Heat-resistant metals play a critical role in industries requiring materials that can withstand extreme temperatures without losing their integrity. From aerospace to automotive, these metals are essential for ensuring long-term performance under high-heat conditions. But when choosing heat-resistant metals, one must also consider the reputation and expertise of the manufacturers. This article takes you through some of the top manufacturers, their key properties, and the qualities that set them apart from the competition. By the end of this article, you will understand who the leaders are in the heat-resistant metal industry and what makes their products top-tier.
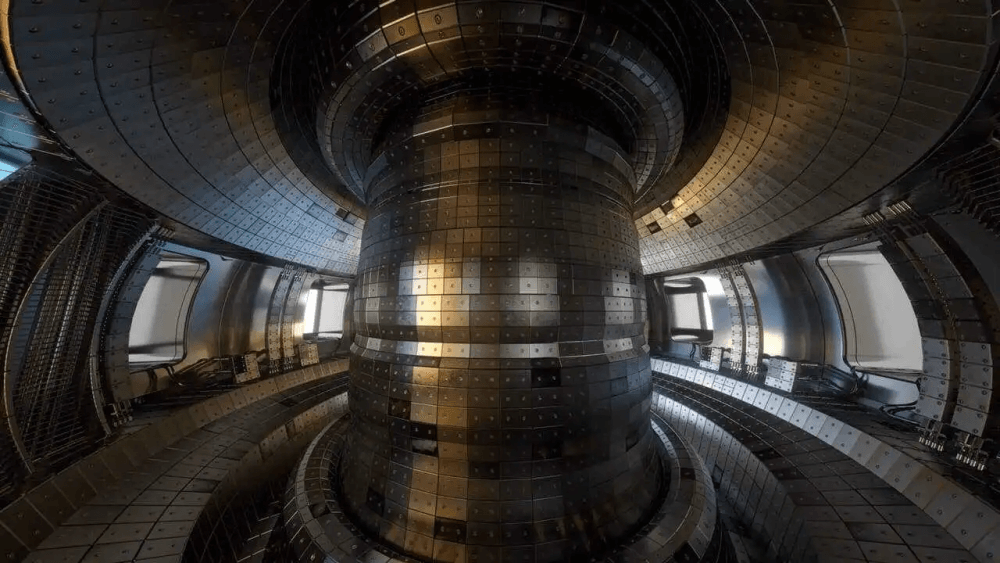
1. What Are Heat-Resistant Metals?
Heat-resistant metals are alloys specifically designed to maintain their strength and structural integrity under high temperatures. Unlike common metals that can melt or deform at elevated temperatures, heat-resistant metals can endure extreme conditions without losing functionality. These metals are usually employed in industries such as aerospace, automotive, and energy, where high-performance materials are required to operate under intense heat for prolonged periods.
But here’s the kicker: not all heat-resistant metals are created equal. Some offer greater thermal stability, while others provide better oxidation resistance or superior mechanical strength. Understanding the different types and their applications is crucial when selecting the right material for a particular task.
Types of Heat-Resistant Metals
Heat-resistant metals come in various forms, each offering specific advantages. Some of the most common types include:
Metal Type | Key Properties | Common Applications |
---|---|---|
Inconel | High strength, oxidation resistance | Aerospace, chemical processing |
Titanium | High melting point, corrosion resistance | Marine, automotive, aerospace |
Stainless Steel | Durability, ease of fabrication | Industrial, food processing |
Molybdenum | Excellent high-temperature strength | Aerospace, nuclear, and electronics |
Each metal has distinct advantages, so manufacturers must carefully choose the right type based on the desired properties.
2. Why Are Heat-Resistant Metals Important?
The importance of heat-resistant metals cannot be overstated. These materials provide the backbone for industries that deal with high-temperature environments, ensuring that everything from jet engines to industrial furnaces operates smoothly. Without heat-resistant metals, many critical systems would fail prematurely, leading to equipment breakdowns and safety risks.
What’s the real story? Well, these metals also improve efficiency and reduce maintenance costs. By choosing the right materials, businesses can extend the life cycle of machinery, decrease downtime, and avoid costly repairs.
Industry | Heat-Resistant Metal Use | Benefits |
---|---|---|
Aerospace | Engine parts, turbine blades | Long service life, high efficiency |
Automotive | Exhaust systems, engine components | Durability, better fuel efficiency |
Energy | Boilers, heat exchangers | Enhanced heat tolerance, corrosion resistance |
In aerospace, for instance, Inconel and titanium alloys are used to build turbine blades, ensuring they withstand extreme temperatures without degrading.
3. What Are the Key Properties of Heat-Resistant Metals?
Heat-resistant metals are distinguished by several critical properties that make them ideal for high-temperature applications. These include:
- Thermal stability: The ability to maintain mechanical properties under elevated temperatures.
- Oxidation resistance: Protects the metal from degradation when exposed to oxygen at high temperatures.
- Corrosion resistance: Helps the metal withstand the chemical reactions that occur at high heat.
- High melting point: Prevents the metal from melting under extreme temperatures.
This is where it gets interesting: each of these properties plays a vital role depending on the application. For example, aerospace components need high oxidation and corrosion resistance, while automotive parts prioritize durability and thermal stability.
Property | Metal Type | Benefit |
---|---|---|
High Melting Point | Titanium | Withstands extreme heat without deforming |
Oxidation Resistance | Inconel | Maintains strength under heat and oxidation |
Corrosion Resistance | Stainless Steel | Resists rust in marine environments |
These properties determine how heat-resistant metals will perform under different conditions, making it crucial to select the right material for the job.
4. How Are Heat-Resistant Metals Manufactured?
The manufacturing process of heat-resistant metals is complex and requires precise control. The materials are produced through various techniques, including casting, forging, and sintering. These methods ensure that the metal can handle extreme temperatures and other stressors without compromising quality.
Ready for the good part? Let’s take a look at some of the manufacturing techniques that contribute to the strength and reliability of heat-resistant metals:
- Casting: Involves pouring molten metal into a mold to create the desired shape.
- Forging: Metal is heated and then shaped by applying force.
- Sintering: Fine powder is heated to bond the particles without melting.
Each of these processes is vital for ensuring the final product can perform reliably in high-temperature environments.
Manufacturing Process | Application | Key Advantage |
---|---|---|
Casting | Aerospace, automotive | Complex shapes with high dimensional accuracy |
Forging | Heavy machinery | Increased strength and durability |
Sintering | Electronics, tools | Precise control of material properties |
By carefully selecting the appropriate manufacturing process, companies ensure that their heat-resistant metals will be of the highest quality.
5. Who Are the Top Manufacturers of Heat-Resistant Metals?
The heat-resistant metal industry is home to several renowned manufacturers who are known for their high-quality products and technological innovations. Companies like Haynes International, ATI Allvac, and VSMPO-AVISMA lead the charge, providing a variety of alloys and components for industries worldwide.
This is where it gets interesting: These companies don’t just supply materials; they also invest heavily in research and development, constantly improving the properties of their metals to meet evolving industry demands.
Manufacturer | Headquarters Location | Specialization |
---|---|---|
Haynes International | USA | High-performance alloys |
ATI Allvac | USA | Superalloys for aerospace |
VSMPO-AVISMA | Russia | Titanium alloys for aerospace |
These manufacturers have built a reputation for reliability, ensuring their metals can withstand the harshest environments while maintaining performance.
6. What Makes These Manufacturers Stand Out?
So, what sets the top manufacturers apart from others? The key lies in their ability to consistently produce high-quality heat-resistant metals that meet stringent industry standards. From the latest technology in alloy development to customer support, these manufacturers offer more than just products; they offer solutions.
But here’s the kicker: It’s not just about the metals. These companies also provide in-depth support services, including custom solutions for specific client needs, fast quoting systems, and on-time delivery—critical factors in industries where time and precision matter.
Company | Key Advantage | Market Focus |
---|---|---|
Haynes International | Innovation and material development | Aerospace, chemical |
ATI Allvac | Superalloy production | Aerospace, energy |
VSMPO-AVISMA | Large-scale titanium production | Aerospace, defense |
They stand out not only for the quality of their products but for the complete customer experience they offer.
7. Leading Manufacturers of Heat-Resistant Metals
Let’s take a closer look at three of the top companies in the field. Haynes International, ATI Allvac, and VSMPO-AVISMA are among the best, providing high-performance metals that meet the needs of the aerospace, automotive, and energy sectors.
Ready for the good part? These manufacturers are known for pushing the boundaries of material science, constantly innovating to create alloys that can withstand higher temperatures, offer better strength, and resist more environmental factors than ever before.
Company | Specialization | Products Offered |
---|---|---|
Haynes International | High-performance alloys | Inconel, Hastelloy, and other superalloys |
ATI Allvac | Superalloys for high-stress environments | Allvac superalloys, powder metallurgy alloys |
VSMPO-AVISMA | Titanium production | Titanium ingots, bars, and sheets |
These companies ensure their materials are at the cutting edge of innovation and reliability.
8. Where Are These Manufacturers Located?
Geography plays a crucial role in the heat-resistant metal market. Leading manufacturers are often located in areas with strong industrial infrastructure, close to key markets such as aerospace and automotive industries.
In the case of Haynes International and ATI Allvac, both are based in the United States, which is a major hub for aerospace and defense. Meanwhile, VSMPO-AVISMA, located in Russia, is one of the largest suppliers of titanium for the aerospace sector, contributing to the global demand for high-performance materials.
Manufacturer | Location | Key Industry Benefits |
---|---|---|
Haynes International | USA | Proximity to aerospace and defense |
ATI Allvac | USA | Close to North American industrial hubs |
VSMPO-AVISMA | Russia | Dominates titanium market, aerospace focus |
The location of these companies often aligns with the needs of industries requiring high-quality, heat-resistant metals.
9. When Do Industries Typically Use Heat-Resistant Metals?
Industries rely on heat-resistant metals whenever high temperatures are involved in production or operation processes. From jet engines to power plants, these metals are used when the performance of materials must be guaranteed under extreme conditions.
Here’s the deal: In aerospace, heat-resistant metals are used in engine turbines, where temperatures can reach over 1,000 degrees Celsius. Meanwhile, in energy production, these metals are crucial for heat exchangers and boilers, where temperature control is vital.
Industry | Typical Applications | Metal Type Used |
---|---|---|
Aerospace | Jet engine components, turbine blades | Inconel, Titanium |
Automotive | Exhaust systems, engine components | Stainless Steel, Molybdenum |
Energy | Heat exchangers, boilers | Inconel, Molybdenum |
Heat-resistant metals are indispensable in industries that operate at the highest temperatures, ensuring systems run smoothly and safely.
10. How to Choose the Right Manufacturer for Heat-Resistant Metals?
Choosing the right manufacturer for heat-resistant metals is critical for ensuring quality, performance, and timely delivery. Several factors should be considered when selecting a supplier, including certifications, technological capabilities, and customer service.
What’s the real story? Look for manufacturers with proven experience in producing high-performance alloys, as well as those who offer flexible solutions tailored to your needs. Quality control and testing standards should also be at the forefront of your selection process to ensure the metals will perform as expected under high-heat conditions.
Factor | What to Look For | Why It’s Important |
---|---|---|
Certifications | ISO, ASTM standards | Ensures compliance with global standards |
Technological Capabilities | Advanced alloy development and testing equipment | Guarantees high-quality materials and performance |
Customer Service | Fast response time, technical support | Minimizes downtime and enhances customer experience |
11. Comparing Heat-Resistant Metals: Properties and Applications
When selecting heat-resistant metals, it’s important to compare the properties of different types. Each metal has its strengths, depending on the environment and temperature ranges it will be exposed to.
For example, titanium is favored for its high melting point and corrosion resistance in marine applications, while Inconel’s ability to resist oxidation makes it the preferred choice for aerospace components.
Metal Type | Melting Point | Key Property | Best Use Case |
---|---|---|---|
Titanium | 1,668°C | Corrosion resistance | Aerospace, Marine |
Inconel | 1,350°C | Oxidation resistance | Aerospace, Chemical Processing |
Molybdenum | 2,623°C | High-temperature strength | Aerospace, Electronics |
Understanding the differences between these metals is essential for selecting the right material for your application.
12. Challenges in Manufacturing Heat-Resistant Metals
Manufacturing heat-resistant metals is not without its challenges. From sourcing the right raw materials to maintaining high-quality production standards, manufacturers must overcome various hurdles to ensure the metals can withstand extreme temperatures without compromising on performance.
Ready for the good part? Technological advances are continuously making it easier to produce stronger and more durable heat-resistant alloys, addressing some of these challenges head-on.
Challenge | Solution |
---|---|
Material Sourcing | Development of new, more abundant alloys |
Quality Control | Automation and advanced testing techniques |
Cost Control | Lean manufacturing processes |
With constant innovation, the industry continues to evolve, ensuring that the metals produced meet the highest standards of quality.
13. The Future of Heat-Resistant Metal Manufacturing
The future of heat-resistant metal manufacturing is full of potential. As industries continue to push the boundaries of technology, there will be greater demand for metals that can withstand even more extreme temperatures.
This is where it gets interesting: Researchers are already working on new alloys with higher temperature thresholds and better resistance to wear and tear. Expect to see more advanced materials being used in applications like electric vehicles, advanced energy storage systems, and more.
Trend | Expected Outcome | Industry Impact |
---|---|---|
Alloys Innovation | Development of higher-performing alloys | Aerospace, Automotive |
Sustainable Manufacturing | Focus on eco-friendly production methods | Reduced environmental impact |
The future holds exciting prospects for heat-resistant metals, with innovations set to change industries for the better.
14. Conclusion
To wrap things up, the top manufacturers of heat-resistant metals are continually pushing the limits of material science. By focusing on key properties such as thermal stability, oxidation resistance, and high melting points, these manufacturers provide the essential materials needed for high-performance applications across industries.
In choosing the right manufacturer, always consider their track record, technological capabilities, and the specific needs of your application. By doing so, you can ensure that your business benefits from the highest-quality heat-resistant metals available.
FAQ Section
Q1: What are heat-resistant metals and why are they important?
Heat-resistant metals are alloys designed to maintain their strength under high temperatures. They are crucial for industries like aerospace, automotive, and energy, where high-performance materials are necessary to ensure longevity and reliability under extreme heat conditions.
Q2: How do manufacturers produce heat-resistant metals?
Manufacturers use casting, forging, and sintering techniques to produce heat-resistant metals. These processes ensure that the materials can withstand high temperatures and other environmental stressors without compromising their structural integrity.
Q3: What are the best applications for heat-resistant metals?
Heat-resistant metals are used in applications requiring durability and performance under high temperatures, such as jet engines, industrial furnaces, and power plant components. They are also essential for machinery exposed to extreme conditions.
Q4: How can I choose the right manufacturer for heat-resistant metals?
Look for manufacturers with a proven track record, high-quality materials, and strong customer service. Consider certifications and testing standards to ensure the metals meet industry requirements and perform as expected in high-heat environments.
Q5: What are some challenges in manufacturing heat-resistant metals?
Manufacturers face challenges like sourcing high-quality raw materials, maintaining consistency in production, and meeting stringent environmental regulations. Innovations in technology are helping address these issues and improve metal performance.