What Are High-Temperature Alloy Castings?
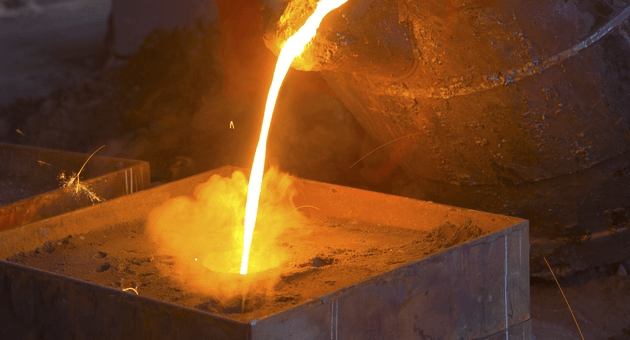
High-temperature alloy castings are advanced materials designed to perform under extreme heat and challenging conditions. These alloys typically comprise metals like nickel, cobalt, and chromium, engineered for applications where durability, corrosion resistance, and heat tolerance are critical. Used in industries such as aerospace, automotive, and energy, they ensure reliable performance where other materials would fail. This technology enables the creation of components that withstand severe environments, such as jet engines, turbines, and power plants. By choosing high-temperature alloy castings, businesses can achieve superior efficiency, safety, and cost savings over time, making them a cornerstone of modern engineering solutions.
The Problem with Standard Materials in High-Temperature Environments
Materials like stainless steel or aluminum, while versatile and cost-effective, fail when exposed to extreme heat and corrosive environments. For instance, at high temperatures, these materials lose mechanical strength, leading to warping or structural failure. This is particularly problematic in critical applications like jet engines or industrial reactors, where any failure can result in catastrophic outcomes. Traditional materials also suffer from thermal expansion, which causes misalignment and wear over time, reducing the lifespan of components. Additionally, corrosion accelerates in harsh environments, weakening the material further and necessitating frequent replacements.
The limitations of conventional materials create significant challenges for industries reliant on efficiency and precision. For example, power plants that rely on steam turbines require materials that can endure both high temperatures and corrosive steam. Using inappropriate materials results in inefficiencies, costly maintenance, and potential safety risks. These constraints highlight the need for specialized solutions that offer enhanced durability, stability, and resistance. High-temperature alloy castings address these issues by providing the robust performance necessary for demanding applications, enabling industries to operate safely and effectively without frequent interruptions.
Why High-Temperature Alloy Casting is the Solution
High-temperature alloy casting is the ideal solution for environments where conventional materials fail to meet performance standards. These castings are engineered to retain their mechanical properties even under intense thermal stress, making them indispensable in industries like aerospace, automotive, and energy. For example, jet engine components crafted from these alloys maintain structural integrity at temperatures exceeding 1,000°C, ensuring reliability and safety during operation.
Another advantage is their exceptional corrosion resistance. High-temperature alloys resist oxidation and chemical degradation, even in highly corrosive environments like chemical reactors or saltwater conditions. This resistance reduces the frequency of repairs and replacements, significantly lowering operational costs. Moreover, these castings are highly customizable, allowing manufacturers to tailor their compositions to meet specific application needs. Whether it’s a turbine blade or an exhaust manifold, the precision offered by these materials ensures optimal performance.
High-temperature alloy casting also supports innovation in design. Their flexibility in molding complex shapes allows engineers to develop components with enhanced functionality and reduced weight. This adaptability leads to greater efficiency and performance across various sectors. By opting for these castings, industries can overcome the limitations of traditional materials, achieving long-term operational success and resilience in extreme environments.
Superior Heat Resistance
High-temperature alloy castings excel in environments where intense heat is a constant challenge. These alloys retain their strength and structural integrity even when exposed to temperatures that would cause standard materials to fail. For example, nickel-based alloys are commonly used in jet engines and turbines, where components are subjected to sustained high temperatures and extreme pressure. These materials ensure that the equipment operates safely and efficiently without degrading over time.
The key to their heat resistance lies in their advanced composition. Elements like chromium and molybdenum form protective oxide layers on the material’s surface, preventing degradation at high temperatures. This feature is especially valuable in power plants, where turbines must endure continuous heat exposure without succumbing to thermal fatigue. The alloys’ ability to resist thermal expansion also ensures that components maintain their shape and alignment, reducing the risk of system failures.
Industries that require reliable performance under extreme heat, such as aerospace or industrial processing, benefit significantly from these properties. By choosing high-temperature alloy castings, manufacturers can create systems that operate longer and more reliably, ultimately reducing maintenance costs and improving safety standards.
Enhanced Corrosion Resistance
High-temperature alloy castings provide exceptional resistance to corrosion, even in the harshest environments. This quality is critical in industries where materials are exposed to aggressive chemicals, moisture, and oxidizing agents. For example, in chemical processing plants, equipment like reactors and heat exchangers must withstand prolonged exposure to corrosive substances without compromising performance.
The inclusion of elements such as chromium and cobalt enhances the corrosion resistance of these alloys. Chromium forms a stable oxide layer that protects the underlying material, while cobalt contributes to maintaining the alloy’s strength in corrosive settings. This combination ensures that the alloys can handle both high temperatures and corrosive conditions simultaneously, making them ideal for applications in marine environments or industrial gas turbines.
By investing in high-temperature alloy castings, businesses can avoid frequent equipment failures and replacements caused by corrosion. This durability translates into lower maintenance costs and improved operational efficiency. Additionally, the reliability of these materials under challenging conditions enhances safety and reduces the risk of unexpected downtimes.
Strength Under Stress
High-temperature alloys are engineered to withstand not only heat and corrosion but also immense mechanical stress. In applications like aerospace and automotive, components are often subjected to extreme forces that could lead to deformation or cracking. High-temperature alloy castings excel in these scenarios, maintaining their structural integrity under both static and dynamic loads.
One reason for their strength is their unique microstructure, designed to resist creep—a phenomenon where materials deform under long-term stress at high temperatures. For example, turbine blades in jet engines experience constant centrifugal forces and heat. High-temperature alloys prevent these components from failing, ensuring safe and efficient operation.
The superior strength of these materials also allows for thinner, lighter components without sacrificing performance. This weight reduction is especially advantageous in aerospace applications, where every kilogram saved translates to fuel efficiency and cost savings. High-temperature alloy castings combine durability with flexibility, enabling innovative designs that push the boundaries of engineering.
Longevity and Cost-Effectiveness
Investing in high-temperature alloy castings offers significant long-term financial benefits. While the initial cost of these materials may be higher than standard options, their durability and performance make them more economical over time. These alloys resist wear, corrosion, and thermal fatigue, reducing the frequency of repairs and replacements. This longevity translates into lower maintenance costs and less downtime, which is crucial for industries like energy and manufacturing.
For example, power plants using high-temperature alloys in turbines experience fewer operational interruptions due to material failure. This reliability enhances efficiency and output, resulting in greater profitability. In the automotive industry, components like exhaust manifolds and turbochargers made from high-temperature alloys withstand prolonged exposure to heat and corrosive gases, ensuring longer vehicle lifespans and reduced warranty claims.
Moreover, the extended service life of these materials aligns with sustainability goals by minimizing waste and resource consumption. By choosing high-temperature alloy castings, businesses can achieve a balance between performance, cost, and environmental responsibility.
Composition of High-Temperature Alloys
The exceptional properties of high-temperature alloys stem from their carefully engineered compositions. These materials are typically made from a combination of nickel, cobalt, chromium, and other elements like molybdenum and aluminum. Each element contributes specific characteristics that enhance the alloy’s performance under extreme conditions.
Nickel serves as the base for most high-temperature alloys due to its excellent heat resistance and strength. Chromium adds corrosion resistance by forming a stable oxide layer, while cobalt improves mechanical stability. Molybdenum enhances resistance to wear and creep, and aluminum contributes to the formation of protective oxide coatings.
Understanding the composition of these alloys allows engineers to select the optimal material for specific applications. For instance, a high-chromium alloy might be chosen for environments with intense chemical exposure, while a nickel-based alloy could be ideal for aerospace components. The versatility and adaptability of these materials make them indispensable for modern engineering challenges.
Innovations in Alloy Technology
Technological advancements have expanded the capabilities of high-temperature alloys, enabling their use in increasingly demanding applications. For example, additive manufacturing techniques like 3D printing allow for precise fabrication of complex components, reducing material waste and production time. These methods also enable the creation of designs that were previously impossible with traditional casting techniques.
Innovations in alloy compositions have also improved performance. New superalloys are being developed to withstand even higher temperatures and harsher environments. For instance, alloys with higher refractory metal content offer enhanced resistance to thermal creep and oxidation.
Research into nanostructured alloys has further pushed the boundaries of what these materials can achieve. By refining the microstructure at a nanoscale level, scientists are creating alloys with unprecedented strength and durability. These innovations ensure that high-temperature alloys remain at the forefront of material science, driving progress across industries.
Aerospace: The Sky-High Need for High-Temperature Alloys
The aerospace industry relies heavily on high-temperature alloy castings for critical components such as jet engines, turbine blades, and exhaust systems. These materials enable aircraft to operate safely and efficiently under extreme conditions. For example, turbine blades made from nickel-based alloys can withstand temperatures exceeding 1,000°C while maintaining their structural integrity.
The use of high-temperature alloys in aerospace also enhances fuel efficiency. By enabling engines to run at higher temperatures, these materials improve combustion efficiency and reduce emissions. This performance is vital for meeting stringent environmental regulations and reducing operating costs.
Safety is another key consideration. Aircraft components must endure high stress without failure, and high-temperature alloys provide the reliability needed to ensure passenger and crew safety. Their exceptional properties make them an indispensable part of modern aviation engineering.
Energy Sector: Heat Management in Power Plants
The energy sector depends on high-temperature alloy castings to improve the efficiency and reliability of power generation. In steam turbines, these materials resist thermal fatigue and corrosion, ensuring consistent performance under prolonged operation. This durability reduces maintenance costs and enhances energy output.
In nuclear and solar power plants, high-temperature alloys play a critical role in managing heat transfer and resisting radiation damage. Their ability to maintain stability under extreme conditions makes them ideal for these demanding applications. By using these materials, power plants can achieve greater efficiency and safety, contributing to a sustainable energy future.
Their application in renewable energy systems also supports the transition to greener technologies. For example, high-temperature alloys are used in concentrated solar power systems, where they withstand intense heat to maximize energy conversion. This versatility ensures their continued importance in advancing global energy solutions.
Automotive Industry: Efficiency and Performance
High-temperature alloy castings are transforming the automotive industry by enabling the development of high-performance and efficient vehicles. These materials are commonly used in components such as turbochargers, exhaust manifolds, and heat shields, where they endure extreme heat and corrosive environments. Their durability ensures reliable performance, even under demanding operating conditions.
Turbochargers made from high-temperature alloys, for example, can withstand the intense heat generated during combustion. This durability allows engines to achieve higher power outputs without compromising efficiency. Additionally, the alloys’ resistance to thermal fatigue ensures a longer lifespan for critical components, reducing maintenance costs for vehicle owners.
The lightweight properties of these materials also contribute to fuel efficiency. By replacing heavier components with high-temperature alloys, manufacturers can produce vehicles that consume less fuel and emit fewer greenhouse gases. This innovation aligns with industry trends toward sustainability and compliance with stricter emissions regulations. High-temperature alloys are thus paving the way for a new era of automotive engineering.
Industrial and Chemical Processing
In industrial and chemical processing, high-temperature alloy castings are indispensable for maintaining efficiency and safety. Equipment such as reactors, heat exchangers, and pipelines must endure extreme heat and corrosive substances without failure. High-temperature alloys meet these demands by offering exceptional resistance to oxidation, wear, and thermal stress.
For example, in petrochemical plants, high-temperature alloys are used in catalytic converters and reformers to resist the harsh environments of chemical reactions. Their ability to withstand prolonged exposure to high temperatures and corrosive gases ensures reliable operation and minimizes downtime.
The adaptability of these materials also allows for customized solutions in industrial applications. Engineers can tailor the composition of high-temperature alloys to meet specific requirements, such as increased resistance to specific chemicals or enhanced thermal conductivity. This versatility makes them a critical component of modern industrial processes.
The Casting Process: Ensuring Precision
The casting process for high-temperature alloys is a highly specialized technique that ensures precision and reliability. Investment casting, also known as the lost-wax process, is the most common method used for these materials. This process allows for the creation of intricate and complex shapes with exceptional accuracy.
Investment casting begins with the creation of a wax model, which is coated in ceramic material to form a mold. Once the wax is melted away, the mold is filled with molten high-temperature alloy. After cooling, the ceramic shell is removed to reveal a finished component. This method ensures that each piece meets strict dimensional and performance specifications.
Advanced technologies, such as vacuum casting, are also used to improve the quality of high-temperature alloy castings. By eliminating impurities and ensuring uniform composition, these techniques produce components that can withstand extreme conditions. The precision of the casting process is essential for achieving the high performance required in critical applications.
Challenges and Solutions in High-Temperature Casting
Despite their many advantages, high-temperature alloy castings present unique challenges during production. Issues such as cracking, porosity, and cost can impact the manufacturing process. However, advances in technology and engineering have provided effective solutions to these problems.
Cracking during cooling is a common issue due to the alloys’ high thermal expansion rates. To address this, manufacturers use controlled cooling techniques and optimized mold designs to minimize stress. Porosity, which can weaken the material, is reduced through vacuum casting and advanced solidification processes.
The cost of high-temperature alloy casting can be significant, but it is offset by the long-term benefits of durability and performance. Manufacturers are also exploring cost-saving measures, such as additive manufacturing and recycling of materials, to make these castings more accessible. By overcoming these challenges, the industry continues to expand the applications of high-temperature alloys.
Choosing the Right Alloy for Your Needs
Selecting the appropriate high-temperature alloy for a specific application requires careful consideration of factors such as temperature, environment, and mechanical stress. Each alloy has unique properties that make it suitable for certain conditions.
For example, nickel-based alloys are ideal for applications requiring high strength and resistance to oxidation, such as jet engines and gas turbines. Cobalt-based alloys, on the other hand, excel in environments with high wear and corrosion, making them suitable for chemical processing equipment.
Consulting with experts and conducting thorough testing are essential steps in the selection process. By choosing the right alloy, businesses can maximize the performance and longevity of their equipment, ensuring successful operations in challenging environments.
Sustainability in High-Temperature Alloy Casting
High-temperature alloy casting supports sustainability by reducing waste and conserving resources. The durability of these materials means fewer replacements and less material consumption over time. Additionally, many manufacturers use recycled metals in the production of high-temperature alloys, minimizing environmental impact.
Energy-efficient production methods, such as advanced casting techniques and additive manufacturing, further enhance sustainability. These processes reduce energy consumption and emissions, aligning with global efforts to combat climate change. By adopting sustainable practices, the industry contributes to a greener future while maintaining high performance standards.
Economic Benefits Across Industries
The economic advantages of high-temperature alloy casting extend across various industries. By reducing maintenance costs and increasing equipment lifespan, these materials provide significant financial savings. For example, power plants that use high-temperature alloys in turbines experience fewer operational interruptions, leading to higher efficiency and profitability.
In the automotive sector, the use of high-temperature alloys enhances vehicle performance and reliability, reducing warranty claims and customer dissatisfaction. These benefits translate into stronger brand reputation and competitive advantage. Across all industries, high-temperature alloys offer a cost-effective solution for achieving long-term success.
Summarizing the Value of High-Temperature Alloy Castings
High-temperature alloy castings are a transformative technology that addresses the limitations of traditional materials. Their exceptional properties, including heat resistance, corrosion resistance, and strength, make them indispensable for critical applications. By investing in these materials, industries can achieve greater efficiency, safety, and sustainability.
To unlock the full potential of high-temperature alloy castings, consult with experts and explore customized solutions for your specific needs. Embrace this advanced technology to enhance performance and reliability across your operations.
FAQ Section
What is high-temperature alloy casting?
High-temperature alloy casting involves using specialized alloys to create components capable of withstanding extreme heat and challenging conditions.
Which industries benefit most from these castings?
Industries such as aerospace, energy, automotive, and chemical processing rely heavily on high-temperature alloy castings for their durability and performance.
What materials are used in high-temperature alloys?
Common elements include nickel, cobalt, chromium, molybdenum, and aluminum, each contributing unique properties.
Are high-temperature alloy castings cost-effective?
While initially more expensive, their durability and reduced maintenance needs make them a cost-effective choice over time.
How do these materials support sustainability?
High-temperature alloys are often made using recycled materials and produced through energy-efficient methods, reducing their environmental impact.