Understanding High-Temperature Alloys
What Are High-Temperature Alloys?
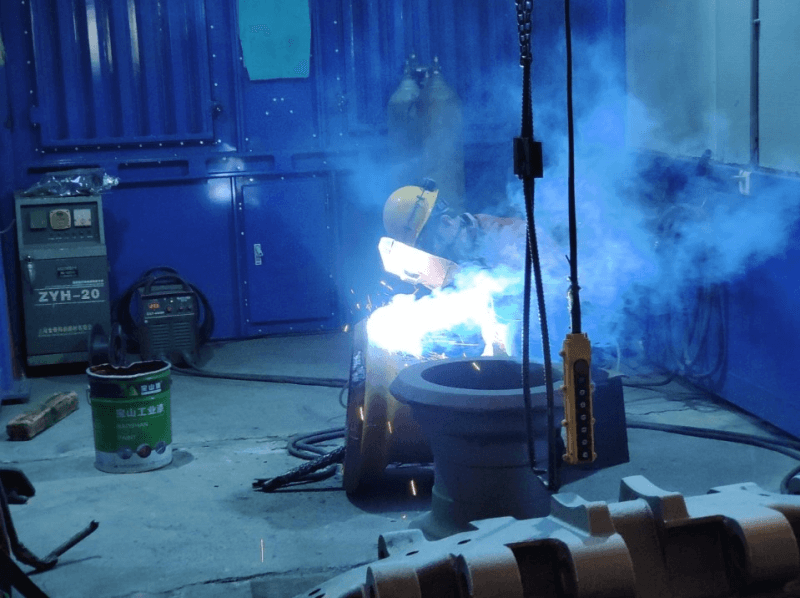
High-temperature alloys serve as essential materials within environments that involve relentless heat, often beyond what conventional metals handle without warping or weakening. These specialized alloys retain structural strength when exposed to elevated furnace-like conditions. Engineers working in advanced industries prefer such solutions because they do not soften easily or degrade under stress. This ability helps prevent catastrophic failures that otherwise cause downtime or hazards. You might be wondering: How do these alloys maintain such resilience? Through carefully designed chemical compositions and microstructures that stabilize grains and phases, they endure harsh thermal cycling. These alloys may incorporate nickel, cobalt, or iron as primary elements, supplemented by chromium, molybdenum, tungsten, and aluminum. Each added element plays a specific role, possibly strengthening grain boundaries or improving oxidation resistance.
Why They Matter In Extreme Conditions
Selecting an alloy that holds firm under punishing heat matters greatly. Consider a turbine blade facing continuous blasts of scorching gases. Without proper alloys, that blade would distort or crack. Similarly, refinery furnace tubes must endure scaling and oxidation without losing structural integrity. Here’s the deal: Failure means lost productivity, expensive maintenance, or worse. High-temperature alloys support stable operations and extended lifespans, offering peace of mind.
Importance Of Choosing The Right Alloy
Professionals with procurement responsibilities do not gamble when picking materials. They seek alloys that meet exacting standards. A suitable alloy resists creep, corrosion, and scale formation, enabling critical components to remain stable through countless cycles. The truth is: Not all alloys shine equally under fire. Understanding differences helps narrow choices, ensuring components last longer, enhance system efficiency, and minimize downtime. Ultimately, investing in robust, specialized alloys promotes safety, maintains output quality, and offers a competitive advantage in demanding sectors.
Key Performance Factors For High-Temperature Alloys
Strength Retention Under Intense Heat
These alloys must maintain tensile and yield strength even when temperatures climb sky-high. Structural integrity at elevated ranges prevents deformation. You might ask: Why does strength matter so much? Imagine rotating turbine blades or boiler tubes under immense stress. If alloys soften, critical machinery stalls or fails.
Resistance To Corrosion, Oxidation, And Thermal Fatigue
High-temperature exposure is rarely benign. Corrosive atmospheres, oxidizing conditions, and thermal gradients push materials to their limits. Effective alloys form protective oxide layers or incorporate elements that resist corrosive attacks. Now, let’s dive deeper: Steels might falter above certain thresholds, but properly crafted superalloys maintain protective films that prevent scale buildup or pitting. This resistance prolongs service life and reduces maintenance intervals.
Stability Of Mechanical Properties Over Long Service Lives
Components such as jet engine blades face countless heat-up and cool-down cycles. Over time, repeated expansion and contraction would fatigue standard metals. High-temperature alloys engineered with grain boundary stabilizers and precise heat treatments can withstand these fluctuations. Here’s a key point: Long-term stability reduces costly replacements. Operators enjoy predictable performance over years, not weeks.
Influence On Alloy Selection
Procurement teams weigh these performance factors carefully. They consider maximum operating temperatures, exposure times, and environmental conditions. You might be wondering: How to choose wisely? Consulting experienced metallurgists and reviewing case studies help identify an alloy that won’t buckle under mechanical or chemical stress. This decision ensures machines run smoothly, meet regulatory standards, and deliver consistent output without unexpected shutdowns. Ultimately, robust alloy selection aligns with strategic business goals and operational reliability.
Common High-Temperature Alloy Families
Nickel-Based Alloys
Nickel-based superalloys often dominate high-temperature environments. Nickel’s crystal structure remains stable, helping alloys hold shape under punishing conditions. Here’s the deal: Inconel and other nickel-rich compositions thrive in jet engines, turbines, and chemical plants. These alloys resist creep, offer standout oxidation resistance, and deliver impressive fatigue strength.
Cobalt-Based Alloys
Cobalt-based solutions excel where toughness and wear resistance matter. Gas turbines or industrial valves often feature cobalt alloys that endure superheated steam or corrosive flue gases. You might be wondering: Are they pricier than nickel ones? They can be, but their ability to maintain surface integrity compensates by limiting costly part replacements.
Iron-Nickel Alloys
Iron-nickel blends balance cost and performance. They excel at intermediate temperatures and meet budget constraints better than pricier superalloys. Now, let’s dive deeper: These alloys suit scenarios where top-tier extremes aren’t required. They appear in industrial furnaces, moderate-temperature tools, and certain petrochemical components.
Titanium Alloys
Titanium-based alloys bring high strength-to-weight ratios. They excel in aerospace components like engine parts where weight reduction matters. Though not always suited for ultra-high temperatures, they handle moderately high ranges effectively. You might ask: Are they cost-effective? They often cost more upfront, but long-term savings emerge from fuel efficiency and extended part life.
Proprietary Brands (Inconel, Hastelloy, Etc.)
Branded alloys like Inconel or Hastelloy represent tried-and-true solutions refined for decades. Here’s a key point: Choosing a known brand reduces guesswork. Such alloys come with established data sheets, proven track records, and global availability. Engineers trust these names because they know the material behaves reliably under the conditions promised.
Typical Industries And Applications That Require High-Temperature Alloys
Aerospace Components
Aerospace thrives on high-temperature alloys. Jet turbines, afterburners, and exhaust components operate under constant thermal stress. You might be wondering: Without these materials, engines couldn’t reach needed thrust levels safely. Pilots rely on metal parts that never deform mid-flight.
Power Generation Equipment
Power plants depend on superalloys for steam turbines, boiler tubes, and superheaters. Elevating plant efficiency often demands pushing steam temperatures ever higher. Here’s the deal: Without robust alloys, power generation faces inefficient cycles or downtime due to part failures.
Petrochemical And Refining Equipment
Refinery furnaces and chemical reactors push materials hard. Inside these units, harsh chemicals and scorching environments necessitate alloys that remain stable. Now, let’s dive deeper: A leaky furnace tube means unplanned shutdowns and lost output. Reliable alloys prevent such costly surprises.
Automotive Exhaust Systems And Turbochargers
High-performance cars and commercial vehicles rely on heat-resistant alloys to keep engines running optimally. Turbochargers encounter extreme heat from exhaust gases. You might ask: Why not just use cheaper steel? Regular steel weakens too quickly. Specialized alloys preserve efficiency and reduce repairs.
Specialized Industrial Manufacturing
Certain manufacturing processes, like glass forming or steelmaking, need tooling that withstands intense radiant heat. The truth is: Standard metals would soften or oxidize rapidly. With high-temperature alloys, equipment remains stable, production lines run smoother, and quality remains consistent.
Understanding Nickel-Based Superalloys: The Gold Standard
Composition And Dominance Of Nickel
Nickel-based superalloys incorporate elements like chromium, aluminum, and titanium for enhanced strength. Nickel’s face-centered cubic structure remains stable at high temperatures. You might be wondering: Why nickel, not something else? Nickel’s atomic arrangement resists slipping or grain boundary weakening, enabling alloys like Inconel 718 or Rene 41 to excel at extreme temperatures.
Notable Examples And Their Advantages
Inconel 600 or 718 appear widely in aviation turbines, nuclear reactors, and chemical plants. Here’s the deal: These alloys resist both oxidation and corrosion simultaneously. Their stable microstructures stand firm under creep loads. Engineers value this dual capability because maintenance intervals decrease.
Limitations And Cost Considerations
Though nickel-based alloys outperform many alternatives, their costs run high. Complex manufacturing processes, expensive raw materials, and strict quality controls raise prices. Now, let’s dive deeper: Decision-makers must consider whether the long-term benefits outweigh upfront expenses. In many cases, extended service life and reduced downtime justify costs.
Why Nickel-Based Alloys Matter
When no shortcuts exist in critical applications, nickel-based solutions deliver unmatched reliability. You might ask: How do they handle repeated thermal cycling? Carefully engineered grain structures and precipitation-hardened phases ensure minimal deformation. Reliability under severe conditions preserves operational efficiency and safety, making these alloys the go-to choice for engineers demanding absolute performance.
Cobalt-Based Alloys: When Toughness And Wear Resistance Matter
Typical Compositions And Microstructures
Cobalt-based alloys often blend cobalt with chromium, tungsten, or nickel. They form stable carbide phases resistant to wear at elevated temperatures. You might be wondering: What sets them apart from nickel-based? Although both resist heat, cobalt alloys excel in environments with intense mechanical abrasion and hot corrosion.
Key Properties And Application Examples
Industrial gas turbines, nozzle guide vanes, and marine applications count on cobalt alloys. Here’s the deal: Their inherent hardness resists erosive conditions found in turbines swallowing abrasive particulates. Valves handling corrosive chemicals at red-hot conditions depend on cobalt alloys that preserve sealing surfaces.
Challenges: Availability, Cost, Fabrication
Cobalt can be more expensive and less readily available. Fabrication may pose challenges because machining and welding demand skilled technicians. Now, let’s dive deeper: Despite these hurdles, companies willing to invest benefit from components that outlast cheaper alternatives. Long-term gains include fewer replacements and lower maintenance costs.
Why Opt For Cobalt-Based Alloys?
Some environments push metals beyond simple heat resistance. You might ask: What if components face constant mechanical stress and corrosive agents? Cobalt alloys hold their shape, hardness, and integrity, ensuring minimal downtime. By choosing cobalt-based materials, procurement professionals secure reliability in applications where failure is not an option.
Iron-Nickel Alloys: Balancing Cost And Performance
Unique Composition Ranges
Iron-nickel alloys combine iron’s affordability with nickel’s stability. Although less robust than pure nickel superalloys, these materials fit environments where moderately high temperatures occur. You might be wondering: Are they second-tier solutions? Not necessarily. They fill a niche that demands decent performance without extreme conditions.
Ideal Use Cases
Intermediate turbines, furnace components, and equipment in power plants or refineries may use iron-nickel alloys. Here’s the deal: Where cost sensitivity exists, these alloys provide a sweet spot. They deliver adequate creep resistance, moderate oxidation protection, and manageable costs, making them appealing for non-critical components.
Comparisons With Nickel-Based Superalloys
Pure nickel-based alloys might outperform iron-nickel blends, but at a premium. Now, let’s dive deeper: Sometimes engineers realize that super-expensive alloys exceed project requirements. Iron-nickel options then make sense. They achieve stable operations where only moderate heat loads apply.
Market Availability And Sourcing
Iron is abundant and less costly. Adding nickel raises properties without ballooning expenses. You might ask: Where do I find them? Many suppliers stock iron-nickel options suitable for intermediate applications. Their availability and price stability simplify procurement. This balance between cost and capability often appeals to decision-makers who must stretch budgets.
Titanium Alloys: Lightweight Solutions For High-Heat Environments
Why Titanium?
Titanium alloys weigh significantly less than nickel-based counterparts. Aerospace and racing applications love this quality. You might be wondering: Can they handle truly extreme heat? They operate well in moderately high ranges, though not as high as nickel superalloys. Still, their strength-to-weight ratio impresses.
Advantages In Specific Applications
Aircraft engine components benefit from titanium alloys that reduce overall mass and improve fuel efficiency. Here’s the deal: Lighter engines mean aircraft can carry more payload or fly farther. Automotive turbochargers see similar advantages, pushing performance limits.
Drawbacks And Limitations
Titanium’s cost ranks higher than ordinary steels, and machining can be challenging due to hardness. Now, let’s dive deeper: In some cases, titanium alloys approach price points of more advanced materials. Engineers must evaluate if weight savings and strength justify these costs.
Ideal Operating Conditions
When environments demand some heat resistance but not top-tier extremes, titanium alloys shine. You might ask: Are they corrosion-resistant? Yes, their oxide film protects surfaces. Their niche lies between standard steels and ultra-high-temperature superalloys, offering an excellent compromise for applications where both weight and moderate temperature endurance matter.
Material Testing And Qualification Standards
Common Industry Standards
Reliable materials must pass rigorous tests before deployment. ASTM, ISO, and other organizations set benchmarks. You might be wondering: Why bother with tests? Without standardized testing, suppliers could deliver subpar products.
Testing Methods For High-Temperature Alloys
Tensile tests measure strength at elevated conditions. Creep and stress-rupture tests check how long an alloy withstands constant stress under heat. Here’s the deal: Such data guides engineers who must confirm alloys won’t deform prematurely.
Traceability And Certification
Quality assurance involves verifying alloy composition, heat treatment history, and manufacturing processes. Now, let’s dive deeper: Certified mill test reports detail chemical and mechanical properties. These documents instill confidence in buyers.
Importance Of Third-Party Inspection
External auditors verify compliance. This independent scrutiny reduces risk of fraudulent materials. You might ask: What if materials fail tests? Then adjustments happen before deployment. In practice, rigorous testing ensures that selected alloys meet intended specifications, reducing mishaps and enabling safer operations.
Comparing Alloys: How To Select The Right One
Assessing Operating Temperature Ranges
Each alloy excels at specific temperature ranges. Matching alloy characteristics with operating conditions matters. You might be wondering: Start by identifying maximum operating temperature, then shortlist alloys capable of enduring that heat without losing strength.
Considering Environmental Conditions
Hot, oxidizing atmospheres differ from corrosive chemical vapors. Here’s the deal: Choose alloys known for stability under given conditions. Engineers examine data sheets and consult experts to pick a stable solution.
Balancing Cost, Availability, And Performance
Budgets matter. Cheap alloys might fail early, while premium superalloys improve lifecycle costs. Now, let’s dive deeper: Finding a sweet spot involves evaluating total cost of ownership. Will a pricier alloy reduce downtime expenses?
Consulting Experts
Professional metallurgists, suppliers, or lab test results guide final decisions. You might ask: Without expert input, guesswork leads to risk. Engage knowledgeable professionals who understand alloy properties and can align them with project requirements. This approach prevents costly trial-and-error.
Fabrication And Machining Considerations
Welding Challenges
High-temperature alloys present welding challenges. Special filler metals, preheating, or post-weld treatments might be required. You might be wondering: Are these steps complicated? Skilled welders and strict procedures ensure joints remain stable under stress.
Machining Difficulties
Hard alloys wear tooling quickly. Here’s the deal: Specialized cutting tools and coolants extend tool life. CNC programmers adjust feed rates to maintain precision without damaging parts.
Heat Treatments And Coatings
Heat treatments stabilize microstructures. Coatings add oxidation or corrosion resistance. Now, let’s dive deeper: Proper heat treatment can enhance creep strength, while coatings prevent scaling in turbines.
Additive Manufacturing Potential
3D printing opens new possibilities. Complex shapes formed layer-by-layer reduce material wastage. You might ask: Does additive manufacturing handle superalloys? Yes, with proper process control. This approach customizes component geometry for better performance and possibly reduces lead times.
Lifecycle And Maintenance Factors
Expected Service Life
Well-chosen alloys operate reliably for years. You might be wondering: Longer service means fewer replacements and stabilized budgets.
Inspection Intervals And Nondestructive Testing
Regular checks using ultrasonic or radiographic methods detect early cracks. Here’s the deal: Catching issues sooner prevents catastrophic failures. Maintenance teams plan shutdowns strategically, minimizing disruptions.
Repair And Refurbishing Strategies
Damaged parts sometimes get refurbished instead of replaced. Skilled technicians apply overlays or re-heat-treat components. Now, let’s dive deeper: Such strategies save money and resources.
Replacement Planning
Eventually, parts reach end-of-life. Proactive planning ensures spares remain in stock. You might ask: Does early replacement raise costs? Actually, well-timed replacements prevent costly emergency interventions and maintain stable operations.
Real-World Case Studies
Aerospace Turbine Blade Selections
A jet engine blade might switch from a cheaper alloy to a nickel-based superalloy. Performance improves, while downtime drops. You might be wondering: Is it worth extra cost? Field data often shows fewer failures, higher efficiency, and better fuel economy.
Petrochemical Furnace Tubes
Refineries upgrade from standard steels to corrosion-resistant alloys. Here’s the deal: Production stabilizes, less scaling occurs, and safety improves. Over time, the investment pays off.
Power Plant Turbine Components
Advanced alloys help power plants hit higher temperatures, boosting efficiency. Now, let’s dive deeper: Operators see improved electricity output from the same fuel input. Cost savings and reduced emissions follow.
Lessons From Failures
Some companies learn lessons after alloys fail prematurely. You might ask: What caused it? Often poor material selection or insufficient testing. These stories highlight that upfront research saves headaches and improves system reliability.
Cost-Benefit Analysis
Evaluating Upfront Material Costs
Premium superalloys cost more than standard metals. You might be wondering: Why pay extra? They last longer and reduce downtime, offsetting initial investment.
Reduced Downtime And Maintenance
Long-life materials mean fewer shutdowns. Here’s the deal: Operational continuity preserves revenue and reputation. Fewer repairs free resources for other projects.
Strategic Sourcing And Supplier Partnerships
Close collaboration with reputable suppliers ensures consistent quality. Now, let’s dive deeper: Reliable supply chains mitigate delays and lower risk of counterfeit materials.
Balancing Material Performance With Budgets
Procurement teams crunch numbers. They consider lifecycle costs, potential losses due to failures, and any performance gains. You might ask: Does a top-tier alloy provide tangible ROI? Often yes, when factoring in efficiency gains, reduced surprises, and peace of mind.
Future Trends In High-Temperature Alloys (Conclusion)
New Alloy Compositions And Research
Researchers push boundaries. Novel compositions and nanoparticle-reinforced alloys aim higher. You might be wondering: Will future alloys endure even harsher environments? Likely yes, as R\&D refines atomic arrangements.
Advancements In Coatings
Improved coatings extend part lifetimes. Here’s the deal: They shield underlying alloys from oxidation or corrosion, cutting down on replacements.
Digital Tools And Predictive Maintenance
Simulations model how alloys behave under future conditions. Now, let’s dive deeper: Predictive analytics guide maintenance schedules, avoiding guesswork.
Sustainability Considerations
Eco-friendliness grows important. Recycling high-value alloys and using cleaner production methods matter. You might ask: Will this change industry priorities? Probably, as stakeholders demand responsible stewardship. Tomorrow’s alloys will likely be greener, smarter, and even more resilient.
FAQ
What Defines A High-Temperature Alloy?
A high-temperature alloy refers to any metal mixture engineered for stable mechanical properties in elevated environments. Such materials resist deformation, oxidation, and creep under prolonged exposure to harsh conditions. They withstand demanding aerospace, power generation, or refining scenarios where standard metals would fail.
How Do Engineers Choose The Right Alloy?
Professionals consider operating temperature ranges, corrosive atmospheres, and mechanical loads. They study data sheets, consult metallurgists, and factor in cost constraints. Each choice depends on balancing performance requirements and budget limitations. Ultimately, experienced insight and industry guidelines help narrow the selection.
Are Nickel-Based Alloys Always The Best Choice?
Nickel-based superalloys excel where extreme conditions exist, but they are not always necessary or cost-effective. Iron-nickel or cobalt alloys might suffice for moderate conditions at lower cost. Choosing the best alloy depends on application needs, budget, and performance expectations.
Why Consider Titanium Instead Of Nickel?
Titanium alloys weigh less while still offering decent heat resistance. Aerospace and racing industries benefit from weight reduction, improved fuel economy, and enhanced speed. Though not suitable for the highest temperatures, titanium provides a sweet spot for moderate conditions where mass matters.
How Important Is Proper Testing?
Testing validates an alloy’s properties, ensuring it meets advertised standards. Without proper testing, buyers risk receiving inferior materials that may fail prematurely. Rigorous evaluation builds trust and prevents expensive surprises. Certified test reports and third-party inspections enhance reliability.
Can Additive Manufacturing Improve Alloy Performance?
Additive manufacturing allows producing complex shapes layer-by-layer, enabling designs that optimize airflow or reduce weight. This technology offers custom geometries that traditional machining struggles with. In some cases, printed components outperform their conventionally manufactured counterparts due to enhanced design freedom.
Do Suppliers Provide Technical Support?
Many reputable suppliers offer technical consultation. They review project requirements, suggest suitable alloys, and guide customers through selection. Partnering with knowledgeable suppliers reduces trial-and-error, streamlines procurement, and ensures materials match intended operating conditions.
Will Future Alloys Be More Affordable?
As research improves efficiency and extraction methods, certain alloys may become more cost-competitive. Moreover, better recycling and material recovery techniques might lower costs over time. While cutting-edge superalloys remain expensive, market forces and innovation might gradually reduce price disparities.
How Often Should Components Be Inspected?
Inspection intervals vary by industry, operating conditions, and safety standards. Regular nondestructive testing detects cracks or deformations before catastrophic failure occurs. Adhering to recommended intervals ensures reliable performance and avoids expensive unplanned shutdowns.
Are There Environmental Benefits To Better Alloys?
High-temperature alloys improve energy efficiency. Turbines running hotter produce more power from the same fuel, cutting emissions. Longer-lasting components reduce waste and resource consumption. Over time, better alloys can contribute to a greener, more sustainable industrial landscape.