Titanium alloys have revolutionized industries such as aerospace, medical devices, and automotive due to their impressive strength, low weight, and exceptional corrosion resistance. But what makes these alloys particularly strong? The key lies in understanding their composition and the ways in which their hardness is measured. Specifically, when evaluating the hardness of titanium alloys, the Brinell scale plays a crucial role in determining their resistance to deformation. In this article, we’ll explore the strongest titanium alloys, examine their hardness by the Brinell scale, and discuss why these alloys are indispensable in high-performance applications.
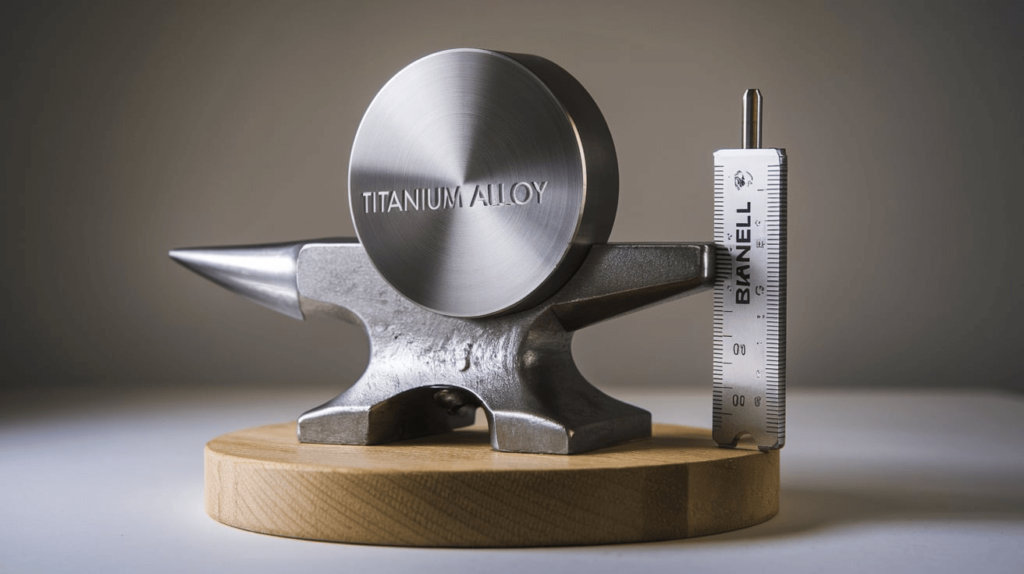
1. Introduction: Understanding Titanium Alloys
Titanium alloys are some of the most robust and versatile materials used in various industries. Combining titanium with other metals creates alloys that offer enhanced mechanical properties, including increased strength, durability, and resistance to corrosion. These alloys are not only known for their structural integrity but also their ability to perform under extreme temperatures and harsh conditions. This article delves into the strongest titanium alloys, focusing particularly on how their hardness is evaluated using the Brinell scale. But here’s the kicker: understanding the strongest titanium alloys isn’t just about knowing their hardness – it’s about how they perform in the real world. So, what’s the real story behind these alloys?
2. The Basics of Titanium Alloys
Titanium, on its own, is a relatively light metal known for its high strength-to-weight ratio. However, when alloyed with elements such as aluminum, vanadium, or molybdenum, it becomes even more resilient. For instance, the addition of aluminum enhances its strength and resistance to corrosion, while vanadium improves its ductility. What’s the significance of these combinations? These alloys are designed to meet the demanding requirements of industries like aerospace, automotive, and medical fields. The presence of different elements in titanium alloys dictates the alloy’s specific properties, and depending on the application, these properties can vary significantly.
Titanium alloys are categorized by grades, each offering unique benefits. For example, Ti-6Al-4V, one of the most common titanium alloys, is composed of 90% titanium, 6% aluminum, and 4% vanadium. It’s known for its excellent strength-to-weight ratio, making it ideal for aerospace applications. Another grade, Ti-5Al-2.5Sn, contains 5% aluminum and 2.5% tin and is often used in industrial applications requiring resistance to oxidation. These different titanium alloy grades are specifically tailored to their applications, and each brings its own set of advantages to the table. Ready for the good part? Let’s explore the hardness of these alloys by the Brinell scale.
3. How Hardness is Measured: The Brinell Scale Explained
To understand the strongest titanium alloys, it’s essential to first comprehend how hardness is measured. The Brinell scale is one of the most common methods for determining the hardness of materials, especially metals like titanium. But how does it work? In the Brinell hardness test, a hard steel or carbide ball is pressed into the material under a specific load, and the diameter of the resulting indentation is measured. The hardness value is then calculated based on the size of this indentation.
In comparison to other hardness tests, such as the Rockwell or Vickers scales, the Brinell test is particularly useful for materials like titanium alloys. This is because the test can accommodate larger particles and is more suited for materials with irregular surfaces. What’s the real story? Titanium alloys, especially the strongest ones, typically score higher on the Brinell scale, indicating their superior ability to resist indentation and wear. But, here’s the kicker: the hardness of titanium alloys doesn’t tell the whole story – their strength also depends on their ability to withstand stress and fatigue. This is where the comparison between different alloys gets interesting.
4. The Strongest Titanium Alloys: Top Contenders
Now, let’s take a closer look at the strongest titanium alloys and how they measure up on the Brinell scale. One of the top contenders in terms of strength is Ti-6Al-4V, a titanium alloy composed of 6% aluminum and 4% vanadium. With a Brinell hardness of around 330, Ti-6Al-4V is highly valued in industries like aerospace and military because of its excellent strength-to-weight ratio. This alloy is not only hard but also incredibly resistant to corrosion, which is why it is often used for components exposed to high stresses, such as turbine blades and structural parts.
Another strong titanium alloy is Ti-5Al-2.5Sn. This alloy, which contains 5% aluminum and 2.5% tin, has a lower Brinell hardness of approximately 320 but is still widely used in applications requiring high strength and low weight. It is often used in industrial applications such as heat exchangers and reactors, where its resistance to oxidation is essential.
Let’s not forget Ti-6Al-2Sn-4Zr-6Mo, an alloy with a Brinell hardness of 350, making it one of the hardest titanium alloys. This alloy is used in more demanding applications, including in the aerospace and marine industries, where both strength and corrosion resistance are critical. So, what’s the takeaway here? The hardest titanium alloys are not only chosen for their strength but also for their versatility across different environments. What’s next? Let’s explore how the hardness of these alloys compares to other metals.
5. Titanium Alloy Grades and Their Applications
Titanium alloys are classified into different grades, each designed for specific applications. These grades are primarily distinguished by their chemical composition and the properties they offer. For example, Ti-6Al-4V, which contains 90% titanium, 6% aluminum, and 4% vanadium, is considered the standard grade for many applications. It is commonly used in aerospace, where its high strength-to-weight ratio is crucial for parts like aircraft components and rocket engines.
Grade 2 titanium, which is commercially pure titanium, is often used for industrial applications requiring high corrosion resistance but without the need for extreme strength. In contrast, Ti-5Al-2.5Sn is used in the production of pipes and tubes, particularly in marine and offshore environments due to its ability to resist corrosion in saltwater.
What’s the real story? Each titanium alloy grade has its own specific benefits, and understanding these differences is key to choosing the right material for a given application. Let’s take a look at a comparison of the different titanium alloy grades and their respective hardness values.
Titanium Alloy Grade | Composition | Brinell Hardness | Common Applications |
---|---|---|---|
Ti-6Al-4V | 90% Titanium, 6% Aluminum, 4% Vanadium | 330 | Aerospace, Military, Medical |
Ti-5Al-2.5Sn | 95% Titanium, 5% Aluminum, 2.5% Tin | 320 | Industrial, Heat exchangers, Reactors |
Ti-6Al-2Sn-4Zr-6Mo | 90% Titanium, 6% Aluminum, 2% Tin, 4% Zirconium, 6% Molybdenum | 350 | Aerospace, Marine, Chemical Processing |
6. What Makes Titanium Alloys So Strong?
So, what makes titanium alloys so strong? The answer lies in the unique properties of titanium itself, combined with the alloying elements that are added to enhance its performance. Titanium is already a strong material, known for its excellent strength-to-weight ratio. But when elements like aluminum, vanadium, and molybdenum are added to the mix, the result is an alloy that offers superior mechanical properties.
Take, for example, Ti-6Al-4V, which contains aluminum to increase its strength and resistance to corrosion. This alloy also benefits from vanadium, which improves its ductility and ability to withstand stress. The combination of these elements allows the alloy to perform exceptionally well in high-stress applications such as aerospace. Additionally, the presence of molybdenum in alloys like Ti-6Al-2Sn-4Zr-6Mo further improves their resistance to corrosion, especially in harsh marine environments. What’s the kicker? These additions don’t just enhance strength; they also make titanium alloys incredibly versatile, able to perform across a wide range of industries.
7. The Hardest Titanium Alloys by Brinell Scale
When evaluating the hardness of titanium alloys, the Brinell scale is often the go-to measurement method. As we’ve already discussed, the Brinell hardness test measures the resistance of a material to indentation by pressing a hard ball into the surface under a standard force. The stronger the material, the smaller the indentation. Ti-6Al-4V, with a Brinell hardness of around 330, is one of the hardest titanium alloys available. This makes it an ideal choice for applications where both strength and resistance to wear are important.
Another noteworthy alloy is Ti-6Al-2Sn-4Zr-6Mo, which boasts a Brinell hardness of 350. This makes it particularly effective in extreme environments, where materials need to withstand high pressure and abrasion. Despite the variation in hardness values, titanium alloys generally rank highly on the Brinell scale, indicating that they are highly resistant to deformation under stress. Ready for the good part? These alloys are chosen not only for their hardness but also for their resistance to corrosion, making them essential in high-performance applications. Let’s dive deeper into the challenges of producing these alloys.
8. Titanium Alloy Strength vs. Other Metals
When comparing titanium alloys to other metals, such as steel, aluminum, or nickel alloys, it’s clear that titanium offers some significant advantages. Titanium alloys are particularly known for their excellent strength-to-weight ratio, which makes them a preferred choice for aerospace applications. For example, Ti-6Al-4V is known for being much lighter than steel, while offering similar or even greater strength.
What’s the real story? Titanium alloys perform exceptionally well in harsh environments where corrosion resistance is crucial. While steel may offer higher tensile strength, titanium alloys excel in areas where weight reduction and resistance to oxidation are needed. Aluminum, on the other hand, may be lighter but doesn’t provide the same strength or resistance to wear. So, why choose titanium alloys over other metals? Simply put, titanium alloys strike the perfect balance between strength, weight, and durability. Let’s take a look at how titanium alloys stack up against steel and aluminum in terms of hardness and strength.
Material | Hardness (Brinell) | Strength (MPa) | Applications |
---|---|---|---|
Titanium Alloy (Ti-6Al-4V) | 330 | 900 | Aerospace, Military |
Steel (AISI 1045) | 300 | 600 | Construction, Automotive |
Aluminum (Al 6061) | 95 | 310 | Aerospace, Automotive |
9. Challenges in Producing Strong Titanium Alloys
Producing strong titanium alloys is no easy feat. The process involves several complex steps, including high-temperature forging, casting, and heat treatment. These processes can be costly and require precise control to ensure the right properties are achieved. One of the challenges of alloy production is managing the addition of alloying elements in the right proportions. Too much of an element can lead to brittleness, while too little may result in weak performance under stress. Additionally, titanium alloys must be carefully heat-treated to improve their mechanical properties. This process can be time-consuming and expensive, which can increase the overall cost of producing titanium alloys. However, despite these challenges, the benefits of titanium alloys outweigh the costs, particularly when it comes to their performance in demanding applications.
10. Corrosion Resistance and Durability of Titanium Alloys
Titanium alloys are known for their exceptional resistance to corrosion. This is one of the key reasons they are used in industries like aerospace, marine, and chemical processing, where materials are exposed to harsh environments. Titanium’s ability to form a passive oxide layer on its surface makes it highly resistant to corrosion, even in aggressive environments like seawater. The addition of alloying elements like aluminum and vanadium further enhances this resistance, making titanium alloys suitable for applications where other materials would degrade quickly. But here’s the kicker: corrosion resistance isn’t just about preventing rust. It also ensures that titanium alloys maintain their strength and structural integrity over time, even under extreme conditions. Let’s look at how titanium alloys hold up in some of the harshest environments.
Alloy Grade | Corrosion Resistance | Common Applications |
---|---|---|
Ti-6Al-4V | Excellent | Aerospace, Medical |
Ti-5Al-2.5Sn | Good | Marine, Offshore |
Ti-6Al-2Sn-4Zr-6Mo | Superior | Marine, Chemical Processing |
11. Technological Advancements in Titanium Alloy Development
The development of titanium alloys has come a long way, and technological advancements continue to push the boundaries of what’s possible. One such advancement is the use of 3D printing, or additive manufacturing, which allows for the creation of complex geometries with titanium alloys. This has revolutionized industries like aerospace, where parts can now be produced more efficiently and with fewer materials. Furthermore, research into new alloy combinations and manufacturing techniques is ongoing, with the goal of improving the strength, durability, and cost-efficiency of titanium alloys. What’s the good part? These advancements open the door for new applications in industries such as medical implants, military hardware, and beyond. The future of titanium alloys looks bright, and innovations are paving the way for even stronger, more versatile materials.
12. Titanium Alloys in Aerospace: The Need for Strength
The aerospace industry demands materials that can withstand extreme stress, temperature variations, and corrosion. Titanium alloys, particularly Ti-6Al-4V, have become a staple in this industry due to their high strength and low weight. These alloys are used in a variety of applications, including aircraft frames, turbine engines, and spacecraft components. What makes titanium alloys so well-suited for aerospace? It’s the unique combination of strength, weight, and resistance to extreme environments that makes them ideal for high-performance aerospace applications. Ready for the good part? Let’s look at some real-world examples of titanium alloys in use in the aerospace industry.
13. Titanium Alloys in Medical Devices: Strength and Biocompatibility
Titanium alloys also play a crucial role in the medical field, particularly in the production of implants and prosthetics. The reason titanium is so popular for medical applications is that it is biocompatible, meaning it doesn’t react negatively with the human body. Alloys like Ti-6Al-4V are used in hip replacements, dental implants, and surgical instruments. What’s the kicker here? The combination of strength and biocompatibility ensures that titanium alloys can be safely implanted into the human body, where they will perform reliably for years.
14. The Future of Titanium Alloys: What’s Next?
The future of titanium alloys looks incredibly promising. Ongoing research continues to improve their strength, durability, and affordability. Advancements in manufacturing techniques, such as additive manufacturing and advanced casting processes, are making it easier to produce high-performance titanium parts. But here’s the kicker: as new materials emerge, titanium alloys will continue to evolve, meeting the ever-growing demands of industries like aerospace, medical, and defense. So, what’s next for titanium alloys? The sky’s the limit.
15. Conclusion: Which Titanium Alloy is Truly the Strongest?
In conclusion, the strongest titanium alloys are those that combine superior strength with exceptional corrosion resistance. Ti-6Al-4V remains the gold standard for many industries, but alloys like Ti-6Al-2Sn-4Zr-6Mo and Ti-5Al-2.5Sn offer additional advantages in specific applications. The future of titanium alloys looks bright, and continued advancements in technology will only make them more indispensable in high-performance applications. The strongest titanium alloy is ultimately the one best suited for the specific demands of a given application, whether it be aerospace, medical, or marine.
Q1: What is a titanium alloy?
A titanium alloy is a material made by combining titanium with other metals like aluminum, vanadium, and molybdenum. These combinations improve its strength, corrosion resistance, and other key properties.
Q2: How does the Brinell hardness scale work?
The Brinell hardness scale measures a material’s resistance to indentation. A ball is pressed into the surface of the material, and the hardness is determined based on the size of the indentation left.
Q3: Which titanium alloy is the hardest?
Ti-6Al-4V is often considered one of the hardest titanium alloys, with a Brinell hardness of around 330, making it ideal for demanding applications in aerospace and military industries.
Q4: What industries use the hardest titanium alloys?
Industries like aerospace, medical, automotive, and defense commonly use the hardest titanium alloys for applications that require strength, lightweight materials, and resistance to extreme environments.
Q5: How does titanium alloy strength compare to other metals?
Titanium alloys offer a better strength-to-weight ratio than many other metals, including steel and aluminum, making them ideal for high-performance applications where weight reduction and strength are critical.