aluminum investment casting depends on several factors, such as the complexity of the design, the type of aluminum alloy, and the volume of production.
Material | Price Per Pound | Common Uses | Advantage |
---|---|---|---|
Aluminum | Lower | Automotive, aerospace, electronics | Lightweight, affordable |
Steel | Medium | Structural components, heavy machinery | Strong, durable |
Titanium | High | Aerospace, medical implants | High strength, resistant to corrosion |
15. What is the Future of Aluminum in Investment Casting?
The future of aluminum in investment casting looks promising. With ongoing developments in alloy formulations and casting technologies, aluminum will continue to be a key material in industries requiring lightweight, high-performance parts. Advances in 3D printing and computer-aided design (CAD) are making it possible to create even more intricate aluminum parts with better precision. Moreover, growing environmental awareness is driving manufacturers to choose materials like aluminum, which can be recycled more easily than other metals.
In conclusion, aluminum investment casting remains a go-to method for industries looking for strong, lightweight, and cost-effective components. As technology advances and more applications emerge, aluminum’s role in the casting process will only continue to grow.
Future Trends | Description | Impact on Aluminum Casting |
---|---|---|
3D Printing | Allows for complex, customized aluminum parts | Increases design flexibility |
Alloy Development | New aluminum alloys for specific needs | Improves casting strength and performance |
Recycling | Enhanced recycling methods for aluminum | Reduces environmental impact |
FAQ Section
Q1: What is investment casting?
Investment casting, also known as the lost-wax process, is a method where a pattern is made of wax, coated with a ceramic shell, and then filled with molten metal to form parts.
Q2: How does aluminum investment casting work?
The process involves creating a mold from a wax pattern, which is then coated with a ceramic shell. After the wax is melted away, molten aluminum is poured into the mold to form the desired part.
Q3: What types of aluminum alloys are used in investment casting?
Common alloys include 380, 319, 356, 4045, and A380, each offering different properties suited for specific applications like automotive or aerospace.
Q4: What industries benefit from aluminum investment casting?
Aluminum casting is widely used in aerospace, automotive, consumer goods, and medical industries due to its lightweight, durable, and corrosion-resistant properties.
Q5: How can aluminum casting defects be avoided?
Defects can be minimized by improving mold design, controlling pouring temperatures, optimizing cooling rates, and thoroughly cleaning the molds before casting.